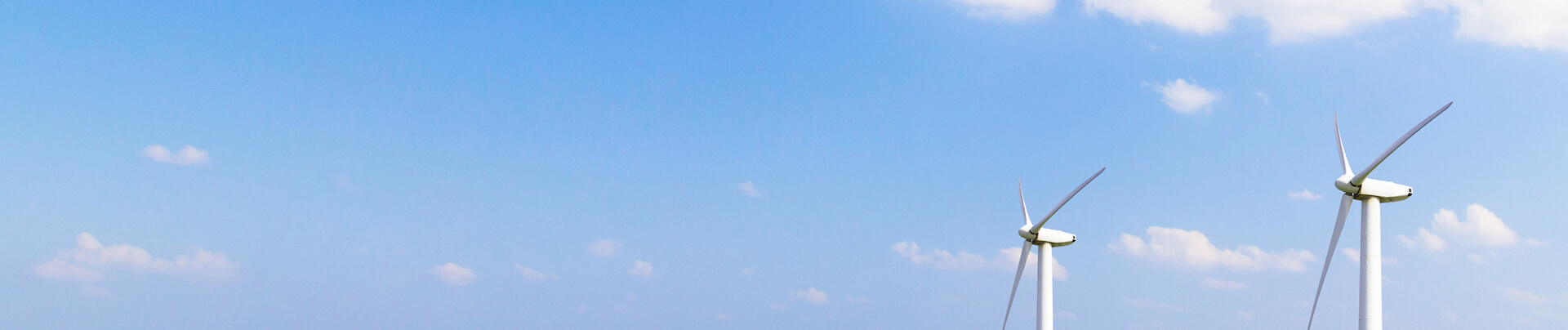
Austausch und Teilen fördern Wachstum,
Zusammenarbeit führt zu gemeinsamer Entwicklung.
Da die CTP-Technologie (Cell to Pack) die traditionelle Batteriepackstruktur vollständig auf den Kopf stellt, hat sich die Rolle des Batterieträgers von passiver Tragfähigkeit zur aktiven Integration verlagert. Schweißtechnologie ist zum Kern von Sicherheit und Leistung geworden. Die Anforderungen an geringes Gewicht (Wandstärke nur 1,5 mm), porenfreie Versiegelung und die Integration mehrerer Materialien (Aluminium/Kupfer/Kohlefaser) haben dazu geführt, dass traditionelle Schweißverfahren mit Verformungen und Defekten zu kämpfen haben. Die Branche erzielt Durchbrüche durch Materialinnovation, intelligente Qualitätsprüfung und Prozessiteration. Dieser Artikel analysiert die disruptiven Herausforderungen, die CTP für das Schweißen mit sich bringt, und zeigt den technischen Weg zu hoher Präzision und Zuverlässigkeit auf.
1-Analyse der veränderten Anforderungen an die Struktur von Batterieträgern durch die CTP-Technologie
Die CTP-Technologie (Cell to Pack) integriert die Batteriezellen direkt in den Batteriepack, indem die Modulstruktur herkömmlicher Batteriepacks eliminiert wird. Diese technologische Innovation stellt umfassende und mehrdimensionale Anforderungen an die Struktur des Batterieträgers. Im Folgenden wird eine spezifische Analyse unter den Gesichtspunkten Material, Leistung, Prozess und Integration vorgenommen:
(1) Umfassende Verbesserung der Strukturfestigkeit und Stoßfestigkeit
a. Anforderungen an die mechanische Lagerung nach dem Wegfall des Moduls:
Nach dem Wegfall der Modulstruktur durch die CTP-Technologie muss der Batterieträger die Funktionen der Unterstützung, Fixierung und Dämpfung externer Kräfte der Batteriezelle direkt übernehmen. Das herkömmliche Modul verteilt die mechanische Belastung, während der CTP-Träger die Dehnungsverformung der Batteriezelle beim Laden und Entladen als Ganzes absorbieren muss (beispielsweise kann die Dehnungskraft einer quadratischen Batteriezelle 10–20 kN erreichen) und gleichzeitig Vibrationen, Extrusion und Stoßbelastungen während der Fahrt standhalten muss.
b. Material- und Strukturoptimierung
· Dominanz hochfester Aluminiumlegierungen: Frühere Stähle wurden aufgrund ihres hohen Gewichts allmählich ersetzt, und 6061-T6 setzte sich durch. Es zeichnet sich durch hohe spezifische Festigkeit und hohe Korrosionsbeständigkeit aus und erfüllt damit die Anforderungen an geringes Gewicht und hohe Steifigkeit.
