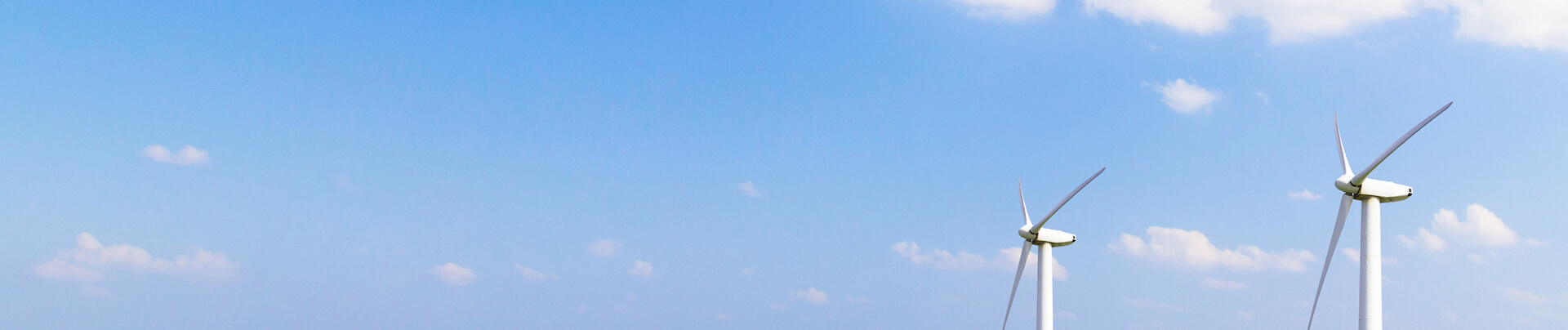
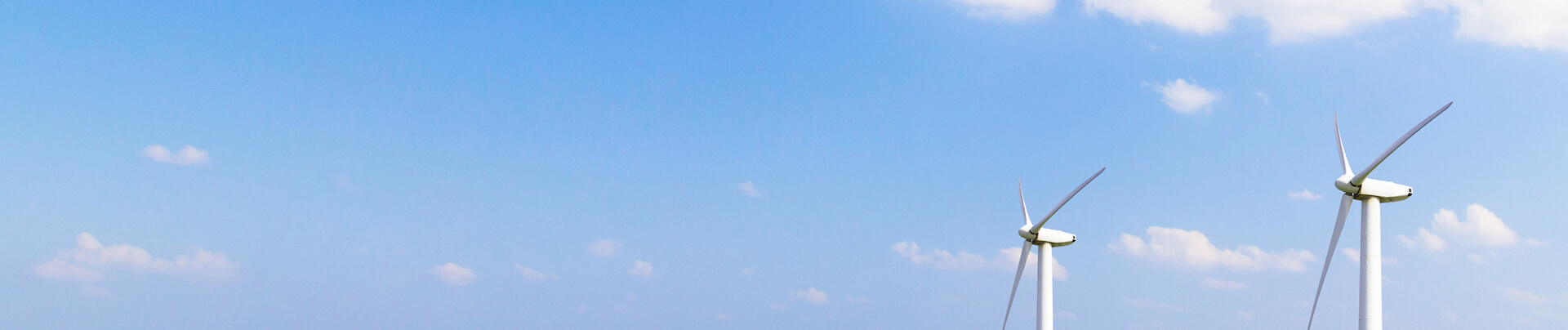
在纯电动汽车中,电池包的重量约占整备质量的30%左右,电池包轻量化,对于提升整车续航里程有着重大意义。因此,对电池包高比能量的研究是新能源汽车目前的主要研究方向之一,也是实现电动汽车轻量化的主要途径,实现动力电池包轻量化可从两个方向开展:提高单体电芯的能量密度,对电池包相关辅件进行优化设计。
多材料轻量化电池包开发旨在通过采用多种轻质材料,降低电池包的重量,提高能量密度和续航里程,同时保证安全性和可靠性。电池Pack各主要部件中,质量最大的是电芯本体,其次为Pack下箱体、上盖、BMS集成部件等。
1-电池包上盖轻量化
电池箱的上盖位于动力电池箱体的上方,不受动力电池箱体侧面的影响,也不会影响整个电池组的质量,其功能主要包括密封、保护等作用。为了提高整车能效,在设计中也会考虑轻量化,采用轻质材料,如铝合金、复合材料(SMC、FRP等),可以显著减轻电池包的重量。
此外,上盖的结构设计还需要考虑制造效率和批量化要求,在结构非常异形的情况下,采用冲压成型或折弯拼焊可能较为困难。上盖的设计还需要考虑到与下箱体、密封结构件等其他部件的连接与配合,确保整个电池箱体的结构稳定性和可靠性。
2-电池包下壳体轻量化
铝合金是电池包壳体制作的理想材料,因其密度低、比强度高、热稳定性好、耐腐蚀性强、导热性好、无磁性、成型容易以及回收价值高等诸多优点。常用的铝合金材料包括6061-T6、6005A-T6和6063-T6等,这些材料具有不同的屈服强度和抗拉强度,可以满足不同的结构需求。
电池包壳体通常由铝合金型材边框和底板构成,采用6系铝合金挤压型材拼焊而成。设计时需要考虑型材断面大小及复杂性、壁厚等因素,以适应不同的结构和功能要求。例如,边框、中间隔板、底板、横梁等部件可能会采用不同的断面设计。
通过合理的结构设计和连接方式,可以有效保证壳体整体强度,降低加工难度,实现壳体减重:
