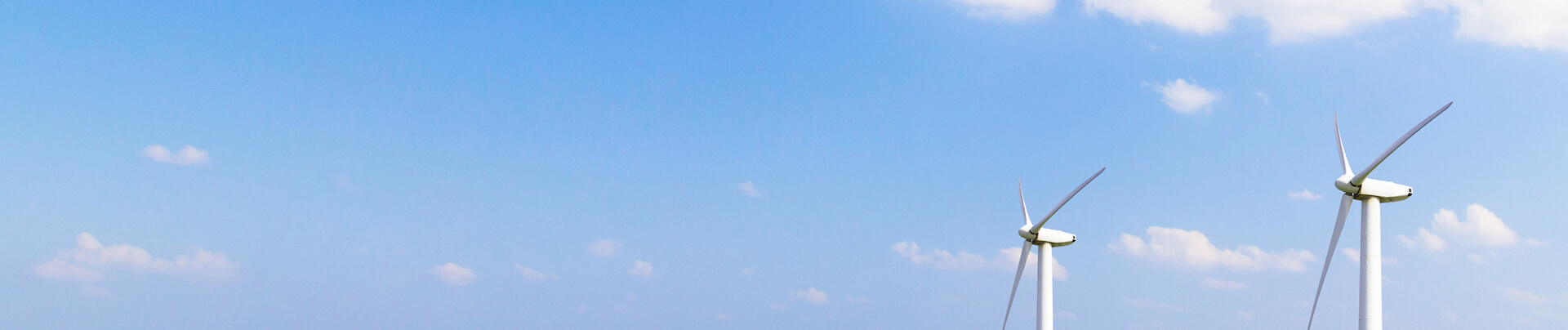
Austausch und Teilen fördern Wachstum,
Zusammenarbeit führt zu gemeinsamer Entwicklung.
Der Akku ist die zentrale Energiequelle von Fahrzeugen mit alternativer Antriebstechnik und liefert die Antriebskraft für das gesamte Fahrzeug. Wir bewerten die Vor- und Nachteile der Akkutechnologie im Allgemeinen anhand der Dimensionen Effizienz (Energiedichte), Sicherheit, Herstellungs- und Wartungskosten.
Beim Batteriedesign beträgt die Spannung einer einzelnen Zelle nur etwa 3–4 V, während die von Elektrofahrzeugen benötigte Spannung mindestens 100 V beträgt. Neue Autos haben jetzt sogar eine Spannung von 700 V/800 V und die Ausgangsleistung beträgt im Allgemeinen 200 W, sodass die Batterie aufgeladen werden muss. Um den Strom- und Spannungsbedarf von Elektrofahrzeugen zu erfüllen, müssen verschiedene Zellen in Reihe oder parallel geschaltet werden.
Der Batteriesatz besteht aus Batteriezellen, elektronischen und elektrischen Systemen, Wärmemanagementsystemen usw., die von einer Batterierahmenstruktur umschlossen sind – Grundplatte (Fach), Rahmen (Metallrahmen), obere Abdeckplatte, Schrauben usw. Wie diese Komponenten und Systeme effizienter und sicherer zu einem Ganzen „verpackt“ werden können, ist seit jeher ein Thema kontinuierlicher Forschung und Erkundung für die gesamte Branche.
Vorheriger Artikel: Innovation und Entwicklung der Batterieintegrationstechnologie
Der Ursprung der Technologie für Power-Battery-Gruppen geht auf die 1950er Jahre zurück und stammt aus der ehemaligen Sowjetunion und einigen europäischen Ländern. Diese Technologie wurde ursprünglich als Konstruktions- und Fertigungskonzept verwendet, um die physikalischen Ähnlichkeiten von Teilen (universelle Prozesswege) zu bestimmen und ihre effiziente Produktion zu etablieren.
