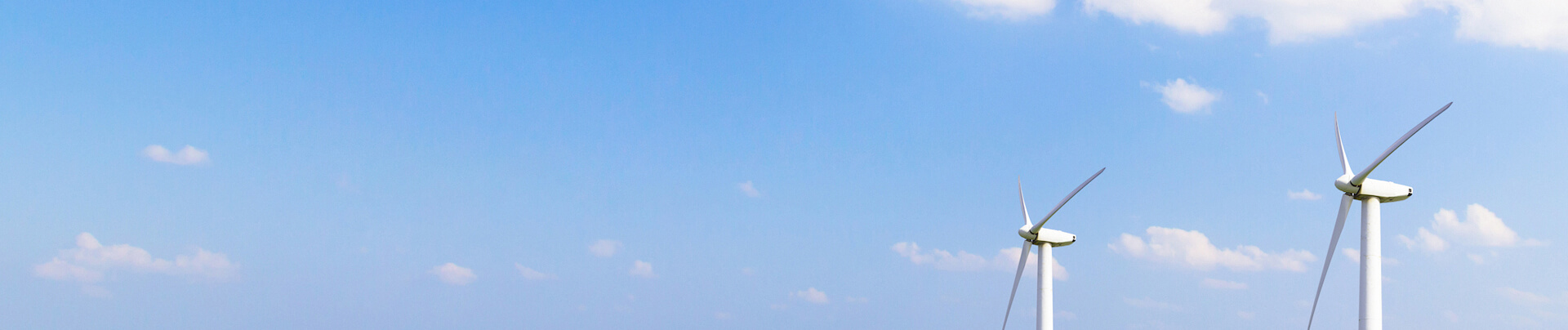
目标并竭力推动您的项目效益提升
目前比较流行的水冷头,基本上采用纯铜微通道型。铜底板直接进行铲齿加工,鳍片与底板一体,减少热阻。底板与盖板之间则采用钎焊或者扩散焊的方式,确保密封的可靠性。
下篇:铲齿工艺加工水冷头主要成本构成
1-铲齿工艺制造水冷头的优势
l 一体化设计:铲齿工艺可以将地板和鳍片进行一体化加工,有利于减少接触热阻,提升热传导性能。此外一体化的底板和鳍片设计还可以提升结构强度。
l 高精度加工:铲齿工艺可以加工出非常精细的齿片结构,齿高、齿厚和齿距可以精确控制,这使得散热鳍片密度更高,散热面积更大,进而更高效散热。同时也能更好的满足不同客户对形状、尺寸等个性化的需求。
l 生产效率高,铲齿工艺可以批量生产,与传统的CNC相比,铲齿工艺可以同时加工多个齿片,大大提高了生产效率。
图1:不同加工工艺的水冷头底座 a-铲齿 b-CNC c-冷锻
2-铲齿工艺水冷头成本构成
l 设计与开发成本:铲齿工艺水冷头的设计复杂度较高,尤其是在散热性能要求较高的情况下,需要进行复杂的工艺设计和优化。
l 材料成本:铲齿工艺中使用的材料主要是铝和铜合金。铝板与铜合金结合的设计方式在散热器制造中较为常见,且性价比较高,因此铝和铜的质量直接影响成本.
l 加工工艺成本:
铲齿工艺成本:铲齿工艺涉及高精度的数控加工设备,如三轴线轨数控机床。这种设备的使用需要较高的投入成本,同时对操作人员的技术要求也较高,这些都会增加生产成本。
焊接工艺成本:在水冷头的制造过程中,焊接工艺也是一个重要的成本因素。真空钎焊和扩散焊是两种常用的焊接方法。钎焊可以同时焊接多个接头、生产效率高,需要钎料,对工艺条件的要求较,质量控制难度大;扩散焊设备一次性投资较大,扩散焊不需要填料,但对工件表面的加工要求高。
表面处理成本:常见的表面处理方式有阳极氧化、镀层处理等。对于铝合金水冷头,阳极氧化处理可以提高表面硬度、耐磨性和耐腐蚀性,同时增加产品的美观度;对于铜质水冷头会进行镀层处理,如镀镍等,以防止铜的氧化和腐蚀,提供产品的使用寿命和可靠性。
l 其他成本:检验检测、包装运输等。
3-成本优化建议
l 优化材料使用:
选择合适的材料:如,铜的导热系数高,单密度大,单价高;铝的质量轻,单价低,导热系数稍差。
材料用量:通过精确计算材料厚度和余量,确保材料的高效利用,减少材料浪费。
图2:材料用量计算示意
l 优化生产流程
简化模具:设计简单的模具,减少模具的复杂度和成本。
减少废品率:通过精确的工艺控制和质量检测,减少废品率。
一次成型:优化工艺路线,减少多次加工工序,提高生产效率。
我们会定期更新有关热设计与轻量化的技术与资讯,与您分享,供您参考,感谢您对迈泰的关注。
水冷头作为液冷散热系统的关键部件,其设计需兼顾换热性能、结构强度、防腐蚀性、防泄漏性以及成本控制等多方面因素。水冷头内部通常设计有复杂的换热槽结构(即流道),其内部流道设计的优劣直接决定了整个系统的换热效率。
中篇:水冷头设计、加工工艺及挑战
1-不同场景对水冷头的设计要求
l 高性能计算:
高性能计算设备(如高性能CPU、GPU等)在运行过程中会产生大量热量,因此需要水冷头具备高效的散热能力。为了应对高热流密度散热需求,水冷头通常采用高密度微流道设计,以增大换热面积,提高散热效率。此外,一些设计将水冷头直接集成到CPU上,省去了涂抹硅脂的步骤,不仅简化了组装过程,还进一步提升了散热性能。可靠性方面,水冷头必须具备出色的密封性能,以防止泄漏,确保长期稳定运行。
l 显卡散热:
显卡是高热量产生区域,因此需要水冷头具备全覆盖设计,以确保显卡上各个发热部件均能得到有效散热。同时,显卡散热对冷却液的流量要求较高,需要水冷头内部结构设计支持高流量通过,以便快速带走热量。
l 数据中心:
在数据中心中,水冷头的结构设计需要满足高效散热、低噪音、高可靠性、适应高功率密度、智能化管理和环境适应性等多方面的要求,以确保数据中心的稳定运行和高效散热。
2-水冷头结构演化趋势
水冷头结构设计的演化趋势体现了技术创新和性能提升的双重追求,主要体现在以下几个方面:
l 散热性能提升:
增大接触面积:一些水冷头设计通过增加与发热元件的接触面积,提高散热性能。如,采用大面积铜底座设计,可以实现良好的接触和热传导。
优化内部结构:对内部水道进行优化,一种思路以优化流体流动为目标,如,由普通Fin片改为转向Fin片风格,呈现长条形流道,促进流动边界层分离,减少边界层厚度,提升热交换效率;另一种思路以增大热容面积为目标,如,从传统的粗水道向微流道设计转变,显著提高了冷却液与底板的接触面积,增强了散热效率。还有些设计中通过导流板将冷却液喷射至微水道底板,提升局部流速和乱流,大幅提高吸热效率。
l 集成化和智能化设计:
一体化设计:通过一体化设计将水泵、散热鳍片、导热底座等部件集成到一起,减少连接点,提高系统稳定性和散热效率。
多功能集成:除了散热性能,现代水冷头还具备温显、监测功能。
模块化设计:通过组合式扣具结构,提高组织的便利性和自由度。
图1:不同Fin厚水冷头底座
l 高性能材料和表面处理:
采用纯铜底座等高性能材料,结合镀镍等表面处理技术,提升导热效率和抗腐蚀性能。
3-加工工艺及挑战
l 材料特性影响加工:
材料硬度与韧性问题:不同材质的散热器,如铜、铝及其合金,硬度和韧性不同,对加工刀具和工艺的要求也不同。硬度较高的材料,刀具磨损加快,需更频繁地更换刀具;韧性好的材料,切削时易产生变形和毛刺。
铜铝复合材料加工复杂:铜铝复合材料铲齿散热片,需先采用连续铸造半熔态压制成型技术制成复合材料,再进行铲齿加工,工艺流程更复杂,对设备和工艺的精度要求更高。
l 尺寸精度要求高
齿高齿厚一致性难保证:对于一些高密齿散热器,其要求每个齿的高度和厚度都高度一致,以确保散热片的性能和均匀性。若齿高齿厚差异过大,会导致热传递不均匀,影响散热效果。加工过程中,需使用高精度设备和自动化控制系统,才能确保每个齿的规格一致。
齿间距控制难度大:散热片上的齿过于密集时,其密度和间距使得加工过程更加复杂,加工设备需具备更高的速度和精度,才能保持齿的均匀性。例如,当齿间距过小,刀具在切削时容易产生干涉,影响加工精度和表面质量。
l 表面质量要求严格
毛刺问题:加工过程中易产生毛刺,这不仅影响散热器的美观度,还可能阻碍空气流动,降低散热效果。毛刺的产生可能由材料切削精度低、加工工具刀具磨损等原因引起,需采取相应的去毛刺工艺来解决。
表面粗糙度:散热器的表面粗糙度影响其散热性能和后续的表面处理效果。过高的表面粗糙度会增加空气流动的阻力,降低散热效率,还需进行额外的表面处理来降低粗糙度,增加了加工成本和时间。
l 加工设备与工艺要求高
设备精度与稳定性:铲齿加工需要高精度的铲齿机,设备的精度直接影响齿的尺寸精度和表面质量。同时,设备需具备良好的稳定性,以保证长时间加工过程中尺寸的一致性。
刀具选择与磨损:合适的刀具对加工质量至关重要。刀具的材质、几何参数等需根据材料特性进行选择。加工过程中,刀具磨损会导致切削力增大、尺寸精度下降和表面粗糙度增加,需及时调整或更换刀具。
进给速度与切削深度:进给速度和切削深度的不合理设置,易导致加工缺陷。如进给速度过快,切削深度过大,会使刀具承受过大负荷,出现抢刀、弹刀、掉刀等现象,影响加工精度和表面质量。
图2:铲齿工艺
l 定制化需求高
不同的应用场景对散热器的尺寸、形状、齿高、齿厚、齿间距等参数有不同的要求,需根据具体需求进行定制化设计和加工。这要求加工厂家具备灵活的工艺调整能力和丰富的经验,以满足多样化的定制需求。
我们会定期更新有关热设计与轻量化的技术与资讯,与您分享,供您参考,感谢您对迈泰的关注。
随着全球人工智能算力的迅猛增长,以及芯片热设计功耗(TDP)的持续攀升,数据中心的冷却需求正面临前所未有的挑战。与此同时,全球范围内节能降碳政策的日益严格,进一步推动了冷却技术的革新。在这一背景下,传统的风冷方案已逐渐难以满足高效散热与节能的双重要求,液冷技术因其卓越的散热性能和显著的节能优势,正迅速崛起,成为数据中心冷却方案的主流选择。服务器作为数据处理和存储的核心设备,其性能与稳定性直接关系到整个系统的运行效率。服务器的核心组件——包括主板、CPU、内存、硬盘和显卡等——在持续高负荷运作下会产生大量热量,若不能及时有效地散热,将严重影响服务器的性能和寿命。为此,先进的液冷系统被引入到服务器散热解决方案中,直接安装在主要热源如CPU和显卡上,以显著提升散热效能。
上篇:水冷块结构及工作原理
液冷系统的核心部件之一是水冷块,它通常由高导热性的铜或铝材料制成,设计有精密的水道和散热片结构。这些水冷块紧密贴合在CPU、GPU等热源表面,通过内部流通的冷却水迅速吸收并转移热量。随后,热量被输送至散热片,通过水冷系统的循环,最终将热量散发到周围空气中。
图1:主流芯片制造商芯片热功耗趋势
1-常见水冷块类型及特点
l 微通道水冷头
特点:微通道水冷头采用精密的微小水道设计,水道结构细密且复杂,能够显著增加冷却液与发热部件的接触面积,从而大幅提升散热效率。微水道设计还能够在冷却液流动过程中产生强烈的湍流效应,进一步增强对流换热系数,实现高效的热量转移。
应用场景:特别适用于高发热量的CPU和GPU,尤其在高性能计算、超频以及数据中心等对散热要求极高的场景中表现卓越。
l 大流量水冷头
特点:大流量水冷头的内部结构相对简单,通常采用铜板或蚀刻凹槽设计,制造成本较低。其核心优势在于依靠高速水流快速带走热量,适合搭配大流量的水冷系统使用。虽然结构简单,但其高效的散热能力使其成为性价比极高的选择。
应用场景:适用于对散热效率有一定要求但预算有限的场景,例如中高端的DIY电脑系统或中小型服务器集群。
l 喷射型水冷头
特点:喷射型水冷头通过导流板将冷却液从狭小的喷嘴高速喷射到微水道底板上,形成强烈的湍流效应,显著提升散热效率。这种设计不仅增加了冷却液与底座的接触面积,还通过高速流动进一步优化了热交换性能。
应用场景:适用于高性能CPU和GPU,尤其在高散热需求和高流量场景中表现突出,例如超频计算、人工智能训练以及图形渲染等领域。
2-水冷块一般结构
水冷块是一个内部留有水道的金属块,通常由铜或铝制成,与CPU、显卡或其他发热不见接触,其结构设计直接决定了散热性能的优劣,典型的水冷块通常由以下几个关键部分构成:
l 底座,通常由高导热材料,如铜或铝合金,表面经过精细加工,以确保与发热部件的紧密接触。底座内部设有复杂的流道设计,以增加冷却液与底座的接触面积。
l 盖板,与底座一起形成流道密封腔,保护水冷块内部的流道、密封等组件,防止灰尘、杂质和外界物理损伤。
l 进出水口,进出水口是冷却液进出水冷头的接口,一般设计在水冷头侧面或顶部,要确保冷却液能够顺利的流入流出,其位置设计需要考虑流体的流动路径,以减少流阻,提高冷却液流动速度。
l 扣具,扣具是将水冷头牢固地固定在CPU或其他发热部件上,确保紧密基础,实现高效热传导。
图2:水冷块典型构造
3-散热性能综合优化
l 流道设计优化
增加流道接触面积:通过设计更窄、更密集的流道,可以显著增加冷却液与底座的接触面积,从而提高对流换热系数。例如,微水道设计通过其细密的水道结构,微通道水冷块的设计参数(如通道宽度、高度、间距)对其散热效率具有决定性影响:随着通道宽度的减小,换热系数显著增加,得益于窄通道内冷却液流动的湍流效应增强,从而提高了热交换效率;较高的通道高度有助于增加冷却液的流动空间,从而提升换热性能;较小的通道间距能够增加冷却液与热源的接触面积,从而提高散热效率。
还可以通过优化流道布局及减少流道弯道进行优化:合理的流道布局能够确保冷却液均匀覆盖发热部件的表面,减少局部温差。而流道中的弯道会增加水头损失和内部流阻,从而降低冷却效率。在设计中应尽量减少弯道数量,若无法避免,则需将弯道设计为圆滑过渡,以降低压降并优化流动性能。
l 高导热材料:水冷块的底座通常采用纯铜或铝合金等高导热材料,这些材料能够高效地将热量从热源传导至冷却液,从而提升整体散热性能。
l 结构参数优化,如:底座基板厚度、Fin片、扰流结构等。基板厚度的增加会导致最高温度上升,因此在设计中需要在散热效果与结构强度之间找到最佳平衡点;通过增加肋片的高度、厚度和间距,可以提升散热性能,但同时也会增加流阻,找到最佳的肋片设计组合,从而实现散热性能的最大化。扰流柱的形状能够有效增强湍流效应并提升热交换效率。
我们会定期更新有关热设计与轻量化的技术与资讯,与您分享,供您参考,感谢您对迈泰的关注。
本文从生产实际出发,总结了搅拌摩擦焊焊接过程中常见的问题、产生原因及改善方法,供大家参考。
1-表面缺陷
(1)表面沟槽
l 问题描述:表面沟槽又称犁沟缺陷,通常出现在焊缝的上表面,偏向于焊缝的前进边,呈沟槽状。
l 产生原因:焊缝周围的热塑性金属流动不充分,焊缝的塑性金属无法充分填充搅拌针行进过程中留下的瞬时空腔。
l 改善方法:增大轴肩直径,增大压力,降低焊接速度。
图1: 沟槽
(2)飞边毛刺
l 问题描述:飞边毛刺出现在焊缝的外边缘,呈波浪形。
l 产生原因:旋转速度和焊接速度的匹配不当,下压量过大。
l 改善方法:优化焊接参数,减少下压量。
图2:飞边毛刺
(3)表面起皮
l 问题描述:表面起皮或起丝呈皮状或丝状出现在焊缝的表面。
l 产生原因:大量的金属摩擦产热积累于焊缝的表层金属,使得表层的局部金属达到熔化状态。
l 改善方法:优化焊接参数,降低转速,提高焊速度。
图3:表面起皮
(4)背部焊瘤
l 问题描述:在焊缝的背面形成焊瘤。
l 产生原因:焊接过程中搅拌头的深度和压力控制不当。
l 改善方法:优化搅拌头的深度和压力设置。
2-内部缺陷
(1)未焊透
l 问题描述:焊缝底部未形成连接或者不完全连接而出现的“裂纹状”缺陷。
l 产生原因:搅拌针长度不足,导致焊缝下部的材料未能充分搅拌。
l 改善方法:选择合适的搅拌针长度,确保焊缝厚度上的材料能够被充分搅拌。
图4:未焊透
(2)孔洞
l 问题描述:焊缝底部未形成连接或者不完全连接而出现的“裂纹状”缺陷。
l 产生原因:焊接过程中,由于摩擦热量输入不够,使达到塑化状态的材料不足,造成不充分的材料流动,导致焊缝区未完全闭合的。
l 改善方法:优化焊接参数,改进搅拌针设计,控制焊接速度和转速。
图5:孔洞
我们会定期更新有关热设计与轻量化的技术与资讯,与您分享,供您参考,感谢您对迈泰的关注。
近段时间,小编注意到多家企业都在关注和布局浸没式液冷储能,浸没液冷技术在沉寂一段时间后再次受到关注,似乎又有“变火”的趋势,相信很多同行也都在关注这一进展。
1-浸没式液冷技术特点
储能电芯走向300+Ah、储能系统纷纷走向5MWh+,电芯越大产热越多、越难散热、越难保证温度一致性,并且储能系统由大量电芯堆叠组成,运行工况复杂多变,更容易造成产热不均、温度分布不均。散热、均温的问题若不能妥善解决,会导致电池的充放电性能、容量和寿命的下降,影响整个系统的性能。此外,安全一直是悬在锂电储能头上的“达摩克利斯之剑”,而提升安全的最普遍做法是向本征安全、主动安全、被动安全三个维度进发。
浸没式液冷是将电芯浸没在在一种绝缘、无毒、可散热的液体中,冷却液具有更高的导热率和比热容,这种直接的接触方式在提供极高的热传递效率的同时,也能够提高更好的均温性。并且,冷却液在作为温度控制的介质外,还可以作为储能系统消防液使用,使得温度控制与消防合二为一,也是浸没式液冷技术的显著特点。浸没式液冷在面对更高散热性能、更强安全性要求的产业背景下,无疑会更具优势。
图1:浸没式液冷储能电池Pack箱
2-浸没式液冷储能系统方案
浸没式液冷技术作为液冷技术一个分支,并非储能行业首创,最初是在高性能计算领域得到应用的,后来逐渐扩展到数据中心、人工智能、加密货币等。
浸没式液冷储能系统的设计初衷是为了解决传统风冷和间接液冷在冷却效率和电池温差控制方面的不足。南方电网梅州宝湖项目正式投运标志着浸没式液冷这一前沿技术在新型储能工程领域的成功应用。
l 冷却方式及冷却液循环方式
冷却方式分为单相和相变两种方式,采用单相浸没液冷,主要包括矿物油、硅油、天然酯等。而另一些方案则采用两相浸没液冷,以氢氟醚为主要代表,利用相变潜热进行散热,提高散热效率。据不完全统计,当前发布的浸没式液冷储能系统中以“单相浸没冷却”的方案居多。
据冷却液的循环方式的差异,在单相浸没液冷又有三条技术路线:自然对流、泵驱动、浸没式耦合冷板式液冷。自然对流利用液体受热后体积膨胀、密度减小的特性,实现热冷却液的上浮和冷却后的下沉,从而完成循环散热;泵驱动系统的核心是液冷机组驱动冷却液在液冷管路及电池浸没箱之间循环流动,完成整个循环散热过程;而浸没式耦合板式液冷的方案中,电池浸没在介电流体中,与介电流体接触的冷板用来带走热量,避免使用复杂的二次回路来冷却介电流体。
l 产品形态与集成方案
浸没式液冷储能系统的集成方案迭代是一个从整体到局部、再到细节的过程,每一步都在前一阶段的基础上进行优化和改进,以实现更高的性能和安全性。
从舱级到Pack级,系统集成技术呈现出场景定制特点。储能场景的多元化使得对储能系统的需求各一,单一产品与无法满足市场需求,模块化设计使得储能产品可以根据项目的规模和电力需求进行优化和扩容,允许根据不同的应用场景和需求快速调整和部署储能解决方案。
3-产业化进程中的挑战及落地场景
浸没式液冷储能系统在商业化过程中面临经济性、技术复杂性、市场接受度、产业链成熟度等多方面的挑战。
l 技术复杂性:相较于冷板式液冷系统,浸没式液冷系统的设计和实施更为复杂。
l 产业链成熟度:浸没式液冷技术的产业链尚未完全成熟,这限制了其在更广泛领域的应用。产业链的成熟度直接影响到技术的推广和商业化进程。
l 经济性挑战:在当前储能行业仍处于商业化发展的初期阶段,盈利性不足使得高成本的技术路线难以受到市场青睐。许多企业在为了一时订单而进行低价竞争,导致浸没式液冷的渗透率受到限制。
当前,储能行业的主要市场仍以风冷和冷板式液冷为主,浸没式液冷尚未完全被市场所接受。尽管浸没式液冷技术的市场渗透率与接受度不高,但在一些特殊的场景下可能展现不出可观的潜力,比如:
l 危化品行业:危化品企业对于储能设备的安全管控极为严格,因为其生产和存储的化学品大多具有高度易燃、易爆、有毒或腐蚀性,一旦发生事故,不仅会对企业自身造成严重损失,还可能引发环境污染和对周边社区造成危害。
l 基站、数据中心:基站、数据中心对热失控容忍度低,数据中心储能系统需保证性能稳定、不易发生热失控的电池,以确保系统的安全性。对电能质量的要求高,需要储能系统具有快速的响应能力,在电网发生故障或停电等紧急情况先,储能系统需能够直接切换至放电模式,以保证电力的连续性和稳定性。
l 快充电站:高倍率充放电时,电池在短时间内产生大量热量,会导致电池温度过高和温度不均,对电池的性能、寿命和安全性构成威胁,就意味着高倍率充放电场景下,电池的热管理变得尤为重要。
我们会定期更新有关热设计与轻量化的技术与资讯,与您分享,供您参考,感谢您对迈泰的关注。
电池包的气密性是电动汽车及储能系统中至关重要的指标,电池包的气密性检测主要针对电池包壳体、接口、连接件、冷却组件等进行检测,以保证电池包内部不受外界环境的灰尘、水气等杂质污染或侵入,冷却组件不发生漏液,确保电池包维持正常的性能和寿命,不发生短路或爆炸等安全事故。
1-电池包的防护等级与气密性检测标准的制定
国际防护等级认证(International Protection Making,IEC60529),也称作异物防护等级或IP代码(IP Code)。IP(Ingress Protection)防护等级系统是有国际电工委员会(IEC)制定的,用于对电气设备外壳对异物侵入和水侵入的防护等级进行分类的标准。电池包箱体的气密等级通常要求达到IP67或IP68,这就意味着电池包箱体需要完全防止灰尘进入(防尘等级6),并且能够在一定压力的水中浸泡一段时间,外壳进水量不致达到有害程度(防水等级7),更严格的要求电池包在1m深的水下浸泡60min而无水进入(防水等级8)。IP防护等级通常由两位数字组成,数字越大,表示防护等级越高,见图1:
图1:IP防护等级说明示意
为了确保电池包IP67、IP68的要求,电池包需要进行沉水测试,此方法耗时较长,对动力电池包具有破坏性,且具有一定的安全风险,并不适合作为动力电池的下线检测。因此使用气密检测来保证电池包满足IP67、IP68的要求成为行业通用做法。气密检测标准的制定需要考虑压降值与泄漏率之间的关系,以及孔径与漏水的关系。气密性检测标准制定时涉及从理论极端到实验验证的一系列步骤,以实现IP等级到气密性检测标准的转换。如,以IP68为例:
图2:气密检测标准制定步骤
2-气密性检测方法选择及检测难点分析
电池包设计和制造质量是影响气密性的关键要素,包括电池箱上盖的韧性和强度、电池包壳体、接口和连接件等部位的密封及防爆透气阀、电气接插件本身的密封性等。此外,使用过程中也会带来一些问题影响气密性,如:热膨胀收缩问题、材料老化及振动冲击影响等。在电池包壳体生产制造中我们更关注焊点和接头质量等问题造成的气密不良,比如焊点不均匀、不牢固或存在裂缝、气隙,接头连接部位密封不良等。
