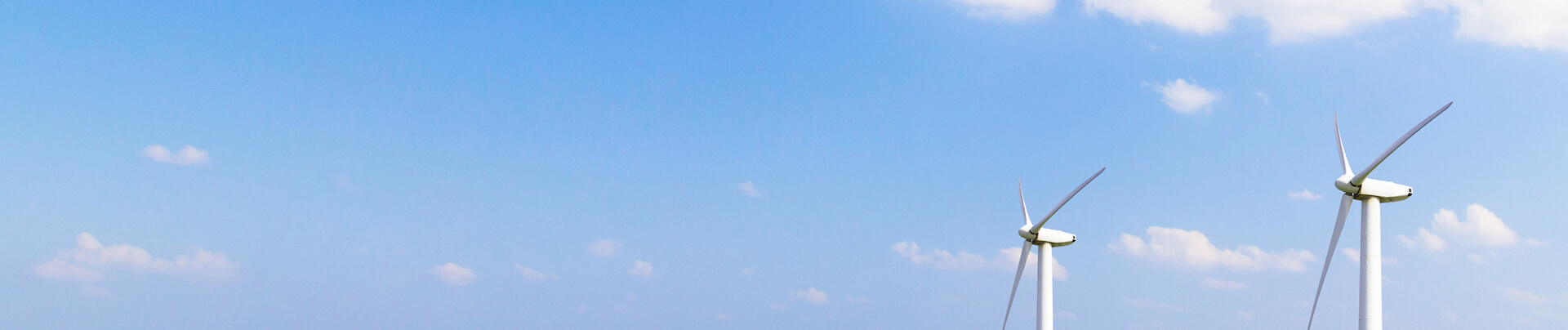
Communication and sharing promote growth
Joining Hands for Development!
As the power density of electronic devices continues to rise, heat dissipation design has become a key link affecting system reliability and lifespan. As a professional manufacturer with 19 years of experience in thermal management, we combine typical engineering cases with multi-physics field simulation experience to deeply analyze the five major technical misunderstandings that engineers tend to overlook in high-power scenarios, and provide solutions that conform to industry practices.
Misunderstanding 1: Abuse of high thermal conductivity materials, calculation deviation of interface thermal resistance
Typical problem: Excessive pursuit of theoretical values of thermal conductive materials, ignoring the engineering reality of interface contact thermal resistance.
Case analysis: A certain automotive laser radar heat dissipation module uses a pure copper substrate (thermal conductivity 401W/m·K), but the coating thickness of the thermal interface material (TIM) is not accurately controlled (designed 0.1mm, actual fluctuation ±0.05mm), and the measured contact thermal resistance reaches 0.6°C·cm²/W, causing the FPGA junction temperature to exceed the standard by 22%. After switching to preformed thermal pads (tolerance ±0.02mm, thermal resistance <0.03°C·cm²/W) and combining with vacuum sintering process, the junction temperature is reduced by 17°C, and the MTBF (mean time between failures) is increased to 100,000 hours.
Optimization plan:
Material selection: According to the ASTM D5470 standard, the thermal resistance of TIM is measured, and phase change materials or metal-filled elastomers are preferred.
Process control: Use automatic dispensing equipment (accuracy ±3%) to ensure thickness tolerance <10% and avoid air gaps.
Misunderstanding 2: Mismatch of airflow organization in air cooling system, local hot spots out of control
Typical problem: blindly stacking the number of fans, ignoring the flow channel impedance matching and boundary layer separation effect.
Engineering example: A data center GPU cluster uses 4 12038 fans (air volume 200CFM), but due to improper design of the air guide angle (90° right angle bend), the actual effective air volume is only 65% of the nominal value, and the local temperature difference reaches 40°C. After CFD simulation optimization, the air guide is changed to a gradually expanding flow channel (diffusion angle <7°), and a staggered fin layout is adopted (the spacing gradient increases from 2mm to 3.5mm), the overall wind resistance is reduced by 30%, and the hot spot temperature difference is controlled within 8°C.
Core strategy:
Flow field design: Wind tunnel testing is carried out according to ISO 5801 standard to optimize the inlet and outlet area ratio (recommended 1:1.2).
