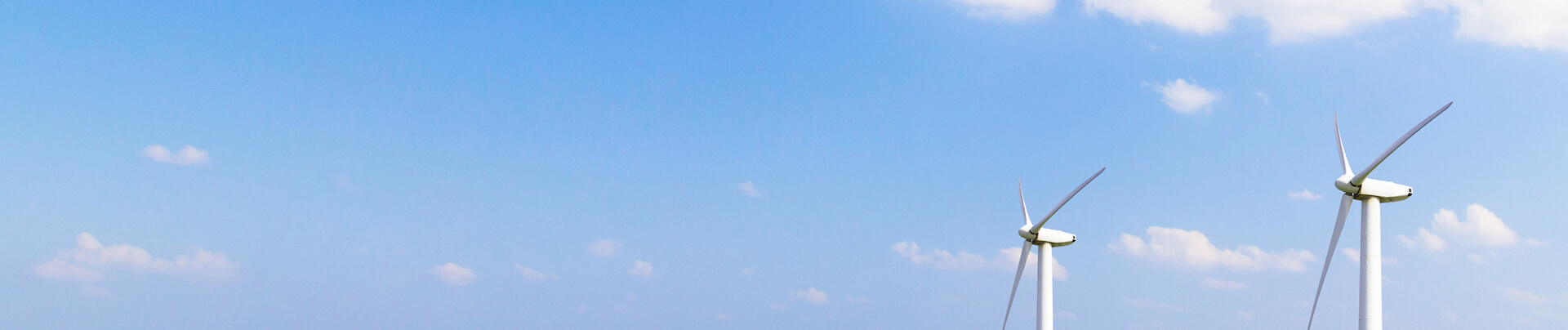
Austausch und Teilen fördern Wachstum,
Zusammenarbeit führt zu gemeinsamer Entwicklung.
Die beliebtesten Wasserblöcke sind grundsätzlich Mikrokanal-Wasserblöcke aus reinem Kupfer. Die Kupferbodenplatte wird direkt mit Schälen bearbeitet und die Lamellen sind in die Bodenplatte integriert, um den Wärmewiderstand zu verringern. Die Bodenplatte und die Deckplatte werden gelötet oder diffundiert, um die Zuverlässigkeit der Abdichtung zu gewährleisten.
Teil 3: Die Hauptkostenstruktur von Wasserblöcken, die im Schälverfahren hergestellt werden
1- Vorteile des Schälprozesses zur Herstellung von Wasserkühlerblöcken
l Integriertes Design: Der Schälprozess kann Boden und Lamellen integrieren, was hilfreich ist, um den thermischen Kontaktwiderstand zu verringern und die Wärmeleitfähigkeit zu verbessern. Darüber hinaus kann das integrierte Design von Bodenplatte und Lamellen auch die strukturelle Festigkeit verbessern.
l Hochpräzise Verarbeitung: Der Schälprozess kann eine sehr feine Zahnstruktur erzeugen, und Zahnhöhe, Zahndicke und Zahnteilung können präzise gesteuert werden, wodurch die Kühlrippen dichter, die Wärmeableitungsfläche größer und die Wärmeableitung effizienter wird. Gleichzeitig können auch die individuellen Anforderungen verschiedener Kunden hinsichtlich Form, Größe usw. besser erfüllt werden.
l Die Produktionseffizienz ist hoch und der Schälprozess kann in Massenproduktion hergestellt werden. Im Vergleich zu herkömmlicher CNC kann der Schälprozess mehrere Zahnradteile gleichzeitig verarbeiten, was die Produktionseffizienz erheblich verbessert.
