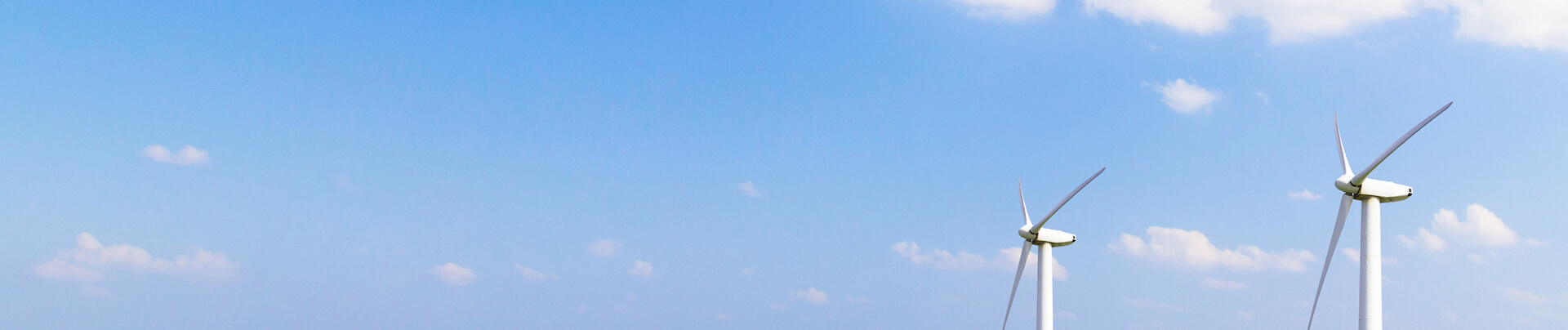
Austausch und Teilen fördern Wachstum,
Zusammenarbeit führt zu gemeinsamer Entwicklung.
Leichtbaumaterialien wie Aluminiumlegierungen sind aufgrund ihrer hervorragenden Eigenschaften erste Wahl, doch stellen geringer Wärmeeintrag, Verformungskontrolle und Prozessstabilität bei Dünnblechen hohe Anforderungen an traditionelle Schweißtechniken. Das Kaltmetalltransfer-Schweißen (CMT) bietet mit seinen Vorteilen – geringer Wärmeeintrag, spritzerfreier Übergang und intelligente Parametersteuerung – eine innovative Lösung für die Batteriegehäusefertigung.
Dieser Artikel untersucht eingehend die präzise Steuerung von CMT in der Dünnblechverarbeitung, analysiert Anpassungsfähigkeit, technische Herausforderungen und kombinierte Anwendungsszenarien, um theoretische und praktische Leitlinien für effiziente Hochqualitätsproduktion zu liefern.
Abbildung 1: CMT-Schweißen des unteren Kühlkastens für 104S-Energiespeicherbatterien
1-Anforderungen an Batteriegehäuseschweißungen und CMT-Kompatibilität
CMT erfüllt durch geringen Wärmeeintrag, spritzerfreien Übergang und intelligente Steuerung präzise die Anforderungen an Präzision, Verformungsminimierung und Effizienz.
(1)Kernanforderungen an das Schweißen von Batteriegehäusen
a. Materialkompatibilität und Leichtbau
Batterieträger bestehen hauptsächlich aus leichten Aluminiumlegierungen (z. B. 6xxx-Serie, 6061) oder Kohlefaserverbundwerkstoffen für High-End-Modelle. Diese erfordern eine hohe Festigkeit (60–70 % Zugfestigkeit des Grundmaterials) und eine geringe Dichte (Aluminiumlegierung: 2,7 g/cm³).
Verbindung ungleichartiger Materialien: Bei hybriden Stahl-Aluminium-Strukturen müssen Unterschiede im Wärmeausdehnungskoeffizienten berücksichtigt werden, um Verformungen zu minimieren.
b. Schweißqualität und Leistungskennzahlen
Geringe Wärmezufuhr und Verformungskontrolle: Bei dünnen Blechen (0,3–3 mm) darf die Verformung ≤ 2 mm betragen. Lange, lineare Schweißnähte erfordern segmentiertes Schweißen oder eine verformungssichere Konstruktion.
