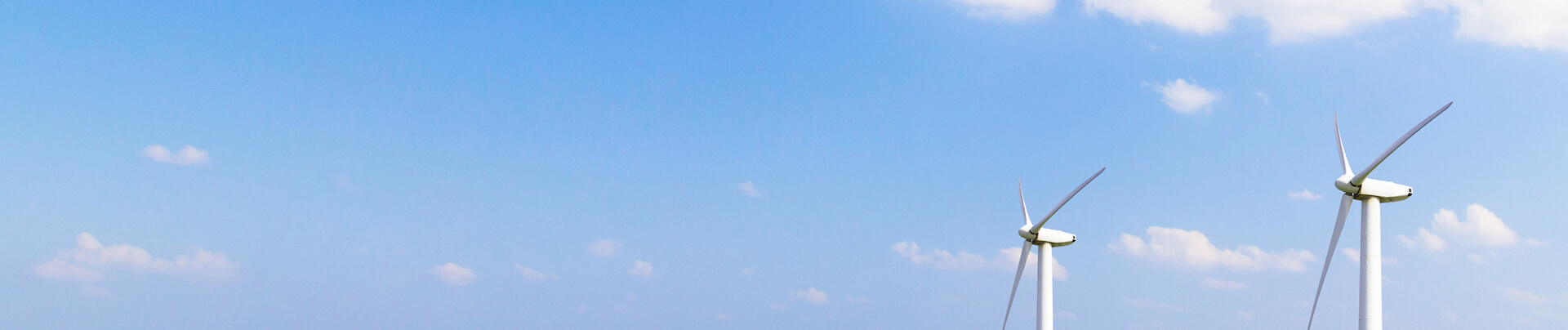
L'échange et le partage favorisent la croissance et
travaillent ensemble pour un développement commun!
Un dissipateur thermique a pour rôle d'augmenter la surface de transfert thermique dans un espace de volume donné. En optimisant la forme de la structure, on peut améliorer l'efficacité de transfert thermique de la surface vers le fluide environnant. Le traitement de surface, entre autres, permet d’augmenter la surface de transfert effective, renforçant ainsi le refroidissement et permettant un meilleur contrôle de la température.
Dans les applications à faible densité de puissance volumétrique et de densité de flux thermique, les dissipateurs thermiques à ailettes droites et rectangulaires sont très appréciés des ingénieurs pour leur structure simple, leur coût de fabrication raisonnable et leur bonne performance de dissipation thermique.
Comparaison des différentes méthodes de transfert de chaleur
1-Conception des ailettes de dissipateur thermique
Un dissipateur thermique agit comme une surface de dissipation élargie et se concentre principalement sur des paramètres tels que la hauteur, la forme, l'espacement des ailettes et l'épaisseur de la plaque de base.
Dimensions du dissipateur thermique à ailettes plates
D'après le schéma ci-dessus, on peut calculer la surface de dissipation étendue du dissipateur thermique:
Surface d'une seule ailette:Af = 2L(h+t/2),
Surface des espaces:Ab= Lh,
Surface totale de dissipation thermique:At=nAf +(n±1)Ab (n étant le nombre d’ailettes).
Vue en coupe des ailettes
La fonction principale des ailettes est d’augmenter la surface pour améliorer l’efficacité de transfert de chaleur.L’espacement, l’épaisseur et la hauteur des ailettes sont des facteurs clés pour déterminer le nombre, la répartition et la surface des ailettes.Comme indiqué dans le schéma, lorsque h↑ ou t↓, les ailettes deviennent plus hautes, plus minces et plus denses, augmentant la surface de dissipation.
Lorsque la surface des ailettes augmente, leur contact avec l’air augmente également, facilitant ainsi la dissipation thermique.Les ingénieurs peuvent également augmenter la surface des dissipateurs en optimisant la forme des ailettes, comme ondulées ou dentelées.
Bien qu’une plus grande surface de dissipation thermique améliore l’effet de refroidissement, cela ne signifie pas nécessairement que plus grand est toujours mieux.Que ce soit pour la dissipation naturelle ou le refroidissement forcé, l’espacement des ailettes est un facteur déterminant du coefficient de transfert thermique de l’air.
Impact de l’espacement et de la hauteur des ailettes sur l’efficacité de dissipation thermique
En cas de dissipation naturelle, les variations de température à la surface du dissipateur provoquent une convection naturelle et le flux de la couche limite d’air le long des ailettes. Un espacement trop petit entrave ce processus.En cas de refroidissement forcé, l’épaisseur de la couche limite des ailettes est comprimée, l’espacement peut être plus étroit, mais il est limité par les méthodes de fabrication et les éléments moteurs. L’équilibre entre l’épaisseur et la hauteur des ailettes est donc crucial.