电池包气密性检测主要分为上壳体、下壳体、总装件的气密性测试,上下壳体的气密性测试必须满足总装后的气密性泄漏要求。选择电池包气密性测试方法时,一般会综合考虑电池包的特性、测试精度要求、生产效率以及成本等因素。
工程中电池包壳体测试一般会分为制程气密检测、出货气密检测。并且上下壳体的气密性测试必须满足总装后的气密性泄漏要求,对检测标准提出了更严格的要求。要保证气密性满足要求,实操中必须克服以下困难:
l 产品结构稳定性:焊缝的质量,包括塞块焊缝、水嘴焊缝、横梁焊缝、边框底板焊缝、边框前后封板焊缝等,焊缝漏气问题主要集中在起弧、收弧处及因烧穿导致的不良等;焊接变形应力造成的开裂,如底板腔体侧壁焊接、底板腔体材料分层,无法承受焊接变形应力等。
l 气密工装的适配性与稳定性:工装设计应紧密贴合被测件的外形和尺寸,确保在检测过程中被测件能够稳固的固定在工装上,减少因为位置偏移或晃动导致的测试误差。然而,实际上电池包尺寸和形状差异较大,就需要设计和制造多种不同的测试工装,增加成本和操作复杂性,如果设计一种通用型工装,这又会加大设计复杂度。
l 气密性检测结果的可重复性:气压、温度、测试工件/夹具的干燥状态等因素都会影响气密检测结果。
l 对于工件存在较多不贯穿的微小裂纹,受检测设备精度、检测参数等因素的影响,可能存在泄漏源未能发现,出现漏检现象。
图3:气密检测工装
3-工程中常用的电池包气密检测方案组合
电池包壳体制程气密测试一般会做气密性试验和浸水试验,在气密性试验中,电池箱上盖被密封,只留一个插接件口作为进气口。通过控制气压并观察是否漏气来判断电池包的气密性。而浸水试验则是将整个电池箱体完全浸入水中,通过检查箱体内是否浸水来判断其气密性。
氦气检漏法是一种利用氦气作为示踪气体,通过检测泄漏点的氦气浓度来实现泄漏检测的技术。当氦气进入被检测设备的内部或外部可能存在泄漏的部位时,如果存在漏孔,氦气会迅速通过漏孔进入或逸出系统,并被质谱仪检测到。氦气检漏法的检测效率较高,尤其是在检测微小泄漏方面。
图4:泄露检测方法比较
在实际生产中,通常会结合多种检测方法以提高检测效率和准确性。例如,氦气检漏法适用于高精度和微小泄漏检测,而压差法则具有高精度和快速响应的特点。此外,传统的水检法虽然检测精度低,但是直观且成本低,是定位泄漏点的便捷方式。
我们会定期更新有关热设计与轻量化的技术与资讯,与您分享,供您参考,感谢您对迈泰的关注。
储能液冷Pack的液密潜在失效会涉及多个方面,如:泄漏、腐蚀和沉积、冷凝水等故障模式。
1-流体互联及组成
在储能液冷系统中,流体互连负责在各个组件之间传输冷却液,通过有效的流体互连,确保冷却液在系统中的高效循环,从而带走电池充放电过程中产生的多余热量。
密封性良好的系统可以有效防止冷却液的泄露,泄漏不仅会导致冷却液的损失,需要频繁补充,还会影响系统的散热性能和稳定稳定性,在储能中冷却液泄露还可能会造成电池短路,引发安全问题。
2-流体互连系统液密设计
流体互连系统的液密设计是确保系统在各种操作条件下保持密封性和防止流体泄露的关键环节。
图1:储能液冷系统典型部署
(1)分析系统中可能的泄漏源与风险点:
l 液冷组件的自密封性,如,在液冷流道系统与Pack箱一体设计中,部件通过焊接进行连接,焊接质量缺陷,焊合不良、气孔、裂纹等,都可能导致渗液问题。
l 结构设计不合理,如液冷箱的定位孔或螺纹孔距离流道过近,焊合不良的部位容易成为渗液的通道。
l 连接部位:液冷系统的管道连接、阀门和接头等部位是常见的泄露点,若连接结构设计不合理或制造工艺不精良,接头内部存在微小缺陷,冷却液也可能从这些缺陷处泄漏出来。
l 由于安装不当、材料老化或损伤等原因导致的泄露。
(2)密封结构设计:
l 液冷PACK使用干湿分离式冷板冷却方式,在正常工作情况下,电芯与冷却液无接触,可保障电芯正常工作。储能液冷箱一种方案是通过挤压工艺成型,流道直接集成在冷板上,然后机械加工打通冷却循环路径。在这个过程中,选择合适的焊接工艺是确保密封性的重要步骤。具体详见《储能用下箱体拼焊工艺设计》。
l 液冷管路主要用于连接液冷源与设备之间、设备之间、设备与管路之间的过渡软(硬)管连接。主要连接方式有:
快插连接:储能液冷系统的连接方式之一是采用VDA或CQC快插连。
螺纹连接:连接结构的两端均滑动连接有管道,内螺纹圈与螺纹套的螺纹连接,增加了连接的牢固性。
限位管和螺母连接:管道一端卡接有连接管路,连接管路两侧固定安装有限位管,限位管内部固定安装有橡胶垫圈和凸圈,连接管头表面开设有限位圈槽,限位管顶部转动连接有螺母,通过螺纹与限位管进行转动连接。
密封圈连接:螺纹套的内壁通过强力胶粘附有密封圈,密封圈的内壁与管道的外表面活动连接,以防止使用过程中漏液。
(3)PACK液冷板、舱内接口、舱内管路等,均考虑在常用冷却液、常用温度、流速条件下的长期防腐蚀,可保障长时间工作不出现腐蚀。操作条件对液密性的影响:
l 温度。高温影响,随着温度的升高,液体的粘度通常会降低,这可能导致液体的密封性能下降,从而影响液密性。例如,某些密封材料在高温下可能会发生变形或老化,导致泄漏。低温影响,在低温环境下,液体可能会变得粘稠,增加了流动的难度,但也可能提高密封材料的性能,从而在一定程度上增强液密性。
l 压力。 高压环境,在高压下,液体的密度和粘度可能会增加,从而提高液体的密封性能。然而,过高的压力也可能对密封材料造成损坏,导致泄漏。低压环境,在低压下,液体的密封性能可能相对较弱,特别是如果密封材料本身存在缺陷或老化,更容易发生泄漏。
l 流速。高流速,液体在高速流动时,可能会对密封面产生较大的冲击力,导致密封材料的磨损或变形,从而影响液密性。低流速,在低流速下,液体的密封性能相对较好,但这也可能掩盖一些潜在的密封问题,如微小的材料缺陷。
3-腐蚀与沉积问题
l 堵塞对秘密性的影响:
冷却液中的颗粒物、沉淀物或微生物生长都可能导致管道内部堵塞,影响冷却液的流通性,进而降低冷却效率。
污垢和结垢:冷却液中的矿物质在长时间运行后可能会在管道内壁形成沉积物,即所谓的“水垢”;也可能会因为固体颗粒沉淀、结晶、腐蚀或微生物活动而形成污垢,这些污垢会堵塞管道和冷板,增加流动阻力,降低传热效率。
泡沫问题:液冷系统中可能会产生泡沫,泡沫会附着在冷板表面,导致传热效果下降,并可能增大系统运行中的阻力,对泵造成气穴腐蚀等,损坏设备。
l 涡流对气密性的影响:
当流体在管道或缝隙中流动时,速度变化会导致涡流产生,特别是在流体经过狭窄部分或障碍物时,涡流更容易形成。流体的粘度和密度也会影响涡流的产生。粘性较高的流体更容易形成涡流,而密度较大的流体可能减弱涡流的形成。
泄漏通道:涡流会在接触表面形成旋涡,这些旋涡可能会在缝隙或不规则表面形成微小的泄漏通道,从而导致气体或液体的泄露。
表面磨损:涡流流动会导致接触表面磨损,特别是在高速流动的情况下,这种磨损会进一步降低气密性,因为磨损的表面更容易形成新的泄漏通道。
热效应:涡流流动会产生热量,这可能会导致接触面材料的变形或热膨胀,从而影响气密性,特别是在温度变化较大的系统中。
4-冷凝水问题
在某些条件下,液冷管路可能会形成冷凝水,这可能会导致设备损坏或效率降低。保温失效:如果管道的保温材料破损或老化,会导致热量散失,影响冷却效果。特别是在低温环境下,保温失效会使管道表面结霜或结冰。冻裂:在寒冷环境中,如果没有采取适当的防冻措施,管道内的冷却液可能会冻结,导致管道破裂。
解决方案
l 密封措施:确保液冷管路的进/出水管口完全封堵,防止外界潮湿空气进入电池舱。
l 除湿设备:安装除湿空调或使用除湿功能,维持电池舱内的湿度在合适范围。
l 温度控制:通过安装空调或通风系统,控制储能柜所在环境的温度和湿度,例如将温度保持在20-25摄氏度,相对湿度控制在40%-60%。
l 隔离措施:对空着的电池架进行简易隔绝,防止湿气进入装有电池簇的舱室。
我们会定期更新有关热设计与轻量化的技术与资讯,与您分享,供您参考,感谢您对迈泰的关注。
储能Pack的全密封设计是确保其安全性和长期稳定运行的关键,密封本质上是用一种装置来密闭(密封)一个缝隙或使一处接合不漏流体(气体或液体)的。全密封计设能够有效防止电池单元内的液体和气体泄漏,这对于保证储能系统的安全和稳定运行至关重要。因此,设计时既要考虑气密性也要保证液体介质的密封性。
储能Pack密封设计在实际操作中需要综合考虑材料、工艺、检测设备、环境条件以及制造过程中的多个因素,以确保其密封性能能达到预期标准。本文从Pack箱体气密、液冷循环液密及液冷工质等方面阐述储能Pack密封设计在实际工程的应用实践及注意要点。
上篇:储能Pack箱体气密性设计
密封设计有助于维持储能Pack内部的温度和压力稳定,这对电池的正常工作和性能发挥起到关键作用;并且密封设计可以减少外界环境对电池内部的影响,比如湿气、尘埃和其他污染物等,从而提高系统的可靠性和使用寿命。此外,采用合适的密封材料和结构可以有效提高密封件的耐磨性和抗老化性能,增强整个储能系统的耐久性,减少维护成本。
气密设计的一般思路是通过箱体结构分析,找出可能存在泄漏的重点区域,然后针对不同区域具体性能、功能需求采取针对性的措施。
1-箱体结构分析
箱体不仅是电池模组、电气件等的物理载体,更是整个储能系统安全、可靠运行的重要保障,是储能Pack的“骨架,一般由上盖、下箱体、支撑组件、密封件及螺栓等组成。
图1:储能pack箱体示意图及密封设计重点关注区域(如,红色箭头标注)
如上图,找出潜在泄漏点可能出现区域:
l 多个零件连接处,如:箱体上盖与下箱体装配界面、高低压连接器与箱体安装界面、外露器件与电池箱体安装接口等。
l 如果采用螺栓固定连接,安装固定处亦可能存在泄漏风险,如,电气接口与箱体前面板安装界面。
l 箱体的上盖、下箱体不能出现漏洞、缝隙,确保箱体的密封性和防护性能。
图2:浸没式液冷下箱体(钣金边框+铝型材液冷底板)
2-上盖与下箱体安装界面密封设计
上盖一般可以分为平板式和异型式两种,它们的结构特点也各不相同,比如SMC复合材料、铝制,无论是何种材质,为了减少自密封结构的复杂性,电池壳的上盖通常采用整体式设计。此外,上盖的开孔要求也应符合接口的要求,并且应将其独立于密封界面,以减少对电池包密封的影响。上盖密封设计一般遵循以下原则:
l 采用一体式零件设计,避免分件设计,确保上盖“自密封”性能的稳定。
l 定位孔、定位特征设计在上盖边缘(上盖和下托盘密封界面外侧)。
l 上盖与下箱体密封界面,需要匹配面满足“均匀”、“连续”的密封要求。
目前储能Pack下箱体主流方案有:钣金箱体+液冷板、压铸箱体+液冷板、型材一体式箱体、压铸一体式箱体等,其中型材一体式箱体与其他方案对比,具备流道承重能力好、开模成本较低等优点,应用广泛。焊接工艺的选择对密封性能影响很大,对于不同材料、厚度的焊件,选择合适的焊接方法能有效提升焊缝的质量,以保证系统的整体强度和密封性能。
另外,下箱体密封设计应当遵循如下密封原则:
l 采用封闭截面型材进行框架的搭建,接头处采用自密封的线性连接技术,如CMT焊接技术。
l 铝型材拼接的电池托盘需要设计有连续的一道或多道密封胶体。
l 下箱体集成液冷板的情况下,需要考虑使用胶体密封或采用自密封的线性连接技术,如FSW搅拌摩擦焊技术。
l 上盖与下箱体密封界面,需要匹配面满足“均匀”、“连续”的密封要求,必要时进行机加工对密封界面进行打磨处理。
图3:箱体上盖与下箱体常见密封形式
通常,储能Pack箱上盖下箱体采用折弯翻边加密封垫设计,见图2。利用紧固螺栓使上盖、下箱体与密封垫充分压实耦合,保证Pack箱满足IP67的相关要求。
3-电气、通信接口与下箱体前面板安装界面密封设计
箱体前面板(如图3),在挤出成型的型材上进行机加工开孔,用于安装电气、通信等接口,实现电流传递、通讯交互、安全控制等功能。
图4:电气、通信接口与下箱体前面板安装界面
箱体与电气、通信等接口安装界面气密性遵循以下原则:
l 接口形状设计成流线型以减少气体和液体在接口处的积聚和渗透可能性。
l 精确对位,避免接口在安装时错位导致的缝隙。
l 安装前对接口进行预密封处理,增加防震垫或密封胶,以增强初始密封效果或减少因振动导致的密封失效。
另外,紧固件的选择方面,使用高强度、高扭矩的紧固件,并在安装过程中进行多次紧固,以确保接口的紧密性。如使用碰焊螺母,其特点是能够直接连接与被连接件(箱体前面板)的壁孔进行碰焊,这种结构设计能够显著提高连接部位的气密性。
图5:使用碰焊螺母增加气密性
4-密封件选择
密封件设计和选择至关重要,因为它们直接影响到系统的可靠性和使用寿命。以下是在设计和选择储能液冷系统密封件时应考虑的关键因素:
l 密封材料必须有一定的化学、压力兼容性,同时能够耐受系统工作温度范围,包括高温和低温环境。密封件的材料选择取决于使用环境和使用寿命要求。常见的密封件材料包括橡胶、聚四氟乙烯(PTFE)、尼龙、金属等。
l 泄漏自由度:密封件必须能够适应系统在工作过程中可能出现的微小变形,以确保在各种工况下均保持良好的密封效果。一般密封垫的变形量要大于30%,小于60%,密封界面压力大于30kPa。
我们会定期更新有关热设计与轻量化的技术与资讯,与您分享,供您参考,感谢您对迈泰的关注。
在纯电动汽车中,电池包的重量约占整备质量的30%左右,电池包轻量化,对于提升整车续航里程有着重大意义。因此,对电池包高比能量的研究是新能源汽车目前的主要研究方向之一,也是实现电动汽车轻量化的主要途径,实现动力电池包轻量化可从两个方向开展:提高单体电芯的能量密度,对电池包相关辅件进行优化设计。
多材料轻量化电池包开发旨在通过采用多种轻质材料,降低电池包的重量,提高能量密度和续航里程,同时保证安全性和可靠性。电池Pack各主要部件中,质量最大的是电芯本体,其次为Pack下箱体、上盖、BMS集成部件等。
1-电池包上盖轻量化
电池箱的上盖位于动力电池箱体的上方,不受动力电池箱体侧面的影响,也不会影响整个电池组的质量,其功能主要包括密封、保护等作用。为了提高整车能效,在设计中也会考虑轻量化,采用轻质材料,如铝合金、复合材料(SMC、FRP等),可以显著减轻电池包的重量。
此外,上盖的结构设计还需要考虑制造效率和批量化要求,在结构非常异形的情况下,采用冲压成型或折弯拼焊可能较为困难。上盖的设计还需要考虑到与下箱体、密封结构件等其他部件的连接与配合,确保整个电池箱体的结构稳定性和可靠性。
2-电池包下壳体轻量化
铝合金是电池包壳体制作的理想材料,因其密度低、比强度高、热稳定性好、耐腐蚀性强、导热性好、无磁性、成型容易以及回收价值高等诸多优点。常用的铝合金材料包括6061-T6、6005A-T6和6063-T6等,这些材料具有不同的屈服强度和抗拉强度,可以满足不同的结构需求。
电池包壳体通常由铝合金型材边框和底板构成,采用6系铝合金挤压型材拼焊而成。设计时需要考虑型材断面大小及复杂性、壁厚等因素,以适应不同的结构和功能要求。例如,边框、中间隔板、底板、横梁等部件可能会采用不同的断面设计。
通过合理的结构设计和连接方式,可以有效保证壳体整体强度,降低加工难度,实现壳体减重:
l 薄壁化:通过采用薄壁设计,配合加强筋来满足强度要求,可以有效减轻材料重量。
l 中空化:在结构设计中引入中空部分,以降低材料密度。
l 尺寸优化:优化电池包的尺寸,减少不必要的材料使用。
l 拓扑优化:通过优化电池包内部组件的布局,减少材料占用空间。
l 集成模块化设计:将冷却板、电池包吊耳等部件集成在箱体中,减少单独部件的数量和重量。
3-制造轻量化技术
l 材料成型
目前电池箱材料成型工艺主要有三类:冲压、铝合金压铸和铝合金挤压成型。动力电池箱整体工艺流程包括材料成型及连接工艺,其中材料成型工艺是动力电池箱体的关键工艺。当前上壳体以冲压为主,下壳体主要工艺为挤压成型及铝合金压铸成型两种方式。
l 连接技术
电池箱体连接工艺在新能源汽车制造中至关重要,涉及多种技术和方法,以确保电池箱的结构强度和密封性。
焊接是电池箱体加工中的主要连接工艺,应用广泛。主要包括以下几种方法:
①传统熔焊:如TIG(钨极惰性气体保护焊)和MIG(金属惰性气体保护焊)。TIG焊接速度低,质量高,适用于点固焊和复杂轨迹焊接,常用于边框拼焊和边梁小件焊接。MIG焊接速度高,熔透能力强,适用于边框底板总成内部整圈焊接。
②搅拌摩擦焊:通过摩擦产生热量实现焊接,具有接头质量好、生产效率高等特点。
③冷金属过渡技术:适用于薄板材料,焊接过程无热输入,减少变形。
④激光焊:高精度、高速度,适用于复杂结构焊接。
⑤螺柱焊和凸焊:用于特定部位的快速连接,螺柱焊通过螺柱和螺母实现紧固,凸焊则通过凸点压紧实现连接。
机械连接方式主要解决薄板材料在焊接中的易焊穿和螺纹滑牙问题,包括:
①拉铆螺母:用于箱体边框密封面和内腔底板的连接,具有紧固效率高、使用成本低等优点。适用于薄板与其他部件的螺纹联接。
②钢丝螺套:用于加强铝或其他低强度机体的螺孔,提高螺钉的承载能力和螺纹的受力分布,适用于电池模组安装孔和密封面安装孔。相对于拉铆螺母,钢丝螺套强度更高且易于修复,但一般不适用于薄壁安装。
我们会定期更新有关热设计与轻量化的技术与资讯,与您分享,供您参考,感谢您对迈泰的关注。
要应对大跨度、快迭代、丰富产品线等市场需求,还要保证降本增效保质,对汽车行业而言,通过产品标准化——造车平台化无疑是项不错的策略,通过电池平台化为不同的车型匹配同一个电池包方案,或者匹配由同一种电芯组成且结构相近的电池包方案,这就意味着尽可能的多零件通用化,可以缩短开发周期、节约成本、精简产线与提高生产效率。
一、电池平台化
电池平台化方案有利于产品的统筹规划、成本的降低和产能的优化。根据整车平台的电池平台化策略,需要考虑平台各车型需求的交集与带宽,用尽量少的电池与电池方案兼容尽可能多的车型。在纯电动项目的架构开发中,合理布置集成动力电池包是至关重要的,具体工作要素包括电量与动力性能需求、碰撞安全、布置位置与空间等。
1-空间尺寸边界与电芯标准化
l 电池包可用布置位置
目前主流的动力电池布置位置为地板下方,包含前座椅下方、后座椅下方、中通道位置及脚踏位置。这种布置方式能够最大限度的获得可用面积,并且有助于降低车身重心、提高整车操纵稳定性和优化碰撞传力路径。
图1:电动车发展过中电池包布置位置
l 电池包空间布置形式演化
分体式电池包:采用分体式的电池包空间布局形式,如江淮同悦系列,能量模块由两个电池包组成,一个放在原来油箱位置,一个放在车尾箱存放备胎位置。
此外,工程师们在燃油车原来架构上不断发掘可利用空间,电池包布局出现了“工”字形、“T”字形、“土”字形的形式。
此类设计是在传统燃油车基础上做较小的改动,空间非常有限,能够装载的电池包体积和重量都很受限,因此容量也很难提升,续航里程不高。
一体式电池包:这是一种全新的产品设计思路,整车设计围绕核心零部件——电池包展开,将电池包进行模块化设计,平铺在车辆底盘上,以最大限度获得可用空间。
l 电池包安装点布置
合理布置电池包至关重要,限制要素设计离地间隙、通过性、碰撞安全和电量需求等诸多方面。
图2:电池包尺寸设计约束
整车平台需定义平台内各车型的类别、级别与定位,进而确定了车辆的大小、轴距,整车布置根据整车空间分解出电池包在X、Y、Z方向的尺寸包络,电池需要在整车给定的包络内进行布置,保证整车各系统间不出现干涉,而整备质量指标可分解出电池包的系统质量要求。
在电池尺寸这一指标上,动力电池包的设计绕不开整车空间、整备质量等硬性参考指标,这就意味着电芯的设计存在阈值,受到这个阈值的约束,电芯尺寸就会往某个特定的区间进行集中,如:方形电芯长度范围150-220mm,宽度范围在20-80mm,高度范围在100mm左右徘徊。电芯尺寸规格的变化趋势正是造车平台化与电池标准化相辅相成的结果。
然而,各车企电池平台策略、承载车型及对标准化的理解也有所差别,致使当前所呈现出来的产品方案仍有较大差异。如比亚迪的标准化策略是全面更换刀片电池,刀片电池的尺寸标准锁定为960*13.5(14)*90(102)mm,单体电压3.2/3.3V。
2-续航边界与电池电量方案开发
动力电池为整车行驶提供能量:电池容量、放电深度、能量密度影响可供电量。为满足不同车型的需求,车型的电耗差异成为重要关注项目,车辆的续航里程会受电驱、电池、整备质量、风阻、机械阻力、低压电耗及能量回收等因素的影响。电耗差别大的车型间共用电池方案的可能性弱,就需要针对性的开发个性化的电池电量方案,包括电池尺寸、质量、电量及做功率性能优化,以满足续航性能的要求。
在造车平台纯电续航里程的约束下,电池需求净放电量会受不同车型电耗的影响,需要确认平台各车型的电耗分布,才能进一步将该电耗带宽转化为电池的需求电量分布,进而确定平台所需电池电量方案。
3-动力性能边界
整车的动力性包括不同SOC、不同环境温度下的加速工况、等速工况和保电工况下的动力表现,对应到电池的变量就是电池在不同SOC和温度下的功率-电压特性,电池的功率对应整车动力系统的功率要求,电压对应驱动电机的额定电压需求。
一般对整车平台电池方案评估从常温高电量下的百公里加速时间及其电池指标分解,逐步延伸到全域全工况的电池指标分解。
二、电池箱体开发
1-电池集成与模块化
优化电池模块的设计,提高电池组的集成度和模块化,减少非活性组件,提升电池组的能量密度。
