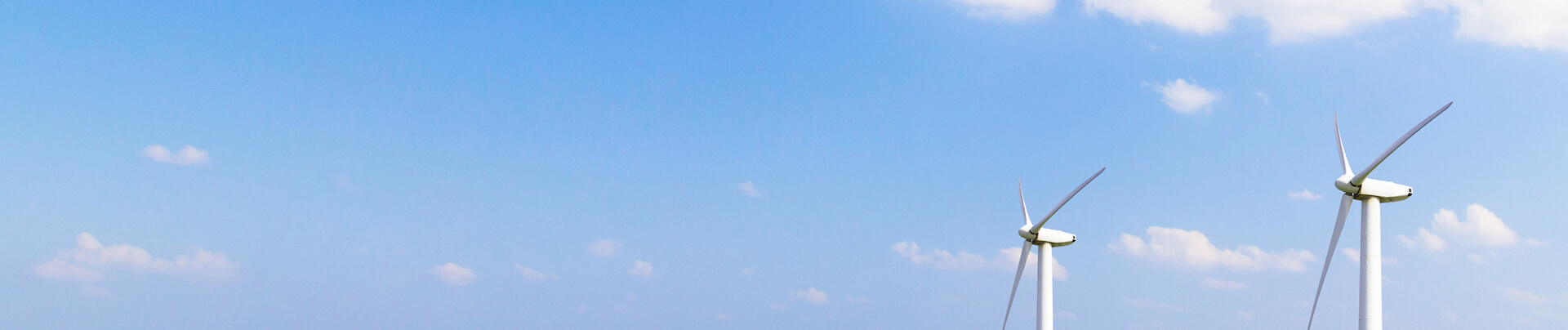
Austausch und Teilen fördern Wachstum,
Zusammenarbeit führt zu gemeinsamer Entwicklung.
Das Batteriegehäuse zur Energiespeicherung spielt eine entscheidende Rolle im Speichersystem. Zu seinen Hauptfunktionen gehören Lastschutz, gleichmäßige Wärmeverteilung, elektrische Installation und wasserdichte Abdichtung.Mit den steigenden Anforderungen an die Energiedichte der Batterien ist die Verwendung von Aluminiumlegierungen, die aufgrund ihrer hohen Wärmeleitfähigkeit und geringen Dichte bevorzugt werden, eine effektive Lösung zur Verbesserung der Systemleistung.
Das Design mit integrierter Strömungskanälen und Seitenwänden des Gehäuses kann die Schweißarbeiten an den tragenden Teilen reduzieren, wodurch die strukturelle Festigkeit verbessert wird. Dadurch bleibt die Struktur bei statischer Belastung, Hebevorgängen und zufälligen Vibrationen sicher und stabil, und gleichzeitig wird die Dichtleistung des Gehäuses in gewissem Maße verbessert.
Darüber hinaus hilft das integrierte Design, die Anzahl der Teile zu reduzieren und das Gewicht des Gehäuses zu verringern. Die Herstellung durch Extrusionsverfahren ermöglicht niedrige Formkosten, einfache Verarbeitung und leichte Anpassungen, um unterschiedliche Produktionsvolumina flexibel zu bedienen.
1-Haupttypen des Aluminium-Extrusionsschweißverfahrens für die Energiespeicher-Bodenbox
Die Breite der flüssigkeitsgekühlten Bodenbox für Energiespeicherung liegt normalerweise zwischen 790 und 810 mm, die Höhe variiert von 40 bis 240 mm. Sie wird in Flach- und Flanschform unterteilt (siehe Abbildung unten). Die Länge der flüssigkeitsgekühlten Bodenbox hängt von der Kapazität des Energiespeicherprodukts ab, gängige Varianten sind 48s, 52s, 104s und andere verschiedene Spezifikationen.
Flachbauweise der flüssigkeitsgekühlten Bodenbox
Flanschbauweise der flüssigkeitsgekühlten Bodenbox
2-Strukturformen des Aluminium-Extrusionsschweißverfahrens für die Energiespeicher-Bodenbox
Der flüssigkeitsgekühlte Kasten ist die Grundstruktur des gesamten Batteriepakets und besteht aus einer rechteckigen Rahmenstruktur, die aus einem Boden mit Kanälen, Dichtleisten, Wasseranschlüssen, Rahmen, Trägern, Halterungen und Haken zusammengesetzt ist. Alle Teile bestehen aus Aluminiumlegierung.