Der Kern der Gruppentechnologie (GT) besteht darin, die Ähnlichkeiten verwandter Dinge in Produktionsaktivitäten zu identifizieren und zu untersuchen, ähnliche Probleme in Gruppen zu klassifizieren und relativ einheitliche optimale Lösungen zu suchen, um diese Gruppe von Problemen zu lösen und wirtschaftliche Vorteile zu erzielen. Im Bereich der Leistungsbatterien umfasst die Gruppentechnologie hauptsächlich die Technologie zur Integration von Batterien aus Einzelzellen in Batteriepacks (Packs), einschließlich Struktur, Wärmemanagement, elektrischem Verbindungsdesign und Batteriemanagementsystem-Technologie (BMS).
Die frühere Gruppierungstechnologie im Automobilbereich ist MTP (Module To Pack), was bedeutet, dass die Zellen zuerst in Module integriert werden und dann die Module in Packs. Diese Technologie zeichnet sich durch abnehmbare und austauschbare Module aus, die gut wartungsfreundlich sind, aber die Gruppierungseffizienz ist gering. Mit der Entwicklung der Technologie hat die Gruppierungstechnologie eine Transformation von MTP zu CTP (Cell To Pack) durchlaufen. CTP-Technologie bezieht sich auf die Technologie der direkten Integration von Zellen in Packs, wodurch die traditionelle Modulstruktur eliminiert und die Gruppierungseffizienz und Produktionseffizienz verbessert wird. In den letzten Jahren erforscht die Branche auch Gruppierungstechnologien wie CTC (Cell To Chassis), CTB (Cell To Body & Bracket) und MTB (Module To Body) mit höherer Integrationseffizienz.
Im Bereich der Leistungsbatterien und der elektrochemischen Energiespeicherung resultieren die wichtigsten technologischen Fortschritte bei Lithiumbatterien aus strukturellen und materiellen Innovationen. Ersteres dient der Optimierung der Struktur des „Zellen-Modul-Batteriepacks“ auf physikalischer Ebene, um das Ziel zu erreichen, sowohl die Volumenenergiedichte des Batteriepacks zu verbessern als auch die Kosten zu senken; letzteres dient der Erforschung von Batteriematerialien auf chemischer Ebene, um das Ziel zu erreichen, sowohl die Leistung einzelner Zellen zu verbessern als auch die Kosten zu senken. Dieser Artikel konzentriert sich auf die Auswirkungen verschiedener struktureller Integrationstechnologien auf die Herstellungstechnologie von Batteriepacks und die Richtung der innovativen Entwicklung aus der Perspektive der strukturellen Integration von Batteriepacks. Die aktuellen Schlüsseltechnologien für die Integration von Leistungsbatterien sind in der folgenden Abbildung dargestellt:
1-MTP wurde eliminiert
Zu Beginn der aktuellen Welle der Entwicklung von Elektrofahrzeugen wurden viele Modelle von Fahrzeugen mit neuer Antriebsart auf den Markt gebracht, die von Benzin auf Elektro umsteigen. Sie führen die räumliche Anordnung und das Design traditioneller Benzinfahrzeuge fort. Ingenieure haben ein relativ großes Batteriezellenmodul zusammengebaut, indem sie eine bestimmte Anzahl einzelner Batteriezellen in Reihe/parallel geschaltet haben, und dann mehrere solcher Batteriezellenmodule in das Batteriepaket eingesetzt, das das bekannte „MTP“-Batteriepaket ist. Da das Batteriepaket mehr als zweimal „verpackt“ werden muss, ist die Anzahl der erforderlichen Komponenten extrem groß, und das Batteriepaket erscheint als „drei Schichten innen und drei Schichten außen“, wobei zu viele redundante Teile mehr Systemvolumen und Gewicht einnehmen, was zu einer schlechten volumetrischen und gravimetrischen Energiedichte des „MTP“-Batteriepakets führt. Da bei der Konstruktion von Benzinfahrzeugen außerdem kein spezieller Platz für die Batterie reserviert wurde, kann das Batteriesystem nur „hineingequetscht werden, wo es passt“, was zu einer schlechten Produktwettbewerbsfähigkeit und Benutzererfahrung führt.
