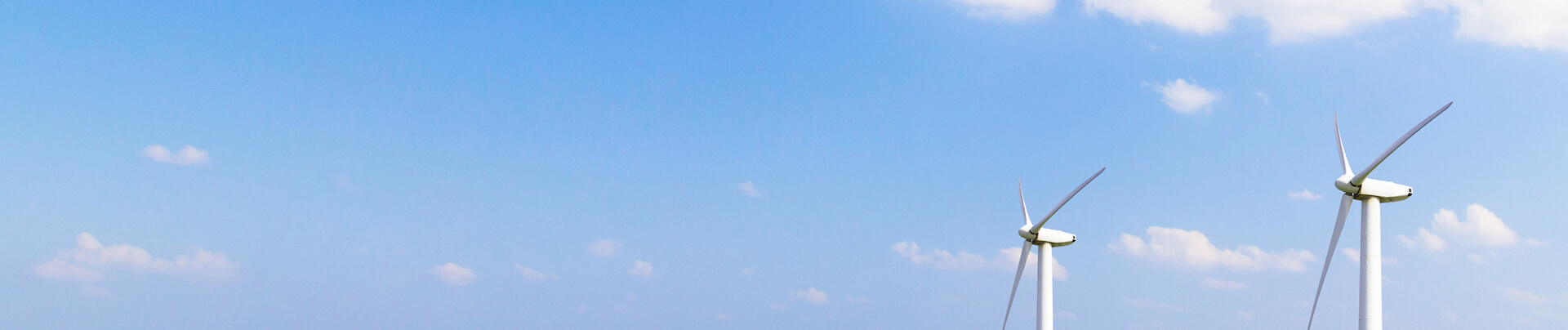
Communication and sharing promote growth
Joining Hands for Development!
The three major focuses of current new energy vehicle development - safety, lightweighting, and reliability - are closely related to the battery pack, and the battery housing is the load-bearing component of the battery system, which has a significant impact on the collision, energy consumption, and other aspects of the battery pack and even the entire vehicle.
Structure of New Energy Vehicle Battery Pack
Safety of battery pack
As the most core component in the three electric systems of new energy vehicles, the battery pack directly affects the main performance indicators of new energy vehicles, and its safety often determines the reliability of the entire vehicle. There are significant safety hazards in the collision of new energy vehicle battery packs. Collision deformation can cause internal battery modules to experience phenomena such as short circuits, open circuits, constant heating, and explosions. The collision resistance performance of the battery pack shell directly affects the safety of the battery module.
The key to battery pack safety design is to reduce the degree of damage to the battery pack during collisions, so optimizing the vehicle collision force transmission path and improving the protective effect of the battery pack shell are the key to design.
The current simulation technology is widely used. By establishing a battery pack simulation model, the failure forms in collision, compression, impact, drop and other working conditions are predicted. The system optimizes the shell structure and component dimensions of the battery pack, and conducts multi-objective optimization of battery pack safety to improve safety.
2、Lightweighting of battery pack
The application of high-strength steel, ultra-high strength steel, aluminum alloys, and composite materials is a necessary link in achieving lightweight of new energy vehicles.
Due to the fact that the upper shell of the battery pack does not provide protection and support, but only serves as a sealing and dust-proof function, the upper shell is mainly made of steel plate, aluminum alloy, and composite materials. The lower shell of the battery pack mainly plays a role in supporting the entire battery mass, resisting external impacts, and protecting the battery module in the battery system.
The mainstream preparation processes for the lower shell of the battery pack include: extruded aluminum profiles+welding forming, stamped aluminum plates+welding forming, and die cast aluminum+casting forming.
Currently, extrusion aluminum profiles+welding forming is a common lower shell manufacturing solution adopted by domestic enterprises. Due to its lower preparation difficulty compared to stamped aluminum lower shells and larger forming dimensions compared to die cast aluminum lower shells.
Battery Tray( Lower shell of battery pack)
Due to the high overlap between the battery pack and chassis of new energy vehicles, the integrated optimization of the chassis and battery pack structure is crucial for the lightweight of new energy vehicles.
CTP technology generally assembles battery cells into modules, which are then installed into the battery pack without the need for intermediate modules. Instead, the battery cells are directly integrated into the battery pack, which is integrated into the vehicle floor as part of the vehicle's structural components. CTP technology effectively improves the space utilization and energy density of battery packs, as well as the overall stiffness of battery packs.
CTC technology is an advanced version of CTP technology, which directly integrates battery cells into the floor frame, uses the battery pack shell as the upper and lower floor panels, and connects the seat directly to the battery pack cover, achieving a space utilization rate of 63%.
CTB technology is an improved version of CTC that retains the crossbeam structure and seat support, with only a portion of the bottom plate replaced by the battery pack cover. The space utilization rate is increased to 66%, and the body structure is more complete, with higher safety.
Battery Packaging Configuration Mode
3. Reliability of battery pack
The entire process of the battery pack shell from service to fatigue failure is: under cyclic loading, fine cracks begin to appear on the surface of the shell, local small fatigue cracks gradually expand, and eventually the instantaneous fracture failure of the parts occurs. Especially, the connection joint of the battery pack housing is a high fatigue failure area. Experimental simulation and optimization of the battery pack casing have become a general approach to improving the reliability design of battery packs.
According to industry requirements, the sealing of the battery pack housing needs to reach IP6K7 level, and even some enterprises need to reach IP6K9K level. Due to the long sealing length of the battery pack casing, usually up to several meters, and the limited sealing design structure, extra attention should be paid to its sealing performance.