Dynamic control: Based on the Q-H curve of the PWM fan, the system impedance point is matched to the highest efficiency range (usually 60-80% of the maximum air volume).
Misconception 3: Failure of environmental protection design accelerates material aging
Typical problem: Only focusing on initial heat dissipation performance, ignoring the effects of long-term environmental stress such as humidity, heat, dust, and salt spray.
Case analysis: An offshore wind power converter uses a 6061 aluminum alloy heat sink (surface anodized). After running in a salt spray environment for 6 months, the oxide layer peeled off, causing the contact thermal resistance to increase by 50%, and the IGBT failure rate to surge. Switching to 5052 aluminum alloy (salt spray resistance >1000h) and spraying polyurethane three-proof paint (thickness 50μm, in line with IEC 60068-2-11 standard), the 3-year field failure rate dropped by 75%.
Design points:
Coating technology: Plasma spraying Al2O3 ceramic coating (thermal conductivity 30W/m·K, temperature resistance >800°C) is used in high-temperature scenarios.
Sealing structure: IP69K protection level (double-pass silicone seal + pressure relief valve) to ensure zero intrusion of dust/water vapor.
Misconception 4: Lack of transient heat load modeling and improper selection of phase change materials
Typical problem: The heat dissipation solution designed by steady-state simulation cannot cope with millisecond-level power pulses.
Measured data: A solid-state power amplifier is subjected to a 2ms@2000W pulse load in a 5G base station. The transient temperature rise of the traditional aluminum substrate solution reaches 55°C, while the microcapsule phase change material (paraffin/graphene composite, phase change latent heat 220J/g) combined with transient thermal simulation (ANSYS Icepak transient step length 1ms) is used to control the temperature rise to 18°C, meeting the MIL-STD-810G impact test requirements.
Dynamic management technology:
Phase change packaging: The honeycomb structure is used to encapsulate the phase change material (porosity>70%) to avoid liquid leakage and improve heat diffusion efficiency.
Model calibration: The simulation boundary conditions are corrected based on infrared thermal imaging (sampling rate 100Hz), and the error is <±1.5°C
Misconception 5: TCO evaluation is one-sided and ignores hidden operation and maintenance costs
Typical problem: Only the initial hardware cost is compared, and the energy consumption/maintenance/downtime losses are not quantified.
Cost comparison: A semiconductor factory originally used air-cooled cabinets (initial cost of 500,000 yuan), with an annual electricity bill of 1.2 million yuan (PUE=1.8). After upgrading to two-phase immersion liquid cooling (initial cost of 1.8 million yuan), the annual electricity bill dropped to 450,000 yuan (PUE=1.05), and due to the reduction of clean room air conditioning load, the annual comprehensive savings reached 900,000 yuan, and the incremental investment can be recovered in 2.1 years (IRR>25%).
Decision model:
Refined modeling: Introduce Monte Carlo simulation to quantify the impact of equipment failure rate (Weibull distribution) on TCO.
Policy superposition: Combined with carbon tax mechanisms (such as EU CBAM), the carbon emissions of liquid cooling systems over their entire life cycle are reduced by 60%, and an additional subsidy of 15% is obtained
Conclusion: Upgrading the thermal design paradigm from experience-driven to data-driven
Standardized process: Introduce the JESD51-14 thermal test standard in the conceptual design stage to avoid rework later (the project cycle of a certain optical module is shortened by 30%).
Multidisciplinary collaboration: Through COMSOL Multiphysics coupling electromagnetic loss (HFSS extraction) and thermal strain field, the heat dissipation efficiency of a radar TR component is improved by 40%.
Intelligent operation and maintenance: Deploy fiber grating temperature sensors (accuracy ±0.1°C) and digital twin platforms to achieve fault prediction (unexpected downtime of a supercomputing center is reduced by 90%).
Through rigorous engineering thinking and full-link data verification, thermal design engineers can accurately avoid "invisible killers" and lay the foundation for high-reliability systems. As industry practitioners, we are committed to providing closed-loop solutions from materials to systems, and jointly address thermal management challenges with customers.
We will regularly update you on technologies and information related to thermal design and lightweighting, sharing them for your reference. Thank you for your attention to Walmate.