Seit der Einführung der neuen intelligenten Elektrofahrzeugplattformen von Tesla können bei reinen Elektrofahrzeugen die Akkus effizienter und regelmäßiger an idealen Stellen installiert werden, die drei elektrischen Systeme können sinnvoller angeordnet werden und die elektronische und elektrische Architektur sowie das Wärmemanagement des Fahrzeugs können effizienter integriert werden. Die Produktstärke des Fahrzeugs in Bezug auf Energieeffizienz, Ausdauer und Intelligenz wurde erheblich verbessert.
2-Ära der integrierten Technologie 2.0 – CTP
Der Akkupack mit MTP-Struktur weist ein erhebliches Platznutzungsproblem auf. Die Platznutzung der Batteriezelle zum Modul beträgt 80 %, die Platznutzung des Moduls zum Akkupack beträgt 50 % und die Gesamtplatznutzung beträgt nur 40 %. Die Hardwarekosten des Moduls machen etwa 14 % der Gesamtkosten des Akkus aus. Diese Struktur mit geringer Platznutzung kann die Entwicklungsanforderungen von Fahrzeugen mit neuer Energie nicht erfüllen. Im Rahmen der Integrationsidee Batteriezelle → Modul → Akkupack → Karosserie muss die Standardisierung jedes Integrationsschritts berücksichtigt werden, wenn das Fahrzeug so viel Leistung wie möglich in den begrenzten Fahrgestellraum laden und die Volumennutzung verbessern möchte. Da die Marktnachfrage nach Reichweite weiter steigt, nimmt das Volumen eines einzelnen Batteriemoduls weiter zu, was indirekt zur Entstehung der CTP-Lösung führt.
Die CTP-Strukturtechnologie wurde unter Berücksichtigung von Sicherheit, Verpackungskomplexität, Kostensenkung usw. entwickelt. Unter der Prämisse, die Sicherheit der Batteriezelle zu gewährleisten, reduziert die CTP-Technologie die Anzahl der internen Kabel und Strukturteile. Im Vergleich zur MTP-Technologie verfügt die CTP-Technologie über keine Modulstruktur und verpackt die Batteriezelle direkt in ein Batteriepaket, bevor sie im Fahrzeug installiert wird.
Derzeit gibt es zwei Hauptideen. Eine besteht darin, das Pack als komplettes großes Modul zu betrachten, das die Struktur mehrerer kleiner Module im Inneren ersetzt, wie es CATL vertritt; die andere besteht darin, beim Entwurf eine modulfreie Lösung in Betracht zu ziehen und die Batterie selbst als Leistungskomponente zu konstruieren, wie beispielsweise die Blade-Batterie von BYD.
Der Kernpunkt der CTP-Technologie besteht darin, das Moduldesign aufzuheben. Die Batteriezelle wird direkt mit der Hülle kombiniert, wodurch der Einsatz von Endplatten und Trennwänden reduziert wird. Die daraus resultierenden Probleme sind die Fixierung des Batteriepacks und das Wärmemanagement.
Tatsächlich war das ursprüngliche Produkt des CTP-Akkupacks kein reines modulfreies Design, sondern ein Design, bei dem die ursprünglichen kleinen Module zu drei großen Modulen und zwei mittleren Modulen zusammengeführt wurden, und an beiden Enden gab es außerdem Aluminium-Endplatten. Theoretisch handelt es sich also immer noch um MTP, aber es gibt tatsächlich große Verbesserungen in der Struktur.
Nach der Einführung von CTP 3.0 präsentierte CATL ein fortschrittlicheres Herstellungsverfahren, mit dem ein vollständig modulfreies Design erreicht wurde. Die Batteriezellen wurden von einer vertikalen Ausrichtung entlang der Höhe auf eine horizontale Position umgestellt. Zusätzlich wurde zwischen den Batteriezellen eine neue Kühllösung implementiert, die nicht nur Wärme ableitet, sondern auch Stütz-, Polsterungs-, Isolierungs- und Temperaturkontrollfunktionen bietet. Die Bodenschale wurde außerdem mit einer begrenzenden Fixierungsfunktion ausgestattet.
