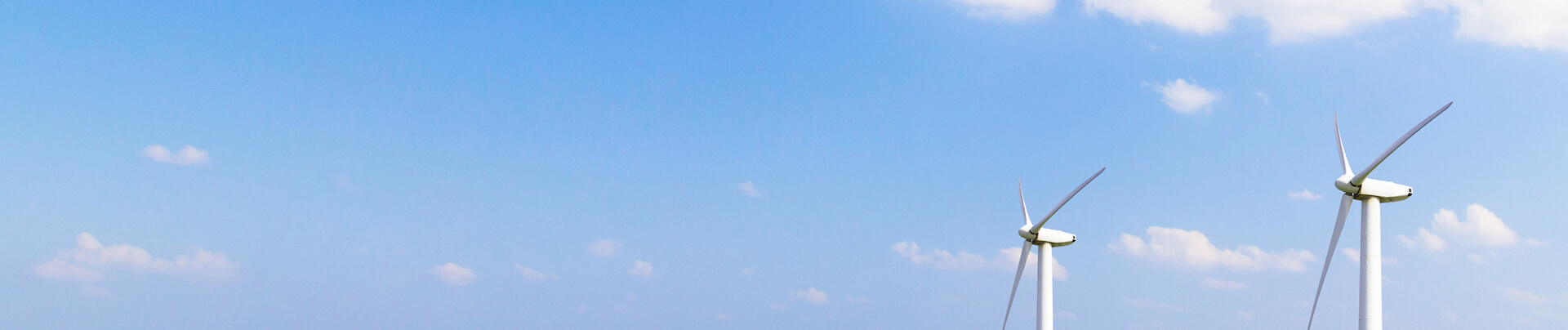
L'échange et le partage favorisent la croissance et
travaillent ensemble pour un développement commun!
La technologie CTP (Cell to Pack) bouleversant la structure traditionnelle des batteries, le rôle du support de batterie est passé d'une simple fonction de support passif à une fonction d'intégration active. La technologie de soudage est devenue essentielle à la sécurité et à la performance. Les exigences de légèreté (épaisseur de paroi de seulement 1,5 mm), d'étanchéité zéro pore et d'intégration multi-matériaux (aluminium, cuivre, fibre de carbone) ont plongé le soudage traditionnel dans le dilemme des déformations et des défauts. L'industrie réalise des avancées majeures grâce à l'innovation des matériaux, au contrôle qualité intelligent et à l'itération des procédés. Cet article analyse les défis disruptifs posés par la technologie CTP au soudage et explore la voie technique vers une haute précision et une fiabilité optimales.
1- Analyse des changements dans les exigences de conception structurelle des bacs de batterie grâce à la technologie CTP
La technologie CTP (Cell to Pack) intègre directement les cellules de batterie au bloc-batterie en supprimant la structure modulaire des blocs-batteries traditionnels. Cette innovation technologique impose des exigences d'amélioration globales et multidimensionnelles pour la conception structurelle du bac de batterie. Voici une analyse spécifique des matériaux, des performances, du procédé, de l'intégration, etc. :
(1) Amélioration globale de la résistance structurelle et de la résistance aux chocs
a. Exigences en matière de support mécanique après suppression du module :
Après suppression de la structure modulaire par la technologie CTP, le bac de batterie doit assurer directement les fonctions de support, de fixation et d'amortissement des forces externes de la cellule de batterie. Le module traditionnel disperse la charge mécanique, tandis que le bac CTP doit absorber la déformation de la cellule de batterie lors de la charge et de la décharge (par exemple, la force de dilatation d'une cellule de batterie carrée peut atteindre 10 à 20 kN), tout en résistant aux vibrations, à l'extrusion et aux chocs pendant la conduite du véhicule.
b. Orientation vers l'optimisation des matériaux et des structures
· Dominance de l'alliage d'aluminium à haute résistance : L'acier a été progressivement remplacé en raison de son poids élevé, et le 6061-T6 s'est imposé. Il présente une résistance spécifique élevée et une forte résistance à la corrosion, ce qui permet de répondre à la double exigence de légèreté et de rigidité élevée.
· Conception de structures composites : Par exemple, la structure « double cadre à poutre annulaire » du Leapmotor améliore la résistance aux chocs locaux grâce à des compartiments de poutre longitudinaux et transversaux, tout en utilisant la technologie d'extrusion pour optimiser la répartition des matériaux et réduire le poids superflu.
· Exploration de l'alliage magnésium-aluminium et de la fibre de carbone : L'alliage magnésium-aluminium est 30 % plus léger que les matériaux en aluminium traditionnels, et les matériaux composites en fibre de carbone présentent à la fois des caractéristiques de résistance et de légèreté élevées, mais ne sont actuellement utilisés que dans les modèles haut de gamme en raison de leur coût et de la maturité de leur procédé.
(2) Exigences relatives à l'étanchéité à l'air et à la gestion thermique intégrées
a. Amélioration des performances d'étanchéité
Une fois le module retiré, la circulation interne du liquide de refroidissement et l'étanchéité au gaz du bloc-batterie dépendent entièrement du plateau, et les défauts de soudure (tels que les pores et les fissures) peuvent entraîner des risques de fuite.
