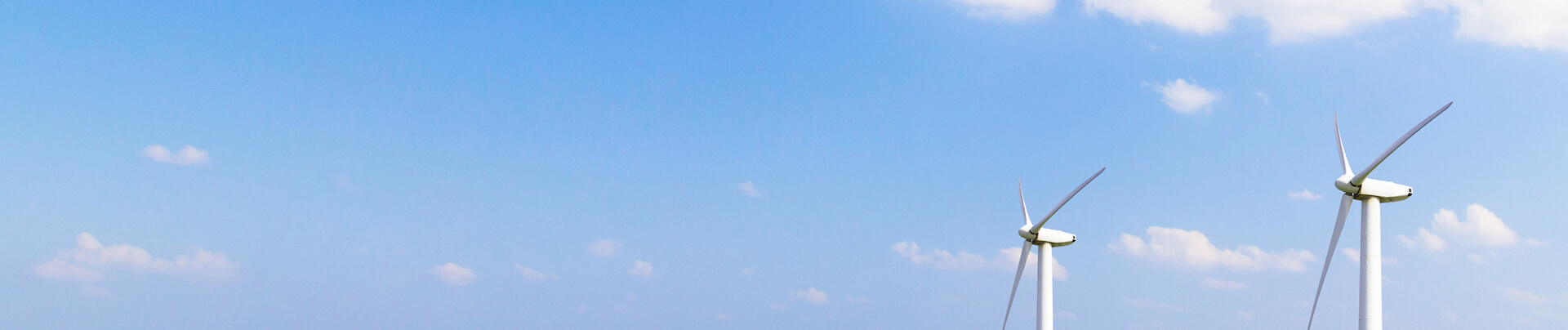
L'échange et le partage favorisent la croissance et
travaillent ensemble pour un développement commun!
Les matériaux légers comme les alliages d'aluminium sont devenus courants grâce à leurs performances supérieures. Cependant, des défis tels que le contrôle de l'apport de chaleur, la suppression des déformations et la stabilité du procédé de soudage des plaques minces constituent des obstacles majeurs pour les technologies de soudage traditionnelles. Le soudage par transfert de métal à froid (CMT), avec ses avantages : faible apport de chaleur, transfert sans projections et contrôle intelligent des paramètres, offre une solution innovante pour la fabrication de bacs de batteries.
Cet article examine les stratégies de contrôle de précision de la technologie CMT pour le soudage des plaques minces destinées aux bacs de batteries, en analysant son adaptabilité, les défis du procédé et les scénarios d'application des composites, afin de fournir des orientations théoriques et pratiques pour une production efficace et de haute qualité.
Figure 1 : Soudage CMT du boîtier inférieur de refroidissement liquide de la batterie de stockage d'énergie 104S
1- Exigences relatives au soudage des bacs de batterie et adaptabilité du CMT
La technologie CMT, avec son faible apport de chaleur, son transfert sans projections et son contrôle intelligent des paramètres, répond parfaitement aux exigences de haute précision, de faible déformation et d'efficacité du soudage des bacs de batterie.
(1)Exigences fondamentales du procédé de soudage des bacs de batterie
a. Compatibilité des matériaux et exigences d'allègement
Les bacs de batterie utilisent principalement des alliages d'aluminium légers (par exemple, série 6xxx, 6061) ou des composites en fibre de carbone pour les modèles haut de gamme, exigeant une résistance élevée (résistance à la traction du matériau de base de 60 à 70 %) et une faible densité (alliage d'aluminium : 2,7 g/cm³).
Assemblage de matériaux différents : Pour les structures hybrides acier-aluminium, les différences de coefficient de dilatation thermique doivent être prises en compte afin de minimiser la déformation.
b. Qualité et performances des soudures
Faible apport de chaleur et contrôle de la déformation : Pour les plaques minces (0,3 à 3 mm), la déformation doit être ≤ 2 mm. Les soudures linéaires longues nécessitent un soudage segmenté ou une conception anti-déformation.
Étanchéité et résistance : Les soudures doivent être parfaitement étanches pour éviter les fuites d’électrolyte et réussir les tests de cisaillement (par exemple, normes T/CWAN 0027-2022).
Contrôle de la porosité : Le soudage des alliages d’aluminium est sujet à la porosité, nécessitant un taux de porosité ≤ 0,5 %.
c. Exigences en matière d’efficacité de production et d’automatisation
La production par lots exige une vitesse de soudage ≥ 7 mm/s, réduisant le temps de soudage d’un seul plateau à 5 à 10 minutes.
Les postes de travail automatisés doivent prendre en charge la conception à deux postes (assemblage et soudage simultanés) et la collaboration multi-robots.