· Verbundkonstruktionen: Beispielsweise erhöht die Doppelrahmen-Ringträgerstruktur von Leapmotor die lokale Stoßfestigkeit durch Längs- und Querträgerfächer. Gleichzeitig wird durch Extrusionstechnologie die Materialverteilung optimiert und unnötiges Gewicht reduziert.
· Erforschung von Magnesium-Aluminium-Legierungen und Kohlefaser: Magnesium-Aluminium-Legierungen sind 30 % leichter als herkömmliche Aluminiumwerkstoffe. Kohlefaser-Verbundwerkstoffe zeichnen sich durch hohe Festigkeit und geringes Gewicht aus, werden aber derzeit aufgrund der Kosten und der Prozessreife nur in High-End-Modellen eingesetzt.
(2) Anforderungen an integrierte Luftdichtheit und Wärmemanagement
a. Verbesserung der Dichtungsleistung
Nach dem Ausbau des Moduls sind die interne Kühlmittelzirkulation und die Gasabdichtung des Batteriepacks vollständig vom Träger abhängig. Schweißfehler (wie Poren und Risse) können zu Undichtigkeiten führen.
Abbildung 1 – Luftdichtheitstest des Batteriefachs
b. Integration von Wärmemanagementfunktionen
CTP-Trays müssen Komponenten wie Flüssigkeitskühlplatten und wärmeleitende Klebstoffe integrieren. Beispielsweise werden Strukturklebstoffe zur Fixierung der Batteriezellen und zur Übertragung von Dehnungsspannungen verwendet, während Polyurethan-Wärmeleitklebstoffe (Wärmeleitfähigkeit > 1,5 W/m·K) zur Wärmeleitung zwischen den Batteriezellen und mit Flüssigkeitskühlschläuchen eingesetzt werden. Die Klebstoffmenge pro PACK ist mehr als 50 % höher als bei herkömmlichen Strukturen. Strömungskanäle im Tray müssen so gestaltet werden, dass die Kühleffizienz optimiert und gleichzeitig Schäden an der Dichtung durch die wärmebeeinflusste Schweißzone vermieden werden.
(3) Leichtbau und Materialinnovation
a. Trends bei der Materialauswahl
Extrusions- und Druckgussverfahren für Aluminiumlegierungen: Stranggepresste Aluminiumprofile werden für Rahmenstrukturen verwendet (z. B. für den 4680-Batterietray von Tesla). Druckgussverfahren (z. B. integriertes Druckgießen) vereinfachen den Schweißprozess und reduzieren das Gewicht um 15–20 %.
Einsatz von Kunststoffverbundwerkstoffen: Beispielsweise werden glasfaserverstärkte PA6-Werkstoffe in nichttragenden Teilen eingesetzt, um das Gewicht weiter zu reduzieren. Allerdings muss das Kompatibilitätsproblem mit der metallischen Verbindungsschnittstelle gelöst werden.
b. Leichtbaustrategie
Topologieoptimierung: Reduzierung redundanter Materialien durch CAE-Simulation und Reduzierung des Gewichts des Trays bei gleichzeitiger Gewährleistung der Festigkeit.
Dünnwandig und integriert: Die Wandstärke des Trays wird von 3 mm auf 1,5–2 mm reduziert, und Funktionskomponenten wie BMS-Halterungen und Kabelbaumkanäle werden integriert, um die Teileanzahl zu reduzieren.
(4) Integration und modulares Design
a. Hohe Integration funktionaler Komponenten
CTP-Trays müssen Module wie Batteriemanagementsystem (BMS), Hochvolt-Steckverbinder und feuerfeste Isolationsschichten integrieren.
b. Modulares und kompatibles Design
Die Schweißproduktionslinie muss die gemischte Produktion verschiedener Tray-Modelle unterstützen, einen Typwechsel per Mausklick ermöglichen und mit Tray-Strukturen unterschiedlicher Batteriezellengrößen (z. B. quadratisch und zylindrisch) kompatibel sein.