Abbildung 1: Wasserblockbasis mit verschiedenen Verarbeitungstechnologien a-Skiving b-CNC c-Kaltschmieden
2- Kostenstruktur des Skiving-Wasserblocks
l Entwicklungs- und Herstellungskosten: Die Designkomplexität des Skiving-Wasserblocks ist relativ hoch, insbesondere wenn hohe Anforderungen an die Wärmeabfuhrleistung gestellt werden, was eine komplexe Prozessgestaltung und -optimierung erfordert.
l Materialkosten: Die im Skiving-Prozess verwendeten Materialien sind hauptsächlich Aluminium und Kupferlegierung. Das Design, das Aluminiumplatten und Kupferlegierungen kombiniert, ist in der Radiatorherstellung gängiger und bietet ein besseres Kosten-Nutzen-Verhältnis, sodass die Qualität von Aluminium und Kupfer die Kosten direkt beeinflusst.
l Bearbeitungskosten:
Kosten des Zahnradschneideprozesses: Beim Zahnradschneideprozess kommen hochpräzise CNC-Bearbeitungsmaschinen zum Einsatz, beispielsweise dreiachsige CNC-Werkzeugmaschinen. Der Einsatz derartiger Geräte erfordert hohe Investitionskosten und stellt zudem hohe technische Anforderungen an die Bediener, was die Produktionskosten erhöht.
Kosten des Schweißprozesses: Im Fertigungsprozess von Wasserblöcken ist der Schweißprozess ebenfalls ein wichtiger Kostenfaktor. Vakuumlöten und Diffusionsschweißen sind zwei gebräuchliche Schweißmethoden. Das Löten kann mehrere Verbindungen gleichzeitig herstellen, hat eine hohe Produktions-effizienz, erfordert Lötmaterialien, hat hohe Anforderungen an die Prozessbedingungen und die Qualitätskontrolle ist schwierig; die Ausrüstung für das Diffusionsschweißen hat eine hohe einmalige Investition, und das Diffusionsschweißen benötigt keine Füllstoffe, hat jedoch hohe Anforderungen an die Oberflächenbearbeitung des Werkstücks.
Kosten der Oberflächenbehandlung: Zu den gängigen Methoden der Oberflächenbehandlung gehören Eloxieren, Beschichten usw. Bei Wasserblöcken aus Aluminiumlegierungen kann das Eloxieren die Oberflächenhärte, Abriebfestigkeit und Korrosionsbeständigkeit verbessern und gleichzeitig die Ästhetik des Produkts erhöhen; Kupferwasserblöcke werden beschichtet, z.B. mit Nickel, um Oxidation und Korrosion des Kupfers zu verhindern und die Lebensdauer und Zuverlässigkeit des Produkts zu erhöhen.
l Sonstige Kosten: Inspektion und Prüfung, Verpackung und Transport usw.
3-Vorschläge zur Kostenoptimierung
l Optimierung des Materialeinsatzes
Wählen Sie das richtige Material: Kupfer hat beispielsweise eine hohe Wärmeleitfähigkeit, eine hohe Stückdichte und einen hohen Stückpreis; Aluminium ist leicht, hat einen niedrigen Stückpreis und eine etwas schlechte Wärmeleitfähigkeit.
Materialeinsatz: Sorgen Sie für einen effizienten Materialeinsatz und reduzieren Sie Materialabfall, indem Sie Materialstärke und -spielraum genau berechnen.
Abbildung 2: Schematische Darstellung der Materialverbrauchsberechnung
l Optimierung von Produktionsprozessen
Formen vereinfachen: Entwerfen Sie einfache Formen, um die Komplexität und Kosten der Formen zu reduzieren.
Reduzieren Sie die Ausschussrate: Reduzieren Sie die Ausschussrate durch präzise Prozesskontrolle und Qualitätskontrolle.
Formen in einem Schritt: Optimieren Sie Prozessabläufe, reduzieren Sie mehrere Verarbeitungsschritte und verbessern Sie die Produktionseffizienz.
Wir werden regelmäßig Informationen und Technologien zu Wärmedesign und Leichtbau aktualisieren und mit Ihnen teilen. Vielen Dank für Ihr Interesse an Walmate.