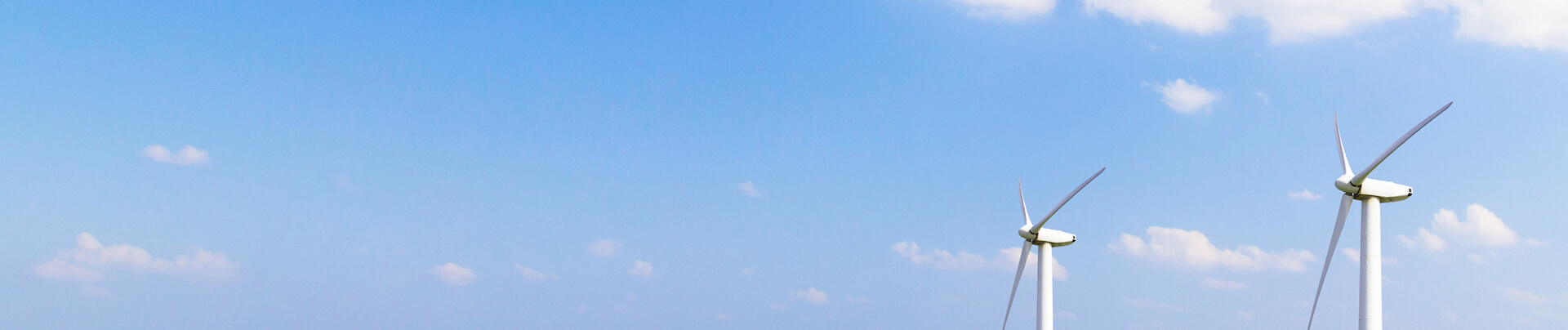
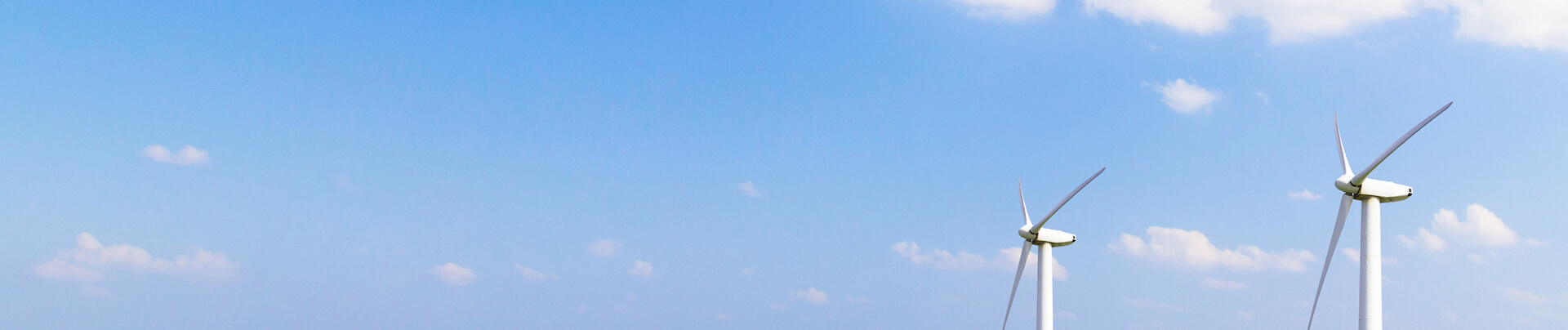
铝合金等轻质材料因其优异的性能成为主流选择,但薄板焊接中的热输入控制、变形抑制及工艺稳定性等难题对传统焊接技术提出了巨大挑战。冷金属过渡焊(CMT)凭借低热输入、无飞溅过渡及智能化参数控制等优势,为电池托盘制造提供了革新性解决方案。
本文深入探讨CMT技术在电池托盘薄板焊接中的精准控制策略,分析其适配性、工艺难点及复合应用场景,以期为高效、高质生产提供理论支持与实践参考。
图1 104S储能电池液冷下箱体CMT焊接
1-电池托盘焊接的工艺要求与CMT适配性
CMT技术通过低热输入、无飞溅过渡和智能化参数控制,完美适配电池托盘焊接的高精度、低变形与高效率需求。
(1)电池托盘焊接的核心工艺要求
a.材料适配性与轻量化需求
电池托盘多采用轻质铝合金(如6xxx系列、6061等),部分高端车型探索碳纤维复合材料,需满足高强度(抗拉强度达母材60%-70%)与低密度(铝合金密度2.7g/cm³)要求。
异种材料连接需求:例如钢铝混合结构,需克服热膨胀系数差异导致的变形。
b.焊接质量与性能指标
低热输入与变形控制:薄板(0.3-3mm)焊接需确保变形量≤2mm,尤其长直线焊缝需分段焊或反变形设计。
密封性与强度:焊缝需完全密封以防止电解液泄漏,并通过剪切试验(如T/CWAN 0027-2022标准要求)。
气孔率控制:铝合金焊接易产生气孔,需将气孔率控制在0.5%以下。
c.生产效率与自动化要求
批量生产需实现焊接速度≥7mm/s,单托盘焊接时间缩短至5-10分钟。
自动化工作站需兼容双工位设计(装配与焊接同步)和多机器人协同作业。
(2)CMT技术适配电池托盘焊接的关键优势
a.低热输入的精准控制
CMT通过熔滴短路时焊丝回抽切断电流,热输入量比传统MIG焊减少33%,尤其适用于0.3mm超薄板焊接(无烧穿风险)。
冷热交替循环(电弧加热-熔滴过渡-焊丝回抽)减少热积累,焊接变形量可控制在1.5mm以内(比亚迪、北汽案例)。
b.工艺稳定性与质量提升
无飞溅焊接:CMT的机械回抽机制消除熔滴爆断飞溅,减少返工率。
气孔控制优化:采用Ar+30%He混合保护气体,气孔数量比纯Ar减少50%,气孔尺寸缩小至≤0.3mm。
间隙容忍度高:可适应1.5mm装配间隙,降低夹具精度要求。