Figure 1 - Test d'étanchéité du bac à piles
b. Intégration des fonctions de gestion thermique
Les plateaux CTP doivent intégrer des composants tels que des plaques de refroidissement liquide et des adhésifs thermoconducteurs. Par exemple, des adhésifs structuraux sont utilisés pour fixer les cellules de batterie et transférer les contraintes de dilatation, tandis que des adhésifs thermoconducteurs polyuréthane (conductivité thermique > 1,5 W/m·K) assurent la conduction thermique entre les cellules de batterie et avec les tubes de refroidissement liquide. La quantité d'adhésif utilisée dans un seul PACK est supérieure de plus de 50 % à celle des structures traditionnelles. Des canaux d'écoulement doivent être conçus à l'intérieur du plateau pour optimiser l'efficacité du refroidissement tout en évitant les dommages à l'étanchéité causés par la zone affectée thermiquement par le soudage.
(3) Allègement et innovation des matériaux
a. Tendances en matière de choix des matériaux
Procédés d'extrusion et de moulage sous pression d'alliages d'aluminium : des profilés en aluminium extrudé sont utilisés pour les structures de cadre (comme le plateau de batterie 4680 de Tesla), et les procédés de moulage sous pression (comme le moulage sous pression intégré) simplifient le soudage et réduisent le poids de 15 à 20 %.
Application des matériaux composites plastiques : Par exemple, les matériaux PA6 renforcés de fibres de verre sont utilisés dans les pièces non porteuses afin de réduire davantage le poids, mais le problème de compatibilité avec l’interface de connexion métallique doit être résolu.
b. Stratégie de conception légère
Optimisation de la topologie : Réduire les matériaux redondants grâce à la simulation IAO et alléger le plateau tout en garantissant sa résistance.
Parois fines et intégrées : L’épaisseur de la paroi du plateau est réduite de 3 mm à 1,5-2 mm, et des composants fonctionnels tels que les supports BMS et les canaux de faisceau de câbles sont intégrés pour réduire le nombre de pièces.
(4) Intégration et conception modulaire
a. Forte intégration des composants fonctionnels
Les plateaux CTP doivent intégrer des modules tels que le système de gestion de batterie (BMS), les connecteurs haute tension et les couches d’isolation ignifuges.
b. Conception modulaire et compatible
La ligne de production de soudage doit prendre en charge la production mixte de plusieurs modèles de plateaux, permettre un changement de type en un clic et être compatible avec des structures de plateaux de différentes tailles de cellules de batterie (par exemple, carrées et cylindriques).
2 - Défis spécifiques de l'innovation technologique CTP pour le procédé de soudage
La technologie CTP (Cell to Pack) a considérablement amélioré l'utilisation de l'espace et la densité énergétique, mais elle a également posé des défis sans précédent au procédé de soudage.
(1) La difficulté de contrôler les défauts de soudage a fortement augmenté.
a. Problèmes de porosité et d'étanchéité
Une fois le module éliminé par la technologie CTP, le support de batterie doit directement assurer l'étanchéité. Les pores de soudage (un défaut fréquent dans le soudage des alliages d'aluminium) entraînent directement un risque de fuite de liquide de refroidissement ou de pénétration de gaz.
b. Fissures et compatibilité des matériaux
Les alliages d'aluminium à haute teneur en zinc (tels que la série 7) sont sujets aux fissures dues aux contraintes thermiques lors du soudage.
c. Erreur d'assemblage et d'espacement
L'intégration directe de plusieurs cellules entraîne une augmentation du nombre de points de jonction de la structure du support. L'accumulation d'erreurs d'assemblage peut entraîner un espacement de soudure supérieur à ± 1 mm.
(2) Problèmes d'adaptation du procédé liés à la mise à niveau du système de matériaux
a. Défis du soudage des matériaux légers
Le matériau des plateaux CTP est passé de l'acier à l'alliage d'aluminium (6061-T6, 7075-T6), à l'alliage magnésium-aluminium (réduction de poids de 30 %) et aux composites en fibre de carbone. Le soudage des alliages d'aluminium doit résoudre le problème de pénétration insuffisante dû à la fusion difficile du film d'oxyde et à une conductivité thermique élevée.
b. Technologie d'assemblage de matériaux différents
Lorsque le plateau intègre des composants fonctionnels tels qu'une plaque de refroidissement liquide (cuivre/aluminium) et une couche ignifuge (matériau composite à matrice céramique), des composés intermétalliques fragiles sont susceptibles d'apparaître à l'interface de matériaux différents.
(3) Complexité structurelle accrue et exigences de précision accrues
a. Contrôle de la déformation des structures minces de grande taille
L'épaisseur de paroi du plateau CTP est réduite de 3 mm à 1,5-2 mm, et la sensibilité à la déformation thermique du soudage augmente considérablement.
b. Joints de soudure haute densité et efficacité du processus
Le nombre de joints de soudure sur un seul plateau est passé de 2 000 dans les modules traditionnels à plus de 5 000.
Figure 2 - Soudage du bac à batterie
3- Modernisation des processus de production et du contrôle qualité
La technologie CTP favorise la transformation du soudage des bacs de batteries, passant d'un « processus unique » à une « collaboration multi-technologies, intelligence et éco-responsabilité ». Les fabricants doivent se concentrer sur trois axes majeurs :
Mise à niveau technologique : amélioration du contrôle des défauts tels que les pores et les fissures, et adaptation aux matériaux légers ;
Transition intelligente : numérisation complète des processus et contrôle qualité par IA pour une production de haute précision ;
Collaboration écologique : élaboration conjointe de normes techniques avec les fournisseurs de matériaux, les équipementiers et les équipementiers.
Nous mettrons régulièrement à jour les informations et technologies relatives à la conception thermique et à l’allègement. Merci de votre intérêt pour Walmate.