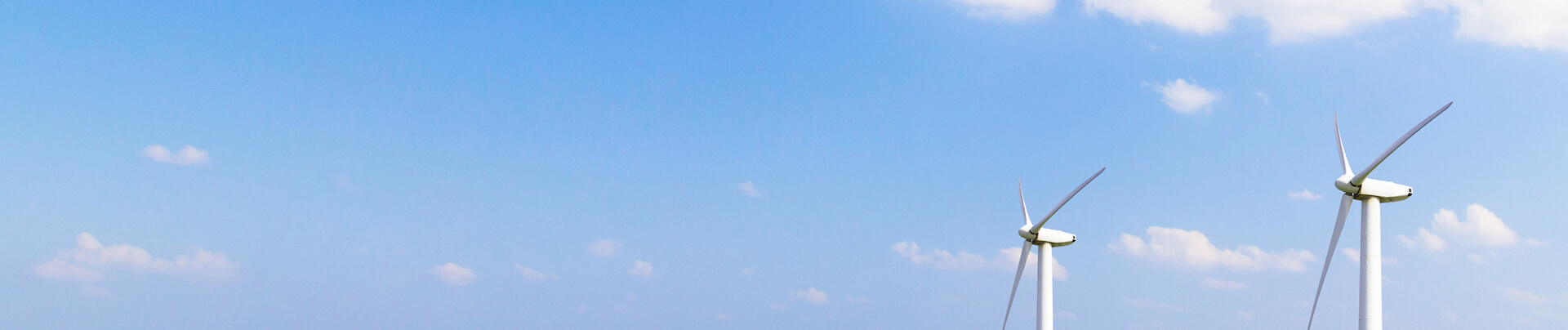
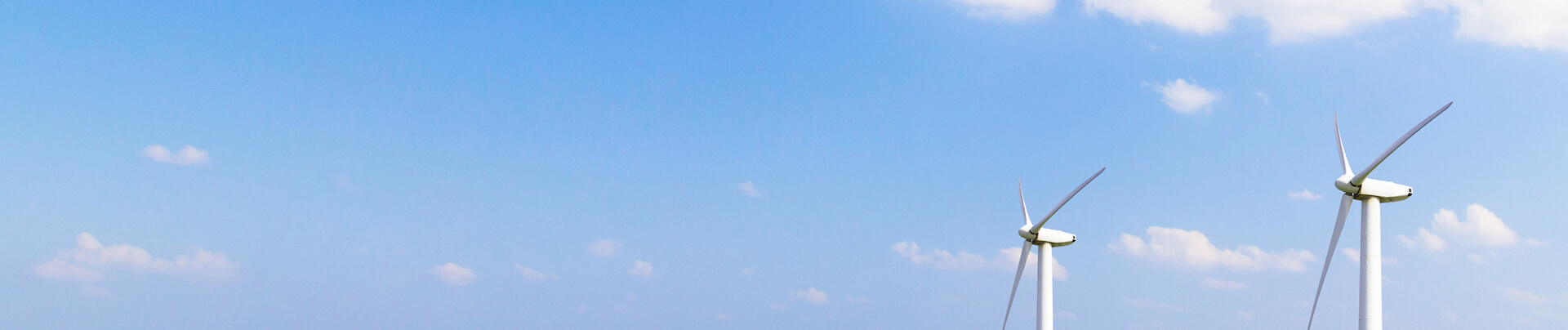
当前新能源汽车开发的3大重点——安全性、轻量化、可靠性,都与电池包密切相关,而电池壳体是电池系统的承载元件,对电池包乃至整车的碰撞、能耗等产生重大影响。
新能源汽车电池包结构
1. 电池包的安全性
作为新能源汽车三电系统中最核心的部件,电池包直接影响着新能源汽车的主要性能指标,其安全性往往决定着整车的可靠性。新能源汽车电池包在碰撞时存在巨大安全隐患,碰撞变形会引发内部电池模组出现诸如短路、断路、常发热、爆炸等现象,而电池包壳体的抗碰撞性能直接影响电池模组的安全性。
电池包安全性设计的关键在于降低碰撞过程中电池包的损伤程度,所以优化整车碰撞传力路径和提升电池包壳体的防护效果是设计的关键。当前仿真技术被广泛应用,通过建立
了电池包仿真模型,预测在碰撞、挤压、冲击、跌 落等工况的失效形式,系统优化电池包壳体结构、零件尺寸,进行电池包安全性多目标优化用以提升安全性。
2. 电池包的轻量化
高强钢、超高强钢、铝合金、复合材料的应用,是实现新能源汽车轻量化必要环节。由于电池包上壳体不起保护和支撑用,仅起到密封防尘作用,上壳体主要使用钢板、铝合金、复合材料。而电池包下壳体在电池系统主要起承载整个电池质量、抵御外部冲击,保护电池模组的作用。电池包下壳体主流制备工艺有:挤出铝型材+焊接成型、冲压铝板+焊接成型、压铸铝+铸造成型。当前,挤出铝型材+焊接成型是国内企业普遍采用的下壳体制造方案,因其较冲压铝制下壳体,制备难度更低,较压铸铝制下壳体,成型尺寸更大。
由于新能源汽车电池包与底盘处于高度重合区域,所以底盘和电池包结构的集成优化,对新能源汽车轻量化十分重要。
CTP技术,一般电池包由电芯组装成为模组,再把模组安装到电池包里省略中间模组环节,直接将电芯集成在电池包上,电池包作为整车结构件的一部分集成到车身地板下。CTP技术有效提升了电池包的空间利用率和能量密度,以及电池包的整体刚度。
CTC技术,是CTP技术的进阶版,直接将电芯集成在地板框架内部,将电池包壳体作为地板上下板,座椅直接与电池包上盖连接,空间利用率达到 63%。
CTB 技术,是 CTC 的改良版,保留了横梁结构和座椅支撑部分,仅部分底板被电池包上盖代替,空间利用率提高至66%,并且车身结构较完整,安全性更高。
电池包装配模式
3. 电池包的可靠性
电池包壳体从服役到疲劳失效的全过程为:在循环载荷作用下,壳体表面开始出现细微裂纹,局部微小的疲劳裂纹逐步扩展,最终发生零件的瞬间断裂失效。尤其,电池包壳体的连接接头部位是高疲劳失效区域。对电池包壳体进行实验仿真,优化成为提升电池包可靠性设计的一般途径。
按照行业要求,电池包壳体的密封性需要达到IP6K7等级,甚至某些企业需要达到IP6K9K 等级。由于电池包壳体密封长度较长,一般多达数米,且密封设计结构较少,所以对其密封性要额外注意。
我们会定期更新有关热设计与轻量化的技术与资讯,与您分享,供您参考,感谢您对迈泰的关注。