Abdichtung und Festigkeit: Schweißnähte müssen vollständig abgedichtet sein, um Elektrolytaustritt zu verhindern und Scherprüfungen zu bestehen (z. B. T/CWAN 0027-2022-Standard).
Porositätskontrolle: Aluminiumlegierungsschweißen ist anfällig für Porosität, daher ist eine Porositätsrate von ≤ 0,5 % erforderlich.
c. Produktionseffizienz und Automatisierungsanforderungen
Die Chargenproduktion erfordert eine Schweißgeschwindigkeit von ≥7 mm/s, wodurch die Schweißzeit für einzelne Schalen auf 5–10 Minuten reduziert wird.
Automatisierte Arbeitsstationen müssen ein Doppelstationen-Design (gleichzeitiges Montieren und Schweißen) und die Zusammenarbeit mehrerer Roboter unterstützen.
(2)Schlüsselvorteile von CMT für Batteriegehäuse
a. Präzise Steuerung des Wärmeeintrags
CMT reduziert Wärmeeintrag um 33 % gegenüber MIG-Schweißen, ideal für ultradünne Bleche (0,3 mm; kein Durchbrennrisiko).
Kalt-Heiß-Zyklen minimieren Wärmeakkumulation; Verformung ≤1,5 mm (Beispiele: BYD, BAIC).
b. Prozessstabilität und Qualitätssteigerung
Spritzerfreies Schweißen: Mechanischer Drahtrückzug verhindert Spritzer, reduziert Nacharbeit.
Porositätsoptimierung: Ar+30 % He-Schutzgas reduziert Porenanzahl um 50 %; Porengröße ≤0,3 mm.
Toleranz gegenüber Spalten: Kompensiert Montagespalten bis 1,5 mm, senkt Anforderungen an Spannvorrichtungen.
c. Automatisierungsintegration und Effizienz
Doppelstationen (z. B. Taixiang Automation) steigern Effizienz um 100 %.
Symmetrisches Robotersschweißen + Verformungsausgleich reduziert Taktzeit auf <10 Minuten.
2-Technische Herausforderungen der CMT-Prozesse
Abbildung 2: CMT-Schweißprozess
(1) Werkstoffeigenschaften und Schweißfehlerkontrolle
a. Porositätsempfindlichkeit beim Schweißen von Aluminiumlegierungen
Aluminiumlegierungsträger (z. B. 6061, 6063) neigen aufgrund schneller Erstarrung und veränderter Wasserstofflöslichkeit zur Porosität. Die Zusammensetzung des Schutzgases ist entscheidend: Reines Argon führt zu einer Porosität von ca. 5 %, während Ar + 30 % He die Porosität auf ≤ 0,5 % reduziert. Die Anpassung der Induktivität (z. B. negative Abstimmung) optimiert den Schmelzbadfluss und minimiert die Porengröße.
b. Heißrissbildung und Zusammensetzungsentmischung
Entmischung von Mg, Si usw. in Aluminiumlegierungen kann zu Korngrenzenversprödung führen. Während die geringe Wärmezufuhr von CMT die WEZ reduziert, ist eine präzise Steuerung der Schweißgeschwindigkeit und des Drahtvorschubs erforderlich, um unzureichende Einbrandtiefe oder lokale Überhitzung zu vermeiden.
c. Metallurgische Verträglichkeit beim Schweißen ungleichartiger Werkstoffe
Schnittstellen in Al-Stahl- oder Al-Verbundverbindungen (z. B. in Querträgern und Gehäusen) müssen die Einwirkung spröder Phasen (z. B. FeAl₃) und Zinkdampf verhindern.
