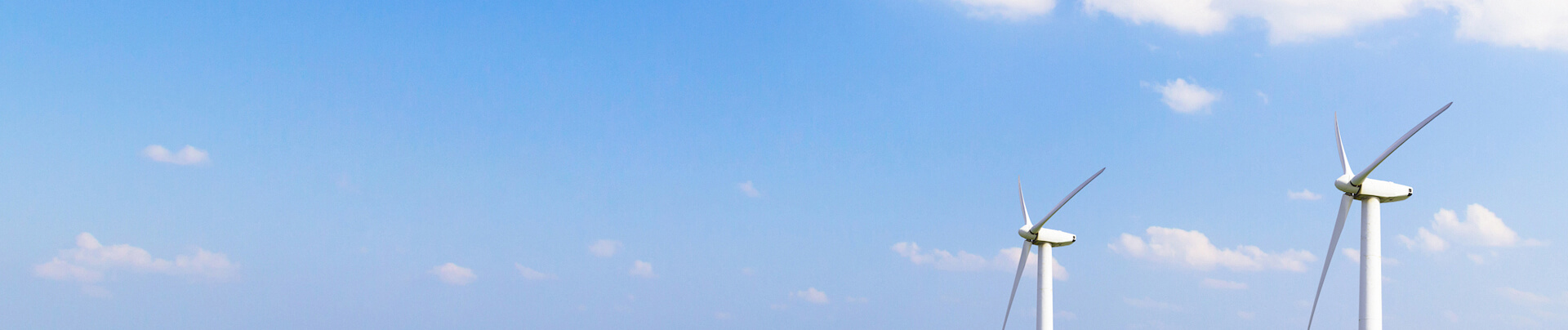
Aluminum Processing Team
Can be manufactured around
the clock, 7 days a week.
Can be manufactured around
the clock, 7 days a week.
Working Condition
0.5C-1C
Layout Location
Bottom liquid cooling
Series Parallel Form
48S/52s
Surface treatment
Sandblasting, Wire Drawing, Painting, Electroplating, Anodizing
Quality Control
full inspection
Application
Commercial and Industrial(C&I)Energy storage for large power plants
OEM
Accept
Key points of FSW(Friction Stir Welding)Cold plate design
1、Flow channel design: Design the cold plate flow channel structure based on manufacturing process, product conditions, thermal resistance distribution, and other factors, including the size of the cold plate, flow channel structure, and inlet and outlet positions.
2、The flow channel design needs to meet the following requirements for friction stir welding process:
Welding structure of cover plate: There are mainly three types of welding structures: overlap, butt overlap, and non planar. The butt overlap is a conventional water-cooled plate welding structure, which has the best welding effect. The overlap step of the cover plate is not less than 1mm to avoid collapse during the welding process.
Cover plate machining allowance: As the surface needs to be milled flat after welding, the thickness of the cover plate generally needs to have CNC machining allowance. The general cover plate thickness is 2-3mm, with an allowance of about 0.5mm, which can meet the pressure within 1 megapascal.
Weld edge margin: There should be a margin of friction stir welding stirring head at the edge of the weld. Generally, for a 3mm cover plate, at least 5mm margin should be left at the edge to avoid edge welding collapse. It is best to communicate with the welding process party before design.