当前流行的电池包集成技术有CTP、CTB、CTC等各种形式,零件的外形、材质和组合形式等都伴随集成技术的进步发生了改变,整体方向是一体化、集成化,通过减少独立零件数量、使用一个大零件替代几个零件,形成尺寸更大、功能更多的组件。
2-电池箱体方案设计
电池箱体是动力电池系统总成的载体,对产品的安全运行和防护起着关键作用,直接影响整车的安全性。电池箱体的结构设计主要包括电池箱上壳体、下壳体等部件的壳体材料选择,制造工艺方案选择等。电池箱体上盖主要起密封作用,受力不大;电池箱体下箱体是整个动力电池系统产品的承载件,电池模组主要布置在下箱体里面,因此电池箱体内部要有嵌槽、挡板等结构措施,使电池模组在车辆行驶的状况下可靠固定,在前后、左右、上下各个方向上均不发生窜动,避免对侧壁和上盖造成冲击,影响电池箱体寿命。
图3:电池下箱体方案,a-蒙皮框架、 b-FSW焊接+围框、c-FSW焊接+围框
l 电池包安装点结构设计与连接固定
电池包安装点通常采用安装梁结构,这种结构前后贯通,前端与前舱纵梁连接,形成有效、连贯的封闭梁结构,并根据电池包重量分布,合理布置安装点。电池包与整车的固定方式包括螺栓固定、机械固定+胶接混合连接、卡扣连接等。
图4:电池包布置与安装断面
动力电池包一般通过多个吊耳结构安装至整车上,吊耳处理要承受动力电池包自身较大的自重外,还要承受汽车行进时带来的路面激励,如石块路和深坑等,此类耐久工况和误用工况对吊耳结构的强度提出更高的要求。
图5:不同吊耳连接方案:a焊接吊耳 b铝挤边框吊耳
l 电池箱体安全与保护结构
机械强度和防护:电池箱体应具备足够的机械强度,以确保其内部电池免受机械撞击和冲击。电池箱体需要能够承受振动、挤压和机械冲击等,以确保在各种条件下电池的安全性。
碰撞保护:电池箱体的设计必须考虑碰撞安全性,特别是针对侧向碰撞和底部碰撞的情况。通常采用铝制或钢制材料,并通过外框架连接到下部托盘,以提供结构刚度并增强碰撞能量吸收能力。此外,还应设计适当的碰撞吸收结构,以防止电池外壳变形和电池单元损坏。
防水防尘和防腐蚀:电池箱体需要具备防水防尘功能,通常采用IP67级别的密封胶垫来保证气密性能。此外,还应考虑防腐蚀措施,如在外部喷涂PVC涂层以增强耐腐蚀性。
防爆和泄压设计:当电池发生爆炸时,应通过平衡防爆阀等装置使能量集中定向泄放,避免进入客户舱。此外,还应采取防爆措施(如部分破坏结构)以防止设备整体破裂。
l 密封设计
电池箱体上盖与下箱体之间密封面的设计对密封性起重要作用,其设计需要配合电池箱体结构和密封圈一起设计。密封面应尽可能保持在同一个平面,避免出现较多的曲面结构。由于上盖和下箱体是通过螺栓连接,所用螺栓数目较多,因此保证孔的同轴度尤其重要,需在合理布置螺栓孔位置的同时,位置尺寸尽量圆整,且在X、Y向呈对称布置。连接螺栓数目的选择需根据密封性高低和拆装工作量大小两方面综合考虑。
图6:上下箱体密封设计方案,1-电池上盖 2-密封垫 3-电池下盖 4-金属导管
l 电气安全和短路保护
连接可靠性:电池箱体内的连接器应具有正确的极性连接,确保电池箱体的过流能力和电气/机械连接的可靠性,包括放松措施等。
电气绝缘耐压设计:模组设计采用双重绝缘防护电芯本身有一层电芯蓝膜及电芯顶帖片可以满足绝缘耐压要求,端/侧板与电芯间、电芯与底部安装面间设置绝缘耐压防护。
l 热管理设计
电池热管理开发贯穿于电池包系统设计开发全周期,包含电池温度控制、冷板、管路系统等的设计。电池热管理系统设计的主要目标是在考虑空间布置、设计成本、轻量化等条件下,通过加热或冷却控制,保证电池系统工作在相对适宜的工作温度,同时减小单体间温差,保证一致性。
我们会定期更新有关热设计与轻量化的技术与资讯,与您分享,供您参考,感谢您对迈泰的关注。
电池包是新能源汽车的核心能量源,为整车提供驱动电能。我们一般会从效率(能量密度)、安全、制造及维修成本等维度评价电池包技术的优劣。
在电池设计中,单个电芯的电压只有3-4V左右,而电动车所需的电压最低都要100V以上,现在的新车甚至有700V/800V的电压,输出功率一般也在200W,所以就需要给电池升压。为了满足电动车的电流和电压需求,就需要将不同的电芯通过串联、并联组合的方式相连。
电池包是将电芯、电子电气系统、热管理系统等通过电池框架结构——底板(托盘)、框架(金属框)、上盖板、螺栓等包络构成的,一直以来,如何将这些部件、系统更高效更安全的“打包”成为一个整体,是整个行业持续不断研究探索的议题。
上篇:电池集成技术创新与发展
动力电池成组技术的由来可以追溯到20世纪50年代,起源于前苏联与欧洲等一些国家。这项技术最初是作为一种工程和制造理念,用于确定零件的物理相似性(通用工艺路线),并建立其有效生产。
成组技术(Group Technology, GT)的核心在于通过识别和发掘生产活动中有关事物的相似性,将相似的问题归类成组,寻求解决这一组问题的相对统一的最优方案,以取得经济效益。在动力电池领域,成组技术主要涉及将电池由单体集成为电池包(Pack)的技术,包括结构、热管理、电连接设计和电池管理系统(BMS)技术。
汽车领域较早的成组技术为MTP(Module To Pack),即先由电芯集成为模组,再由模组集成为Pack。这种技术的特征是模组可拆卸和更换,具有较好的可维护性,但成组效率较低。随着技术的发展,成组技术经历了从MTP到CTP(Cell To Pack)的转变,CTP技术指将电芯直接集成到Pack的技术,取消了传统的模组结构,提升了成组效率和生产效率。近年来,行业还在探索更高集成效率的CTC(Cell To Chassis)、CTB(Cell To Body & Bracket)和MTB(Module To Body)等成组技术。
在动力电池及电化学储能领域,锂电池主要的技术进步来源于结构创新和材料创新,前者是在物理层面对“电芯—模组—电池包”进行结构优化,达到兼顾提高电池包体积能量密度与降低成本的目的;后者是在化学层面对电池材料进行探索,达到兼顾提高单体电池性能与降低成本的目的。本文注重从电池包结构集成视角探讨不同结构集成技术对电池包制造技术的影响及创新发展方向,当前动力电池集成关键技术,见下图:
1-已被淘汰的MTP
在当前这波电动汽车发展潮流的伊始,很多油改电新能源车型上市,它们延续传统油车的空间布局与造型设计,工程师们将一定数量的电芯单体通过串/并联的方式,组成一个相对较大的电芯模组,然后再将几个这样的电芯模组布置到电池包中,也就是我们熟悉的“MTP”电池包,由于电池包需要“打包”两次以上,因此需要的零部件数量十分庞大,电池包也以“里三层外三层”的形象示人,过多冗余部件也占据更多的系统体积空间和重量,使得“MTP”电池包在体积能量密度、质量能量密度表现差;并且因为燃油车设计过程并没有专门为电池预留空间,电池系统只能“见缝插针”地塞进车内,产品力低下,用户体验欠佳。
自以特斯拉为代表的全新智能化电动车平台推出以后,原生纯电动车使得电池包以更高效、规整的安装在理想的空间位置上,三电系统可以更合理的布局,整车的电子电器架构及热管理设计实现更高效的集成,车辆的能效、续航、智能化维度的产品力极大加强。
2-集成技术2.0时代——CTP
MTP结构的电池包存在显著的空间利用率问题,电芯对模组的空间利用率为80%,模组对电池包的空间利用率为50%,整体空间利用率仅为40%,模组硬件费用约占电池电池总成本的14%,这种低空间利用率结构无法满足新能源汽车的发展要求。在电芯→模组→电池包→车身集成思路的框架下,整车想要在有限的底盘空间内尽可能装载更多电量,提高体积利用率,就要考虑每个集成步骤的标准化,随着市场对续航里程需求的不断攀升,单个电池模组的体积不断增大,间接带动了CTP方案的出现。
出于安全、封装复杂程度、降本等方面的考虑,CTP结构技术应运而生。在保证电芯安全的前提下,CTP技术减少了内部线缆和结构件,相比MTP技术,CTP技术没有模组结构,直接由电芯封装成电池包再安装到车上。
目前主要有两种思路,一是将Pack看成是一个完整大模组替代内部多个小模组的结构,以宁德时代为代表;二是设计时即考虑采用无模组方案,以电池本身作为强度的参与件去设计,例如比亚迪刀片电池。
CTP技术的核心点就是取消了模组设计,电芯直接与壳体相结合,减少了端板与隔板的使用,随之而来的问题是电池组的固定以及热管理问题。
实际上CTP电池包的最初产品并非是纯无模组的设计,而是将原有的小模组合并为3个大模组和2个中模组的设计,并且两端同样存在铝制端板,所以理论上依然是MTP,但结构上确有很大的进步。
而到CTP3.0之后,宁德时代给出了更为先进的制造方式,实现了彻底的无模组设计,电芯从原来的沿高度方向立置改为侧置,同时提盒电芯间采用了全新的冷却方案,除却散热外,冷板还承担了支撑、缓冲、隔热、温控等多种功能;底壳也做了限位固定设计。
图1:宁德时代麒麟电池CTP2.0与CTP3.0对比
3-集成技术3.0时代——CTB、CTC
a. CTB技术
CTP技术是电池结构创新的一大进步,却没有突破电池包本身,在CTP技术中,电池包仍然是一个独立的零部件,相较于CTP对电池包的精简策略,CTB技术把车身底板面板与电池包上盖合二为一,电池上盖与门槛及前后横梁形成的平整密封面,通过密封胶密封乘员舱,底部通过安装点与车身组装。在设计制造电池包的时候,把电池系统作为一个整体与车身集成,电池本身的密封及防水要求可以满足,电池与乘员舱的密封相对简单,风险可控。
这样将原来的“电池包上盖-电芯-托盘”的三明治结构转化成“车身底板集成电池包上盖-电芯-托盘”的整车三明治结构,减少了因车身与电池盖连接而产生的空间损失。这种结构模式下,电池包不仅仅是能量源,同时也作为结构体参与整车的受力与传力。
图2:CTB技术结构示意
b. CTC技术
采用CTC方式后,电池包不再是一个独立的总成,而是融合为车身的一部分,优化了产品设计和生产工艺,减少整车零件数量,特别是减少了电池内部结构件与连接件,具备轻量化的先天优势,最大程度提升空间利用率,为增加电池数量、提升续驶里程提供了空间。在电化学体系本身技术不变的条件下,能够通过提升电池数量增加续驶里程。
图3:特斯拉CTC技术结构示意
如,特斯拉等车企先后推出CTC技术车型,在电芯层面可采用多功能弹性夹层结构、大面积水冷技术,叠加一体化开发带来的电池包底部防撞击空间复用技术,兼顾了成组效率、散热性和安全性,从电芯优化和整车结构防护两个维度,推进CTC技术的应用。在整车一体化开发层面,将电芯直接集成到底盘,省去模组和电池包的环节。实现大三电系统(电机、电控、电池)、小三电系统(DC/DC、OBC、PDU)、底盘系统(传动系统、驾驶系统、转向系统、制动系统)以及自动驾驶相关模块的集成,并通过智能化动力域控制器优化动力分配和降低能耗。
4-CTP、CTB和CTC技术对电池盒的具体要求变化
在传统电池包结构中,电池模组起到支撑、固定和保护电芯的作用,而电池盒箱体主要承受外部的挤压力。CTP、CTB和CTC技术的应用对电池盒的提出新的要求,具体体现在:
电池盒箱体强度要求提升:由于CTP或CTB及CTC结构中减少了或取消了模组环节,电池盒箱体不仅要承受外部的挤压力,还需要承担原本由模组承担的来自电芯的膨胀力,因此对电池盒箱体的强度要求更高。
碰撞防护能力:利用CTP技术去除电池组的侧梁后,电池将直接承受碰撞的影响,因此CTP电池组需要具备足够的抗碰撞能力。
保温、绝缘和散热需求:CTP或CTB及CTC结构在底盘承载式结构箱体的基础上,把底板型材更改为水冷板,电池盒箱体不仅要承载电芯重量,还要为电池提供热管理等功能,结构更加紧凑、制造工艺优化、自动化程度较高。
维修性便利性降低:高度集成度设计使得电池包的更换变得复杂,如在CTC结构中,电池内部电芯间充填树脂材料,导致难易更换电芯,几乎不能进行维修。
5-电池包集成度提升对电动汽车充电基础设施的影响
选择不同的电池包集成技术同时隐含选择了不同的补偿方式,CTP倾向于换电,而集成化更高的CTB/CTC则倾向于快充。
高度集成化意味着在相同的空间内可以容纳更多的电池,从而增加了电动汽车的续航里程。用户可能不再需要频繁地进行短距离充电,而是更倾向于在长途旅行中进行快速充电。因此,充电基础设施的规划需要考虑到这些变化,以确保能够满足用户的需求。
由于电池包集成度的提升,电池包的物理尺寸和结构可能发生变化,这可能影响充电接口的设计和充电设备的兼容性。
此外,电池包集成度的提升也可能影响充电速度和效率。更高效的电池管理系统和充电技术可能需要被开发和部署,以确保快速且安全的充电过程。
我们会定期更新有关热设计与轻量化的技术与资讯,与您分享,供您参考,感谢您对迈泰的关注。
新能源汽车用电池托盘和储能液冷箱在生产过程中,必要适当的表面处理是一个关键步骤,如:采用涂装、氧化处理等在金属表面形成保护层,抵御腐蚀介质的侵蚀;对需要电气隔离的组件,如电芯、水冷板、模组壁等需要建立绝缘保护膜,一般通过喷涂绝缘粉末或绝缘漆来实现绝缘;选择合适的表面处理技术不仅能够提升托盘/液冷箱的耐用性和安全性,还能满足不同应用场景的需求。本文对常见表面处理技术进行整理,以供参考。
1-清洁、打磨
在生产过程中,托盘表面可能会积累加工油污、机油残留、粉屑、灰尘等杂质。这些杂质不仅会影响电池托盘的使用寿命,还可能对电池的性能和安全造成不利影响。通过清洁打磨,可以有效去除这些杂质,确保托盘表面的洁净。清洁打磨可以有效去除表面杂质、毛刺、焊渣,使其表面光滑、平整,从而提高电池托盘/箱体的整体质量。
a.化学清洗
碱洗:碱洗主要是利用碱性溶液(如氢氧化钠、碳酸钠等)去除铝合金表面的油脂、污垢和其他有机物。碱洗通过皂化作用、乳化作用和浸透润湿作用来去除油脂,同时生成可溶于水的沉淀物,从而达到清洁的效果。碱洗通常用于去除铝合金表面的油脂、灰尘和有机污染物。
酸洗:酸洗则是利用酸性溶液(如硝酸、盐酸等)去除铝合金表面的氧化皮、锈蚀和其他无机沉积物。酸洗通过酸与金属表面的氧化物反应,将其转化为可溶性盐类,从而去除表面杂质。酸洗主要用于去除铝合金表面的氧化皮膜、锈蚀和无机盐垢。酸洗常用于金属表面的最终处理,以提高其光洁度和平整度。
b.机械打磨
生产中,通过打磨工序可以去除加工余量、修正形状误差,确保托盘/箱体表面的平滑度和精度、满足装配要求,进而提高整体性能和使用寿命。
经过清洁打磨后的表面能增加涂装材料或其他材料的处理,对后续的防腐、密封、导热、绝缘、保温等涂层的施工非常重要,对这些材料牢固的附着在托盘/箱体起到关键作用。
2-涂覆与防护膜建立
除了基础的清洁、打磨外,托盘/箱体生产中通过会采用喷涂工艺进行表面处理用以形成保护层,防止氧化、腐蚀以及满足保温隔热、绝缘耐压等不同场景的需要。
a.保温隔热
电池托盘的防凝露和保温隔热可以通过综合设计隔热保温系统、使用高效保温隔热材料、应用气凝胶、进行电池包保温设计以及喷涂发泡保温材料等路径实现。
底面喷涂PVC、发泡材料
b.绝缘耐压
电池包箱体绝缘、液冷组件绝缘,主要是防止电流泄漏,保护人员免受电击,确保电池系统的正常工作。绝缘的实现通常采用喷粉和覆膜两种方案,主流的覆膜工艺包括:室温贴膜、热压、UV光照等。
内部喷涂绝缘粉、绝缘漆
3-标志、标识
在电池托盘的显著位置设置铭牌或标签,一般通过镭射、机械雕刻等方法实现。这些标识通常采用耐磨损、耐腐蚀的介质进行制作,以保证其在整个使用期内不易磨灭。
我们会定期更新有关热设计与轻量化的技术与资讯,与您分享,供您参考,感谢您对迈泰的关注。
储能变流器作为储能系统的核心设备,是电能转换、能量管理、确保电网稳定性,提高能源使用效率等的重要工具,随着储能变流器功率单元向着高度集成化、高工作频率和大容量的发展,对散热要求越来越高。
1-散热需求变化
a.匹配更大直流舱,变流器容量不断变大,高效散热技术确保设备可靠
伴随储能电芯单体容量愈来愈大,储能系统单机容量也在同步扩大。2023年初,市面上标准20呎单舱电池容量仅为3.35MWh,进入下半年多家电芯企业相继推出310+Ah储能产品,20呎单舱的电容量也扩容至5MWh。然而,5MWh模式更新不到半年,一些头部储能紧接着又发布6MWh、8MWh系统。根据一般经验,储能变流器按负荷容量的1.2倍配置,5MWh储能系统单机容量就必须大于2.5MW,大功率需要更高效的散热技术来确保设备在持续高负载下稳定运行。
储能系统集成拓扑方案迭代演化
b.直流高压技术的应用要求器件具备更高的耐压等级和绝缘强度,功率器件散热严峻
为匹配大容量储能系统,直流高压技术成为一种技术趋势,通过电压等级的提高,实现节能增效和性能提升,1500V电压升级源于光伏,现由光伏切入储能。然而,储能PCS高压演进之路还很长,一些厂商优化开始推向2000V。直流高压技术的应用迫使储能变流器中的电力电子器件需要具备更高的耐压等级、更高的绝缘强度以适应高压工作环境。高压环境下,功率器件的散热设计变得更为重要,功率器件的pn结温度一般不能超过125℃,封装外壳的温度不超过85℃。
c.构网型储能系统需要具备复杂的控制算法、电路设计及高功率密度储能变流器
不同于跟网型储能系统电流源的本质属性,构网型储能系统本质上是电压源,能够内部设定电压参数,输出稳定的电压与频率。因此要求构网型变流器模拟同步发电机的特性,提供电压和频率的支撑,增强电力系统的稳定性,这种控制策略要求变流器具备更高的功率密度和更加复杂的控制算法,并且需要更高性能的功率器件和更复杂的电路设计来实现控制策略。如何有效地管理由于高功率密度、复杂控制策略产生的热量,在保持高性能的同时减少散热系统体积和成本成为热设计的新挑战。
2-常用散热方案比较
储能变流器的散热方案在近年来经历了显著的迭代演化,主要体现在散热技术从传统的风冷向液冷技术的转变。
a.风冷方案
风冷是储能变流器初期采用的温控形式,以空气为介质,通过风扇和散热器来实现热量的散发。风冷方案通过不断降低能耗、优化结构、改进散热材料等途径提升散热效率。在2.5MW功率等级下,风冷仍能满足要求。
b.液冷方案
随着储能系统的功率密度和能量密度不断增加,液冷PCS因为采用了高导热系数的冷却液作为介质,通过水泵驱动冷却液在冷板内循环流动,并且不受海拔和气压等因素的影响,液冷系统拥有比风冷系统更高效的散热效率,液冷方案的匹配度更高,近一两年开始探索,普及。
除全液冷储能方案外,一些厂家推出储能直冷机,采用相变直冷,无水循环。直冷方案也正在进入储能领域。
我们会定期更新有关热设计与轻量化的技术与资讯,与您分享,供您参考,感谢您对迈泰的关注。
电池包是新能源汽车、储能一体柜及集装箱的关键部件,它是通过壳体包络构成能量源,为电动汽车提供动力,为储能柜与集装箱提供消纳能力。本文结合实际工程需要,通过分析电池包机械强度、安全性、热管理及轻量化等多方面要求,对电池包用型材设计要点进行总结说明。
1-电池包壳体设计要求
a.机械强度,耐振动强度和耐冲击强度,在试验后不能有机械损坏、变形及紧固不见松动的现象,锁止机构不应收到损坏。
b.密封性,电池包的密封性直接影响到电池系统的工作安全,通常要求达到IP67防护等级,以确保电池包密封防水。
c.电池包壳体设计需要考虑热管理性能,通过适当的热管理设计,保证电池在适合的范围内工作。
d.安装固定,壳体应留有铭牌和安全标志布置位置,并为采集线、各种传感元件等安装预留足够空间和固定基础。
e.所有无极基本绝缘的连接件、端子、电触头结合后应满足相应的防护等级需求。
f.轻量化,壳体轻量化对于提升电池包能量密度有着重大意义,铝合金质轻质优是当下最可行的选择,结合实际应用通过适当的极限设计提升轻量化水平。
g.耐久性,电池包壳体的设计寿命不得低于整体产品使用寿命,使用周期内不应发生明显的塑性变形,防护等级、绝缘性能不应降低;结构具备维护方便性,包括铭牌与安全标志布置、连接件防护等。
图1典型铝合金拼焊电池包壳体
2-典型铝合金电池包壳体方案
电池包壳体常用的铝合金材料有6061-T6、6005A-T6和6063-T6等,这些材料具有不同的屈服强度和抗拉强度,可以满足不同的结构需求。这几种材料的强度大小:6061-T6>6005A-T6>6063-T6。
当前电池包壳体成型方案有铝型材焊接、铝合金铸造、铸铝加型材铝、冲压铝板焊接等,铝型材拼焊方案因其灵活性和加工方便性成为主流选择,如图1,壳体主要有铝合金型材边框、铝合金型材底板构成,采用6系铝合金挤压型材拼焊而成。铝合金铸造方案因其简化工艺和降本潜力被视为未来发展方向。
3-型材断面设计
a.断面大小及复杂性:型材断面大小用外接圆来衡量,外接圆越大,所需要的挤压力就越大;型材断面通常由多个空腔组成,以提高结构刚度和强度,通常边框、中间隔板、底板、横梁等采用不同的断面设计以适应不同的结构和功能要求。
图2典型铝合金型材断面
b.铝型材壁厚:某一特定铝型材的壁厚最小值与型材外接圆半径、形状及合金成分有关,如,6063铝合金壁厚取为1mm时,6061铝合金就要取为1.5mm左右,同等断面挤压难度:6061-T6>6005A-T6>6063-T6。电池包用型材设计中,边框型材通常选用6061-T6铝合金材料,其典型断面由多个空腔组成,壁厚最薄处约为2mm左右;底板型材也由多个空腔组成,材质一般为6061-T6、6065A-T6,起壁厚最薄处也为2mm左右;另外,在底板承重的托盘及底板液冷集成的设计方案中,一般底板均采用双面结构,底板厚度一般为10mm,壁厚及腔体内壁约为2mm。
