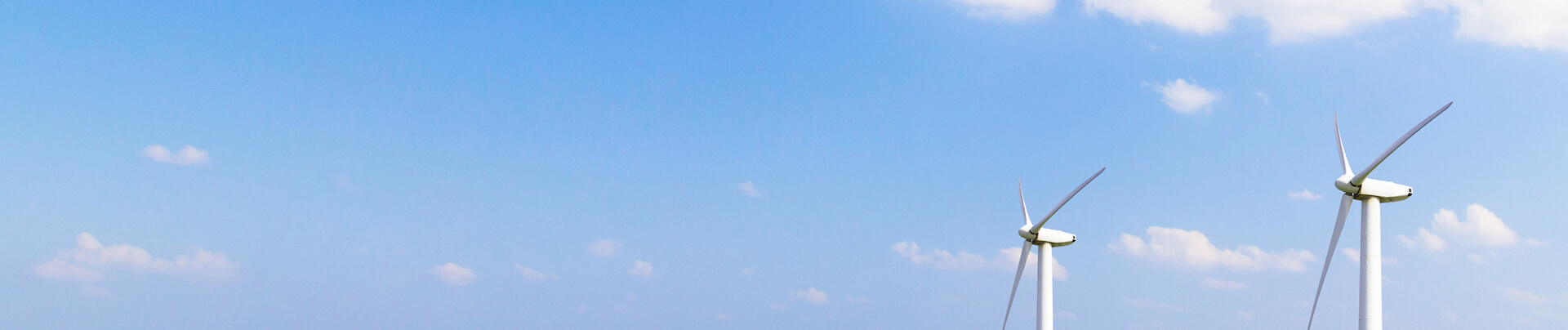
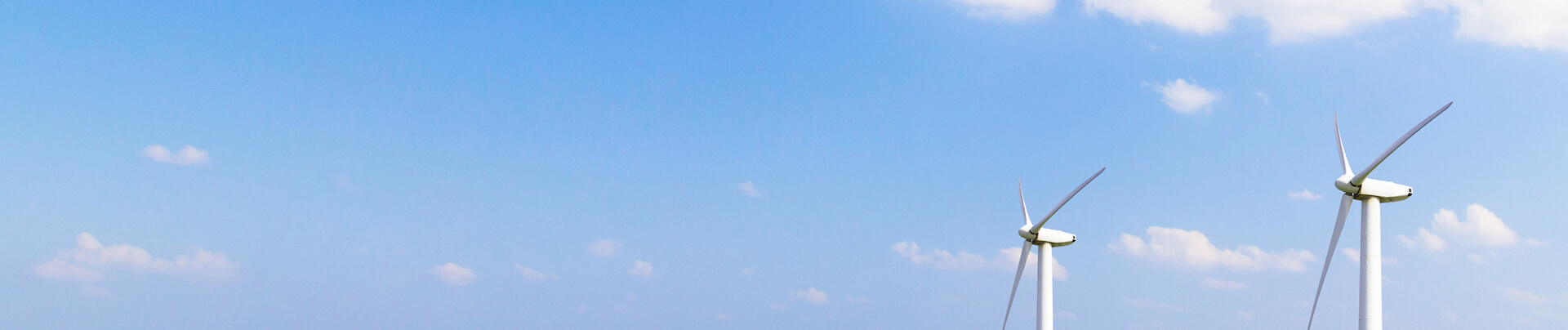
随着新能源汽车与储能产业的快速发展,轻量化、高安全性及高效热管理成为核心诉求。我司深耕铝合金材料加工领域,依托先进的材料选型、成型工艺与焊接技术,专注于电池托盘、液冷板、储能Pack箱及散热器的研发与制造。铝合金因其密度低(约2.7g/cm³)、强度高、耐腐蚀及优异导热性(热导率约150-220 W/m·K),成为新能源装备轻量化与热管理的理想选择。
1-铝合金材料选型及关键考量
不同产品对铝合金的性能需求差异显著,需结合强度、耐蚀性、焊接性及工艺适配性综合选材:
a.电池托盘
常用牌号:6061-T6、6005A-T6、6063-T6。
选型依据:
·需满足抗拉强度≥240 MPa(如6061-T6)以通过国标挤压、跌落及球击测试;
·焊接性要求高,需避免热裂纹(优先选用Mg/Si强化的6xxx系);
·耐腐蚀性通过阳极氧化或包铝工艺提升。
图1-铝合金电池托盘
b.储能Pack箱
常用牌号:5083、6061-T6(兼顾强度与耐蚀性)。
选型依据:
·需承受振动与冲击载荷,屈服强度需≥200 MPa;
·表面处理要求高,避免电化学腐蚀。
c.液冷板
常用牌号:3003、6061/6063、6082。
选型依据:
·高导热性与耐腐蚀性;
·液冷流道需复杂成型,优先挤压性能优的6xxx系。
2-工艺性能差异与加工难点
铝合金的加工需适配其物理特性,尤其在切割、CNC、焊接及表面处理环节:
a.切割与CNC加工
难点:
·高精度孔加工易因材料延展性产生毛刺或变形(如台阶孔边缘突起);
·薄壁结构(如液冷板流道)需控制切削力以防翘曲。
解决方案:
·采用金刚石涂层刀具提升刃口锋利度,减少挤压变形;
·优化加工参数(如高转速、低进给)配合通用CNC设备实现稳定加工。
b.焊接工艺
核心挑战:
·氧化膜(Al₂O₃熔点2050℃)阻碍熔合,易导致气孔与夹渣;