Abbildung 1: Vergleich zwischen CATL Kirin Battery CTP2.0 und CTP3.0
3-Ära der integrierten Technologie 3.0 – CTB, CTC
l CTB-Technologie
Die CTP-Technologie ist ein großer Fortschritt bei der Innovation der Batteriestruktur, hat jedoch keinen Durchbruch beim Batteriepack selbst gebracht. Bei der CTP-Technologie ist das Batteriepack immer noch eine unabhängige Komponente. Im Vergleich zur rationalisierten Strategie von CTP für Batteriepacks kombiniert die CTB-Technologie die Karosseriebodenplatte und die Batteriepackabdeckung zu einem. Die flache Dichtfläche, die durch die Batterieabdeckung, die Türschwelle und die vorderen und hinteren Träger gebildet wird, dichtet den Fahrgastraum mit Dichtmittel ab, und der Boden wird durch den Montagepunkt mit der Karosserie verbunden. Bei der Konstruktion und Herstellung des Batteriepacks wird das Batteriesystem als Ganzes in die Karosserie integriert, die Dichtungs- und Wasserdichtigkeitsanforderungen der Batterie selbst können erfüllt werden, und die Abdichtung der Batterie und des Fahrgastraums ist relativ einfach und die Risiken sind kontrollierbar.
Auf diese Weise wird die ursprüngliche Sandwichstruktur „Batteriepackabdeckung-Batteriezellenfach“ in eine Sandwichstruktur „in den Unterboden integrierte Batteriepackabdeckung-Batteriezellenfach“ umgewandelt, wodurch der durch die Verbindung zwischen Karosserie und Batterieabdeckung verursachte Platzverlust verringert wird. In diesem Strukturmodus ist das Batteriepack nicht nur eine Energiequelle, sondern nimmt als Struktur auch an der Kraft und Übertragung des gesamten Fahrzeugs teil.
Abbildung 2: Schematische Darstellung der CTB-Technologiestruktur
l CTC-Technologie
Nach der Anwendung der CTC-Methode ist das Batteriepaket nicht mehr eine unabhängige Baugruppe, sondern Teil der Fahrzeugkarosserie. Dies optimiert das Produktdesign und die Produktionsprozesse, reduziert die Anzahl der Fahrzeugteile, insbesondere die internen Struktur- und Verbindungselemente der Batterie. Dadurch wird ein angeborener Vorteil in Bezug auf das Gewicht erreicht, was die Raumausnutzung maximiert und Platz für eine Erhöhung der Batteriezahl sowie eine Verbesserung der Reichweite schafft. Unter der Bedingung, dass die Technologie des elektrochemischen Systems unverändert bleibt, kann die Reichweite durch die Erhöhung der Batteriezahl gesteigert werden.
Abbildung 3: Strukturdiagramm der Tesla CTC-Technologie
Tesla und andere Automobilhersteller haben beispielsweise sukzessive Modelle mit CTC-Technologie auf den Markt gebracht. Auf Zellebene können sie multifunktionale elastische Sandwichstrukturen und großflächige Wasserkühlungstechnologie verwenden und die durch integrierte Entwicklung entstandene Technologie zur Kollisionsvermeidung auf der Unterseite des Batteriepakets überlagern, wobei Gruppierungseffizienz, Wärmeableitung und Sicherheit berücksichtigt werden und die Anwendung der CTC-Technologie aus den beiden Dimensionen Zelloptimierung und Schutz der Fahrzeugstruktur gefördert wird. Auf der Ebene der integrierten Fahrzeugentwicklung wird die Batteriezelle direkt in das Fahrgestell integriert, wodurch die Verbindung von Modulen und Batteriepaketen entfällt. Die Integration der drei großen elektrischen Systeme (Motor, elektronische Steuerung, Batterie), der drei kleinen elektrischen Systeme (DC/DC, OBC, PDU), des Fahrgestellsystems (Getriebesystem, Antriebssystem, Lenksystem, Bremssystem) und der Module für autonomes Fahren wird realisiert, und die Leistungsverteilung wird optimiert und der Energieverbrauch durch den intelligenten Power Domain Controller reduziert.