c.型材断面尺寸公差:断面尺寸公差应根据铝型材的加工余量、使用条件、型材挤压难易程度、形状的部位来确定,对一些挤压难度大的铝型材可以改变形状或增大工艺余量、尺寸公差,来减小挤压难度,挤压出近似要求的铝型材制品,然后通过或整形或者加工满足使用要求。
此外,进行型材断面设计时需要考虑不同焊接工艺对接头、坡口、壁厚等具体要求。
我们会定期更新有关热设计与轻量化的技术与资讯,与您分享,供您参考,感谢您对迈泰的关注。
电池托盘又称电池盒或PACK箱体等,作为新能源汽车开发中十分重要的部件日益受到重视,电池托盘的设计需要平衡重量、安全、成本、材料性能等因素之间的关系。铝合金由于其密度低、强度高等优点,在保证车身性能时仍能保证其刚性,在汽车轻量化工程中得到广泛应用。
1-电池托盘焊接部位及方法选择
铝制电池托盘以挤压铝型材为基础材料,通过焊接方式将各个部件组合为一个整体,形成完整的框架结构。类似的结构在储能Pack箱中也得到了广泛的应用。
电池托盘的焊接部位通常包括底板拼接、底板与侧边的连接、侧边框的连接、横纵梁、液冷系统组件焊接及支架、吊耳等配件的焊接。在焊接方法选择时,会根据不同的材料和结构要求选择不同的焊接方法,参见下表:
2-焊接热变形影响分析
焊接作为一种局部加热的加工方法,由于热源集中在焊缝处加热,因而造成焊件上温度分布不均匀,最终导致在焊接结构内部产生了焊接变形与焊接应力。焊接热变形就是在焊接过程中由于不均匀的热输入和热输出,导致被焊件的形状和尺寸发生改变的现象。结合实际的工程项目经验,对易产生焊接热变形的部位及影响因素进行了归纳总结:
a.长直线焊接部位
实际生产中,电池托盘底板一般由2~4块铝合金型材采用搅拌摩擦焊拼接而成,焊缝较长,底板与侧板、底板与间隔梁之间连接也有较长的焊缝。长焊缝由于热输入集中,容易导致焊接区域的局部过热,从而产生热变形。
电池托盘边框焊接
b.多部件拼接处
在多部件焊接处由于焊接过程中局部高温加热和随后的冷却导致的。在焊接过程中,焊件受到不均匀的热输入,使得焊缝区域与周围母材之间的温度差异显著,从而引起热膨胀和冷缩效应,引起被焊件变形。储能Pack箱电气安装端通常设有水嘴、线束支架、横梁等,焊缝密集,极易发生变形。
焊缝密集区,托盘前侧翘起变形
c.冷板流道侧壁
液冷板一体化集成设计的电池托盘中,结构刚度较小的部位,如薄板、管道结构等,在焊接过程中不能很好的抵抗热变形,容易发生变形,如:液冷板流道侧壁很薄,一般只有2mm左右,模组安装面焊接横梁、线束支架等零件时,容易造成流道侧壁有裂纹和变形褶皱,影响整体性能。
横梁焊接导致的液冷流道腔壁热裂纹缺陷
3-焊接热变形控制方法
a.分段焊、双面焊
对于强度要求相对较低的部件采取分段焊,将焊接过程分解成多个小段进行,对称布置焊缝,将焊缝对称地布置在构建截面中中和轴附近,以使焊缝产生的变形有可能互相抵消。同时,尽量减少焊缝长度和数量,避免焊缝过度集中或交叉,可以减小焊接温度梯度,从而减少焊接变形。对于底板、底板与侧面框等强度要求高的部位,采取双面焊,增加强度的同时减少因零件较大,焊道较长产生的弯曲变形。
b.优化焊接顺序
控制焊接变形,使用刚性较小的接头形式、避免双向、三向相交的焊缝位置,以及避开高应力区。优化焊接顺序,先焊刚度较弱的区域,最后焊刚度较好的区域,例如先焊角焊缝、再焊短焊缝、后焊长焊缝;先焊横焊缝、后焊纵焊缝。合理的焊接顺序可以有效控制焊接变形,从而控制焊缝外形尺寸。
c.焊接参数调整
控制焊接参数和流程,合理设置焊接速度、焊接层数和每层焊缝的厚度。对较厚的焊缝,采用多层多通道焊接方法,每层焊缝的厚度不大于4mm,多层焊能够减小结构显微组织,提高接头性能。精确控制焊接参数,合理选择焊接电流、电压、焊条型号和焊接速度等参数,可以确保熔池形状和大小一致,从而避免因参数选择不当造成的误差。
d.焊接技能提升
提高焊工操作技术水平(大型构件或要求严格节点采用机械加工),确保焊接过程中动作一致性和规范性,减少人为因素导致的尺寸问题。
我们会定期更新有关热设计与轻量化的技术与资讯,与您分享,供您参考,感谢您对迈泰的关注。
铝合金是工业中应用最广泛的一类有色金属结构材料,尤其在材料导热性能备受关注的场景下,在需要高效热传导的场合,如电子设备散热、电动汽车三电散热、电池储能系统散热以及航空航天领域,通常被用作制造散热器、导热板、电子元件等高效传热设备。
导热率也叫导热系数,是表征材料导热性能的参数指标,它表明单位时间、单位面积、负的温度梯度下的导热量,单位为W/m·K或W/m·℃。铝合金是一种由铝和其他金属组成的合金材料,其导热性能非常优异,导热系数通常在140-200W/(m•K)之间,铝作为地壳中含量最高的金属,因热传导系数较高、密度小、价格低而受到青睐。
1-铝合金材料的导热原理
当材料的相邻区域存在温度差时,热量就会从高温区域经接触部位流向低温区域,产生热传导。金属材料内有着大量的自由电子存在,自由电子可以在金属中快速运动,可以快速实现热量的传递,晶格振动是金属热传递的另一种方式,但相对自由电子传递方式来说处于次要地位。
金属与非金属的热传导方式对比
2-影响铝合金导热性的因素
a.合金化是影响热导率的主要因素之一。合金元素通过固溶原子、析出相和中间相形式存在,这些形式会带来晶体缺陷,如空位、位错和晶格畸变,这些缺陷会增加电子散射的几率,导致自由电子数量减少,从而降低合金的热导性。不同合金元素对Al基体产生晶格畸变程度不同,对热导率的影响也不同。这种差异是由合金元素的化合价、原子体积差异、核外电子排布、凝固反应类型等多因素共同作用的结果。
b.热处理是铝合金加工过程中非常重要的环节,通过改变铝合金微观结构和相变,可以显著影响其热导性。固溶处理是将铝合金加热到一定温度,使其溶质原子充分溶解于基体中,然后快速冷却,以获得均匀的固溶体。这种处理方式可以提高材料的力学性能,但通常会降低其热导率。时效处理是通过在固溶处理后进行适当的冷变形和再加热,可以优化合金的微观组织,提高其综合性能。时效处理兼顾了合金的力学性能和热导率,使合金在保持较高强度的同时,也具有较好的导热性。退火处理通过在较低温度下保温,使合金中的第二相析出并重新分布,从而改善合金的微观组织。退火处理可以提高铝合金的塑性和韧性,但对热导率的影响因具体情况而异。
Al-Cu合金在时效过程中的晶体结构变化示意图
c.其他因素影响,杂质和第二相粒子:铝合金中的杂质和第二相粒子(如氧化物、碳化物等)会散射热载流子(电子和声子),从而降低热导率。杂质含量越高,第二相粒子越粗大,热导率通常越低。铝合金的晶粒尺寸也会影响热导率。一般来说,晶粒尺寸越小,晶界越多,热导率越低。此外,铝合金的加工方式(如轧制、挤压、锻造等)会影响其微观结构和残余应力状态,进而影响热导率。加工硬化和残余应力会降低热导率。
综上,铝合金是高导热材料的理想选择,铝合金中合金元素类型及其存在形式、热处理方式、杂质情况、晶粒大小及成型方式等因素均会影响铝合金材料的热导率,在进行材料成分设计及工艺规划时应该综合考虑。
我们会定期更新有关热设计与轻量化的技术与资讯,与您分享,供您参考,感谢您对迈泰的关注。
电池包气密性是确保电池包质量和安全性的关键,关系到电池包的安全性、可靠性和使用寿命,电池包气密性检测不仅要在生产过程中进行,还在电池维护和检修中进行。
1-电池包气密性要求
实际生产中电池包的气密性需满足以下要求:
密封性能,电池包壳体、接口和连接件等部位需具有良好的密封性能,以防止灰尘、水气等外界杂质进入电池包内部,可以通过焊接、密封胶、防水材料等实现。
防水性能,以防止水分进入电池内部,导致短路、腐蚀等问题。根据国标GB38031-2020《电动汽车用动力电池安全要求》,电池及其组件的密封性能应达到IP67标准,多数新能源汽车用电池及其组件的密封性能要求更高,需满足IP68标准,即电池包在规定的水深和沉水时间内能够防止水进入。
传统的气密性检测方法包括压力法和浸泡法(水检)等。浸泡法则是将液冷板浸泡在水中,观察是否有气泡产生来判断密封性。
水道气密性测试槽
虽然IP68标准更加严格,但在实际应用中,压降法往往作为主要的检测手段,通过设定合适的气密检测标准来满足IP68的要求。压降法是通过测量电池包内部压力变化来判断电池包气密性。在进行气密性检测时,需要关注多个参数,如充气气压、充气时间、稳压时间和泄漏率。
差压基本原理图 直压基本原理图
2-液冷板渗液问题分析
随着动力电池汽车、电化学储能等市场需求的不断升级,更高的能量密度与功率密度电池包得到广泛应用。因为电池热特性,确保电池等核心设备的稳定运行,并提高能源利用效率,液冷技术是储能热管理主流技术路线之一,液冷系统的气密性测试成为了一个关键环节。
液冷板渗液是一个严重的问题:渗液会阻碍冷却液正常流动,影响液冷板散热效果,使得设备性能下降;渗液还可能会造成系统组件老化、损坏,降低系统的可靠性;渗液还可能腐蚀电子元件和线路,增加设备故障和火灾风险。
在液冷板生产制造过程中经过严密气密性测试,为何还会出现渗液问题?
液冷系统气密测试流程
渗液可能由多种因素导致:
l 微小裂缝和缺陷,景观气密性检测可能检测到大的泄露通道,但微小裂缝和缺陷可能仍然存在,这些微小的裂缝在液体压力或高温环境下可能会扩大,导致渗液。
l 冷却液表面张力与浸润性差异:冷却液的表面张力较低时,更容易通过微小缝隙渗透。如果液冷板的表面张力设计不合理或冷却液选择不当,可能会加剧渗液问题。
浸润性差异:不同冷却液对固体表面的浸润性有差异。如果液冷板的材料表面粗糙度高或有微观结构缺陷,冷却液可能更容易渗透。
l 安装或工艺问题:液冷板的安装工艺如果不够精细,或者焊接、连接等过程中存在缺陷,也可能导致密封不严,增加渗液的可能性。
l 环境条件:温度的变化,特别是高压环境,可能会影响冷却液的渗透性。尽管在气密性检测时可能未考虑这些环境因素,但在实际操作中,温度波动可能导致密封失效。
l 材料老化或疲劳:液冷板的材料如果使用时间过长,可能会发生老化或疲劳,导致其密封性能下降,从而增加渗液的风险。
3-液冷板渗液问题预防措施
l 改进液冷板设计:通过优化液冷板的结构和设计,减少微小裂缝和缺陷,提高其密封性能。例如,在流道面焊接模组安装梁时,采取防泄漏措施,避免冷却液泄漏。
l 提高制造工艺水平:在液冷板生产过程中,采用高质量的焊接工艺和材料,确保冷却液不易渗透。同时,在组装过程中,严格按照操作规程进行,避免出现松动或错误安装。
l 优化检测方法组合,保障检测效率的同时提高检测精度,降低漏检率。采用浸泡法、压降法进行气密性检测,操作简单、经济、效率高,适合大批量常规性的检测需求。但两种方法的检测精度较低,压降法检测精度一般为1×10-4Pa·m³/s的泄露速率,检测结果准确性易受温度、湿度、洁净度、压力等因素的干扰。采用检测精度更高、效果更好的检测设备将检测精度提升至1×10-6Pa·m³/s,提升检测效果。
除了液冷板本体的防范措施外,还需在冷却液选型、密封件选择及设备工作环境等多环节中采用合适的应对策略。
我们会定期更新有关热设计与轻量化的技术与资讯,与您分享,供您参考,感谢您对迈泰的关注。
在散热器设计中,采用有效的降本方式能够提高整体系统的可靠性和效率,同时可以减少不必要的成本。
1-降额降本
降额设计是一种有目的地降低元器件或产品在工作时承受电、热和机械应力的设计方法。实际生产和使用的场景中,可以通过降低元器件承受的应力,从而提高电子设备的稳定性。
2D、3D封装方式的散热路径示意
l 降低工作应力:在产品的设计和运行时,可以通过降低工作负载,控制工作频率、限制电流和电压等方法来减少元器件的工作应力。
l 降低环境应力:通过选择适合的元器件类型、布局和封装形式来降低环境应力,如选择温度裕度较大的元器件,或者使用密封性良好的封装形式,以减少温度、湿度和压力对元器件的影响。
l 可靠性工程应用:合理的冗余设计、故障检测和隔离等,进一步降低元器件的失效风险。
通过降低元器件在工作时承受的应力,可以降低其功耗和发热量。当功率器件在低于其额定应力条件下工作时,可以降低其耗电量和产热量,有助于提高系统的能效和可靠性。从长远来看,降额设计有效提高元器件寿命、降低故障率、减少维护工作量,进而降低成本。
2-优化布局
通过合理的布置热元件可以显著提高散热器的工作效率,合理的元器件布局策略可以实现产品性能和成本的平衡。
l 分散发热元件:将发热量大的元件分散开来,减少单位面积上的热量负荷。
l 有利于散热的位置:将发热元件放置在有利于散热的位置,如靠近通风口或者设备的边缘。
l 交错排列:在布局时,将发热元器件与其他一般元器件交错排列,同时尽量使发热元件远离温度敏感元件,以减少其对热敏元件的影响。
l 改善气流:通过改变走向设计和元件布局,优化气流路径,增大流速,提高换热系数。
元器件间间距建议
3-冷却方法的选择
随着电子元器件的性能提升和集成度的增加,功率密度不断增大,导致电子元器件在工作时产生的热量也显著增加。在选择电子元器件的散热方法时,温度控制要求主要包含以下方面:
l 温度范围:不同的元器件对温度容忍的范围不同,如CPU等高性能芯片的工作温度要求在85-100℃之间,而一些低功耗设备可以容忍更高的温度,因此散热系统要确保元器件在安全的温度范围内工作。
l 温度控制精度:在一些温度控制要求严格的场景中,需要采用能够精确控制温度的散热方案,以免过高过低的温度造成元器件性能下降,甚至损坏。
l 环境温度:电子设备的散热效果不仅取决于器件自身的散热能力,还受到周围环境温度的影响,散热设计需要考虑环境温度变化,并尽可能通过散热手段保持设备在适宜的温度范围内。
l 功耗和可靠性:一些低功率电子元器件在发热量较低时,可以采用自然散热,对于高功耗设备则需要更高效的散热技术以确保其在高负荷运行时保持正常的性能并延长使用寿命。
l 密封性和密集性:在密封及高密度组装的器件中,如果发热量不高,可以依赖自然散热。而当元器件密集且发热量大的情形下,需要强制散热或液体冷却等更为有效的散热技术。液体冷却和热管技术在高功耗、大发热量的场景,如行波管、磁控管、功放管等高功率电子元器件,服务器和高功耗设备,以及新能源汽车三电系统,有其独特的应用优势。
充电桩风冷散热模块 充电桩液冷散热模块
在选择电子元器件的散热方式时需要综合考虑发热量和热流密度、环境温度与工作温度、空间约束与热隔离需要及成本与可行性等要素。通过运用适当的散热技术及散热装置保证元器件在适宜的温度下运行,可以有效降低系统更换和维护成本。此外复用历史项目也是降低开发制造成本,提升可靠性的有效策略。
我们会定期更新有关热设计与轻量化的技术与资讯,与您分享,供您参考,感谢您对迈泰的关注。
储能浸没式液冷技术是一种先进的电池冷却方法,利用液体的高效导热特性,实现了对电池的快速、直接和充分冷却,确保了电池在安全和高效的环境中运行。其基本原理是将储能电池完全浸没在一种绝缘、无毒且具有散热能力的液体中。这种技术通过液体直接与电池接触进行热交换,从而快速吸收电池在充放电过程中产生的热量,并将其带到外部循环系统中进行冷却。
单项浸没式液冷储能系统原理示意图
浸没式液冷储能Pack箱作为电池包的承载和保障电芯在合适的环境中工作的关键部件,主要承担电池包及冷却液承载、安全防护、传导换热等功能。因此在箱体结构设计中需要综合考虑密闭性、冷却效率、安全性、材料选择及加工工艺等多个方面,以确保系统的高效、安全和可靠运行。而箱体结构设计是整个液冷系统的基础。
1-均匀受载
浸没式液冷储能Pack下箱体由底板与侧板构成,底板作为基础支撑,而侧板则固定在底板的四周,共同构成箱体的主体框架。箱体的尺寸综合考了液冷系统的整体需求和荷载情况进行调整,在较大尺寸箱体的设计中可以合理设置内部隔板或支撑结构,将大空间划分成多个小空间,通过增加受力面积,提高均匀受载力。而内部结构上可以通过增加支撑肋、加强筋来提高局部的承载能力,还可以在箱体内部设置均载结构以平衡各个角落的负载。
同时,为降低塑性变形对均匀受载性的影响,可以将高低不同的加工面设计为同一平面,这样可以减少机床调整次数,避免高度差导致的变形;还可以通过增加箱体的宽度或高度来分散负载,减少变形。
此外,液冷流道与箱体底板的一体化设计,通过搅拌摩擦焊或激光焊完成拼接,这种设计能有效提高整体结构强度。
单项浸没式液冷储能Pack下箱体结构示意
2-换热设计
导热能力是浸没式液冷储能技术中的重要环节,设计目标是确保电池在高温环境下能够有效散热,从而保持其性能和安全性。
箱体的材料应具有高导热性能,常用的材料有铝合金、铜、铝基复合材料。箱体设计还需要考虑环境温度变化的影响,适当厚度的保温层,能够保证箱体内部温度在一个较恒定的范围内,进而提升系统的整体效率。
箱体的结构设计直接影响其导热能力,合理的流道布置,确保液体在箱体内部顺畅流动,并最大限度地增加接触面积,是提升箱体导热能力的主要策略。箱体内部可以设置多个流道,以增加冷却液循环路径,从而提高散热效果。
方案一 全浸没+单项+板换 方案二 全浸没+单项+箱换
液冷系统包括冷却介质、导热结构、液冷管路和支撑结构。
方案一中,可选择同种或不同种的冷却液分别充入液冷板流道腔与箱体空腔,两个腔体均密封且互不连通。箱体空腔中,冷却液将电池模组浸没,充分接触,冷却不流动,利用液体的导热性好的特点吸收电池表面的热量,降低温升。液冷板中,冷却液在进水集管内分成多个流道并行进入冷板,然后在出水集管内汇合流出,主要负责将热量带出,实现散热。
方案二中,温度低的冷却液从下面或侧面流进,温度高的从上面流出,冷却液在电池包内循环流动,这样能够有效均匀地分配热量,提高整体的冷却效率,保持电芯或电池包温度的一致性。
了进一步提高冷却效果,可以采取多种优化措施,如优化液体流量和循环方式,选择高热容量的冷却液,以及改进液体的温度分布。这些措施能够减少热量的积聚和能量损失,确保电池在高效冷却状态下运行。
3-密封设计
对于液冷pack箱来说,通过采用先进的密封材料和结构进行全密封设计,密封设计不仅要考虑气密性,还需考虑液体介质的密封,确保电池单元在各个方向上均无泄漏。
设计应根据具体应用需求选择合适的密封形式和形状,还要考虑密封件的泄漏自由度、耐磨性、介质和温度兼容性、低摩擦等因素,并根据详细的规格选择合适的密封件类型和材料。
另外,焊接工艺的选择对密封性能影响也很大,对于不同的材料和厚度,选择合适的焊接方法能有效提升焊缝质量,以保证系统的整体强度和密封性。
单项浸没式液冷储能Pack下箱体成品图
我们会定期更新有关热设计与轻量化的技术与资讯,与您分享,供您参考,感谢您对迈泰的关注。
Lori is a heat sink manufacturer of design and manufacturing high power heat sink, we have provided innovative thermal solutions for many high power industry device such as Aerospace industry,Medical, Communication server, Consumer Electronics etc. Our solutions include high power heat pipe thermal mould, liquid cooling system, staked fin heat sink solution etc.
Lori is a heat sink manufacturer of design and manufacturing high power heat sink, we have provided innovative thermal solutions for many high power industry device such as Aerospace industry,Medical, Communication server, Consumer Electronics etc. Our solutions include high power heat pipe thermal mould, liquid cooling system, staked fin heat sink solution etc.
Lori is a heat sink manufacturer of design and manufacturing high power heat sink, we have provided innovative thermal solutions for many high power industry device such as Aerospace industry,Medical, Communication server, Consumer Electronics etc. Our solutions include high power heat pipe thermal mould, liquid cooling system, staked fin heat sink solution etc.
