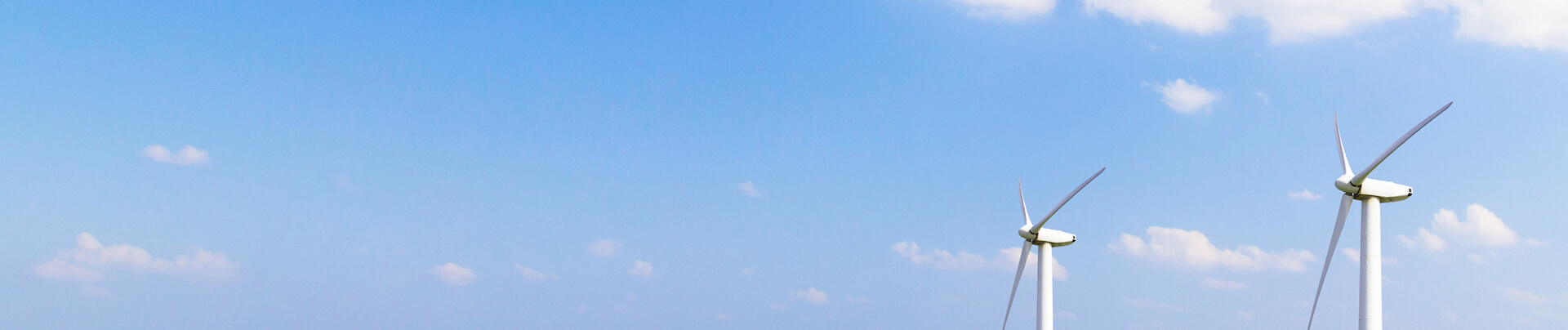
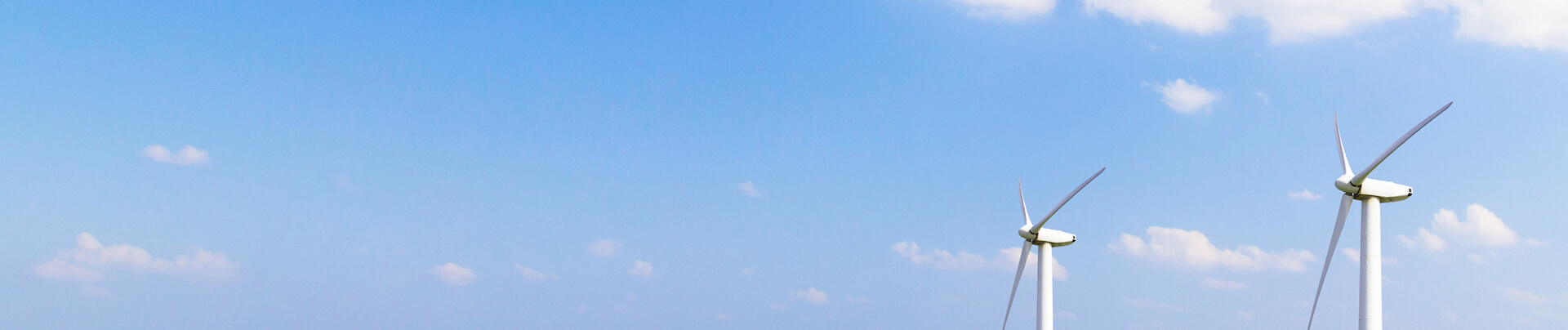
电池包是新能源汽车、储能一体柜及集装箱的关键部件,它是通过壳体包络构成能量源,为电动汽车提供动力,为储能柜与集装箱提供消纳能力。本文结合实际工程需要,通过分析电池包机械强度、安全性、热管理及轻量化等多方面要求,对电池包用型材设计要点进行总结说明。
1-电池包壳体设计要求
a.机械强度,耐振动强度和耐冲击强度,在试验后不能有机械损坏、变形及紧固不见松动的现象,锁止机构不应收到损坏。
b.密封性,电池包的密封性直接影响到电池系统的工作安全,通常要求达到IP67防护等级,以确保电池包密封防水。
c.电池包壳体设计需要考虑热管理性能,通过适当的热管理设计,保证电池在适合的范围内工作。
d.安装固定,壳体应留有铭牌和安全标志布置位置,并为采集线、各种传感元件等安装预留足够空间和固定基础。
e.所有无极基本绝缘的连接件、端子、电触头结合后应满足相应的防护等级需求。
f.轻量化,壳体轻量化对于提升电池包能量密度有着重大意义,铝合金质轻质优是当下最可行的选择,结合实际应用通过适当的极限设计提升轻量化水平。
g.耐久性,电池包壳体的设计寿命不得低于整体产品使用寿命,使用周期内不应发生明显的塑性变形,防护等级、绝缘性能不应降低;结构具备维护方便性,包括铭牌与安全标志布置、连接件防护等。
图1典型铝合金拼焊电池包壳体
2-典型铝合金电池包壳体方案
电池包壳体常用的铝合金材料有6061-T6、6005A-T6和6063-T6等,这些材料具有不同的屈服强度和抗拉强度,可以满足不同的结构需求。这几种材料的强度大小:6061-T6>6005A-T6>6063-T6。
当前电池包壳体成型方案有铝型材焊接、铝合金铸造、铸铝加型材铝、冲压铝板焊接等,铝型材拼焊方案因其灵活性和加工方便性成为主流选择,如图1,壳体主要有铝合金型材边框、铝合金型材底板构成,采用6系铝合金挤压型材拼焊而成。铝合金铸造方案因其简化工艺和降本潜力被视为未来发展方向。
3-型材断面设计
a.断面大小及复杂性:型材断面大小用外接圆来衡量,外接圆越大,所需要的挤压力就越大;型材断面通常由多个空腔组成,以提高结构刚度和强度,通常边框、中间隔板、底板、横梁等采用不同的断面设计以适应不同的结构和功能要求。
图2典型铝合金型材断面
b.铝型材壁厚:某一特定铝型材的壁厚最小值与型材外接圆半径、形状及合金成分有关,如,6063铝合金壁厚取为1mm时,6061铝合金就要取为1.5mm左右,同等断面挤压难度:6061-T6>6005A-T6>6063-T6。电池包用型材设计中,边框型材通常选用6061-T6铝合金材料,其典型断面由多个空腔组成,壁厚最薄处约为2mm左右;底板型材也由多个空腔组成,材质一般为6061-T6、6065A-T6,起壁厚最薄处也为2mm左右;另外,在底板承重的托盘及底板液冷集成的设计方案中,一般底板均采用双面结构,底板厚度一般为10mm,壁厚及腔体内壁约为2mm。
c.型材断面尺寸公差:断面尺寸公差应根据铝型材的加工余量、使用条件、型材挤压难易程度、形状的部位来确定,对一些挤压难度大的铝型材可以改变形状或增大工艺余量、尺寸公差,来减小挤压难度,挤压出近似要求的铝型材制品,然后通过或整形或者加工满足使用要求。
此外,进行型材断面设计时需要考虑不同焊接工艺对接头、坡口、壁厚等具体要求。
我们会定期更新有关热设计与轻量化的技术与资讯,与您分享,供您参考,感谢您对迈泰的关注。