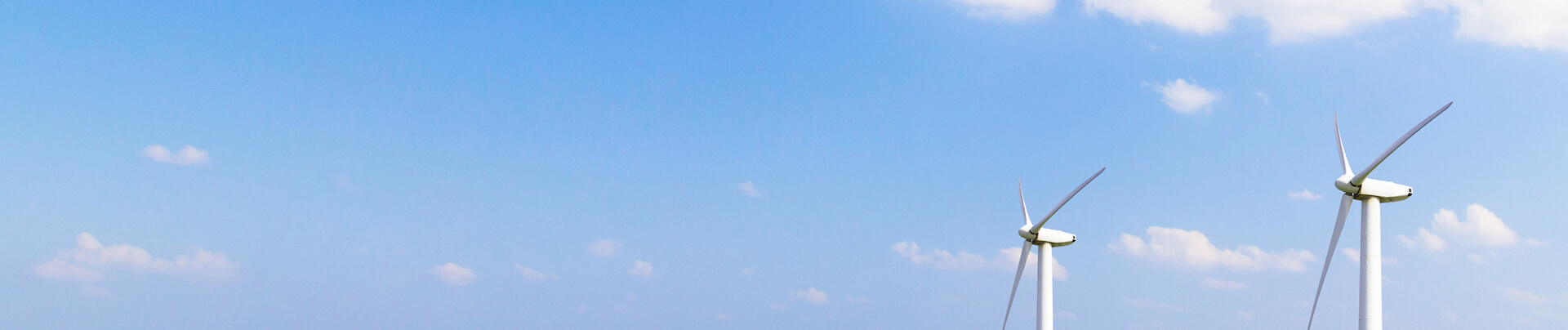
Austausch und Teilen fördern Wachstum,
Zusammenarbeit führt zu gemeinsamer Entwicklung.
Die CTC-Technologie (Cell-to-Chassis) steht aufgrund ihrer Fähigkeit, Reichweite und Raumeffizienz von Elektrofahrzeugen signifikant zu steigern, im Fokus. Doch ob sie traditionelle Batterietechnologien tatsächlich ersetzen kann, bleibt umstritten. Der zentrale Engpass in der Fertigung – die Schweißtechnik für Batteriegehäuse – entscheidet über ihre Zukunft: Komplexe Strukturen, Materialvielfalt und anspruchsvolle Thermomanagement-Anforderungen stellen konventionelle Schweißverfahren vor enorme Prüfungen. Dieser Artikel analysiert aus Ingenieursperspektive das Potenzial und die Grenzen der CTC-Technologie und zeigt, wie Schweißprozesse zum „Gradmesser“ dieser technologischen Revolution werden.
1-„Ideale vs. Realität“ der CTC-Technologie
CTC integriert Zellen direkt in das Fahrwerk, reduziert theoretisch überflüssige Komponenten und erhöht die Energiedichte. Doch die Machbarkeit der Massenanwendung wird kritisch hinterfragt:
Ambitionen vs. Zurückhaltung der Hersteller: Tesla, BYD und andere Marktführer haben CTC-Lösungen eingeführt, doch viele Hersteller zögern noch. Bis 2025 werden CTC-Modelle nur 15–20 % des globalen Marktes ausmachen, während CTP (Cell-to-Pack) dominant bleibt.
„Kosten der Reichweitensteigerung“: CTC erhöht die Energiedichte um 15–20 %, doch die strukturelle Komplexität treibt die Fertigungskosten um 30–50 % in die Höhe (Berechnungen von Beratungsunternehmen). Das Kosten-Nutzen-Verhältnis bleibt unklar.
Reparaturkosten-Debatte: Die monolithische Bauweise erhöht die Batteriereparaturkosten drastisch. Versicherungsdaten zeigen, dass bei CTC-Fahrzeugen nach Unfällen in 70 % der Fälle das gesamte Batteriesystem ersetzt werden muss – im Vergleich zu 25 % bei konventionellen Modellen.
Diese Widersprüche machen die Zukunft von CTC ungewiss. Ob der Marktanteil 20 % übersteigt, hängt von drei Faktoren ab: Teslas Cybertruck-Serienproduktion, Kostensenkungsdruck durch chinesische Preiskämpfe und europäische Regulierung zur Batteriereparaturfähigkeit. Die Schweißtechnik wird entscheiden, ob CTC die Kluft zwischen Labor und Massenproduktion überwindet.
2-Drei entscheidende Hürden des Schweißprozesses
Hersteller von Batterieträgern müssen bei der Implementierung der CTC-Technologie drei Kernprobleme überwinden:
a. Präzision im Mikrometerbereich und Effizienz
Traditionelle Schweißverfahren tolerieren Fehler von 0,5 mm. CTC-Träger müssen jedoch mehr Batterien aufnehmen, die Anzahl der Nähte erhöht sich um mehr als das Dreifache, und die meisten davon befinden sich auf gekrümmten und unregelmäßigen Teilen. Tests eines Herstellers zeigen, dass bei einem Schweißpositionierungsfehler von mehr als 0,15 mm die Ausbeute der Batteriezellenmontage von 99 % auf 82 % stark sinkt. Erschwerend kommt hinzu, dass die verbesserte Präzision oft mit einem Rückgang der Effizienz einhergeht – obwohl die Genauigkeit des Laserschweißens hoch ist, sind die Anlagenkosten mehr als fünfmal so hoch wie beim herkömmlichen Schweißen.