流体仿真
使用模拟软件分析散热器和冷板的散热性能
应用场景
工况: 高热流密度情境
安装布置: 单面安装
典型应用:客户定制
特点:散热效果好
应用场景
0.5-1C
安装布置: 底部液冷
典型应用:36s,48s,52s,104s
特点:冷却效果好
制冷剂通过蒸发器释放电池冷板吸收的热量,然后将水泵运行产生的电力送入冷板吸收设备产生的热量。
液冷技术是以液体为介质进行热交换,相比于空气,液体具备更大的载热量,更低的流阻,能提供更快的散热速度、更高的散热效率。并且液冷系统无需设计风道,减少了风扇等机械部件的使用, 故障率更低,噪声小,环境友好,占地面积节约,更适合未来拜MW级以上的大型储能电站,在电池能量密度⾼, 充放电速度快场合得到⼴泛的应用。
电池储能系统是一种使用电池作为储能介质的储能系统。与传统化石燃料不同,电池储能系统可以储存太阳能和风能等可再生能源,并在需要平衡能源供需时释放它们。
DFM优化建议
帮您减少潜在的生产过程中可能的错误和缺陷,确保产品在生产满足设计要求的质量标准
应用场景
工况: 高热流密度情境
安装布置: 单面安装
典型应用:客户定制
特点:散热效果好
目前比较流行的水冷头,基本上采用纯铜微通道型。铜底板直接进行铲齿加工,鳍片与底板一体,减少热阻。底板与盖板之间则采用钎焊或者扩散焊的方式,确保密封的可靠性。
下篇:铲齿工艺加工水冷头主要成本构成
1-铲齿工艺制造水冷头的优势
l 一体化设计:铲齿工艺可以将地板和鳍片进行一体化加工,有利于减少接触热阻,提升热传导性能。此外一体化的底板和鳍片设计还可以提升结构强度。
l 高精度加工:铲齿工艺可以加工出非常精细的齿片结构,齿高、齿厚和齿距可以精确控制,这使得散热鳍片密度更高,散热面积更大,进而更高效散热。同时也能更好的满足不同客户对形状、尺寸等个性化的需求。
l 生产效率高,铲齿工艺可以批量生产,与传统的CNC相比,铲齿工艺可以同时加工多个齿片,大大提高了生产效率。
图1:不同加工工艺的水冷头底座 a-铲齿 b-CNC c-冷锻
2-铲齿工艺水冷头成本构成
l 设计与开发成本:铲齿工艺水冷头的设计复杂度较高,尤其是在散热性能要求较高的情况下,需要进行复杂的工艺设计和优化。
l 材料成本:铲齿工艺中使用的材料主要是铝和铜合金。铝板与铜合金结合的设计方式在散热器制造中较为常见,且性价比较高,因此铝和铜的质量直接影响成本.
l 加工工艺成本:
铲齿工艺成本:铲齿工艺涉及高精度的数控加工设备,如三轴线轨数控机床。这种设备的使用需要较高的投入成本,同时对操作人员的技术要求也较高,这些都会增加生产成本。
焊接工艺成本:在水冷头的制造过程中,焊接工艺也是一个重要的成本因素。真空钎焊和扩散焊是两种常用的焊接方法。钎焊可以同时焊接多个接头、生产效率高,需要钎料,对工艺条件的要求较,质量控制难度大;扩散焊设备一次性投资较大,扩散焊不需要填料,但对工件表面的加工要求高。
表面处理成本:常见的表面处理方式有阳极氧化、镀层处理等。对于铝合金水冷头,阳极氧化处理可以提高表面硬度、耐磨性和耐腐蚀性,同时增加产品的美观度;对于铜质水冷头会进行镀层处理,如镀镍等,以防止铜的氧化和腐蚀,提供产品的使用寿命和可靠性。
l 其他成本:检验检测、包装运输等。
3-成本优化建议
l 优化材料使用:
选择合适的材料:如,铜的导热系数高,单密度大,单价高;铝的质量轻,单价低,导热系数稍差。
材料用量:通过精确计算材料厚度和余量,确保材料的高效利用,减少材料浪费。
图2:材料用量计算示意
l 优化生产流程
简化模具:设计简单的模具,减少模具的复杂度和成本。
减少废品率:通过精确的工艺控制和质量检测,减少废品率。
一次成型:优化工艺路线,减少多次加工工序,提高生产效率。
我们会定期更新有关热设计与轻量化的技术与资讯,与您分享,供您参考,感谢您对迈泰的关注。
水冷头作为液冷散热系统的关键部件,其设计需兼顾换热性能、结构强度、防腐蚀性、防泄漏性以及成本控制等多方面因素。水冷头内部通常设计有复杂的换热槽结构(即流道),其内部流道设计的优劣直接决定了整个系统的换热效率。
中篇:水冷头设计、加工工艺及挑战
1-不同场景对水冷头的设计要求
l 高性能计算:
高性能计算设备(如高性能CPU、GPU等)在运行过程中会产生大量热量,因此需要水冷头具备高效的散热能力。为了应对高热流密度散热需求,水冷头通常采用高密度微流道设计,以增大换热面积,提高散热效率。此外,一些设计将水冷头直接集成到CPU上,省去了涂抹硅脂的步骤,不仅简化了组装过程,还进一步提升了散热性能。可靠性方面,水冷头必须具备出色的密封性能,以防止泄漏,确保长期稳定运行。
l 显卡散热:
显卡是高热量产生区域,因此需要水冷头具备全覆盖设计,以确保显卡上各个发热部件均能得到有效散热。同时,显卡散热对冷却液的流量要求较高,需要水冷头内部结构设计支持高流量通过,以便快速带走热量。
l 数据中心:
在数据中心中,水冷头的结构设计需要满足高效散热、低噪音、高可靠性、适应高功率密度、智能化管理和环境适应性等多方面的要求,以确保数据中心的稳定运行和高效散热。
2-水冷头结构演化趋势
水冷头结构设计的演化趋势体现了技术创新和性能提升的双重追求,主要体现在以下几个方面:
l 散热性能提升:
增大接触面积:一些水冷头设计通过增加与发热元件的接触面积,提高散热性能。如,采用大面积铜底座设计,可以实现良好的接触和热传导。
优化内部结构:对内部水道进行优化,一种思路以优化流体流动为目标,如,由普通Fin片改为转向Fin片风格,呈现长条形流道,促进流动边界层分离,减少边界层厚度,提升热交换效率;另一种思路以增大热容面积为目标,如,从传统的粗水道向微流道设计转变,显著提高了冷却液与底板的接触面积,增强了散热效率。还有些设计中通过导流板将冷却液喷射至微水道底板,提升局部流速和乱流,大幅提高吸热效率。
l 集成化和智能化设计:
一体化设计:通过一体化设计将水泵、散热鳍片、导热底座等部件集成到一起,减少连接点,提高系统稳定性和散热效率。
多功能集成:除了散热性能,现代水冷头还具备温显、监测功能。
模块化设计:通过组合式扣具结构,提高组织的便利性和自由度。
图1:不同Fin厚水冷头底座
l 高性能材料和表面处理:
采用纯铜底座等高性能材料,结合镀镍等表面处理技术,提升导热效率和抗腐蚀性能。
3-加工工艺及挑战
l 材料特性影响加工:
材料硬度与韧性问题:不同材质的散热器,如铜、铝及其合金,硬度和韧性不同,对加工刀具和工艺的要求也不同。硬度较高的材料,刀具磨损加快,需更频繁地更换刀具;韧性好的材料,切削时易产生变形和毛刺。
铜铝复合材料加工复杂:铜铝复合材料铲齿散热片,需先采用连续铸造半熔态压制成型技术制成复合材料,再进行铲齿加工,工艺流程更复杂,对设备和工艺的精度要求更高。
l 尺寸精度要求高
齿高齿厚一致性难保证:对于一些高密齿散热器,其要求每个齿的高度和厚度都高度一致,以确保散热片的性能和均匀性。若齿高齿厚差异过大,会导致热传递不均匀,影响散热效果。加工过程中,需使用高精度设备和自动化控制系统,才能确保每个齿的规格一致。
齿间距控制难度大:散热片上的齿过于密集时,其密度和间距使得加工过程更加复杂,加工设备需具备更高的速度和精度,才能保持齿的均匀性。例如,当齿间距过小,刀具在切削时容易产生干涉,影响加工精度和表面质量。
l 表面质量要求严格
毛刺问题:加工过程中易产生毛刺,这不仅影响散热器的美观度,还可能阻碍空气流动,降低散热效果。毛刺的产生可能由材料切削精度低、加工工具刀具磨损等原因引起,需采取相应的去毛刺工艺来解决。
表面粗糙度:散热器的表面粗糙度影响其散热性能和后续的表面处理效果。过高的表面粗糙度会增加空气流动的阻力,降低散热效率,还需进行额外的表面处理来降低粗糙度,增加了加工成本和时间。
l 加工设备与工艺要求高
设备精度与稳定性:铲齿加工需要高精度的铲齿机,设备的精度直接影响齿的尺寸精度和表面质量。同时,设备需具备良好的稳定性,以保证长时间加工过程中尺寸的一致性。
刀具选择与磨损:合适的刀具对加工质量至关重要。刀具的材质、几何参数等需根据材料特性进行选择。加工过程中,刀具磨损会导致切削力增大、尺寸精度下降和表面粗糙度增加,需及时调整或更换刀具。
进给速度与切削深度:进给速度和切削深度的不合理设置,易导致加工缺陷。如进给速度过快,切削深度过大,会使刀具承受过大负荷,出现抢刀、弹刀、掉刀等现象,影响加工精度和表面质量。
图2:铲齿工艺
l 定制化需求高
不同的应用场景对散热器的尺寸、形状、齿高、齿厚、齿间距等参数有不同的要求,需根据具体需求进行定制化设计和加工。这要求加工厂家具备灵活的工艺调整能力和丰富的经验,以满足多样化的定制需求。
我们会定期更新有关热设计与轻量化的技术与资讯,与您分享,供您参考,感谢您对迈泰的关注。
随着全球人工智能算力的迅猛增长,以及芯片热设计功耗(TDP)的持续攀升,数据中心的冷却需求正面临前所未有的挑战。与此同时,全球范围内节能降碳政策的日益严格,进一步推动了冷却技术的革新。在这一背景下,传统的风冷方案已逐渐难以满足高效散热与节能的双重要求,液冷技术因其卓越的散热性能和显著的节能优势,正迅速崛起,成为数据中心冷却方案的主流选择。服务器作为数据处理和存储的核心设备,其性能与稳定性直接关系到整个系统的运行效率。服务器的核心组件——包括主板、CPU、内存、硬盘和显卡等——在持续高负荷运作下会产生大量热量,若不能及时有效地散热,将严重影响服务器的性能和寿命。为此,先进的液冷系统被引入到服务器散热解决方案中,直接安装在主要热源如CPU和显卡上,以显著提升散热效能。
上篇:水冷块结构及工作原理
液冷系统的核心部件之一是水冷块,它通常由高导热性的铜或铝材料制成,设计有精密的水道和散热片结构。这些水冷块紧密贴合在CPU、GPU等热源表面,通过内部流通的冷却水迅速吸收并转移热量。随后,热量被输送至散热片,通过水冷系统的循环,最终将热量散发到周围空气中。
图1:主流芯片制造商芯片热功耗趋势
1-常见水冷块类型及特点
l 微通道水冷头
特点:微通道水冷头采用精密的微小水道设计,水道结构细密且复杂,能够显著增加冷却液与发热部件的接触面积,从而大幅提升散热效率。微水道设计还能够在冷却液流动过程中产生强烈的湍流效应,进一步增强对流换热系数,实现高效的热量转移。
应用场景:特别适用于高发热量的CPU和GPU,尤其在高性能计算、超频以及数据中心等对散热要求极高的场景中表现卓越。
l 大流量水冷头
特点:大流量水冷头的内部结构相对简单,通常采用铜板或蚀刻凹槽设计,制造成本较低。其核心优势在于依靠高速水流快速带走热量,适合搭配大流量的水冷系统使用。虽然结构简单,但其高效的散热能力使其成为性价比极高的选择。
应用场景:适用于对散热效率有一定要求但预算有限的场景,例如中高端的DIY电脑系统或中小型服务器集群。
l 喷射型水冷头
特点:喷射型水冷头通过导流板将冷却液从狭小的喷嘴高速喷射到微水道底板上,形成强烈的湍流效应,显著提升散热效率。这种设计不仅增加了冷却液与底座的接触面积,还通过高速流动进一步优化了热交换性能。
应用场景:适用于高性能CPU和GPU,尤其在高散热需求和高流量场景中表现突出,例如超频计算、人工智能训练以及图形渲染等领域。
2-水冷块一般结构
水冷块是一个内部留有水道的金属块,通常由铜或铝制成,与CPU、显卡或其他发热不见接触,其结构设计直接决定了散热性能的优劣,典型的水冷块通常由以下几个关键部分构成:
l 底座,通常由高导热材料,如铜或铝合金,表面经过精细加工,以确保与发热部件的紧密接触。底座内部设有复杂的流道设计,以增加冷却液与底座的接触面积。
l 盖板,与底座一起形成流道密封腔,保护水冷块内部的流道、密封等组件,防止灰尘、杂质和外界物理损伤。
l 进出水口,进出水口是冷却液进出水冷头的接口,一般设计在水冷头侧面或顶部,要确保冷却液能够顺利的流入流出,其位置设计需要考虑流体的流动路径,以减少流阻,提高冷却液流动速度。
l 扣具,扣具是将水冷头牢固地固定在CPU或其他发热部件上,确保紧密基础,实现高效热传导。
图2:水冷块典型构造
3-散热性能综合优化
l 流道设计优化
增加流道接触面积:通过设计更窄、更密集的流道,可以显著增加冷却液与底座的接触面积,从而提高对流换热系数。例如,微水道设计通过其细密的水道结构,微通道水冷块的设计参数(如通道宽度、高度、间距)对其散热效率具有决定性影响:随着通道宽度的减小,换热系数显著增加,得益于窄通道内冷却液流动的湍流效应增强,从而提高了热交换效率;较高的通道高度有助于增加冷却液的流动空间,从而提升换热性能;较小的通道间距能够增加冷却液与热源的接触面积,从而提高散热效率。
还可以通过优化流道布局及减少流道弯道进行优化:合理的流道布局能够确保冷却液均匀覆盖发热部件的表面,减少局部温差。而流道中的弯道会增加水头损失和内部流阻,从而降低冷却效率。在设计中应尽量减少弯道数量,若无法避免,则需将弯道设计为圆滑过渡,以降低压降并优化流动性能。
l 高导热材料:水冷块的底座通常采用纯铜或铝合金等高导热材料,这些材料能够高效地将热量从热源传导至冷却液,从而提升整体散热性能。
l 结构参数优化,如:底座基板厚度、Fin片、扰流结构等。基板厚度的增加会导致最高温度上升,因此在设计中需要在散热效果与结构强度之间找到最佳平衡点;通过增加肋片的高度、厚度和间距,可以提升散热性能,但同时也会增加流阻,找到最佳的肋片设计组合,从而实现散热性能的最大化。扰流柱的形状能够有效增强湍流效应并提升热交换效率。
我们会定期更新有关热设计与轻量化的技术与资讯,与您分享,供您参考,感谢您对迈泰的关注。
本文从生产实际出发,总结了搅拌摩擦焊焊接过程中常见的问题、产生原因及改善方法,供大家参考。
1-表面缺陷
(1)表面沟槽
l 问题描述:表面沟槽又称犁沟缺陷,通常出现在焊缝的上表面,偏向于焊缝的前进边,呈沟槽状。
l 产生原因:焊缝周围的热塑性金属流动不充分,焊缝的塑性金属无法充分填充搅拌针行进过程中留下的瞬时空腔。
l 改善方法:增大轴肩直径,增大压力,降低焊接速度。
图1: 沟槽
(2)飞边毛刺
l 问题描述:飞边毛刺出现在焊缝的外边缘,呈波浪形。
l 产生原因:旋转速度和焊接速度的匹配不当,下压量过大。
l 改善方法:优化焊接参数,减少下压量。
图2:飞边毛刺
(3)表面起皮
l 问题描述:表面起皮或起丝呈皮状或丝状出现在焊缝的表面。
l 产生原因:大量的金属摩擦产热积累于焊缝的表层金属,使得表层的局部金属达到熔化状态。
l 改善方法:优化焊接参数,降低转速,提高焊速度。
图3:表面起皮
(4)背部焊瘤
l 问题描述:在焊缝的背面形成焊瘤。
l 产生原因:焊接过程中搅拌头的深度和压力控制不当。
l 改善方法:优化搅拌头的深度和压力设置。
2-内部缺陷
(1)未焊透
l 问题描述:焊缝底部未形成连接或者不完全连接而出现的“裂纹状”缺陷。
l 产生原因:搅拌针长度不足,导致焊缝下部的材料未能充分搅拌。
l 改善方法:选择合适的搅拌针长度,确保焊缝厚度上的材料能够被充分搅拌。
图4:未焊透
(2)孔洞
l 问题描述:焊缝底部未形成连接或者不完全连接而出现的“裂纹状”缺陷。
l 产生原因:焊接过程中,由于摩擦热量输入不够,使达到塑化状态的材料不足,造成不充分的材料流动,导致焊缝区未完全闭合的。
l 改善方法:优化焊接参数,改进搅拌针设计,控制焊接速度和转速。
图5:孔洞
我们会定期更新有关热设计与轻量化的技术与资讯,与您分享,供您参考,感谢您对迈泰的关注。
近段时间,小编注意到多家企业都在关注和布局浸没式液冷储能,浸没液冷技术在沉寂一段时间后再次受到关注,似乎又有“变火”的趋势,相信很多同行也都在关注这一进展。
1-浸没式液冷技术特点
储能电芯走向300+Ah、储能系统纷纷走向5MWh+,电芯越大产热越多、越难散热、越难保证温度一致性,并且储能系统由大量电芯堆叠组成,运行工况复杂多变,更容易造成产热不均、温度分布不均。散热、均温的问题若不能妥善解决,会导致电池的充放电性能、容量和寿命的下降,影响整个系统的性能。此外,安全一直是悬在锂电储能头上的“达摩克利斯之剑”,而提升安全的最普遍做法是向本征安全、主动安全、被动安全三个维度进发。
浸没式液冷是将电芯浸没在在一种绝缘、无毒、可散热的液体中,冷却液具有更高的导热率和比热容,这种直接的接触方式在提供极高的热传递效率的同时,也能够提高更好的均温性。并且,冷却液在作为温度控制的介质外,还可以作为储能系统消防液使用,使得温度控制与消防合二为一,也是浸没式液冷技术的显著特点。浸没式液冷在面对更高散热性能、更强安全性要求的产业背景下,无疑会更具优势。
图1:浸没式液冷储能电池Pack箱
2-浸没式液冷储能系统方案
浸没式液冷技术作为液冷技术一个分支,并非储能行业首创,最初是在高性能计算领域得到应用的,后来逐渐扩展到数据中心、人工智能、加密货币等。
浸没式液冷储能系统的设计初衷是为了解决传统风冷和间接液冷在冷却效率和电池温差控制方面的不足。南方电网梅州宝湖项目正式投运标志着浸没式液冷这一前沿技术在新型储能工程领域的成功应用。
l 冷却方式及冷却液循环方式
冷却方式分为单相和相变两种方式,采用单相浸没液冷,主要包括矿物油、硅油、天然酯等。而另一些方案则采用两相浸没液冷,以氢氟醚为主要代表,利用相变潜热进行散热,提高散热效率。据不完全统计,当前发布的浸没式液冷储能系统中以“单相浸没冷却”的方案居多。
据冷却液的循环方式的差异,在单相浸没液冷又有三条技术路线:自然对流、泵驱动、浸没式耦合冷板式液冷。自然对流利用液体受热后体积膨胀、密度减小的特性,实现热冷却液的上浮和冷却后的下沉,从而完成循环散热;泵驱动系统的核心是液冷机组驱动冷却液在液冷管路及电池浸没箱之间循环流动,完成整个循环散热过程;而浸没式耦合板式液冷的方案中,电池浸没在介电流体中,与介电流体接触的冷板用来带走热量,避免使用复杂的二次回路来冷却介电流体。
l 产品形态与集成方案
浸没式液冷储能系统的集成方案迭代是一个从整体到局部、再到细节的过程,每一步都在前一阶段的基础上进行优化和改进,以实现更高的性能和安全性。
从舱级到Pack级,系统集成技术呈现出场景定制特点。储能场景的多元化使得对储能系统的需求各一,单一产品与无法满足市场需求,模块化设计使得储能产品可以根据项目的规模和电力需求进行优化和扩容,允许根据不同的应用场景和需求快速调整和部署储能解决方案。
3-产业化进程中的挑战及落地场景
浸没式液冷储能系统在商业化过程中面临经济性、技术复杂性、市场接受度、产业链成熟度等多方面的挑战。
l 技术复杂性:相较于冷板式液冷系统,浸没式液冷系统的设计和实施更为复杂。
l 产业链成熟度:浸没式液冷技术的产业链尚未完全成熟,这限制了其在更广泛领域的应用。产业链的成熟度直接影响到技术的推广和商业化进程。
l 经济性挑战:在当前储能行业仍处于商业化发展的初期阶段,盈利性不足使得高成本的技术路线难以受到市场青睐。许多企业在为了一时订单而进行低价竞争,导致浸没式液冷的渗透率受到限制。
当前,储能行业的主要市场仍以风冷和冷板式液冷为主,浸没式液冷尚未完全被市场所接受。尽管浸没式液冷技术的市场渗透率与接受度不高,但在一些特殊的场景下可能展现不出可观的潜力,比如:
l 危化品行业:危化品企业对于储能设备的安全管控极为严格,因为其生产和存储的化学品大多具有高度易燃、易爆、有毒或腐蚀性,一旦发生事故,不仅会对企业自身造成严重损失,还可能引发环境污染和对周边社区造成危害。
l 基站、数据中心:基站、数据中心对热失控容忍度低,数据中心储能系统需保证性能稳定、不易发生热失控的电池,以确保系统的安全性。对电能质量的要求高,需要储能系统具有快速的响应能力,在电网发生故障或停电等紧急情况先,储能系统需能够直接切换至放电模式,以保证电力的连续性和稳定性。
l 快充电站:高倍率充放电时,电池在短时间内产生大量热量,会导致电池温度过高和温度不均,对电池的性能、寿命和安全性构成威胁,就意味着高倍率充放电场景下,电池的热管理变得尤为重要。
我们会定期更新有关热设计与轻量化的技术与资讯,与您分享,供您参考,感谢您对迈泰的关注。
电池包的气密性是电动汽车及储能系统中至关重要的指标,电池包的气密性检测主要针对电池包壳体、接口、连接件、冷却组件等进行检测,以保证电池包内部不受外界环境的灰尘、水气等杂质污染或侵入,冷却组件不发生漏液,确保电池包维持正常的性能和寿命,不发生短路或爆炸等安全事故。
1-电池包的防护等级与气密性检测标准的制定
国际防护等级认证(International Protection Making,IEC60529),也称作异物防护等级或IP代码(IP Code)。IP(Ingress Protection)防护等级系统是有国际电工委员会(IEC)制定的,用于对电气设备外壳对异物侵入和水侵入的防护等级进行分类的标准。电池包箱体的气密等级通常要求达到IP67或IP68,这就意味着电池包箱体需要完全防止灰尘进入(防尘等级6),并且能够在一定压力的水中浸泡一段时间,外壳进水量不致达到有害程度(防水等级7),更严格的要求电池包在1m深的水下浸泡60min而无水进入(防水等级8)。IP防护等级通常由两位数字组成,数字越大,表示防护等级越高,见图1:
图1:IP防护等级说明示意
为了确保电池包IP67、IP68的要求,电池包需要进行沉水测试,此方法耗时较长,对动力电池包具有破坏性,且具有一定的安全风险,并不适合作为动力电池的下线检测。因此使用气密检测来保证电池包满足IP67、IP68的要求成为行业通用做法。气密检测标准的制定需要考虑压降值与泄漏率之间的关系,以及孔径与漏水的关系。气密性检测标准制定时涉及从理论极端到实验验证的一系列步骤,以实现IP等级到气密性检测标准的转换。如,以IP68为例:
图2:气密检测标准制定步骤
2-气密性检测方法选择及检测难点分析
