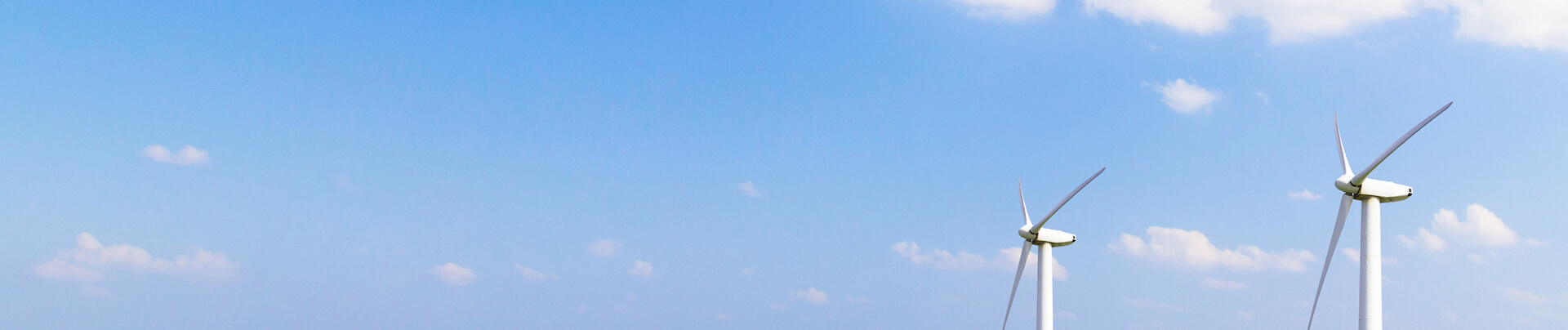
Communication and sharing promote growth
Joining Hands for Development!
As CTP (Cell to Pack) technology completely subverts the traditional battery pack structure, the "role" of the battery tray has shifted from passive load-bearing to active integration. Welding technology has become the core of safety and performance. The requirements of lightweight (wall thickness is only 1.5mm), zero pore sealing, and multi-material (aluminum/copper/carbon fiber) integration have caused traditional welding to fall into the dilemma of deformation and defects. The industry is making breakthroughs through material innovation, intelligent quality inspection and process iteration. This article will analyze the disruptive challenges that CTP poses to welding and explore the technical path to high precision and high reliability.
1-Analysis of the changes in the structural design requirements of battery trays due to CTP technology
CTP (Cell to Pack) technology directly integrates the battery cells into the battery pack by eliminating the module structure in the traditional battery pack. This technological innovation puts forward all-round and multi-dimensional upgrade requirements for the structural design of the battery tray. The following is a specific analysis from the perspectives of materials, performance, process, integration, etc.:
(1) Comprehensive improvement of structural strength and shockproof performance
a. Mechanical bearing requirements after eliminating the module:
After CTP technology eliminates the module structure, the battery tray needs to directly bear the support, fixation and external force buffering functions of the battery cell. The traditional module disperses the mechanical load, while the CTP tray needs to absorb the expansion deformation of the battery cell during charging and discharging as a whole (for example, the expansion force of the square battery cell can reach 10-20kN), while resisting the vibration, extrusion and impact load during vehicle driving.
b. Material and structural optimization direction
· Dominance of high-strength aluminum alloy: Early steel was gradually replaced due to its heavy weight, and 6061-T6 became the mainstream. It has high specific strength and strong corrosion resistance, which can meet the dual requirements of lightweight and high rigidity.
· Composite structure design: For example, the "double-frame ring beam" structure of Leapmotor enhances local impact resistance through longitudinal and transverse beam compartments, while using extrusion technology to optimize material distribution and reduce redundant weight.
· Exploration of magnesium-aluminum alloy and carbon fiber: Magnesium-aluminum alloy is 30% lighter than traditional aluminum materials, and carbon fiber composite materials have both high strength and lightweight characteristics, but are currently only used in high-end models due to cost and process maturity.
(2) Requirements for integrated air tightness and thermal management
a. Sealing performance upgrade
After the module is removed, the internal coolant circulation and gas sealing of the battery pack are completely dependent on the tray, and welding defects (such as pores and cracks) may lead to leakage risks.