l 薄壁化:通过采用薄壁设计,配合加强筋来满足强度要求,可以有效减轻材料重量。
l 中空化:在结构设计中引入中空部分,以降低材料密度。
l 尺寸优化:优化电池包的尺寸,减少不必要的材料使用。
l 拓扑优化:通过优化电池包内部组件的布局,减少材料占用空间。
l 集成模块化设计:将冷却板、电池包吊耳等部件集成在箱体中,减少单独部件的数量和重量。
3-制造轻量化技术
l 材料成型
目前电池箱材料成型工艺主要有三类:冲压、铝合金压铸和铝合金挤压成型。动力电池箱整体工艺流程包括材料成型及连接工艺,其中材料成型工艺是动力电池箱体的关键工艺。当前上壳体以冲压为主,下壳体主要工艺为挤压成型及铝合金压铸成型两种方式。
l 连接技术
电池箱体连接工艺在新能源汽车制造中至关重要,涉及多种技术和方法,以确保电池箱的结构强度和密封性。
焊接是电池箱体加工中的主要连接工艺,应用广泛。主要包括以下几种方法:
①传统熔焊:如TIG(钨极惰性气体保护焊)和MIG(金属惰性气体保护焊)。TIG焊接速度低,质量高,适用于点固焊和复杂轨迹焊接,常用于边框拼焊和边梁小件焊接。MIG焊接速度高,熔透能力强,适用于边框底板总成内部整圈焊接。
②搅拌摩擦焊:通过摩擦产生热量实现焊接,具有接头质量好、生产效率高等特点。
③冷金属过渡技术:适用于薄板材料,焊接过程无热输入,减少变形。
④激光焊:高精度、高速度,适用于复杂结构焊接。
⑤螺柱焊和凸焊:用于特定部位的快速连接,螺柱焊通过螺柱和螺母实现紧固,凸焊则通过凸点压紧实现连接。
机械连接方式主要解决薄板材料在焊接中的易焊穿和螺纹滑牙问题,包括:
①拉铆螺母:用于箱体边框密封面和内腔底板的连接,具有紧固效率高、使用成本低等优点。适用于薄板与其他部件的螺纹联接。
②钢丝螺套:用于加强铝或其他低强度机体的螺孔,提高螺钉的承载能力和螺纹的受力分布,适用于电池模组安装孔和密封面安装孔。相对于拉铆螺母,钢丝螺套强度更高且易于修复,但一般不适用于薄壁安装。
我们会定期更新有关热设计与轻量化的技术与资讯,与您分享,供您参考,感谢您对迈泰的关注。