电池包设计和制造质量是影响气密性的关键要素,包括电池箱上盖的韧性和强度、电池包壳体、接口和连接件等部位的密封及防爆透气阀、电气接插件本身的密封性等。此外,使用过程中也会带来一些问题影响气密性,如:热膨胀收缩问题、材料老化及振动冲击影响等。在电池包壳体生产制造中我们更关注焊点和接头质量等问题造成的气密不良,比如焊点不均匀、不牢固或存在裂缝、气隙,接头连接部位密封不良等。
电池包气密性检测主要分为上壳体、下壳体、总装件的气密性测试,上下壳体的气密性测试必须满足总装后的气密性泄漏要求。选择电池包气密性测试方法时,一般会综合考虑电池包的特性、测试精度要求、生产效率以及成本等因素。
工程中电池包壳体测试一般会分为制程气密检测、出货气密检测。并且上下壳体的气密性测试必须满足总装后的气密性泄漏要求,对检测标准提出了更严格的要求。要保证气密性满足要求,实操中必须克服以下困难:
l 产品结构稳定性:焊缝的质量,包括塞块焊缝、水嘴焊缝、横梁焊缝、边框底板焊缝、边框前后封板焊缝等,焊缝漏气问题主要集中在起弧、收弧处及因烧穿导致的不良等;焊接变形应力造成的开裂,如底板腔体侧壁焊接、底板腔体材料分层,无法承受焊接变形应力等。
l 气密工装的适配性与稳定性:工装设计应紧密贴合被测件的外形和尺寸,确保在检测过程中被测件能够稳固的固定在工装上,减少因为位置偏移或晃动导致的测试误差。然而,实际上电池包尺寸和形状差异较大,就需要设计和制造多种不同的测试工装,增加成本和操作复杂性,如果设计一种通用型工装,这又会加大设计复杂度。
l 气密性检测结果的可重复性:气压、温度、测试工件/夹具的干燥状态等因素都会影响气密检测结果。
l 对于工件存在较多不贯穿的微小裂纹,受检测设备精度、检测参数等因素的影响,可能存在泄漏源未能发现,出现漏检现象。
图3:气密检测工装
3-工程中常用的电池包气密检测方案组合
电池包壳体制程气密测试一般会做气密性试验和浸水试验,在气密性试验中,电池箱上盖被密封,只留一个插接件口作为进气口。通过控制气压并观察是否漏气来判断电池包的气密性。而浸水试验则是将整个电池箱体完全浸入水中,通过检查箱体内是否浸水来判断其气密性。
氦气检漏法是一种利用氦气作为示踪气体,通过检测泄漏点的氦气浓度来实现泄漏检测的技术。当氦气进入被检测设备的内部或外部可能存在泄漏的部位时,如果存在漏孔,氦气会迅速通过漏孔进入或逸出系统,并被质谱仪检测到。氦气检漏法的检测效率较高,尤其是在检测微小泄漏方面。
图4:泄露检测方法比较
在实际生产中,通常会结合多种检测方法以提高检测效率和准确性。例如,氦气检漏法适用于高精度和微小泄漏检测,而压差法则具有高精度和快速响应的特点。此外,传统的水检法虽然检测精度低,但是直观且成本低,是定位泄漏点的便捷方式。
我们会定期更新有关热设计与轻量化的技术与资讯,与您分享,供您参考,感谢您对迈泰的关注。
储能液冷Pack的液密潜在失效会涉及多个方面,如:泄漏、腐蚀和沉积、冷凝水等故障模式。
1-流体互联及组成
在储能液冷系统中,流体互连负责在各个组件之间传输冷却液,通过有效的流体互连,确保冷却液在系统中的高效循环,从而带走电池充放电过程中产生的多余热量。
密封性良好的系统可以有效防止冷却液的泄露,泄漏不仅会导致冷却液的损失,需要频繁补充,还会影响系统的散热性能和稳定稳定性,在储能中冷却液泄露还可能会造成电池短路,引发安全问题。
2-流体互连系统液密设计
流体互连系统的液密设计是确保系统在各种操作条件下保持密封性和防止流体泄露的关键环节。
图1:储能液冷系统典型部署
(1)分析系统中可能的泄漏源与风险点:
l 液冷组件的自密封性,如,在液冷流道系统与Pack箱一体设计中,部件通过焊接进行连接,焊接质量缺陷,焊合不良、气孔、裂纹等,都可能导致渗液问题。
l 结构设计不合理,如液冷箱的定位孔或螺纹孔距离流道过近,焊合不良的部位容易成为渗液的通道。
l 连接部位:液冷系统的管道连接、阀门和接头等部位是常见的泄露点,若连接结构设计不合理或制造工艺不精良,接头内部存在微小缺陷,冷却液也可能从这些缺陷处泄漏出来。
l 由于安装不当、材料老化或损伤等原因导致的泄露。
(2)密封结构设计:
l 液冷PACK使用干湿分离式冷板冷却方式,在正常工作情况下,电芯与冷却液无接触,可保障电芯正常工作。储能液冷箱一种方案是通过挤压工艺成型,流道直接集成在冷板上,然后机械加工打通冷却循环路径。在这个过程中,选择合适的焊接工艺是确保密封性的重要步骤。具体详见《储能用下箱体拼焊工艺设计》。
l 液冷管路主要用于连接液冷源与设备之间、设备之间、设备与管路之间的过渡软(硬)管连接。主要连接方式有:
快插连接:储能液冷系统的连接方式之一是采用VDA或CQC快插连。
螺纹连接:连接结构的两端均滑动连接有管道,内螺纹圈与螺纹套的螺纹连接,增加了连接的牢固性。
限位管和螺母连接:管道一端卡接有连接管路,连接管路两侧固定安装有限位管,限位管内部固定安装有橡胶垫圈和凸圈,连接管头表面开设有限位圈槽,限位管顶部转动连接有螺母,通过螺纹与限位管进行转动连接。
密封圈连接:螺纹套的内壁通过强力胶粘附有密封圈,密封圈的内壁与管道的外表面活动连接,以防止使用过程中漏液。
(3)PACK液冷板、舱内接口、舱内管路等,均考虑在常用冷却液、常用温度、流速条件下的长期防腐蚀,可保障长时间工作不出现腐蚀。操作条件对液密性的影响:
l 温度。高温影响,随着温度的升高,液体的粘度通常会降低,这可能导致液体的密封性能下降,从而影响液密性。例如,某些密封材料在高温下可能会发生变形或老化,导致泄漏。低温影响,在低温环境下,液体可能会变得粘稠,增加了流动的难度,但也可能提高密封材料的性能,从而在一定程度上增强液密性。
l 压力。 高压环境,在高压下,液体的密度和粘度可能会增加,从而提高液体的密封性能。然而,过高的压力也可能对密封材料造成损坏,导致泄漏。低压环境,在低压下,液体的密封性能可能相对较弱,特别是如果密封材料本身存在缺陷或老化,更容易发生泄漏。
l 流速。高流速,液体在高速流动时,可能会对密封面产生较大的冲击力,导致密封材料的磨损或变形,从而影响液密性。低流速,在低流速下,液体的密封性能相对较好,但这也可能掩盖一些潜在的密封问题,如微小的材料缺陷。
3-腐蚀与沉积问题
l 堵塞对秘密性的影响:
冷却液中的颗粒物、沉淀物或微生物生长都可能导致管道内部堵塞,影响冷却液的流通性,进而降低冷却效率。
污垢和结垢:冷却液中的矿物质在长时间运行后可能会在管道内壁形成沉积物,即所谓的“水垢”;也可能会因为固体颗粒沉淀、结晶、腐蚀或微生物活动而形成污垢,这些污垢会堵塞管道和冷板,增加流动阻力,降低传热效率。
泡沫问题:液冷系统中可能会产生泡沫,泡沫会附着在冷板表面,导致传热效果下降,并可能增大系统运行中的阻力,对泵造成气穴腐蚀等,损坏设备。
l 涡流对气密性的影响:
当流体在管道或缝隙中流动时,速度变化会导致涡流产生,特别是在流体经过狭窄部分或障碍物时,涡流更容易形成。流体的粘度和密度也会影响涡流的产生。粘性较高的流体更容易形成涡流,而密度较大的流体可能减弱涡流的形成。
泄漏通道:涡流会在接触表面形成旋涡,这些旋涡可能会在缝隙或不规则表面形成微小的泄漏通道,从而导致气体或液体的泄露。
表面磨损:涡流流动会导致接触表面磨损,特别是在高速流动的情况下,这种磨损会进一步降低气密性,因为磨损的表面更容易形成新的泄漏通道。
热效应:涡流流动会产生热量,这可能会导致接触面材料的变形或热膨胀,从而影响气密性,特别是在温度变化较大的系统中。
4-冷凝水问题
在某些条件下,液冷管路可能会形成冷凝水,这可能会导致设备损坏或效率降低。保温失效:如果管道的保温材料破损或老化,会导致热量散失,影响冷却效果。特别是在低温环境下,保温失效会使管道表面结霜或结冰。冻裂:在寒冷环境中,如果没有采取适当的防冻措施,管道内的冷却液可能会冻结,导致管道破裂。
解决方案
l 密封措施:确保液冷管路的进/出水管口完全封堵,防止外界潮湿空气进入电池舱。
l 除湿设备:安装除湿空调或使用除湿功能,维持电池舱内的湿度在合适范围。
l 温度控制:通过安装空调或通风系统,控制储能柜所在环境的温度和湿度,例如将温度保持在20-25摄氏度,相对湿度控制在40%-60%。
l 隔离措施:对空着的电池架进行简易隔绝,防止湿气进入装有电池簇的舱室。
我们会定期更新有关热设计与轻量化的技术与资讯,与您分享,供您参考,感谢您对迈泰的关注。
储能Pack的全密封设计是确保其安全性和长期稳定运行的关键,密封本质上是用一种装置来密闭(密封)一个缝隙或使一处接合不漏流体(气体或液体)的。全密封计设能够有效防止电池单元内的液体和气体泄漏,这对于保证储能系统的安全和稳定运行至关重要。因此,设计时既要考虑气密性也要保证液体介质的密封性。
储能Pack密封设计在实际操作中需要综合考虑材料、工艺、检测设备、环境条件以及制造过程中的多个因素,以确保其密封性能能达到预期标准。本文从Pack箱体气密、液冷循环液密及液冷工质等方面阐述储能Pack密封设计在实际工程的应用实践及注意要点。
上篇:储能Pack箱体气密性设计
密封设计有助于维持储能Pack内部的温度和压力稳定,这对电池的正常工作和性能发挥起到关键作用;并且密封设计可以减少外界环境对电池内部的影响,比如湿气、尘埃和其他污染物等,从而提高系统的可靠性和使用寿命。此外,采用合适的密封材料和结构可以有效提高密封件的耐磨性和抗老化性能,增强整个储能系统的耐久性,减少维护成本。
气密设计的一般思路是通过箱体结构分析,找出可能存在泄漏的重点区域,然后针对不同区域具体性能、功能需求采取针对性的措施。
1-箱体结构分析
箱体不仅是电池模组、电气件等的物理载体,更是整个储能系统安全、可靠运行的重要保障,是储能Pack的“骨架,一般由上盖、下箱体、支撑组件、密封件及螺栓等组成。
图1:储能pack箱体示意图及密封设计重点关注区域(如,红色箭头标注)
如上图,找出潜在泄漏点可能出现区域:
l 多个零件连接处,如:箱体上盖与下箱体装配界面、高低压连接器与箱体安装界面、外露器件与电池箱体安装接口等。
l 如果采用螺栓固定连接,安装固定处亦可能存在泄漏风险,如,电气接口与箱体前面板安装界面。
l 箱体的上盖、下箱体不能出现漏洞、缝隙,确保箱体的密封性和防护性能。
图2:浸没式液冷下箱体(钣金边框+铝型材液冷底板)
2-上盖与下箱体安装界面密封设计
上盖一般可以分为平板式和异型式两种,它们的结构特点也各不相同,比如SMC复合材料、铝制,无论是何种材质,为了减少自密封结构的复杂性,电池壳的上盖通常采用整体式设计。此外,上盖的开孔要求也应符合接口的要求,并且应将其独立于密封界面,以减少对电池包密封的影响。上盖密封设计一般遵循以下原则:
l 采用一体式零件设计,避免分件设计,确保上盖“自密封”性能的稳定。
l 定位孔、定位特征设计在上盖边缘(上盖和下托盘密封界面外侧)。
l 上盖与下箱体密封界面,需要匹配面满足“均匀”、“连续”的密封要求。
目前储能Pack下箱体主流方案有:钣金箱体+液冷板、压铸箱体+液冷板、型材一体式箱体、压铸一体式箱体等,其中型材一体式箱体与其他方案对比,具备流道承重能力好、开模成本较低等优点,应用广泛。焊接工艺的选择对密封性能影响很大,对于不同材料、厚度的焊件,选择合适的焊接方法能有效提升焊缝的质量,以保证系统的整体强度和密封性能。
另外,下箱体密封设计应当遵循如下密封原则:
l 采用封闭截面型材进行框架的搭建,接头处采用自密封的线性连接技术,如CMT焊接技术。
l 铝型材拼接的电池托盘需要设计有连续的一道或多道密封胶体。
l 下箱体集成液冷板的情况下,需要考虑使用胶体密封或采用自密封的线性连接技术,如FSW搅拌摩擦焊技术。
l 上盖与下箱体密封界面,需要匹配面满足“均匀”、“连续”的密封要求,必要时进行机加工对密封界面进行打磨处理。
图3:箱体上盖与下箱体常见密封形式
通常,储能Pack箱上盖下箱体采用折弯翻边加密封垫设计,见图2。利用紧固螺栓使上盖、下箱体与密封垫充分压实耦合,保证Pack箱满足IP67的相关要求。
3-电气、通信接口与下箱体前面板安装界面密封设计
箱体前面板(如图3),在挤出成型的型材上进行机加工开孔,用于安装电气、通信等接口,实现电流传递、通讯交互、安全控制等功能。
图4:电气、通信接口与下箱体前面板安装界面
箱体与电气、通信等接口安装界面气密性遵循以下原则:
l 接口形状设计成流线型以减少气体和液体在接口处的积聚和渗透可能性。
l 精确对位,避免接口在安装时错位导致的缝隙。
l 安装前对接口进行预密封处理,增加防震垫或密封胶,以增强初始密封效果或减少因振动导致的密封失效。
另外,紧固件的选择方面,使用高强度、高扭矩的紧固件,并在安装过程中进行多次紧固,以确保接口的紧密性。如使用碰焊螺母,其特点是能够直接连接与被连接件(箱体前面板)的壁孔进行碰焊,这种结构设计能够显著提高连接部位的气密性。
图5:使用碰焊螺母增加气密性
4-密封件选择
密封件设计和选择至关重要,因为它们直接影响到系统的可靠性和使用寿命。以下是在设计和选择储能液冷系统密封件时应考虑的关键因素:
l 密封材料必须有一定的化学、压力兼容性,同时能够耐受系统工作温度范围,包括高温和低温环境。密封件的材料选择取决于使用环境和使用寿命要求。常见的密封件材料包括橡胶、聚四氟乙烯(PTFE)、尼龙、金属等。
l 泄漏自由度:密封件必须能够适应系统在工作过程中可能出现的微小变形,以确保在各种工况下均保持良好的密封效果。一般密封垫的变形量要大于30%,小于60%,密封界面压力大于30kPa。
我们会定期更新有关热设计与轻量化的技术与资讯,与您分享,供您参考,感谢您对迈泰的关注。
在纯电动汽车中,电池包的重量约占整备质量的30%左右,电池包轻量化,对于提升整车续航里程有着重大意义。因此,对电池包高比能量的研究是新能源汽车目前的主要研究方向之一,也是实现电动汽车轻量化的主要途径,实现动力电池包轻量化可从两个方向开展:提高单体电芯的能量密度,对电池包相关辅件进行优化设计。
多材料轻量化电池包开发旨在通过采用多种轻质材料,降低电池包的重量,提高能量密度和续航里程,同时保证安全性和可靠性。电池Pack各主要部件中,质量最大的是电芯本体,其次为Pack下箱体、上盖、BMS集成部件等。
1-电池包上盖轻量化
电池箱的上盖位于动力电池箱体的上方,不受动力电池箱体侧面的影响,也不会影响整个电池组的质量,其功能主要包括密封、保护等作用。为了提高整车能效,在设计中也会考虑轻量化,采用轻质材料,如铝合金、复合材料(SMC、FRP等),可以显著减轻电池包的重量。
此外,上盖的结构设计还需要考虑制造效率和批量化要求,在结构非常异形的情况下,采用冲压成型或折弯拼焊可能较为困难。上盖的设计还需要考虑到与下箱体、密封结构件等其他部件的连接与配合,确保整个电池箱体的结构稳定性和可靠性。
2-电池包下壳体轻量化
铝合金是电池包壳体制作的理想材料,因其密度低、比强度高、热稳定性好、耐腐蚀性强、导热性好、无磁性、成型容易以及回收价值高等诸多优点。常用的铝合金材料包括6061-T6、6005A-T6和6063-T6等,这些材料具有不同的屈服强度和抗拉强度,可以满足不同的结构需求。
电池包壳体通常由铝合金型材边框和底板构成,采用6系铝合金挤压型材拼焊而成。设计时需要考虑型材断面大小及复杂性、壁厚等因素,以适应不同的结构和功能要求。例如,边框、中间隔板、底板、横梁等部件可能会采用不同的断面设计。
通过合理的结构设计和连接方式,可以有效保证壳体整体强度,降低加工难度,实现壳体减重:
l 薄壁化:通过采用薄壁设计,配合加强筋来满足强度要求,可以有效减轻材料重量。
l 中空化:在结构设计中引入中空部分,以降低材料密度。
l 尺寸优化:优化电池包的尺寸,减少不必要的材料使用。
l 拓扑优化:通过优化电池包内部组件的布局,减少材料占用空间。
l 集成模块化设计:将冷却板、电池包吊耳等部件集成在箱体中,减少单独部件的数量和重量。
3-制造轻量化技术
l 材料成型
目前电池箱材料成型工艺主要有三类:冲压、铝合金压铸和铝合金挤压成型。动力电池箱整体工艺流程包括材料成型及连接工艺,其中材料成型工艺是动力电池箱体的关键工艺。当前上壳体以冲压为主,下壳体主要工艺为挤压成型及铝合金压铸成型两种方式。
l 连接技术
电池箱体连接工艺在新能源汽车制造中至关重要,涉及多种技术和方法,以确保电池箱的结构强度和密封性。
焊接是电池箱体加工中的主要连接工艺,应用广泛。主要包括以下几种方法:
①传统熔焊:如TIG(钨极惰性气体保护焊)和MIG(金属惰性气体保护焊)。TIG焊接速度低,质量高,适用于点固焊和复杂轨迹焊接,常用于边框拼焊和边梁小件焊接。MIG焊接速度高,熔透能力强,适用于边框底板总成内部整圈焊接。
②搅拌摩擦焊:通过摩擦产生热量实现焊接,具有接头质量好、生产效率高等特点。
③冷金属过渡技术:适用于薄板材料,焊接过程无热输入,减少变形。
④激光焊:高精度、高速度,适用于复杂结构焊接。
⑤螺柱焊和凸焊:用于特定部位的快速连接,螺柱焊通过螺柱和螺母实现紧固,凸焊则通过凸点压紧实现连接。
机械连接方式主要解决薄板材料在焊接中的易焊穿和螺纹滑牙问题,包括:
①拉铆螺母:用于箱体边框密封面和内腔底板的连接,具有紧固效率高、使用成本低等优点。适用于薄板与其他部件的螺纹联接。
②钢丝螺套:用于加强铝或其他低强度机体的螺孔,提高螺钉的承载能力和螺纹的受力分布,适用于电池模组安装孔和密封面安装孔。相对于拉铆螺母,钢丝螺套强度更高且易于修复,但一般不适用于薄壁安装。
我们会定期更新有关热设计与轻量化的技术与资讯,与您分享,供您参考,感谢您对迈泰的关注。
要应对大跨度、快迭代、丰富产品线等市场需求,还要保证降本增效保质,对汽车行业而言,通过产品标准化——造车平台化无疑是项不错的策略,通过电池平台化为不同的车型匹配同一个电池包方案,或者匹配由同一种电芯组成且结构相近的电池包方案,这就意味着尽可能的多零件通用化,可以缩短开发周期、节约成本、精简产线与提高生产效率。
一、电池平台化
电池平台化方案有利于产品的统筹规划、成本的降低和产能的优化。根据整车平台的电池平台化策略,需要考虑平台各车型需求的交集与带宽,用尽量少的电池与电池方案兼容尽可能多的车型。在纯电动项目的架构开发中,合理布置集成动力电池包是至关重要的,具体工作要素包括电量与动力性能需求、碰撞安全、布置位置与空间等。
1-空间尺寸边界与电芯标准化
l 电池包可用布置位置
目前主流的动力电池布置位置为地板下方,包含前座椅下方、后座椅下方、中通道位置及脚踏位置。这种布置方式能够最大限度的获得可用面积,并且有助于降低车身重心、提高整车操纵稳定性和优化碰撞传力路径。
图1:电动车发展过中电池包布置位置
l 电池包空间布置形式演化
分体式电池包:采用分体式的电池包空间布局形式,如江淮同悦系列,能量模块由两个电池包组成,一个放在原来油箱位置,一个放在车尾箱存放备胎位置。
此外,工程师们在燃油车原来架构上不断发掘可利用空间,电池包布局出现了“工”字形、“T”字形、“土”字形的形式。
此类设计是在传统燃油车基础上做较小的改动,空间非常有限,能够装载的电池包体积和重量都很受限,因此容量也很难提升,续航里程不高。
一体式电池包:这是一种全新的产品设计思路,整车设计围绕核心零部件——电池包展开,将电池包进行模块化设计,平铺在车辆底盘上,以最大限度获得可用空间。
l 电池包安装点布置
合理布置电池包至关重要,限制要素设计离地间隙、通过性、碰撞安全和电量需求等诸多方面。
图2:电池包尺寸设计约束
整车平台需定义平台内各车型的类别、级别与定位,进而确定了车辆的大小、轴距,整车布置根据整车空间分解出电池包在X、Y、Z方向的尺寸包络,电池需要在整车给定的包络内进行布置,保证整车各系统间不出现干涉,而整备质量指标可分解出电池包的系统质量要求。
在电池尺寸这一指标上,动力电池包的设计绕不开整车空间、整备质量等硬性参考指标,这就意味着电芯的设计存在阈值,受到这个阈值的约束,电芯尺寸就会往某个特定的区间进行集中,如:方形电芯长度范围150-220mm,宽度范围在20-80mm,高度范围在100mm左右徘徊。电芯尺寸规格的变化趋势正是造车平台化与电池标准化相辅相成的结果。
然而,各车企电池平台策略、承载车型及对标准化的理解也有所差别,致使当前所呈现出来的产品方案仍有较大差异。如比亚迪的标准化策略是全面更换刀片电池,刀片电池的尺寸标准锁定为960*13.5(14)*90(102)mm,单体电压3.2/3.3V。
2-续航边界与电池电量方案开发
动力电池为整车行驶提供能量:电池容量、放电深度、能量密度影响可供电量。为满足不同车型的需求,车型的电耗差异成为重要关注项目,车辆的续航里程会受电驱、电池、整备质量、风阻、机械阻力、低压电耗及能量回收等因素的影响。电耗差别大的车型间共用电池方案的可能性弱,就需要针对性的开发个性化的电池电量方案,包括电池尺寸、质量、电量及做功率性能优化,以满足续航性能的要求。
在造车平台纯电续航里程的约束下,电池需求净放电量会受不同车型电耗的影响,需要确认平台各车型的电耗分布,才能进一步将该电耗带宽转化为电池的需求电量分布,进而确定平台所需电池电量方案。
3-动力性能边界
整车的动力性包括不同SOC、不同环境温度下的加速工况、等速工况和保电工况下的动力表现,对应到电池的变量就是电池在不同SOC和温度下的功率-电压特性,电池的功率对应整车动力系统的功率要求,电压对应驱动电机的额定电压需求。
一般对整车平台电池方案评估从常温高电量下的百公里加速时间及其电池指标分解,逐步延伸到全域全工况的电池指标分解。
二、电池箱体开发
1-电池集成与模块化
优化电池模块的设计,提高电池组的集成度和模块化,减少非活性组件,提升电池组的能量密度。
当前流行的电池包集成技术有CTP、CTB、CTC等各种形式,零件的外形、材质和组合形式等都伴随集成技术的进步发生了改变,整体方向是一体化、集成化,通过减少独立零件数量、使用一个大零件替代几个零件,形成尺寸更大、功能更多的组件。