c.自动化集成与效率提升
双工位工作站(如泰翔科技设计)实现焊接与装配并行,效率提升2倍。
机器人对称焊接(两台机器人同步作业)配合反变形设计,缩短节拍至10分钟内。
2-电池托盘CMT工艺难点分析
图2 CMT焊接工艺过程
(1)材料特性与焊接缺陷控制
a.铝合金焊接的气孔敏感性
铝合金电池托盘(如6061、6063等)在CMT焊接中易因熔池快速凝固、氢溶解度变化等因素形成气孔。保护气体成分对气孔抑制至关重要:纯Ar保护时,气孔率较高(约5%);采用Ar+30%He混合气体可加速气体逸出,气孔率降至0.5%以下。电感修正参数(如负向调节)可优化熔池流动,减少气孔尺寸。
b.热裂纹倾向与成分偏析
铝合金中Mg、Si等元素的偏析易导致焊缝晶界脆化。CMT工艺的低热输入虽能减少热影响区,但需精确控制焊接速度与送丝量,避免熔深不足或局部过热引发裂纹。
c.异种材料焊接的冶金兼容性
若托盘涉及铝-钢或铝-复合材料连接(如防撞梁与箱体),需克服界面脆性相(如FeAl₃)和Zn蒸气干扰。
(2)工艺参数优化挑战
a.熔深与热输入的平衡
电池托盘需满足T/CWAN 0027标准对焊缝熔深(≥0.8mm)的要求。CMT工艺的低热输入特性可能导致熔深不足,需通过调整弧长,利用脉冲电流提升熔池穿透力。
b.焊接速度与稳定性的权衡
自动化产线要求焊接速度≥1.2m/min,但高速下易出现电弧不稳定或熔滴过渡不均。
c.复杂焊缝的搭桥能力
托盘结构常含大间隙(0.5-1.5mm)或异形焊缝(如T型接头)。
(3)结构设计与制造工艺适配性
a.薄板焊接变形控制
铝合金托盘壁厚通常为2-3mm,传统MAG焊变形量可达1.2mm,而CMT焊接通过低热输入可将变形量降至0.3mm以下。但需配合反变形工装设计和机器人对称焊接(双工位工作站)以进一步提升精度。
b.长焊缝的连续性与密封性
电池托盘密封焊缝长度可达数米,需避免断弧或熔池波动。CMT技术通过每秒70次以上的电弧重燃周期,确保焊缝均匀性,配合激光跟踪系统可将气密合格率提升至99%。
c.多工艺复合应用的协同性
高端托盘常采用CMT+FSW(搅拌摩擦焊)复合工艺:CMT用于复杂结构(如边框与底板连接)。FSW用于高载荷区域(如纵梁)以提升强度。需解决两种工艺的衔接参数(如预热温度、焊后热处理)匹配问题。
3-CMT工艺在电池托盘制造中的典型应用场景