·部分合金热裂纹倾向高,需控制线能量与焊丝成分。
优选工艺:
·TIG焊(交流电源):适用于薄板,通过“阴极清理”破除氧化膜;
·MIG焊(大电流+氦混合气体):厚板焊接效率高,热输入可控。
图2-电池托盘焊接
c.表面处理
·绝缘耐压涂层:应用于电池托盘与Pack箱内部,需通过耐压测试(≥3000V DC/1min),涂层厚度20-50μm,确保高压环境下的绝缘安全性;
·保温除湿涂层:针对储能Pack箱,采用疏水材料(如氟碳树脂)降低内部结露风险,达因值≥34以保证附着力;
·防撞保护涂层:用于电池托盘外壁,选用聚氨酯弹性体(硬度≥80 Shore A),抗冲击性能提升30%以上;
·阳极氧化:常规防腐处理,膜厚误差≤3μm,适配复杂结构。
3-审验性检查与设备适配性
为满足新能源行业标准(如GB/T31467.3、UL2580),需进行多维度验证与工艺适配:
a.审验性检查
·结构强度:通过有限元仿真验证托盘承载、挤压及球击性能(最大应力≤材料屈服强度);
·密封性测试:液冷系统采用氦检漏(泄漏率≤1×10⁻⁶ mbar·L/s)与循环压力测试(0.5-1.5MPa/5000次);
·涂层性能验证:
绝缘涂层耐压测试(5000V DC/60s无击穿);
防撞涂层通过落球冲击(1kg钢球1m高度)与盐雾测试(1000h无剥落)。
b.设备适配性优化
· 通用CNC设备改造:通过高精度夹具设计与动态补偿算法,实现薄壁件加工变形量≤0.1mm;
·焊接参数库:针对不同铝合金牌号建立标准焊接参数(如电流、送丝速度),降低调试周期;
·涂层自动化喷涂:采用多轴机器人喷涂,结合红外固化技术,涂层均匀性误差≤5%。
结语
铝合金在新能源装备中的广泛应用,既是材料科学的胜利,亦是工艺创新的体现。我司将持续探索高强、耐蚀、易加工的新型铝合金,并通过工艺革新推动电池托盘、液冷板等产品的性能升级,助力行业迈向高效、轻量化的未来。
我们会定期更新有关热设计与轻量化的技术与资讯,与您分享,供您参考,感谢您对迈泰的关注。