2-电池箱体方案设计
电池箱体是动力电池系统总成的载体,对产品的安全运行和防护起着关键作用,直接影响整车的安全性。电池箱体的结构设计主要包括电池箱上壳体、下壳体等部件的壳体材料选择,制造工艺方案选择等。电池箱体上盖主要起密封作用,受力不大;电池箱体下箱体是整个动力电池系统产品的承载件,电池模组主要布置在下箱体里面,因此电池箱体内部要有嵌槽、挡板等结构措施,使电池模组在车辆行驶的状况下可靠固定,在前后、左右、上下各个方向上均不发生窜动,避免对侧壁和上盖造成冲击,影响电池箱体寿命。
图3:电池下箱体方案,a-蒙皮框架、 b-FSW焊接+围框、c-FSW焊接+围框
l 电池包安装点结构设计与连接固定
电池包安装点通常采用安装梁结构,这种结构前后贯通,前端与前舱纵梁连接,形成有效、连贯的封闭梁结构,并根据电池包重量分布,合理布置安装点。电池包与整车的固定方式包括螺栓固定、机械固定+胶接混合连接、卡扣连接等。
图4:电池包布置与安装断面
动力电池包一般通过多个吊耳结构安装至整车上,吊耳处理要承受动力电池包自身较大的自重外,还要承受汽车行进时带来的路面激励,如石块路和深坑等,此类耐久工况和误用工况对吊耳结构的强度提出更高的要求。
图5:不同吊耳连接方案:a焊接吊耳 b铝挤边框吊耳
l 电池箱体安全与保护结构
机械强度和防护:电池箱体应具备足够的机械强度,以确保其内部电池免受机械撞击和冲击。电池箱体需要能够承受振动、挤压和机械冲击等,以确保在各种条件下电池的安全性。
碰撞保护:电池箱体的设计必须考虑碰撞安全性,特别是针对侧向碰撞和底部碰撞的情况。通常采用铝制或钢制材料,并通过外框架连接到下部托盘,以提供结构刚度并增强碰撞能量吸收能力。此外,还应设计适当的碰撞吸收结构,以防止电池外壳变形和电池单元损坏。
防水防尘和防腐蚀:电池箱体需要具备防水防尘功能,通常采用IP67级别的密封胶垫来保证气密性能。此外,还应考虑防腐蚀措施,如在外部喷涂PVC涂层以增强耐腐蚀性。
防爆和泄压设计:当电池发生爆炸时,应通过平衡防爆阀等装置使能量集中定向泄放,避免进入客户舱。此外,还应采取防爆措施(如部分破坏结构)以防止设备整体破裂。
l 密封设计
电池箱体上盖与下箱体之间密封面的设计对密封性起重要作用,其设计需要配合电池箱体结构和密封圈一起设计。密封面应尽可能保持在同一个平面,避免出现较多的曲面结构。由于上盖和下箱体是通过螺栓连接,所用螺栓数目较多,因此保证孔的同轴度尤其重要,需在合理布置螺栓孔位置的同时,位置尺寸尽量圆整,且在X、Y向呈对称布置。连接螺栓数目的选择需根据密封性高低和拆装工作量大小两方面综合考虑。
图6:上下箱体密封设计方案,1-电池上盖 2-密封垫 3-电池下盖 4-金属导管
l 电气安全和短路保护
连接可靠性:电池箱体内的连接器应具有正确的极性连接,确保电池箱体的过流能力和电气/机械连接的可靠性,包括放松措施等。
电气绝缘耐压设计:模组设计采用双重绝缘防护电芯本身有一层电芯蓝膜及电芯顶帖片可以满足绝缘耐压要求,端/侧板与电芯间、电芯与底部安装面间设置绝缘耐压防护。
l 热管理设计
电池热管理开发贯穿于电池包系统设计开发全周期,包含电池温度控制、冷板、管路系统等的设计。电池热管理系统设计的主要目标是在考虑空间布置、设计成本、轻量化等条件下,通过加热或冷却控制,保证电池系统工作在相对适宜的工作温度,同时减小单体间温差,保证一致性。
我们会定期更新有关热设计与轻量化的技术与资讯,与您分享,供您参考,感谢您对迈泰的关注。
电池包是新能源汽车的核心能量源,为整车提供驱动电能。我们一般会从效率(能量密度)、安全、制造及维修成本等维度评价电池包技术的优劣。
在电池设计中,单个电芯的电压只有3-4V左右,而电动车所需的电压最低都要100V以上,现在的新车甚至有700V/800V的电压,输出功率一般也在200W,所以就需要给电池升压。为了满足电动车的电流和电压需求,就需要将不同的电芯通过串联、并联组合的方式相连。
电池包是将电芯、电子电气系统、热管理系统等通过电池框架结构——底板(托盘)、框架(金属框)、上盖板、螺栓等包络构成的,一直以来,如何将这些部件、系统更高效更安全的“打包”成为一个整体,是整个行业持续不断研究探索的议题。
上篇:电池集成技术创新与发展
动力电池成组技术的由来可以追溯到20世纪50年代,起源于前苏联与欧洲等一些国家。这项技术最初是作为一种工程和制造理念,用于确定零件的物理相似性(通用工艺路线),并建立其有效生产。
成组技术(Group Technology, GT)的核心在于通过识别和发掘生产活动中有关事物的相似性,将相似的问题归类成组,寻求解决这一组问题的相对统一的最优方案,以取得经济效益。在动力电池领域,成组技术主要涉及将电池由单体集成为电池包(Pack)的技术,包括结构、热管理、电连接设计和电池管理系统(BMS)技术。
汽车领域较早的成组技术为MTP(Module To Pack),即先由电芯集成为模组,再由模组集成为Pack。这种技术的特征是模组可拆卸和更换,具有较好的可维护性,但成组效率较低。随着技术的发展,成组技术经历了从MTP到CTP(Cell To Pack)的转变,CTP技术指将电芯直接集成到Pack的技术,取消了传统的模组结构,提升了成组效率和生产效率。近年来,行业还在探索更高集成效率的CTC(Cell To Chassis)、CTB(Cell To Body & Bracket)和MTB(Module To Body)等成组技术。
在动力电池及电化学储能领域,锂电池主要的技术进步来源于结构创新和材料创新,前者是在物理层面对“电芯—模组—电池包”进行结构优化,达到兼顾提高电池包体积能量密度与降低成本的目的;后者是在化学层面对电池材料进行探索,达到兼顾提高单体电池性能与降低成本的目的。本文注重从电池包结构集成视角探讨不同结构集成技术对电池包制造技术的影响及创新发展方向,当前动力电池集成关键技术,见下图:
1-已被淘汰的MTP
在当前这波电动汽车发展潮流的伊始,很多油改电新能源车型上市,它们延续传统油车的空间布局与造型设计,工程师们将一定数量的电芯单体通过串/并联的方式,组成一个相对较大的电芯模组,然后再将几个这样的电芯模组布置到电池包中,也就是我们熟悉的“MTP”电池包,由于电池包需要“打包”两次以上,因此需要的零部件数量十分庞大,电池包也以“里三层外三层”的形象示人,过多冗余部件也占据更多的系统体积空间和重量,使得“MTP”电池包在体积能量密度、质量能量密度表现差;并且因为燃油车设计过程并没有专门为电池预留空间,电池系统只能“见缝插针”地塞进车内,产品力低下,用户体验欠佳。
自以特斯拉为代表的全新智能化电动车平台推出以后,原生纯电动车使得电池包以更高效、规整的安装在理想的空间位置上,三电系统可以更合理的布局,整车的电子电器架构及热管理设计实现更高效的集成,车辆的能效、续航、智能化维度的产品力极大加强。
2-集成技术2.0时代——CTP
MTP结构的电池包存在显著的空间利用率问题,电芯对模组的空间利用率为80%,模组对电池包的空间利用率为50%,整体空间利用率仅为40%,模组硬件费用约占电池电池总成本的14%,这种低空间利用率结构无法满足新能源汽车的发展要求。在电芯→模组→电池包→车身集成思路的框架下,整车想要在有限的底盘空间内尽可能装载更多电量,提高体积利用率,就要考虑每个集成步骤的标准化,随着市场对续航里程需求的不断攀升,单个电池模组的体积不断增大,间接带动了CTP方案的出现。
出于安全、封装复杂程度、降本等方面的考虑,CTP结构技术应运而生。在保证电芯安全的前提下,CTP技术减少了内部线缆和结构件,相比MTP技术,CTP技术没有模组结构,直接由电芯封装成电池包再安装到车上。
目前主要有两种思路,一是将Pack看成是一个完整大模组替代内部多个小模组的结构,以宁德时代为代表;二是设计时即考虑采用无模组方案,以电池本身作为强度的参与件去设计,例如比亚迪刀片电池。
CTP技术的核心点就是取消了模组设计,电芯直接与壳体相结合,减少了端板与隔板的使用,随之而来的问题是电池组的固定以及热管理问题。
实际上CTP电池包的最初产品并非是纯无模组的设计,而是将原有的小模组合并为3个大模组和2个中模组的设计,并且两端同样存在铝制端板,所以理论上依然是MTP,但结构上确有很大的进步。
而到CTP3.0之后,宁德时代给出了更为先进的制造方式,实现了彻底的无模组设计,电芯从原来的沿高度方向立置改为侧置,同时提盒电芯间采用了全新的冷却方案,除却散热外,冷板还承担了支撑、缓冲、隔热、温控等多种功能;底壳也做了限位固定设计。
图1:宁德时代麒麟电池CTP2.0与CTP3.0对比
3-集成技术3.0时代——CTB、CTC
a. CTB技术
CTP技术是电池结构创新的一大进步,却没有突破电池包本身,在CTP技术中,电池包仍然是一个独立的零部件,相较于CTP对电池包的精简策略,CTB技术把车身底板面板与电池包上盖合二为一,电池上盖与门槛及前后横梁形成的平整密封面,通过密封胶密封乘员舱,底部通过安装点与车身组装。在设计制造电池包的时候,把电池系统作为一个整体与车身集成,电池本身的密封及防水要求可以满足,电池与乘员舱的密封相对简单,风险可控。
这样将原来的“电池包上盖-电芯-托盘”的三明治结构转化成“车身底板集成电池包上盖-电芯-托盘”的整车三明治结构,减少了因车身与电池盖连接而产生的空间损失。这种结构模式下,电池包不仅仅是能量源,同时也作为结构体参与整车的受力与传力。
图2:CTB技术结构示意
b. CTC技术
采用CTC方式后,电池包不再是一个独立的总成,而是融合为车身的一部分,优化了产品设计和生产工艺,减少整车零件数量,特别是减少了电池内部结构件与连接件,具备轻量化的先天优势,最大程度提升空间利用率,为增加电池数量、提升续驶里程提供了空间。在电化学体系本身技术不变的条件下,能够通过提升电池数量增加续驶里程。
图3:特斯拉CTC技术结构示意
如,特斯拉等车企先后推出CTC技术车型,在电芯层面可采用多功能弹性夹层结构、大面积水冷技术,叠加一体化开发带来的电池包底部防撞击空间复用技术,兼顾了成组效率、散热性和安全性,从电芯优化和整车结构防护两个维度,推进CTC技术的应用。在整车一体化开发层面,将电芯直接集成到底盘,省去模组和电池包的环节。实现大三电系统(电机、电控、电池)、小三电系统(DC/DC、OBC、PDU)、底盘系统(传动系统、驾驶系统、转向系统、制动系统)以及自动驾驶相关模块的集成,并通过智能化动力域控制器优化动力分配和降低能耗。
4-CTP、CTB和CTC技术对电池盒的具体要求变化
在传统电池包结构中,电池模组起到支撑、固定和保护电芯的作用,而电池盒箱体主要承受外部的挤压力。CTP、CTB和CTC技术的应用对电池盒的提出新的要求,具体体现在:
电池盒箱体强度要求提升:由于CTP或CTB及CTC结构中减少了或取消了模组环节,电池盒箱体不仅要承受外部的挤压力,还需要承担原本由模组承担的来自电芯的膨胀力,因此对电池盒箱体的强度要求更高。
碰撞防护能力:利用CTP技术去除电池组的侧梁后,电池将直接承受碰撞的影响,因此CTP电池组需要具备足够的抗碰撞能力。
保温、绝缘和散热需求:CTP或CTB及CTC结构在底盘承载式结构箱体的基础上,把底板型材更改为水冷板,电池盒箱体不仅要承载电芯重量,还要为电池提供热管理等功能,结构更加紧凑、制造工艺优化、自动化程度较高。
维修性便利性降低:高度集成度设计使得电池包的更换变得复杂,如在CTC结构中,电池内部电芯间充填树脂材料,导致难易更换电芯,几乎不能进行维修。
5-电池包集成度提升对电动汽车充电基础设施的影响
选择不同的电池包集成技术同时隐含选择了不同的补偿方式,CTP倾向于换电,而集成化更高的CTB/CTC则倾向于快充。
高度集成化意味着在相同的空间内可以容纳更多的电池,从而增加了电动汽车的续航里程。用户可能不再需要频繁地进行短距离充电,而是更倾向于在长途旅行中进行快速充电。因此,充电基础设施的规划需要考虑到这些变化,以确保能够满足用户的需求。
由于电池包集成度的提升,电池包的物理尺寸和结构可能发生变化,这可能影响充电接口的设计和充电设备的兼容性。
此外,电池包集成度的提升也可能影响充电速度和效率。更高效的电池管理系统和充电技术可能需要被开发和部署,以确保快速且安全的充电过程。
我们会定期更新有关热设计与轻量化的技术与资讯,与您分享,供您参考,感谢您对迈泰的关注。
新能源汽车用电池托盘和储能液冷箱在生产过程中,必要适当的表面处理是一个关键步骤,如:采用涂装、氧化处理等在金属表面形成保护层,抵御腐蚀介质的侵蚀;对需要电气隔离的组件,如电芯、水冷板、模组壁等需要建立绝缘保护膜,一般通过喷涂绝缘粉末或绝缘漆来实现绝缘;选择合适的表面处理技术不仅能够提升托盘/液冷箱的耐用性和安全性,还能满足不同应用场景的需求。本文对常见表面处理技术进行整理,以供参考。
1-清洁、打磨
在生产过程中,托盘表面可能会积累加工油污、机油残留、粉屑、灰尘等杂质。这些杂质不仅会影响电池托盘的使用寿命,还可能对电池的性能和安全造成不利影响。通过清洁打磨,可以有效去除这些杂质,确保托盘表面的洁净。清洁打磨可以有效去除表面杂质、毛刺、焊渣,使其表面光滑、平整,从而提高电池托盘/箱体的整体质量。
a.化学清洗
碱洗:碱洗主要是利用碱性溶液(如氢氧化钠、碳酸钠等)去除铝合金表面的油脂、污垢和其他有机物。碱洗通过皂化作用、乳化作用和浸透润湿作用来去除油脂,同时生成可溶于水的沉淀物,从而达到清洁的效果。碱洗通常用于去除铝合金表面的油脂、灰尘和有机污染物。
酸洗:酸洗则是利用酸性溶液(如硝酸、盐酸等)去除铝合金表面的氧化皮、锈蚀和其他无机沉积物。酸洗通过酸与金属表面的氧化物反应,将其转化为可溶性盐类,从而去除表面杂质。酸洗主要用于去除铝合金表面的氧化皮膜、锈蚀和无机盐垢。酸洗常用于金属表面的最终处理,以提高其光洁度和平整度。
b.机械打磨
生产中,通过打磨工序可以去除加工余量、修正形状误差,确保托盘/箱体表面的平滑度和精度、满足装配要求,进而提高整体性能和使用寿命。
经过清洁打磨后的表面能增加涂装材料或其他材料的处理,对后续的防腐、密封、导热、绝缘、保温等涂层的施工非常重要,对这些材料牢固的附着在托盘/箱体起到关键作用。
2-涂覆与防护膜建立
除了基础的清洁、打磨外,托盘/箱体生产中通过会采用喷涂工艺进行表面处理用以形成保护层,防止氧化、腐蚀以及满足保温隔热、绝缘耐压等不同场景的需要。
a.保温隔热
电池托盘的防凝露和保温隔热可以通过综合设计隔热保温系统、使用高效保温隔热材料、应用气凝胶、进行电池包保温设计以及喷涂发泡保温材料等路径实现。
底面喷涂PVC、发泡材料
b.绝缘耐压
电池包箱体绝缘、液冷组件绝缘,主要是防止电流泄漏,保护人员免受电击,确保电池系统的正常工作。绝缘的实现通常采用喷粉和覆膜两种方案,主流的覆膜工艺包括:室温贴膜、热压、UV光照等。
内部喷涂绝缘粉、绝缘漆
3-标志、标识
在电池托盘的显著位置设置铭牌或标签,一般通过镭射、机械雕刻等方法实现。这些标识通常采用耐磨损、耐腐蚀的介质进行制作,以保证其在整个使用期内不易磨灭。
我们会定期更新有关热设计与轻量化的技术与资讯,与您分享,供您参考,感谢您对迈泰的关注。
储能变流器作为储能系统的核心设备,是电能转换、能量管理、确保电网稳定性,提高能源使用效率等的重要工具,随着储能变流器功率单元向着高度集成化、高工作频率和大容量的发展,对散热要求越来越高。
1-散热需求变化
a.匹配更大直流舱,变流器容量不断变大,高效散热技术确保设备可靠
伴随储能电芯单体容量愈来愈大,储能系统单机容量也在同步扩大。2023年初,市面上标准20呎单舱电池容量仅为3.35MWh,进入下半年多家电芯企业相继推出310+Ah储能产品,20呎单舱的电容量也扩容至5MWh。然而,5MWh模式更新不到半年,一些头部储能紧接着又发布6MWh、8MWh系统。根据一般经验,储能变流器按负荷容量的1.2倍配置,5MWh储能系统单机容量就必须大于2.5MW,大功率需要更高效的散热技术来确保设备在持续高负载下稳定运行。
储能系统集成拓扑方案迭代演化
b.直流高压技术的应用要求器件具备更高的耐压等级和绝缘强度,功率器件散热严峻
为匹配大容量储能系统,直流高压技术成为一种技术趋势,通过电压等级的提高,实现节能增效和性能提升,1500V电压升级源于光伏,现由光伏切入储能。然而,储能PCS高压演进之路还很长,一些厂商优化开始推向2000V。直流高压技术的应用迫使储能变流器中的电力电子器件需要具备更高的耐压等级、更高的绝缘强度以适应高压工作环境。高压环境下,功率器件的散热设计变得更为重要,功率器件的pn结温度一般不能超过125℃,封装外壳的温度不超过85℃。
c.构网型储能系统需要具备复杂的控制算法、电路设计及高功率密度储能变流器
不同于跟网型储能系统电流源的本质属性,构网型储能系统本质上是电压源,能够内部设定电压参数,输出稳定的电压与频率。因此要求构网型变流器模拟同步发电机的特性,提供电压和频率的支撑,增强电力系统的稳定性,这种控制策略要求变流器具备更高的功率密度和更加复杂的控制算法,并且需要更高性能的功率器件和更复杂的电路设计来实现控制策略。如何有效地管理由于高功率密度、复杂控制策略产生的热量,在保持高性能的同时减少散热系统体积和成本成为热设计的新挑战。
2-常用散热方案比较
储能变流器的散热方案在近年来经历了显著的迭代演化,主要体现在散热技术从传统的风冷向液冷技术的转变。
a.风冷方案
风冷是储能变流器初期采用的温控形式,以空气为介质,通过风扇和散热器来实现热量的散发。风冷方案通过不断降低能耗、优化结构、改进散热材料等途径提升散热效率。在2.5MW功率等级下,风冷仍能满足要求。
b.液冷方案
随着储能系统的功率密度和能量密度不断增加,液冷PCS因为采用了高导热系数的冷却液作为介质,通过水泵驱动冷却液在冷板内循环流动,并且不受海拔和气压等因素的影响,液冷系统拥有比风冷系统更高效的散热效率,液冷方案的匹配度更高,近一两年开始探索,普及。
除全液冷储能方案外,一些厂家推出储能直冷机,采用相变直冷,无水循环。直冷方案也正在进入储能领域。
我们会定期更新有关热设计与轻量化的技术与资讯,与您分享,供您参考,感谢您对迈泰的关注。
电池包是新能源汽车、储能一体柜及集装箱的关键部件,它是通过壳体包络构成能量源,为电动汽车提供动力,为储能柜与集装箱提供消纳能力。本文结合实际工程需要,通过分析电池包机械强度、安全性、热管理及轻量化等多方面要求,对电池包用型材设计要点进行总结说明。
1-电池包壳体设计要求
a.机械强度,耐振动强度和耐冲击强度,在试验后不能有机械损坏、变形及紧固不见松动的现象,锁止机构不应收到损坏。
b.密封性,电池包的密封性直接影响到电池系统的工作安全,通常要求达到IP67防护等级,以确保电池包密封防水。
c.电池包壳体设计需要考虑热管理性能,通过适当的热管理设计,保证电池在适合的范围内工作。
d.安装固定,壳体应留有铭牌和安全标志布置位置,并为采集线、各种传感元件等安装预留足够空间和固定基础。
e.所有无极基本绝缘的连接件、端子、电触头结合后应满足相应的防护等级需求。
f.轻量化,壳体轻量化对于提升电池包能量密度有着重大意义,铝合金质轻质优是当下最可行的选择,结合实际应用通过适当的极限设计提升轻量化水平。
g.耐久性,电池包壳体的设计寿命不得低于整体产品使用寿命,使用周期内不应发生明显的塑性变形,防护等级、绝缘性能不应降低;结构具备维护方便性,包括铭牌与安全标志布置、连接件防护等。
图1典型铝合金拼焊电池包壳体
2-典型铝合金电池包壳体方案
电池包壳体常用的铝合金材料有6061-T6、6005A-T6和6063-T6等,这些材料具有不同的屈服强度和抗拉强度,可以满足不同的结构需求。这几种材料的强度大小:6061-T6>6005A-T6>6063-T6。
当前电池包壳体成型方案有铝型材焊接、铝合金铸造、铸铝加型材铝、冲压铝板焊接等,铝型材拼焊方案因其灵活性和加工方便性成为主流选择,如图1,壳体主要有铝合金型材边框、铝合金型材底板构成,采用6系铝合金挤压型材拼焊而成。铝合金铸造方案因其简化工艺和降本潜力被视为未来发展方向。
3-型材断面设计
a.断面大小及复杂性:型材断面大小用外接圆来衡量,外接圆越大,所需要的挤压力就越大;型材断面通常由多个空腔组成,以提高结构刚度和强度,通常边框、中间隔板、底板、横梁等采用不同的断面设计以适应不同的结构和功能要求。
图2典型铝合金型材断面
b.铝型材壁厚:某一特定铝型材的壁厚最小值与型材外接圆半径、形状及合金成分有关,如,6063铝合金壁厚取为1mm时,6061铝合金就要取为1.5mm左右,同等断面挤压难度:6061-T6>6005A-T6>6063-T6。电池包用型材设计中,边框型材通常选用6061-T6铝合金材料,其典型断面由多个空腔组成,壁厚最薄处约为2mm左右;底板型材也由多个空腔组成,材质一般为6061-T6、6065A-T6,起壁厚最薄处也为2mm左右;另外,在底板承重的托盘及底板液冷集成的设计方案中,一般底板均采用双面结构,底板厚度一般为10mm,壁厚及腔体内壁约为2mm。
c.型材断面尺寸公差:断面尺寸公差应根据铝型材的加工余量、使用条件、型材挤压难易程度、形状的部位来确定,对一些挤压难度大的铝型材可以改变形状或增大工艺余量、尺寸公差,来减小挤压难度,挤压出近似要求的铝型材制品,然后通过或整形或者加工满足使用要求。
此外,进行型材断面设计时需要考虑不同焊接工艺对接头、坡口、壁厚等具体要求。
我们会定期更新有关热设计与轻量化的技术与资讯,与您分享,供您参考,感谢您对迈泰的关注。
电池托盘又称电池盒或PACK箱体等,作为新能源汽车开发中十分重要的部件日益受到重视,电池托盘的设计需要平衡重量、安全、成本、材料性能等因素之间的关系。铝合金由于其密度低、强度高等优点,在保证车身性能时仍能保证其刚性,在汽车轻量化工程中得到广泛应用。