(2) Principaux avantages du CMT pour le soudage des bacs à batteries
a. Contrôle précis de l'apport de chaleur
Le CMT réduit l'apport de chaleur de 33 % par rapport au soudage MIG traditionnel en rétractant le fil de soudage pour couper le courant lors du court-circuit des gouttelettes, éliminant ainsi les risques de brûlure pour les plaques ultra-fines (0,3 mm).
L'alternance des cycles froid-chaud (chauffage de l'arc, transfert des gouttelettes, rétraction du fil) minimise l'accumulation de chaleur et contrôle la déformation à ≤ 1,5 mm (études de cas BYD et BAIC).
b. Stabilité du procédé et amélioration de la qualité
Soudage sans projections : La rétraction mécanique élimine les projections de gouttelettes, réduisant ainsi les reprises.
Optimisation de la porosité : L'utilisation d'un gaz de protection Ar+30 % He réduit la porosité de 50 % par rapport à l'Ar pur, avec des pores ≤ 0,3 mm.
Tolérance élevée aux jeux : Prise en charge des jeux d'assemblage jusqu'à 1,5 mm, réduisant ainsi les exigences de précision des fixations.
c. Intégration de l'automatisation et gains d'efficacité
Les postes de travail à deux postes (par exemple, ceux conçus par Taixiang Tech) permettent le soudage et l'assemblage en parallèle, doublant ainsi l'efficacité.
Le soudage robotisé symétrique (synchronisation à deux robots) avec conception anti-déformation réduit le temps de cycle à ≤ 10 minutes.
2-Défis du processus CMT pour les bacs à batteries
Figure 2 : Déroulement du processus de soudage CMT
(1) Propriétés des matériaux et contrôle des défauts de soudure
a. Sensibilité à la porosité dans le soudage des alliages d'aluminium
Les plateaux en alliage d'aluminium (par exemple, 6061, 6063) sont sujets à la porosité en raison de leur solidification rapide et des variations de solubilité de l'hydrogène. La composition du gaz de protection est essentielle : l'argon pur entraîne une porosité d'environ 5 %, tandis que l'argon + 30 % d'hélium réduit la porosité à ≤ 0,5 %. Le réglage de l'inductance (par exemple, réglage négatif) optimise l'écoulement du bain de fusion et minimise la taille des pores.
b. Fissuration à chaud et ségrégation de composition
La ségrégation de Mg, Si, etc., dans les alliages d'aluminium peut entraîner une fragilisation des joints de grains. Bien que le faible apport de chaleur du CMT réduise la zone de fusion, un contrôle précis de la vitesse de soudage et du dévidage du fil est nécessaire pour éviter une pénétration insuffisante ou une surchauffe localisée.
c. Compatibilité métallurgique dans le soudage de matériaux différents
Les interfaces des joints Al-acier ou Al-composite (par exemple, poutres et enceintes de protection) doivent atténuer les phases fragiles (par exemple, FeAl₃) et les interférences de vapeur de Zn.
(2) Défis liés à l'optimisation des paramètres du procédé
a. Équilibrage de la pénétration et de l'apport thermique
Les soudures doivent respecter la norme T/CWAN 0027 relative à la profondeur de pénétration (≥ 0,8 mm). Le faible apport thermique du CMT peut entraîner une pénétration insuffisante, nécessitant un ajustement de la longueur de l'arc ou un courant pulsé pour améliorer la pénétration.
b. Compromis entre vitesse et stabilité
Les lignes automatisées exigent des vitesses ≥ 1,2 m/min, mais les vitesses élevées risquent d'entraîner une instabilité de l'arc ou un transfert irrégulier des gouttes.
c. Pontage des jeux dans les soudures complexes
Les plateaux présentent souvent des jeux importants (0,5 à 1,5 mm) ou des joints irréguliers (par exemple, des joints en T).
(3) Compatibilité entre la conception structurelle et le procédé de fabrication
a. Contrôle de la déformation par soudage de plaques minces
L'épaisseur de paroi des palettes en alliage d'aluminium est généralement de 2 à 3 mm. La déformation du soudage MAG traditionnel peut atteindre 1,2 mm, tandis que le soudage CMT permet de la réduire à moins de 0,3 mm grâce à un faible apport de chaleur. Cependant, la conception d'outillages anti-déformation et le soudage symétrique robotisé (poste de travail double) sont nécessaires pour améliorer encore la précision.
b. Continuité et étanchéité des soudures longues
La longueur de la soudure scellée du bac de batterie peut atteindre plusieurs mètres, et il est impératif d'éviter les ruptures d'arc ou les fluctuations du bain de fusion. La technologie CMT assure l'uniformité de la soudure grâce à plus de 70 cycles de rallumage d'arc par seconde, et le taux de qualification de l'étanchéité à l'air peut atteindre 99 % grâce au système de suivi laser.
c. Synergie des applications composites multi-procédés
Les palettes haut de gamme utilisent souvent le procédé composite CMT+FSW (soudage par friction-malaxage). Le CMT est utilisé pour les structures complexes (comme l'assemblage entre le cadre et la plaque inférieure). Le FSW est utilisé dans les zones à forte charge (comme les poutres longitudinales) pour améliorer la résistance. Le problème de compatibilité des paramètres d'assemblage des deux procédés (comme la température de préchauffage et le traitement thermique après soudage) doit être résolu.
