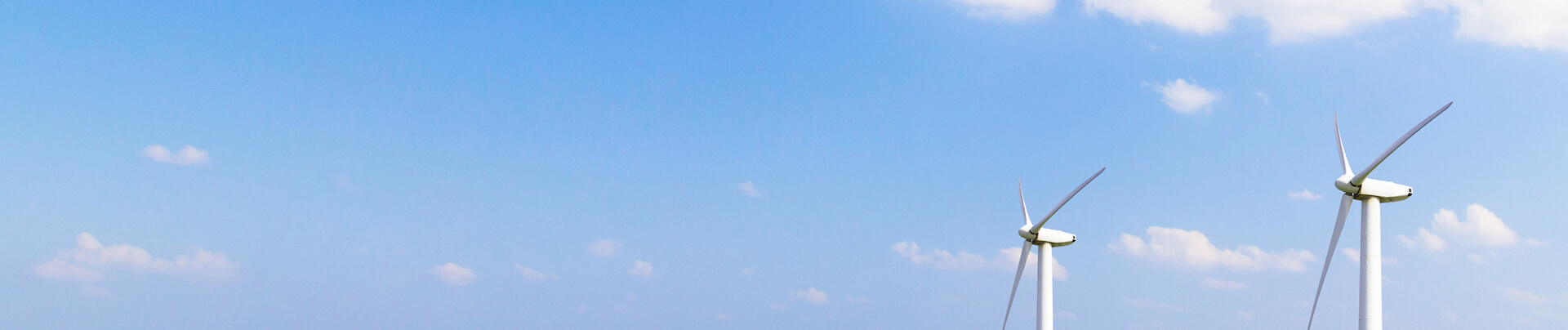
Communication and sharing promote growth
Joining Hands for Development!
With the rapid development of new energy vehicles and energy storage industries, lightweight, high safety and efficient thermal management have become core demands. Our company is deeply engaged in the field of aluminum alloy material processing. Relying on advanced material selection, forming process and welding technology, we focus on the research and development and manufacturing of battery trays, liquid cooling plates, energy storage pack boxes and radiators. Aluminum alloy has become an ideal choice for lightweight and thermal management of new energy equipment due to its low density (about 2.7g/cm³), high strength, corrosion resistance and excellent thermal conductivity (thermal conductivity is about 150-220 W/m·K).
1- Aluminum alloy material selection and key considerations
Different products have significantly different performance requirements for aluminum alloys, and it is necessary to combine strength, corrosion resistance, weldability and process adaptability to comprehensively select materials:
a. Battery tray
Common grades: 6061-T6, 6005A-T6, 6063-T6.
Selection basis:
·Must meet the tensile strength ≥ 240 MPa (such as 6061-T6) to pass the national standard extrusion, drop and ball impact tests;
·High weldability requirements, thermal cracks must be avoided (Mg/Si-strengthened 6xxx series is preferred);
·Corrosion resistance is improved by anodizing or aluminum cladding.
Figure 1- Aluminum Alloy Battery Tray
b. Energy storage pack box
Common brands: 5083, 6061-T6 (both strength and corrosion resistance).
Selection basis:
·Need to withstand vibration and impact loads, yield strength must be ≥200 MPa;
·High surface treatment requirements to avoid electrochemical corrosion.
c. Liquid cooling plate
Common brands: 3003, 6061/6063, 6082.
Selection basis:
·High thermal conductivity and corrosion resistance;
·Liquid cooling channel requires complex molding, and 6xxx series with excellent extrusion performance are preferred.
2- Differences in process performance and processing difficulties
The processing of aluminum alloys needs to adapt to their physical properties, especially in cutting, CNC, welding and surface treatment:
a. Cutting and CNC processing
Difficulties:
· High-precision hole processing is prone to burrs or deformation (such as protrusions on the edge of step holes) due to material ductility;
· Thin-walled structures (such as liquid cooling plate flow channels) need to control cutting forces to prevent warping.
Solution:
· Use diamond-coated tools to improve edge sharpness and reduce extrusion deformation;
· Optimize processing parameters (such as high speed and low feed) and cooperate with general CNC equipment to achieve stable processing.
b. Welding process
Core challenges:
· Oxide film (Al₂O₃ melting point 2050℃) hinders fusion and easily leads to pores and slag inclusions;
· Some alloys have a high tendency to hot cracks, and the line energy and welding wire composition need to be controlled.
Preferred processes:
·TIG welding (AC power supply): suitable for thin plates, and the oxide film is removed by "cathode cleaning";
·MIG welding (high current + helium mixed gas): high welding efficiency for thick plates, and controllable heat input.
Figure 2- Battery tray welding
c. Surface treatment
·Insulation pressure-resistant coating: Applied to the battery tray and the inside of the Pack box, it must pass the pressure test (≥3000V DC/1min), the coating thickness is 20-50μm, to ensure the insulation safety under high-voltage environment;
·Insulation and dehumidification coating: For the energy storage Pack box, hydrophobic materials (such as fluorocarbon resin) are used to reduce the risk of internal condensation, and the dyne value is ≥34 to ensure adhesion;
·Anti-collision protection coating: used for the outer wall of the battery tray, polyurethane elastomer (hardness ≥80 Shore A) is selected, and the impact resistance is improved by more than 30%;
·Anodizing: Conventional anti-corrosion treatment, film thickness error ≤3μm, suitable for complex structures.
3- Verification inspection and equipment adaptability
In order to meet the standards of the new energy industry (such as GB/T31467.3, UL2580), multi-dimensional verification and process adaptation are required:
a. Verification inspection
· Structural strength: Verify the load-bearing, extrusion and ball impact performance of the tray through finite element simulation (maximum stress ≤ material yield strength);
· Sealing test: The liquid cooling system uses helium leak detection (leakage rate ≤1×10⁻⁶ mbar·L/s) and cyclic pressure test (0.5-1.5MPa/5000 times);
· Coating performance verification:
Insulation coating withstand voltage test (5000V DC/60s without breakdown);
Anti-collision coating passes falling ball impact (1kg steel ball 1m height) and salt spray test (1000h without peeling).
b. Equipment adaptability optimization
· General CNC equipment transformation: Through high-precision fixture design and dynamic compensation algorithm, the processing deformation of thin-walled parts can be ≤0.1mm;
· Welding parameter library: Establish standard welding parameters (such as current and wire feeding speed) for different aluminum alloy grades to reduce the debugging cycle;
· Automated coating spraying: Use multi-axis robot spraying, combined with infrared curing technology, the coating uniformity error is ≤5%.
Conclusion
The wide application of aluminum alloys in new energy equipment is not only a victory of materials science, but also a manifestation of process innovation. Our company will continue to explore new aluminum alloys that are high-strength, corrosion-resistant, and easy to process, and promote the performance upgrade of products such as battery trays and liquid cooling plates through process innovation, helping the industry move towards an efficient and lightweight future.
We will regularly update you on technologies and information related to thermal design and lightweighting, sharing them for your reference. Thank you for your attention to Walmate.