Schematische Darstellung der Montage von Komponenten des flüssigkeitsgekühlten Kasten
Der flüssigkeitsgekühlte Kasten muss über ausreichende Tragfähigkeit und strukturelle Festigkeit verfügen, was hohe Anforderungen an die Schweißqualität stellt, einschließlich Schweißverfahren, Schweißnahtklassifizierung und Schweißerfähigkeiten, um die Sicherheit und Zuverlässigkeit in der praktischen Anwendung zu gewährleisten.
Die Flüssigkeitskühltechnik stellt hohe Anforderungen an die Luftdichtheit des Flüssigkeitskühlkastens, einschließlich der Luftdichtheit des unteren Kastens und der Flüssigkeitskanäle. Zudem müssen die Flüssigkeitskanäle den Druck des Kühlmittels standhalten, weshalb die Anforderungen an die Luftdichtheit der Flüssigkeitskanäle noch höher sind.
3-Anforderungen an die Schweißqualität
Es wird allgemein gefordert, dass der Flüssigkeitskühlboden mit Reibungswiderstandsschweißen geschweißt wird. Auch die Stopfen des flachen Flüssigkeitskühlkastens werden mit Reibungswiderstandsschweißen verbunden. In der Regel sollte die Vertiefung der Reibungsnaht ≤ 0,5 betragen, und es dürfen keine abfallenden oder durch Vibrationen abfallenden Metallteile auftreten.
Flüssigkeitskanäle, Rahmen, Wasseranschlüsse, Aufhängungen, Querträger und andere Komponenten werden häufig mit TIG- oder CMT-Schweißen hergestellt. Aufgrund der unterschiedlichen Leistungsanforderungen der Teile wird für Flüssigkeitskanäle, Rahmen, Wasseranschlüsse, Aufhängungen usw. das volle Schweißen verwendet, während Querträger und Zubehör segmentweise geschweißt werden. Die Planheit im Bereich der vorderen und hinteren Batterie-Modulträger sollte für ein einzelnes Modul < 1,5 mm und für das gesamte Modul < 2 mm betragen; die Planheit des Rahmens muss für jede zusätzliche Länge von 500 mm ± 0,5 mm eingehalten werden.
An der Schweißnaht dürfen keine Risse, unvollständige Schweißungen, ungeschmolzene Bereiche, Oberflächenporen, freiliegende Schlacke oder unvollständige Schweißungen vorhanden sein. In der Regel wird gefordert, dass die Höhe der Wasseranschluss-Schweißnaht ≤ 6 mm beträgt, während die Schweißnähte an anderen Stellen die Unterseite des Gehäuses nicht überschreiten dürfen und die Schweißnähte an der Innenseite der vorderen und hinteren Modulträger nicht über die Innenseite hinausragen dürfen.
Die Schweißnahttiefe muss den relevanten Standardanforderungen entsprechen. Die Zugfestigkeit von Lichtbogen-Schweißverbindungen sollte mindestens 60 % des minimalen Zugfestigkeitswerts des Grundmaterials betragen; bei Laser- und Reibungsschweißverbindungen sollte die Zugfestigkeit mindestens 70 % des minimalen Zugfestigkeitswerts des Grundmaterials betragen.
Darüber hinaus muss das Schweißen des unteren Gehäuses auch die IP67-Dichtigkeitsstandards erfüllen. Daher wird für die Nachbearbeitung der Schweißnähte allgemein gefordert, dass die Schlacke und Schweißnähte im Bereich der vorderen und hinteren Modulträger glatt geschliffen werden; Schweißungen an der Außenseite der Palette dürfen nicht geschliffen werden, und die Schweißnähte an den Dichtflächen müssen glatt geschliffen werden, ohne nennenswerte Höhenunterschiede zum Rahmen.
Tabelle: Auswahl der Verarbeitungstechniken für den Verbund von Flüssigkeitskühlungsuntergehäusen in Energiespeichersystemen und typische Anwendungen
Wir werden regelmäßig Informationen und Technologien zu Wärmedesign und Leichtbau aktualisieren und mit Ihnen teilen. Vielen Dank für Ihr Interesse an Walmate.