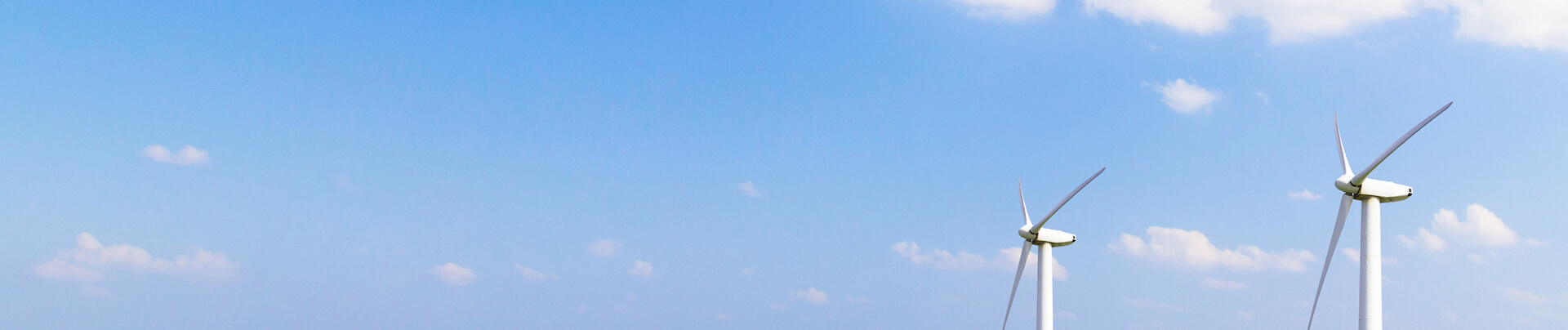
Communication and sharing promote growth
Joining Hands for Development!
CTC (Cell-to-Chassis) technology has attracted much attention because it can significantly improve the range and space efficiency of electric vehicles, but whether it can truly replace traditional battery technology is still controversial. The core bottleneck on the manufacturing side - the battery tray welding process - has become the key to determining the future of this technology: complex structural design, multi-material compatibility, and stringent thermal management requirements have put traditional welding technology to a huge test. Starting from the perspective of front-line engineers, combining industry trends and engineering practices, this article analyzes the potential and limitations of CTC technology, and explores how welding technology has become the "touchstone" of this technological revolution.
1-The "Ideal and Reality" of CTC Technology
CTC technology can theoretically reduce redundant structural parts and improve energy density by integrating the battery cell directly into the chassis, but the feasibility of its large-scale application is facing realistic challenges:
Car companies' radicalism and caution: Tesla, BYD and other leading companies have launched CTC solutions, but more manufacturers are still waiting and watching. Industry data shows that as of February 2025, CTC mass-produced models account for 15-20% of the world, and traditional CTP (Cell-to-Pack) technology is still the mainstream.
The "cost" of improved battery life: Although CTC can increase energy density by 15%-20%, the complexity of the chassis structure leads to an increase in manufacturing costs of 30%-50% (calculated by a consulting agency), and the balance between cost and benefit is not yet clear.
Maintenance economic controversy: The integrated design has caused the battery maintenance cost to soar. Insurance company data show that the replacement rate of battery assemblies after accidents of CTC models is as high as 70%, far higher than the 25% of traditional models.
These contradictions make the future of CTC technology full of variables. Whether the market can break through 20% depends on three major variables: the progress of Tesla Cybertruck mass production; whether the price war among Chinese automakers forces CTC to reduce costs; and the degree of compromise of European regulations on battery repairability. The level of welding technology on the manufacturing side will be the key to determining whether it can cross the gap between laboratory and mass production.
2-Three "life and death barriers" of welding process
For battery tray manufacturers, the implementation of CTC technology needs to overcome three core problems:
a. The game between "micron-level" precision and efficiency
Traditional welding processes can tolerate 0.5mm errors, but CTC trays need to carry more batteries, and the number of seams increases by more than 3 times, and most of them are distributed on curved and irregular parts. Tests by a manufacturer show that when the welding positioning error exceeds 0.15mm, the yield rate of battery cell assembly will drop sharply from 99% to 82%. What's more tricky is that the improvement in precision is often accompanied by a decrease in efficiency-although the accuracy of laser welding is high, the equipment cost is more than 5 times that of traditional welding.
b. The "water and fire" of mixed materials
In order to balance lightweight and strength, CTC trays often use a mixed structure of "aluminum alloy + carbon fiber + special steel". The difference in thermal expansion coefficients of different materials can be up to 20 times (such as aluminum 23μm/m·K vs. carbon fiber 0.8μm/m·K), which is easy to generate internal stress during welding and cause cracking. When a company tried to connect aluminum and carbon fiber, the crack rate of the weld was as high as 18%, far exceeding the industry's acceptable threshold of 3%.
c. "Invisible killer" of the heat-affected zone
High welding temperature may damage the insulating materials or sensor circuits around the battery cell. A car company once increased the self-discharge rate of the battery module by 50% due to improper control of welding heat input. Engineers must control the welding temperature fluctuation within ±15℃ within 0.1 seconds - this is equivalent to installing a "high-precision temperature brake" on the welding gun.
3-The way out: There is no silver bullet, only system innovation
Faced with these challenges, the industry is exploring three breakthrough paths:
a. "Cocktail therapy" of process combination
Laser arc hybrid welding: Combining the accuracy of laser welding with the advantages of arc welding penetration, the welding speed of aluminum alloy is increased by 40%;
Cold metal transition technology (CMT): Through precise heat input control, the area of heat affected zone is reduced by 60%;
Robot intelligent compensation system: Automatically adjust the welding gun path based on real-time weld scanning data, and increase the qualified rate of complex curved surface welding from 75% to 95%.
b. "Pre-compromise" on the material side
Some companies have begun to jointly develop "welding-friendly" composite materials with material suppliers. For example, the welding crack sensitivity of a domestic modified aluminum alloy (aluminum alloy material adjusted by physical, chemical or process means) has been reduced from level 7 to level 3 (according to ISO standards). Although it sacrifices 5% of the lightweight effect, it increases the welding yield to 98%.
4- Engineers’ new proposition: Finding certainty in uncertainty
a. The controversy over CTC technology is essentially a game between “system optimization” and “local limits”:
If the breakthrough speed of welding process is slower than the cost reduction expectations of car companies, CTC may become a niche technology;
If materials, processes, and testing technologies make breakthroughs in a coordinated manner, it is expected to usher in a new era of electric vehicle structural design.
b. For engineers, it is necessary to reconstruct capabilities from two dimensions:
Cross-domain knowledge integration: understand the sensitive threshold of electrochemical properties to welding heat input;
Agile response capability: A case study of a European supplier shows that the team that can complete the optimization of welding parameters of new alloy materials within a week has a 3-fold increase in the probability of obtaining orders.
CTC technology stands at the crossroads of “disruptive innovation” and “mass production trap”. It may not completely replace existing technology, but it is forcing the welding process to evolve towards higher precision, stronger compatibility, and more intelligent control. In this technology marathon, the real winner may not be the earliest car company, but the engineering team that turns “impossible welds” into “standardized interfaces” on the manufacturing side.
We will regularly update you on technologies and information related to thermal design and lightweighting, sharing them for your reference. Thank you for your attention to Walmate.