(2) Herausforderungen bei der Prozessparameteroptimierung
a. Abstimmung von Einbrandtiefe und Wärmeeintrag
Schweißnähte müssen die T/CWAN 0027-Norm für die Einbrandtiefe (≥ 0,8 mm) erfüllen. Der geringe Wärmeeintrag von CMT kann zu unzureichender Einbrandtiefe führen, sodass eine Anpassung der Lichtbogenlänge oder gepulster Strom zur Verbesserung der Einbrandtiefe erforderlich ist.
b. Kompromiss zwischen Geschwindigkeit und Stabilität
Automatisierte Linien erfordern Geschwindigkeiten von ≥ 1,2 m/min. Hohe Geschwindigkeiten bergen jedoch das Risiko einer Lichtbogeninstabilität oder eines ungleichmäßigen Tropfenübergangs.
c. Spaltüberbrückung bei komplexen Schweißnähten
Schalen weisen häufig große Spalte (0,5–1,5 mm) oder unregelmäßige Verbindungen (z. B. T-Verbindungen) auf.
(3) Kompatibilität von Konstruktionsdesign und Fertigungsprozess
a. Kontrolle der Verformung beim Dünnblechschweißen
Die Wandstärke von Aluminiumlegierungspaletten beträgt üblicherweise 2–3 mm. Die Verformung beim herkömmlichen MAG-Schweißen kann bis zu 1,2 mm betragen, während das CMT-Schweißen die Verformung durch geringen Wärmeeintrag auf unter 0,3 mm reduzieren kann. Um die Genauigkeit weiter zu verbessern, ist jedoch die Kombination mit verformungssicheren Werkzeugen und robotersymmetrischem Schweißen (Doppelstation) erforderlich.
b. Kontinuität und Abdichtung langer Schweißnähte
Die Länge der versiegelten Schweißnaht des Batterieträgers kann mehrere Meter betragen, Lichtbogenbrüche oder Schwankungen des Schmelzbades müssen vermieden werden. Die CMT-Technologie gewährleistet die Gleichmäßigkeit der Schweißnaht durch mehr als 70 Lichtbogenneuzündungen pro Sekunde, und die Luftdichtheitsquote kann durch das Laser-Tracking-System auf 99 % erhöht werden.
c. Synergie von Multiprozess-Verbundwerkstoffanwendungen
Hochwertige Paletten nutzen häufig das CMT+FSW-Verbundverfahren (Reibrührschweißen): CMT wird für komplexe Strukturen (wie die Verbindung zwischen Rahmen und Bodenplatte) eingesetzt. FSW wird in hochbelasteten Bereichen (wie Längsträgern) zur Verbesserung der Festigkeit eingesetzt. Die Abstimmung der Verbindungsparameter beider Verfahren (wie Vorwärmtemperatur und Wärmebehandlung nach dem Schweißen) muss gelöst werden.
3-Typische Anwendungsszenarien des CMT-Verfahrens in der Batterieträgerherstellung
(1) Verbindung der Hauptstruktur des Batterieträgers
a. Rahmen- und Bodenplattenschweißen
Das CMT-Verfahren wird häufig für die Verbindung von Rahmen und Bodenplatte von Batterieträgern aus Aluminiumlegierungen eingesetzt, insbesondere für lange Schweißnähte und dünne Platten (2–3 mm Dicke).
b. Verbindung zwischen Träger und Bodenplatte
Bei der Konstruktion von CTP-Batterieträgern wird das CMT-Verfahren aufgrund der reduzierten Trägeranzahl und der komplexen Struktur für folgende Zwecke eingesetzt: Hochpräzises Positionsschweißen: Die lokale Verbindung zwischen Träger und Bodenplatte (z. B. T-Stoß) muss eine unzureichende Eindringtiefe vermeiden. CMT erreicht eine stabile Eindringtiefe ≥ 0,8 mm durch digitale Lichtbogenlängenregelung (z. B. Fonis CMT Advanced-Technologie). Anpassung an verschiedene Materialien: Wenn der Träger aus einer Aluminium-Magnesium-Legierung (z. B. 6061) und die Bodenplatte aus hochfestem Aluminium besteht, kann CMT Poren durch Ar-He-Mischgasschutz reduzieren und gleichzeitig die unterschiedlichen Wärmeleitfähigkeiten verschiedener Materialien berücksichtigen.