4-Änderungen der spezifischen Anforderungen an Batteriekästen für CTP-, CTB- und CTC-Technologien
In der traditionellen Akkupackstruktur übernimmt das Akkumodul die Aufgabe, die Akkuzelle zu stützen, zu fixieren und zu schützen, während der Akkukastenkörper hauptsächlich die äußere Extrusionskraft trägt. Die Anwendung der CTP-, CTB- und CTC-Technologien bringt neue Anforderungen an Akkukästen mit sich, die sich insbesondere in Folgendem widerspiegeln:
Die Festigkeitsanforderungen an den Batteriekastenkörper werden verbessert: Da die Modulverbindung in den CTP-, CTB- und CTC-Strukturen reduziert oder eliminiert wird, muss der Batteriekastenkörper nicht nur der externen Extrusionskraft standhalten, sondern auch der Expansionskraft der Batteriezelle, die ursprünglich vom Modul getragen wird. Daher sind die Festigkeitsanforderungen an den Batteriekastenkörper höher.
Kollisionsschutzfähigkeit: Nachdem die Seitenträger des Akkupacks mithilfe der CTP-Technologie entfernt wurden, ist der Akku der Aufprallkraft des Aufpralls direkt ausgesetzt. Daher muss der CTP-Akkupack über eine ausreichende Kollisionsfestigkeit verfügen.
Anforderungen an Isolierung, Wärmedämmung und Wärmeableitung: CTP- oder CTB- und CTC-Strukturen ändern das Bodenplattenprofil in eine wassergekühlte Platte auf Basis des Chassis-tragenden Strukturkastens. Der Batteriekasten trägt nicht nur das Gewicht der Batteriezellen, sondern bietet auch Wärmemanagement und andere Funktionen für die Batterie. Die Struktur ist kompakter, der Herstellungsprozess ist optimiert und der Automatisierungsgrad ist höher.
Reduzierte Wartungsfähigkeit: Das hochintegrierte Design erschwert den Austausch des Akkupacks. Beispielsweise sind die Akkuzellen in der CTC-Struktur mit Harzmaterial gefüllt, was den Austausch der Akkuzellen erschwert und eine Reparatur nahezu unmöglich macht.
5- Auswirkungen der Batteriepackintegration auf die Ladeinfrastruktur für Elektrofahrzeuge
Die Wahl unterschiedlicher Akku-Integrationstechnologien impliziert auch die Wahl unterschiedlicher Kompensationsmethoden. CTP neigt dazu, die Akkus auszutauschen, während CTB/CTC, das stärker integriert ist, zum Schnellladen tendiert.
Hohe Integration bedeutet, dass mehr Batterien auf demselben Raum untergebracht werden können, wodurch die Reichweite von Elektrofahrzeugen erhöht wird. Benutzer müssen für kurze Strecken möglicherweise nicht mehr häufig aufladen, sondern bevorzugen für lange Fahrten möglicherweise schnelles Aufladen. Daher muss die Planung der Ladeinfrastruktur diese Änderungen berücksichtigen, um sicherzustellen, dass sie den Benutzeranforderungen gerecht wird.
Mit der zunehmenden Integration von Akkupacks können sich die physikalische Größe und Struktur der Akkupacks ändern, was sich auf das Design der Ladeschnittstelle und die Kompatibilität der Ladeausrüstung auswirken kann.
Darüber hinaus kann die zunehmende Integration von Akkupacks auch die Ladegeschwindigkeit und -effizienz beeinträchtigen. Um einen schnellen und sicheren Ladevorgang zu gewährleisten, müssen möglicherweise effizientere Batteriemanagementsysteme und Ladetechnologien entwickelt und eingesetzt werden.
Wir werden regelmäßig Informationen und Technologien zu Wärmedesign und Leichtbau aktualisieren und mit Ihnen teilen. Vielen Dank für Ihr Interesse an Walmate.