2-Spezifische Herausforderungen der CTP-Technologie für den Schweißprozess
Die CTP-Technologie (Cell to Pack) hat die Raumausnutzung und Energiedichte deutlich verbessert, stellt aber auch den Schweißprozess vor beispiellose Herausforderungen.
(1) Die Kontrolle von Schweißfehlern ist stark gestiegen.
a. Porosität und Dichtungsprobleme
Nachdem die CTP-Technologie das Modul eliminiert hat, muss der Batterieträger die Dichtungsfunktion direkt übernehmen. Schweißporen (ein häufiger Fehler beim Schweißen von Aluminiumlegierungen) führen direkt zu Kühlmittelleckagen oder Gaseintritt.
b. Risse und Materialverträglichkeit
Hochzinkhaltige Aluminiumlegierungen (wie z. B. die 7er-Serie) neigen aufgrund thermischer Spannungen beim Schweißen zu Rissen.
c. Spalt- und Montagefehler
Die direkte Integration mehrerer Zellen führt zu einer erhöhten Anzahl von Verbindungsstellen in der Trägerstruktur. Die Häufung von Montagefehlern kann dazu führen, dass der Schweißspalt ±1 mm überschreitet.
(2) Probleme bei der Prozessanpassung durch die Weiterentwicklung des Materialsystems
a. Herausforderungen beim Schweißen von Leichtbauwerkstoffen
Der Werkstoff für CTP-Schalen hat sich von Stahl zu Aluminiumlegierungen (6061-T6, 7075-T6), Magnesium-Aluminium-Legierungen (30 % Gewichtsreduzierung) und Kohlefaserverbundwerkstoffen entwickelt. Beim Schweißen von Aluminiumlegierungen muss das Problem der unzureichenden Durchdringung gelöst werden, das durch das schwierige Schmelzen der Oxidschicht und die hohe Wärmeleitfähigkeit verursacht wird.
b. Verbindungstechnologie für ungleichartige Werkstoffe
Wenn die Schale Funktionskomponenten wie eine Flüssigkeitskühlplatte (Kupfer/Aluminium) und eine Feuerschutzschicht (Keramikmatrix-Verbundwerkstoff) integriert, bilden sich an den Schnittstellen ungleichartiger Werkstoffe leicht spröde intermetallische Verbindungen.
(3) Erhöhte Anforderungen an strukturelle Komplexität und Präzision
a. Kontrolle der Verformung großer, dünnwandiger Strukturen
Die Wandstärke der CTP-Schale reduziert sich von 3 mm auf 1,5–2 mm, wodurch die Empfindlichkeit gegenüber thermischer Schweißverformung stark zunimmt.
b. Lötstellen mit hoher Dichte und Prozesseffizienz
Die Anzahl der Lötstellen auf einem einzelnen Tray ist von 2.000 bei herkömmlichen Modulen auf über 5.000 gestiegen.
Abbildung 2 - Schweißen des Batteriefachs
3-Verbesserung des Produktionsprozesses und der Qualitätskontrolle
Die CTP-Technologie fördert die Transformation des Batterieträgerschweißens vom Einzelprozess zum technologieübergreifenden, intelligenten und umweltfreundlichen Prozess. Hersteller müssen sich auf drei Hauptbereiche konzentrieren:
Technologieverbesserung: Durchbruch bei der Kontrolle von Defekten wie Poren und Rissen und Anpassung an Leichtbaumaterialien;
Intelligente Transformation: Vollständige Prozessdigitalisierung und KI-Qualitätsprüfung für eine hochpräzise Produktion;
Ökologische Zusammenarbeit: Gemeinsame Entwicklung technischer Standards mit Materiallieferanten, Anlagenbauern und OEMs.
Wir werden regelmäßig Informationen und Technologien zu Wärmedesign und Leichtbau aktualisieren und mit Ihnen teilen. Vielen Dank für Ihr Interesse an Walmate.