(2) Schweißen dünner Bleche und komplexer geometrischer Strukturen
a. Schweißen dünnwandiger Aluminiumlegierungen (2–3 mm)
Der Bedarf an leichten Batteriewannen fördert den Einsatz dünner Bleche. Traditionelles MIG-Schweißen neigt jedoch zu Verformungen. Die Vorteile des CMT-Verfahrens sind:
b. Schweißen ultradünner Bleche: Taixiang Automation nutzt die CMT-Technologie, um spritzerfreies Schweißen von 0,3 mm dünnen Blechen für die Kantenversiegelung von Batteriewannen zu erreichen.
c. Überbrücken von Schweißnähten mit Sonderformen: Bei speziell geformten Strukturen wie inneren Verstärkungsrippen und Antikollisionsträgern der Wanne kann der CMT-Spaltüberbrückungsmodus den 0,5–1,5 mm breiten Spalt durch Drahtrückzug und Lichtbogenumlenkung schließen, um nicht verschmolzene Defekte zu vermeiden.
d. Schweißnähte mit hohen Dichtheitsanforderungen: Die Abdichtung der Batteriewanne steht in direktem Zusammenhang mit der Batteriesicherheit. Das CMT-Verfahren gewährleistet dies auf folgende Weise:
· Kontinuierliche, lange Schweißnähte: Durch den Einsatz von mehr als 70 Lichtbogen-Neuzündungszyklen pro Sekunde (z. B. der Fronius LaserHybrid-Technologie) wird die Kontinuität von mehreren Metern Schweißnähten mit einer Dichtheitsquote von 99 % gewährleistet.
· Geringe Wärmezufuhr: Im Vergleich zum Laserschweißen weist CMT eine geringere Wärmezufuhr auf, wodurch die thermischen Auswirkungen von Schmelzbadschwankungen auf die Dichtschicht reduziert werden und es sich für den Klebebeschichtungsprozess eignet.
(3) Szenario der Herstellung von Verbundwerkstoffen mit mehreren Prozessen
a. CMT+FSW-Verbundwerkstoff
In Produktionslinien für hochwertige Batterieträger wird CMT häufig mit Rührreibschweißen (FSW) kombiniert:
Arbeitsteilung und Zusammenarbeit: CMT wird für das flexible Schweißen komplexer Strukturen (wie Rahmen und speziell geformte Verbindungen) eingesetzt, FSW für hochbelastete Bereiche (wie Längsträger), um die Festigkeit zu verbessern. Beispielsweise nutzt die automatisierte Produktionslinie von Shanghai Weisheng eine Kombination aus CMT+FSW+CNC, um die Produktionseffizienz der Träger um 30 % zu steigern.
Optimierung der Prozessanbindung: Die Produktionslinie von Huashu Jinming ist modular aufgebaut und erreicht durch die Anpassung der Vorwärmparameter (z. B. lokales Erhitzen auf 150 °C nach dem CMT-Schweißen) eine nahtlose Verbindung mit FSW.
b. Kombiniert mit FDS/SPR-Niettechnologie
In der CTP-Technologie der zweiten Generation wird CMT mit der Friktions-Selbstspann- (FDS) und Stanzniettechnologie (SPR) kombiniert: Hybride Verbindungslösung: Beispielsweise werden die tragenden Bereiche des Rahmens und der Bodenplatte mittels FSW-Verfahren hergestellt, während abnehmbare Teile (wie Wasserkühlplatten und Isolierschichten) durch CMT-Schweißen vorpositioniert und anschließend durch FDS-Nieten fixiert werden. Dabei werden sowohl Festigkeit als auch Wartungsfreundlichkeit berücksichtigt.
Wir werden regelmäßig Informationen und Technologien zu Wärmedesign und Leichtbau aktualisieren und mit Ihnen teilen. Vielen Dank für Ihr Interesse an Walmate.