(1)电池托盘主体结构的连接
a.边框与底板焊接
CMT工艺广泛应用于铝合金电池托盘的边框与底板连接,尤其适用于 长焊缝、薄板(2-3mm厚度) 场景。
b.横梁与底板连接
在CTP电池托盘设计中,由于横梁数量减少且结构复杂,CMT工艺被用于:高精度定位焊接:横梁与底板的局部连接(如T型接头)需避免熔深不足,CMT通过电弧长度数字化控制(如福尼斯CMT Advanced技术)实现稳定熔深≥0.8mm。多材料适配:若横梁采用铝镁合金(如6061)而底板为高强度铝材,CMT可通过Ar+He混合气体保护减少气孔,同时适应不同材料的导热差异。
(2)薄板与复杂几何结构的焊接
a.薄壁铝合金焊接(2-3mm)
电池托盘的轻量化需求推动薄板应用,但传统MIG焊易导致变形。CMT工艺的优势在于:
b.超薄板焊接:泰翔自动化通过CMT技术实现0.3mm超薄板的无飞溅焊接,用于电池托盘边缘密封结构。
c.异形焊缝搭桥:针对托盘内部加强筋、防撞梁等异形结构,CMT Gap Bridging模式通过焊丝回抽与电弧重定向,可填补0.5-1.5mm间隙,避免未熔合缺陷。
d.密封性要求高的焊缝:电池托盘的密封性直接关系电池安全,CMT工艺通过以下方式保障:
· 连续长焊缝:采用每秒70次以上的电弧重燃周期(如伏能士LaserHybrid技术),确保数米长焊缝的连续性,气密合格率达99%。
· 低热输入控制:相比激光焊,CMT热输入更低,减少熔池波动对密封胶层的热影响,适配涂胶工艺。
(3)多工艺复合制造场景
a.CMT+FSW复合工艺
在高端电池托盘生产线中,CMT常与搅拌摩擦焊(FSW)协同:
分工协作:CMT用于复杂结构(如边框、异形接头)的灵活焊接,FSW用于高载荷区域(如纵梁)以提升强度。例如上海伟晟的自动化生产线通过CMT+FSW+CNC组合,将托盘生产效率提升30%。
工艺衔接优化:华数锦明的生产线采用模块化设计,通过预热参数匹配(如CMT焊后局部加热至150℃)实现与FSW的无缝衔接。
b.与FDS/SPR铆接技术结合
第二代CTP技术中,CMT与摩擦自拧紧(FDS)、自冲铆接(SPR)技术协同:混合连接方案:例如框架与底板的承重区域采用FSW,而可拆卸部件(如水冷板、隔热层)通过CMT焊接预定位,再以FDS铆接固定,兼顾强度与维护便利性。
我们会定期更新有关热设计与轻量化的技术与资讯,与您分享,供您参考,感谢您对迈泰的关注。