b. Materialmix: Wasser und Feuer
Um ein ausgewogenes Verhältnis zwischen geringem Gewicht und Festigkeit zu erreichen, wird für CTC-Träger häufig eine Mischstruktur aus Aluminiumlegierung, Kohlefaser und Spezialstahl verwendet. Die Unterschiede im Wärmeausdehnungskoeffizienten verschiedener Materialien können bis zu 20-mal so groß sein (z. B. Aluminium 23 μm/m·K gegenüber Kohlefaser 0,8 μm/m·K). Dadurch entstehen beim Schweißen leicht innere Spannungen und können zu Rissen führen. Beim Versuch, Aluminium und Kohlefaser zu verbinden, erreichte die Rissrate der Schweißnaht bis zu 18 % und überschritt damit deutlich den branchenüblichen Grenzwert von 3 %.
c. „Unsichtbarer Killer“ der Wärmeeinflusszone
Hohe Schweißtemperaturen können die Isoliermaterialien oder Sensorschaltungen um die Batteriezelle beschädigen. Ein Automobilhersteller erhöhte die Selbstentladungsrate des Batteriemoduls aufgrund unsachgemäßer Kontrolle der Schweißwärmezufuhr um 50 %. Ingenieure müssen die Schweißtemperaturschwankungen innerhalb von 0,1 Sekunden auf ±15 °C genau kontrollieren – dies entspricht dem Einbau einer hochpräzisen Temperaturbremse am Schweißbrenner.
3-Der Ausweg: Kein Patentrezept, nur Systeminnovation
Angesichts dieser Herausforderungen erkundet die Branche drei bahnbrechende Wege:
a. „Cocktailtherapie“ durch Prozesskombination
Laser-Lichtbogen-Hybridschweißen: Durch die Kombination der Präzision des Laserschweißens mit den Vorteilen des Lichtbogenschweißens wird die Schweißgeschwindigkeit von Aluminiumlegierungen um 40 % erhöht;
Kaltmetall-Übergangstechnologie (CMT): Durch präzise Steuerung der Wärmezufuhr wird die Wärmeeinflusszone um 60 % reduziert;
Intelligentes Roboterkompensationssystem: Automatische Anpassung des Schweißbrennerpfads anhand von Echtzeit-Schweißdaten und Steigerung der qualifizierten Schweißrate komplexer gekrümmter Oberflächen von 75 % auf 95 %.
b. Kompromisse im Vorfeld der Werkstoffentwicklung
Einige Unternehmen entwickeln gemeinsam mit Materiallieferanten schweißfreundliche Verbundwerkstoffe. Beispielsweise wurde die Schweißrissempfindlichkeit einer inländischen modifizierten Aluminiumlegierung (physikalische, chemische oder prozesstechnisch modifiziertes Aluminiumlegierungsmaterial) von Stufe 7 auf Stufe 3 (gemäß ISO-Normen) reduziert. Obwohl dadurch 5 % des Leichtbaueffekts verloren gehen, erhöht sich die Schweißausbeute auf 98 %.
c. „Digitaler Zwilling“ in der Erkennungsdimension
Durch die Erfassung aller Daten des Schweißprozesses (Strom, Temperatur, Geschwindigkeit usw.) und die Kombination mit KI-Modellen wird die Fehlerwahrscheinlichkeit vorhergesagt. Nach der Einführung dieser Technologie in einem Werk stieg die Online-Erkennungsrate von Schweißfehlern von 80 % auf 97 % und die Ausschusskosten wurden um 45 % gesenkt.
4-Neue Aufgaben für Ingenieure: Sicherheit in der Unsicherheit finden
a. CTCs Kontroverse ist ein Kampf zwischen „Systemoptimierung“ und „lokalen Grenzen“:
Wenn Schweißtechnik-Fortschritte langsamer sind als Kostensenkungsziele, bleibt CTC eine Nische.
Bei Durchbrüchen in Material, Technik und Prüfung könnte CTC ein neues Zeitalter einläuten.
b. Ingenieure müssen Kompetenzen neu definieren:
Interdisziplinäres Wissen: Verständnis für elektrochemische Sensibilität gegenüber Schweißwärme.
Agilität: Teams, die Schweißparameter für neue Legierungen in einer Woche optimieren, verdreifachen ihre Auftragschancen (europäischer Fall).
CTC steht am Scheideweg zwischen „disruptiver Innovation“ und „Serienfallen“. Es wird bestehende Technologien nicht vollständig ersetzen, zwingt die Schweißtechnik jedoch zu höherer Präzision, Materialkompatibilität und Intelligenz. Die wahren Gewinner sind nicht die Pionier-Hersteller, sondern Ingenieurteams, die „unmögliche Nähte“ in standardisierte Schnittstellen verwandeln.
Wir werden regelmäßig Informationen und Technologien zu Wärmedesign und Leichtbau aktualisieren und mit Ihnen teilen. Vielen Dank für Ihr Interesse an Walmate.