1-电池托盘焊接部位及方法选择
铝制电池托盘以挤压铝型材为基础材料,通过焊接方式将各个部件组合为一个整体,形成完整的框架结构。类似的结构在储能Pack箱中也得到了广泛的应用。
电池托盘的焊接部位通常包括底板拼接、底板与侧边的连接、侧边框的连接、横纵梁、液冷系统组件焊接及支架、吊耳等配件的焊接。在焊接方法选择时,会根据不同的材料和结构要求选择不同的焊接方法,参见下表:
2-焊接热变形影响分析
焊接作为一种局部加热的加工方法,由于热源集中在焊缝处加热,因而造成焊件上温度分布不均匀,最终导致在焊接结构内部产生了焊接变形与焊接应力。焊接热变形就是在焊接过程中由于不均匀的热输入和热输出,导致被焊件的形状和尺寸发生改变的现象。结合实际的工程项目经验,对易产生焊接热变形的部位及影响因素进行了归纳总结:
a.长直线焊接部位
实际生产中,电池托盘底板一般由2~4块铝合金型材采用搅拌摩擦焊拼接而成,焊缝较长,底板与侧板、底板与间隔梁之间连接也有较长的焊缝。长焊缝由于热输入集中,容易导致焊接区域的局部过热,从而产生热变形。
电池托盘边框焊接
b.多部件拼接处
在多部件焊接处由于焊接过程中局部高温加热和随后的冷却导致的。在焊接过程中,焊件受到不均匀的热输入,使得焊缝区域与周围母材之间的温度差异显著,从而引起热膨胀和冷缩效应,引起被焊件变形。储能Pack箱电气安装端通常设有水嘴、线束支架、横梁等,焊缝密集,极易发生变形。
焊缝密集区,托盘前侧翘起变形
c.冷板流道侧壁
液冷板一体化集成设计的电池托盘中,结构刚度较小的部位,如薄板、管道结构等,在焊接过程中不能很好的抵抗热变形,容易发生变形,如:液冷板流道侧壁很薄,一般只有2mm左右,模组安装面焊接横梁、线束支架等零件时,容易造成流道侧壁有裂纹和变形褶皱,影响整体性能。
横梁焊接导致的液冷流道腔壁热裂纹缺陷
3-焊接热变形控制方法
a.分段焊、双面焊
对于强度要求相对较低的部件采取分段焊,将焊接过程分解成多个小段进行,对称布置焊缝,将焊缝对称地布置在构建截面中中和轴附近,以使焊缝产生的变形有可能互相抵消。同时,尽量减少焊缝长度和数量,避免焊缝过度集中或交叉,可以减小焊接温度梯度,从而减少焊接变形。对于底板、底板与侧面框等强度要求高的部位,采取双面焊,增加强度的同时减少因零件较大,焊道较长产生的弯曲变形。
b.优化焊接顺序
控制焊接变形,使用刚性较小的接头形式、避免双向、三向相交的焊缝位置,以及避开高应力区。优化焊接顺序,先焊刚度较弱的区域,最后焊刚度较好的区域,例如先焊角焊缝、再焊短焊缝、后焊长焊缝;先焊横焊缝、后焊纵焊缝。合理的焊接顺序可以有效控制焊接变形,从而控制焊缝外形尺寸。
c.焊接参数调整
控制焊接参数和流程,合理设置焊接速度、焊接层数和每层焊缝的厚度。对较厚的焊缝,采用多层多通道焊接方法,每层焊缝的厚度不大于4mm,多层焊能够减小结构显微组织,提高接头性能。精确控制焊接参数,合理选择焊接电流、电压、焊条型号和焊接速度等参数,可以确保熔池形状和大小一致,从而避免因参数选择不当造成的误差。
d.焊接技能提升
提高焊工操作技术水平(大型构件或要求严格节点采用机械加工),确保焊接过程中动作一致性和规范性,减少人为因素导致的尺寸问题。
我们会定期更新有关热设计与轻量化的技术与资讯,与您分享,供您参考,感谢您对迈泰的关注。
铝合金是工业中应用最广泛的一类有色金属结构材料,尤其在材料导热性能备受关注的场景下,在需要高效热传导的场合,如电子设备散热、电动汽车三电散热、电池储能系统散热以及航空航天领域,通常被用作制造散热器、导热板、电子元件等高效传热设备。
导热率也叫导热系数,是表征材料导热性能的参数指标,它表明单位时间、单位面积、负的温度梯度下的导热量,单位为W/m·K或W/m·℃。铝合金是一种由铝和其他金属组成的合金材料,其导热性能非常优异,导热系数通常在140-200W/(m•K)之间,铝作为地壳中含量最高的金属,因热传导系数较高、密度小、价格低而受到青睐。
1-铝合金材料的导热原理
当材料的相邻区域存在温度差时,热量就会从高温区域经接触部位流向低温区域,产生热传导。金属材料内有着大量的自由电子存在,自由电子可以在金属中快速运动,可以快速实现热量的传递,晶格振动是金属热传递的另一种方式,但相对自由电子传递方式来说处于次要地位。
金属与非金属的热传导方式对比
2-影响铝合金导热性的因素
a.合金化是影响热导率的主要因素之一。合金元素通过固溶原子、析出相和中间相形式存在,这些形式会带来晶体缺陷,如空位、位错和晶格畸变,这些缺陷会增加电子散射的几率,导致自由电子数量减少,从而降低合金的热导性。不同合金元素对Al基体产生晶格畸变程度不同,对热导率的影响也不同。这种差异是由合金元素的化合价、原子体积差异、核外电子排布、凝固反应类型等多因素共同作用的结果。
b.热处理是铝合金加工过程中非常重要的环节,通过改变铝合金微观结构和相变,可以显著影响其热导性。固溶处理是将铝合金加热到一定温度,使其溶质原子充分溶解于基体中,然后快速冷却,以获得均匀的固溶体。这种处理方式可以提高材料的力学性能,但通常会降低其热导率。时效处理是通过在固溶处理后进行适当的冷变形和再加热,可以优化合金的微观组织,提高其综合性能。时效处理兼顾了合金的力学性能和热导率,使合金在保持较高强度的同时,也具有较好的导热性。退火处理通过在较低温度下保温,使合金中的第二相析出并重新分布,从而改善合金的微观组织。退火处理可以提高铝合金的塑性和韧性,但对热导率的影响因具体情况而异。
Al-Cu合金在时效过程中的晶体结构变化示意图
c.其他因素影响,杂质和第二相粒子:铝合金中的杂质和第二相粒子(如氧化物、碳化物等)会散射热载流子(电子和声子),从而降低热导率。杂质含量越高,第二相粒子越粗大,热导率通常越低。铝合金的晶粒尺寸也会影响热导率。一般来说,晶粒尺寸越小,晶界越多,热导率越低。此外,铝合金的加工方式(如轧制、挤压、锻造等)会影响其微观结构和残余应力状态,进而影响热导率。加工硬化和残余应力会降低热导率。
综上,铝合金是高导热材料的理想选择,铝合金中合金元素类型及其存在形式、热处理方式、杂质情况、晶粒大小及成型方式等因素均会影响铝合金材料的热导率,在进行材料成分设计及工艺规划时应该综合考虑。
我们会定期更新有关热设计与轻量化的技术与资讯,与您分享,供您参考,感谢您对迈泰的关注。
电池包气密性是确保电池包质量和安全性的关键,关系到电池包的安全性、可靠性和使用寿命,电池包气密性检测不仅要在生产过程中进行,还在电池维护和检修中进行。
1-电池包气密性要求
实际生产中电池包的气密性需满足以下要求:
密封性能,电池包壳体、接口和连接件等部位需具有良好的密封性能,以防止灰尘、水气等外界杂质进入电池包内部,可以通过焊接、密封胶、防水材料等实现。
防水性能,以防止水分进入电池内部,导致短路、腐蚀等问题。根据国标GB38031-2020《电动汽车用动力电池安全要求》,电池及其组件的密封性能应达到IP67标准,多数新能源汽车用电池及其组件的密封性能要求更高,需满足IP68标准,即电池包在规定的水深和沉水时间内能够防止水进入。
传统的气密性检测方法包括压力法和浸泡法(水检)等。浸泡法则是将液冷板浸泡在水中,观察是否有气泡产生来判断密封性。
水道气密性测试槽
虽然IP68标准更加严格,但在实际应用中,压降法往往作为主要的检测手段,通过设定合适的气密检测标准来满足IP68的要求。压降法是通过测量电池包内部压力变化来判断电池包气密性。在进行气密性检测时,需要关注多个参数,如充气气压、充气时间、稳压时间和泄漏率。
差压基本原理图 直压基本原理图
2-液冷板渗液问题分析
随着动力电池汽车、电化学储能等市场需求的不断升级,更高的能量密度与功率密度电池包得到广泛应用。因为电池热特性,确保电池等核心设备的稳定运行,并提高能源利用效率,液冷技术是储能热管理主流技术路线之一,液冷系统的气密性测试成为了一个关键环节。
液冷板渗液是一个严重的问题:渗液会阻碍冷却液正常流动,影响液冷板散热效果,使得设备性能下降;渗液还可能会造成系统组件老化、损坏,降低系统的可靠性;渗液还可能腐蚀电子元件和线路,增加设备故障和火灾风险。
在液冷板生产制造过程中经过严密气密性测试,为何还会出现渗液问题?
液冷系统气密测试流程
渗液可能由多种因素导致:
l 微小裂缝和缺陷,景观气密性检测可能检测到大的泄露通道,但微小裂缝和缺陷可能仍然存在,这些微小的裂缝在液体压力或高温环境下可能会扩大,导致渗液。
l 冷却液表面张力与浸润性差异:冷却液的表面张力较低时,更容易通过微小缝隙渗透。如果液冷板的表面张力设计不合理或冷却液选择不当,可能会加剧渗液问题。
浸润性差异:不同冷却液对固体表面的浸润性有差异。如果液冷板的材料表面粗糙度高或有微观结构缺陷,冷却液可能更容易渗透。
l 安装或工艺问题:液冷板的安装工艺如果不够精细,或者焊接、连接等过程中存在缺陷,也可能导致密封不严,增加渗液的可能性。
l 环境条件:温度的变化,特别是高压环境,可能会影响冷却液的渗透性。尽管在气密性检测时可能未考虑这些环境因素,但在实际操作中,温度波动可能导致密封失效。
l 材料老化或疲劳:液冷板的材料如果使用时间过长,可能会发生老化或疲劳,导致其密封性能下降,从而增加渗液的风险。
3-液冷板渗液问题预防措施
l 改进液冷板设计:通过优化液冷板的结构和设计,减少微小裂缝和缺陷,提高其密封性能。例如,在流道面焊接模组安装梁时,采取防泄漏措施,避免冷却液泄漏。
l 提高制造工艺水平:在液冷板生产过程中,采用高质量的焊接工艺和材料,确保冷却液不易渗透。同时,在组装过程中,严格按照操作规程进行,避免出现松动或错误安装。
l 优化检测方法组合,保障检测效率的同时提高检测精度,降低漏检率。采用浸泡法、压降法进行气密性检测,操作简单、经济、效率高,适合大批量常规性的检测需求。但两种方法的检测精度较低,压降法检测精度一般为1×10-4Pa·m³/s的泄露速率,检测结果准确性易受温度、湿度、洁净度、压力等因素的干扰。采用检测精度更高、效果更好的检测设备将检测精度提升至1×10-6Pa·m³/s,提升检测效果。
除了液冷板本体的防范措施外,还需在冷却液选型、密封件选择及设备工作环境等多环节中采用合适的应对策略。
我们会定期更新有关热设计与轻量化的技术与资讯,与您分享,供您参考,感谢您对迈泰的关注。
在散热器设计中,采用有效的降本方式能够提高整体系统的可靠性和效率,同时可以减少不必要的成本。
1-降额降本
降额设计是一种有目的地降低元器件或产品在工作时承受电、热和机械应力的设计方法。实际生产和使用的场景中,可以通过降低元器件承受的应力,从而提高电子设备的稳定性。
2D、3D封装方式的散热路径示意
l 降低工作应力:在产品的设计和运行时,可以通过降低工作负载,控制工作频率、限制电流和电压等方法来减少元器件的工作应力。
l 降低环境应力:通过选择适合的元器件类型、布局和封装形式来降低环境应力,如选择温度裕度较大的元器件,或者使用密封性良好的封装形式,以减少温度、湿度和压力对元器件的影响。
l 可靠性工程应用:合理的冗余设计、故障检测和隔离等,进一步降低元器件的失效风险。
通过降低元器件在工作时承受的应力,可以降低其功耗和发热量。当功率器件在低于其额定应力条件下工作时,可以降低其耗电量和产热量,有助于提高系统的能效和可靠性。从长远来看,降额设计有效提高元器件寿命、降低故障率、减少维护工作量,进而降低成本。
2-优化布局
通过合理的布置热元件可以显著提高散热器的工作效率,合理的元器件布局策略可以实现产品性能和成本的平衡。
l 分散发热元件:将发热量大的元件分散开来,减少单位面积上的热量负荷。
l 有利于散热的位置:将发热元件放置在有利于散热的位置,如靠近通风口或者设备的边缘。
l 交错排列:在布局时,将发热元器件与其他一般元器件交错排列,同时尽量使发热元件远离温度敏感元件,以减少其对热敏元件的影响。
l 改善气流:通过改变走向设计和元件布局,优化气流路径,增大流速,提高换热系数。
元器件间间距建议
3-冷却方法的选择
随着电子元器件的性能提升和集成度的增加,功率密度不断增大,导致电子元器件在工作时产生的热量也显著增加。在选择电子元器件的散热方法时,温度控制要求主要包含以下方面:
l 温度范围:不同的元器件对温度容忍的范围不同,如CPU等高性能芯片的工作温度要求在85-100℃之间,而一些低功耗设备可以容忍更高的温度,因此散热系统要确保元器件在安全的温度范围内工作。
l 温度控制精度:在一些温度控制要求严格的场景中,需要采用能够精确控制温度的散热方案,以免过高过低的温度造成元器件性能下降,甚至损坏。
l 环境温度:电子设备的散热效果不仅取决于器件自身的散热能力,还受到周围环境温度的影响,散热设计需要考虑环境温度变化,并尽可能通过散热手段保持设备在适宜的温度范围内。
l 功耗和可靠性:一些低功率电子元器件在发热量较低时,可以采用自然散热,对于高功耗设备则需要更高效的散热技术以确保其在高负荷运行时保持正常的性能并延长使用寿命。
l 密封性和密集性:在密封及高密度组装的器件中,如果发热量不高,可以依赖自然散热。而当元器件密集且发热量大的情形下,需要强制散热或液体冷却等更为有效的散热技术。液体冷却和热管技术在高功耗、大发热量的场景,如行波管、磁控管、功放管等高功率电子元器件,服务器和高功耗设备,以及新能源汽车三电系统,有其独特的应用优势。
充电桩风冷散热模块 充电桩液冷散热模块
在选择电子元器件的散热方式时需要综合考虑发热量和热流密度、环境温度与工作温度、空间约束与热隔离需要及成本与可行性等要素。通过运用适当的散热技术及散热装置保证元器件在适宜的温度下运行,可以有效降低系统更换和维护成本。此外复用历史项目也是降低开发制造成本,提升可靠性的有效策略。
我们会定期更新有关热设计与轻量化的技术与资讯,与您分享,供您参考,感谢您对迈泰的关注。
储能浸没式液冷技术是一种先进的电池冷却方法,利用液体的高效导热特性,实现了对电池的快速、直接和充分冷却,确保了电池在安全和高效的环境中运行。其基本原理是将储能电池完全浸没在一种绝缘、无毒且具有散热能力的液体中。这种技术通过液体直接与电池接触进行热交换,从而快速吸收电池在充放电过程中产生的热量,并将其带到外部循环系统中进行冷却。
单项浸没式液冷储能系统原理示意图
浸没式液冷储能Pack箱作为电池包的承载和保障电芯在合适的环境中工作的关键部件,主要承担电池包及冷却液承载、安全防护、传导换热等功能。因此在箱体结构设计中需要综合考虑密闭性、冷却效率、安全性、材料选择及加工工艺等多个方面,以确保系统的高效、安全和可靠运行。而箱体结构设计是整个液冷系统的基础。
1-均匀受载
浸没式液冷储能Pack下箱体由底板与侧板构成,底板作为基础支撑,而侧板则固定在底板的四周,共同构成箱体的主体框架。箱体的尺寸综合考了液冷系统的整体需求和荷载情况进行调整,在较大尺寸箱体的设计中可以合理设置内部隔板或支撑结构,将大空间划分成多个小空间,通过增加受力面积,提高均匀受载力。而内部结构上可以通过增加支撑肋、加强筋来提高局部的承载能力,还可以在箱体内部设置均载结构以平衡各个角落的负载。
同时,为降低塑性变形对均匀受载性的影响,可以将高低不同的加工面设计为同一平面,这样可以减少机床调整次数,避免高度差导致的变形;还可以通过增加箱体的宽度或高度来分散负载,减少变形。
此外,液冷流道与箱体底板的一体化设计,通过搅拌摩擦焊或激光焊完成拼接,这种设计能有效提高整体结构强度。
单项浸没式液冷储能Pack下箱体结构示意
2-换热设计
导热能力是浸没式液冷储能技术中的重要环节,设计目标是确保电池在高温环境下能够有效散热,从而保持其性能和安全性。
箱体的材料应具有高导热性能,常用的材料有铝合金、铜、铝基复合材料。箱体设计还需要考虑环境温度变化的影响,适当厚度的保温层,能够保证箱体内部温度在一个较恒定的范围内,进而提升系统的整体效率。
箱体的结构设计直接影响其导热能力,合理的流道布置,确保液体在箱体内部顺畅流动,并最大限度地增加接触面积,是提升箱体导热能力的主要策略。箱体内部可以设置多个流道,以增加冷却液循环路径,从而提高散热效果。
方案一 全浸没+单项+板换 方案二 全浸没+单项+箱换
液冷系统包括冷却介质、导热结构、液冷管路和支撑结构。
方案一中,可选择同种或不同种的冷却液分别充入液冷板流道腔与箱体空腔,两个腔体均密封且互不连通。箱体空腔中,冷却液将电池模组浸没,充分接触,冷却不流动,利用液体的导热性好的特点吸收电池表面的热量,降低温升。液冷板中,冷却液在进水集管内分成多个流道并行进入冷板,然后在出水集管内汇合流出,主要负责将热量带出,实现散热。
方案二中,温度低的冷却液从下面或侧面流进,温度高的从上面流出,冷却液在电池包内循环流动,这样能够有效均匀地分配热量,提高整体的冷却效率,保持电芯或电池包温度的一致性。
了进一步提高冷却效果,可以采取多种优化措施,如优化液体流量和循环方式,选择高热容量的冷却液,以及改进液体的温度分布。这些措施能够减少热量的积聚和能量损失,确保电池在高效冷却状态下运行。
3-密封设计
对于液冷pack箱来说,通过采用先进的密封材料和结构进行全密封设计,密封设计不仅要考虑气密性,还需考虑液体介质的密封,确保电池单元在各个方向上均无泄漏。
设计应根据具体应用需求选择合适的密封形式和形状,还要考虑密封件的泄漏自由度、耐磨性、介质和温度兼容性、低摩擦等因素,并根据详细的规格选择合适的密封件类型和材料。
另外,焊接工艺的选择对密封性能影响也很大,对于不同的材料和厚度,选择合适的焊接方法能有效提升焊缝质量,以保证系统的整体强度和密封性。
单项浸没式液冷储能Pack下箱体成品图
我们会定期更新有关热设计与轻量化的技术与资讯,与您分享,供您参考,感谢您对迈泰的关注。
流体仿真
使用模拟软件分析散热器和冷板的散热性能
应用场景
工况: 高热流密度情境
安装布置: 单面安装
典型应用:客户定制
特点:散热效果好
应用场景
工艺: 铝型材拼焊
布置安装: 底部液冷
典型应用:客户定制
特点:重量轻,冷却效果好
冷却液在泵的驱动下通过管路循环。当冷却剂流经服务器内部的热交换器时,它与高温组件(如CPU、GPU等)进行热交换,带走热量。
Lori is a heat sink manufacturer of design and manufacturing high power heat sink, we have provided innovative thermal solutions for many high power industry device such as Aerospace industry,Medical, Communication server, Consumer Electronics etc. Our solutions include high power heat pipe thermal mould, liquid cooling system, staked fin heat sink solution etc.
Lori is a heat sink manufacturer of design and manufacturing high power heat sink, we have provided innovative thermal solutions for many high power industry device such as Aerospace industry,Medical, Communication server, Consumer Electronics etc. Our solutions include high power heat pipe thermal mould, liquid cooling system, staked fin heat sink solution etc.
Lori is a heat sink manufacturer of design and manufacturing high power heat sink, we have provided innovative thermal solutions for many high power industry device such as Aerospace industry,Medical, Communication server, Consumer Electronics etc. Our solutions include high power heat pipe thermal mould, liquid cooling system, staked fin heat sink solution etc.
液体冷却技术的特点:
液冷的方案基本原理:液冷是一种以液体作为冷媒,利用液体流动将数据中心IT设备的内部元器件产生的热量传递到设备外,使IT设备的发 热部件得到冷却,从而保证IT设备安全运行的技术。
液冷的优势:液冷具备超高能效、超高热密度,能够高效散热,并且不受海拔、地域、气温等环境的影响。
迈泰热传冷板式液冷解决方案:
冷板式液冷是通过液冷板(通常为铜铝等导热金属构成的封闭腔体)将发热器件的热量间接传递给封闭在循环管路中 的冷却液体,通过冷却液体将热量带走的一种散热形式。冷板式液冷方案中技术成熟度最高,是解决大功耗设备部署、提升能效、降低制冷运行费用、降低TCO(Total Cost of Ownership)的有效应用方案。
高功耗、高密度是数据中心的未来,液冷将成AI服务器散热主流方案。
DFM优化建议
帮您减少潜在的生产过程中可能的错误和缺陷,确保产品在生产满足设计要求的质量标准
应用场景
工况: 高热流密度情境
安装布置: 单面安装
典型应用:客户定制
特点:散热效果好