2-Conception du substrat du dissipateur thermique
L’épaisseur du substrat est un facteur crucial dans l’efficacité d’un dissipateur thermique. Si le substrat est trop mince, la résistance thermique entre les ailettes éloignées de la source de chaleur est plus élevée, provoquant une répartition inégale de la température et une résistance moindre aux chocs thermiques.
L’augmentation de l’épaisseur du substrat peut corriger la répartition inégale de la température et accroître la résistance aux chocs thermiques. Cependant, un substrat trop épais pourrait provoquer une accumulation de chaleur et réduire ainsi la conductivité thermique.
Schéma du principe de fonctionnement du dissipateur thermique
Comme illustré ci-dessus :
lorsque la surface de la source de chaleur est inférieure à celle de la plaque de base, la chaleur doit se diffuser du centre vers les bords, ce qui crée une résistance thermique de diffusion. La position de la source de chaleur affecte également cette résistance. Si la source est proche du bord du dissipateur, la chaleur peut être plus facilement dissipée par le bord, réduisant ainsi la résistance de diffusion.
Remarque : la résistance thermique de diffusion désigne la résistance rencontrée dans la conception d’un dissipateur thermique lorsque la chaleur se diffuse du centre de la source de chaleur vers les bords. Ce phénomène se produit généralement lorsque la surface de la source de chaleur est nettement inférieure à celle de la plaque de base, nécessitant la diffusion de la chaleur d’une petite zone vers une zone plus large.
3-Procédé de connexion entre les ailettes et la plaque de base
La méthode de connexion entre les ailettes du dissipateur et la plaque de base comprend généralement plusieurs techniques pour garantir une bonne conduction thermique et une stabilité mécanique. Elle se divise principalement en deux catégories : intégrée et non intégrée.
Les dissipateurs intégrés, où les ailettes et la plaque de base forment un ensemble unique, ne présentent pas de résistance thermique de contact. Les procédés sont principalement les suivants :
l Moulage sous pression de l’aluminium : après avoir fondu les lingots d’aluminium, celui-ci est injecté sous haute pression dans un moule métallique. Le dissipateur est alors moulé directement, permettant ainsi de réaliser des ailettes de formes complexes.
l Extrusion de l’aluminium : une fois l’aluminium chauffé, il est placé dans un cylindre d’extrusion et soumis à une pression pour le faire sortir par un moule spécifique, obtenant ainsi un matériau brut avec la forme et les dimensions de la section souhaitée, ensuite usiné.
l Le forgeage à froid permet de réaliser des ailettes de dissipation fines avec un coefficient de conductivité thermique élevé, bien que les coûts soient relativement élevés. Cette méthode est meilleure pour traiter des formes spéciales que l’extrusion d’aluminium.
l Les dissipateurs à rainures peuvent être en cuivre, avec un coefficient de conductivité thermique élevé, et les ailettes peuvent être très fines. Les ailettes sont directement sculptées à partir de la plaque de base, mais de fortes tensions peuvent déformer les ailettes hautes ou longues.
Dans la fabrication non intégrée, les ailettes de refroidissement et la plaque de base sont usinées séparément, puis assemblées par des procédés tels que le soudage, le rivetage ou le collage. Les principaux procédés sont :
l Soudure : Les ailettes et la plaque de base sont connectées par un matériau de soudage, comprenant le brasage à haute température et le brasage à basse température ;
La soudure présente de bonnes performances de transfert de chaleur ; pour souder des substrats en aluminium et des ailettes, un placage au nickel est nécessaire, ce qui augmente le coût et n'est pas adapté aux dissipateurs de grande taille ; le brasage ne nécessite pas de placage au nickel, mais le coût de soudure reste élevé.
l Rivetage : Les ailettes sont insérées dans la rainure de la plaque de base, puis la rainure est pressée vers le centre par un moule pour maintenir fermement les ailettes de refroidissement et réaliser une connexion solide.
L'avantage du rivetage est sa bonne performance de transfert de chaleur, mais les produits rivetés présentent un risque de jeu et de relâchement après une utilisation répétée ; il est possible d'améliorer le processus de rivetage pour accroître la fiabilité, mais cela entraîne également une augmentation des coûts. Par conséquent, les dissipateurs à rivet sont souvent utilisés dans des situations où les exigences de fiabilité ne sont pas élevées.
l Collage : En général, on utilise une résine époxy thermoconductrice pour coller fermement les ailettes de refroidissement à la plaque de base, permettant ainsi la conduction thermique.
Le collage utilise de la résine époxy thermoconductrice, dont le coefficient de conductivité thermique est beaucoup plus faible que celui des soudures, mais qui est adapté aux ailettes plus hautes, aux rapports élevés et aux dissipateurs à petit espacement. Il peut être utilisé dans des scénarios où les exigences en matière de performance thermique ne sont pas élevées.
Nous mettrons régulièrement à jour les informations et technologies relatives à la conception thermique et à l’allègement.Merci de votre intérêt pour Walmate.