Figure 1-Battery tray air tightness test
b. Integration of thermal management functions
CTP trays need to integrate components such as liquid cooling plates and thermal conductive adhesives. For example, structural adhesives are used to fix the battery cells and transfer expansion stress, and polyurethane thermal conductive adhesives (thermal conductivity > 1.5 W/m·K) are used for heat conduction between battery cells and with liquid cooling tubes. The amount of adhesive used in a single PACK is more than 50% higher than that in traditional structures. Flow channels need to be designed inside the tray to optimize cooling efficiency while avoiding damage to the sealing caused by the heat affected zone of welding.
(3) Lightweighting and material innovation
a. Material selection trends
Aluminum alloy extrusion and die-casting process: extruded aluminum profiles are used for frame structures (such as Tesla's 4680 battery tray), and die-casting processes (such as integrated die-casting) simplify the welding process and reduce weight by 15%-20%.
Application of plastic composite materials: For example, glass fiber reinforced PA6 materials are used in non-load-bearing parts to further reduce weight, but the compatibility problem with the metal connection interface needs to be solved.
b. Lightweight design strategy
Topology optimization: Reduce redundant materials through CAE simulation and reduce the weight of the tray while ensuring strength.
Thin-wall and integrated: The wall thickness of the tray is reduced from 3mm to 1.5-2mm, and functional components such as BMS brackets and wiring harness channels are integrated to reduce the number of parts.
(4) Integration and modular design
a. High integration of functional components
CTP trays need to integrate modules such as battery management system (BMS), high-voltage connectors, and fireproof isolation layers.
b. Modular and compatible design
The welding production line needs to support mixed production of multiple models of trays, be able to achieve "one-click change of type", and be compatible with tray structures of different battery cell sizes (such as square and cylindrical).
2-Specific challenges of CTP technology innovation to welding process
CTP (Cell to Pack) technology has significantly improved space utilization and energy density, but it has also posed unprecedented challenges to welding process.
(1) The difficulty of controlling welding defects has increased sharply
a. Porosity and sealing challenges
After CTP technology eliminates the module, the battery tray needs to directly assume the sealing function. Welding pores (a common defect in aluminum alloy welding) will directly lead to the risk of coolant leakage or gas penetration.
b. Cracks and material compatibility
High zinc aluminum alloys (such as 7 series) are prone to cracks due to thermal stress during welding.
c. Gap and assembly error
The direct integration of multiple cells leads to an increase in the number of splicing points of the tray structure. The accumulation of assembly errors may cause the weld gap to exceed ±1mm.
(2) Process adaptation problems brought about by the upgrade of the material system
a. Welding challenges of lightweight materials
The CTP tray material has shifted from steel to aluminum alloy (6061-T6, 7075-T6), magnesium-aluminum alloy (30% weight reduction) and carbon fiber composite materials. Aluminum alloy welding needs to solve the problem of insufficient penetration caused by the difficult melting of the oxide film and high thermal conductivity.
b. Dissimilar material connection technology
When the tray integrates functional components such as liquid cooling plate (copper/aluminum) and fireproof layer (ceramic matrix composite material), brittle intermetallic compounds are prone to appear at the interface of dissimilar materials.
(3) Upgraded structural complexity and precision requirements
a. Deformation control of large-size thin-walled structures
The wall thickness of the CTP tray is reduced from 3mm to 1.5-2mm, and the sensitivity of welding thermal deformation increases sharply.
b. High-density solder joints and process efficiency
The number of solder joints on a single tray has increased from 2,000 in traditional modules to more than 5,000.
Figure 2- Battery tray welding
3-Upgrade of production process and quality control
CTP technology promotes the transformation of battery tray welding from "single process" to "multi-technology collaboration, intelligence, and greening". Manufacturers need to focus on three major directions:
Technology upgrade: break through the control of defects such as pores and cracks, and adapt to lightweight materials;
Intelligent transition: full process digitization and AI quality inspection to achieve high-precision production;
Ecological collaboration: jointly build technical standards with material suppliers, equipment suppliers, and OEMs.
We will regularly update you on technologies and information related to thermal design and lightweighting, sharing them for your reference. Thank you for your attention to Walmate.