3-Scénarios d'application typiques du procédé CMT dans la fabrication de bacs à batteries
(1) Assemblage de la structure principale du bac à batteries
a. Soudage du cadre et de la plaque inférieure
Le procédé CMT est largement utilisé pour l'assemblage du cadre et de la plaque inférieure des bacs à batteries en alliage d'aluminium, notamment pour les soudures longues et les plaques fines (2-3 mm d'épaisseur).
b. Assemblage de la poutre et de la plaque inférieure
Dans la conception des bacs à batteries CTP, en raison du nombre réduit de poutres et de la structure complexe, le procédé CMT est utilisé pour : le soudage de positionnement de haute précision : la connexion locale entre la poutre et la plaque inférieure (comme un joint en T) doit éviter une pénétration insuffisante. Le procédé CMT permet une pénétration stable ≥ 0,8 mm grâce au contrôle numérique de la longueur d'arc (comme la technologie Fonis CMT Advanced). Adaptation multi-matériaux : si la poutre est en alliage aluminium-magnésium (comme le 6061) et la plaque inférieure en aluminium haute résistance, le procédé CMT permet de réduire les pores grâce à la protection par gaz mixte Ar+He, tout en s'adaptant aux différences de conductivité thermique des différents matériaux.
(2) Soudage de plaques minces et de structures géométriques complexes
a. Soudage d'alliages d'aluminium à parois minces (2-3 mm)
La légèreté des bacs de batterie favorise l'utilisation de plaques minces, mais le soudage MIG traditionnel est sujet à la déformation. Les avantages du procédé CMT sont les suivants :
b. Soudage de plaques ultra-minces : Taixiang Automation utilise la technologie CMT pour réaliser un soudage sans projections de plaques ultra-minces de 0,3 mm pour les structures d'étanchéité des bords des bacs de batterie.
c. Pontage de soudures de formes spéciales : Pour les structures de formes spéciales telles que les nervures de renfort internes et les poutres anti-collision du bac, le mode de pontage CMT permet de combler un espace de 0,5 à 1,5 mm par rétraction du fil et redirection de l'arc afin d'éviter les défauts de fusion.
d. Soudures exigeant une étanchéité élevée : L'étanchéité du bac de batterie est directement liée à la sécurité de la batterie. Le procédé CMT garantit cela de la manière suivante :
· Soudures longues et continues : plus de 70 cycles de réamorçage d'arc par seconde (comme la technologie Fronius LaserHybrid) garantissent la continuité de plusieurs mètres de soudures, avec un taux de réussite de 99 %.
· Contrôle de l'apport de chaleur faible : par rapport au soudage laser, le CMT présente un apport de chaleur plus faible, ce qui réduit l'impact thermique des fluctuations du bain de fusion sur la couche de scellant et convient au procédé de revêtement de colle.
(3) Scénario de fabrication composite multi-processus
a. Procédé composite CMT+FSW
Sur les lignes de production de bacs de batteries haut de gamme, le CMT est souvent associé au soudage par friction-malaxage (FSW) :
Division du travail et coopération : le CMT est utilisé pour le soudage flexible de structures complexes (telles que les cadres et les joints de formes spéciales), tandis que le FSW est utilisé pour les zones à forte charge (telles que les poutres longitudinales) afin d'améliorer la résistance. Par exemple, la ligne de production automatisée de Shanghai Weisheng utilise une combinaison CMT+FSW+CNC pour augmenter l'efficacité de la production de bacs de 30 %.
Optimisation des connexions de processus : la ligne de production de Huashu Jinming adopte une conception modulaire et permet une connexion transparente avec le FSW grâce à l'adaptation des paramètres de préchauffage (par exemple, un chauffage local à 150 °C après le soudage CMT).
b. Combiné à la technologie de rivetage FDS/SPR
Dans la technologie CTP de deuxième génération, le CMT est coordonné avec les technologies de rivetage auto-serrant par friction (FDS) et auto-perçant (SPR) : Solution de connexion hybride : Par exemple, la zone porteuse du cadre et la plaque inférieure adoptent le soudage FSW, tandis que les pièces détachables (telles que les plaques de refroidissement par eau et les couches isolantes) sont prépositionnées par soudage CMT, puis fixées par rivetage FDS, en tenant compte à la fois de la résistance et de la facilité d'entretien.
Nous mettrons régulièrement à jour les informations et technologies relatives à la conception thermique et à l’allègement. Merci de votre intérêt pour Walmate.