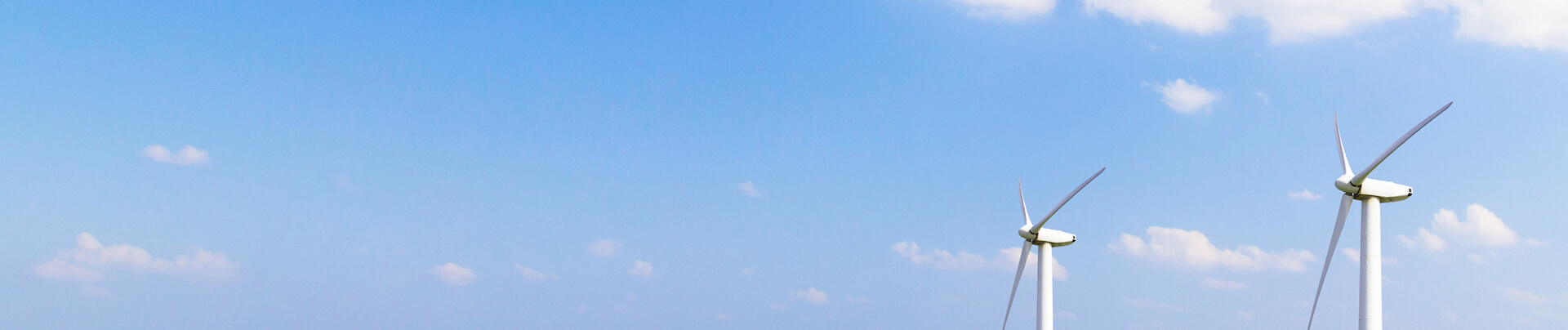
Communication and sharing promote growth
Joining Hands for Development!
The battery storage housing plays a crucial role in energy storage systems, serving essential functions such as load protection, thermal uniformity, electrical installation, and waterproof sealing. With the increasing demands for battery energy density, aluminum alloy materials have become an effective solution to enhance battery system performance due to their higher thermal conductivity and lower density.
The integrated design of flow channels with the housing sidewalls can save welding work in critical load-bearing areas, thereby improving overall structural strength. This design ensures structural safety and stability under various conditions, including static loads, lifting, and random vibrations, while also improving the airtight performance of the housing to some extent. Furthermore, the integrated design helps reduce the number of parts and lower the weight of the housing. Made through extrusion molding, this process has low mold costs, is easy to process, and can be easily modified to meet flexible production needs.
1-Main Types of Aluminum Extruded and Welded Energy Storage Lower Housing
The liquid-cooled lower housing for energy storage typically has a width of 790-810 mm and a height ranging from 40-240 mm, divided into flat and flange types (see below). The length of the liquid-cooled lower housing is related to the capacity of the energy storage product, with common specifications including 48s, 52s, and 104s.
flat tray liquid-cooled lower housing
flanged battery tray liquid-cooled lower housing
2-Structural Form of Aluminum Extruded and Welded Energy Storage Lower Housing
The liquid-cooled lower housing serves as the foundational structure of the entire battery pack, consisting of a bottom plate with flow channels, sealing strips, water nozzles, frames, beams, brackets, and lifting ears, all welded together to form a rectangular frame structure made entirely of aluminum alloy.
Explosive view of the battery lower tray
The liquid-cooled lower housing must possess sufficient load-bearing capacity and structural strength, which imposes high requirements on welding quality, including welding processes, weld grade control, and welder skills, to ensure safety and reliability in actual applications. Liquid cooling technology demands high airtightness for the liquid-cooled housing, including the airtightness of the lower housing and the liquid cooling flow channels. Additionally, the liquid cooling flow channels must withstand the pressure of the coolant flow, necessitating even higher airtightness requirements.
3-Welding Quality Requirements
Generally, the liquid-cooled bottom plate is welded using friction stir welding, and the end caps of the flat liquid-cooled lower housing also employ friction stir welding. Typically, the weld depression for friction stir welding should be ≤0.5 mm, and there should be no detachment or metallic foreign objects that could fall off under vibration conditions.
Liquid cooling flow channels, frames, water nozzles, lifting ears, beams, and accessories are often welded using TIG or CMT welding. Considering the performance requirements of different components, full welding is used for liquid cooling flow channels, frames, water nozzles, and lifting ears, while segment welding is applied to beams and accessories. The flatness of the front and rear battery module beam areas should be <1.5 mm for a single module and <2 mm overall, with frame flatness allowing ±0.5 mm for every additional 500 mm of frame length.
Weld surfaces must be free from defects such as cracks, incomplete penetration, lack of fusion, surface porosity, exposed slag inclusions, and incomplete filling. Generally, the height of the water nozzle weld should be ≤6 mm, and other welds should not extend beyond the lower surface of the housing. The internal welds of the front and rear module beams must not protrude from the inner surface.
The weld penetration must meet relevant standard requirements. For arc-welded joints, the tensile strength should not be less than 60% of the minimum tensile strength of the base material; for laser and friction stir welded joints, the tensile strength should not be less than 70% of the minimum tensile strength of the base material.
Additionally, the welding of the lower housing must meet the airtightness standard of IP67. Therefore, post-welding treatment generally requires the weld slag and seams in the front and rear module beam areas to be ground flat. External welding on the tray should not be ground, and the sealing surfaces at the welds need to be smooth, with no significant height differences from the frame.
Below:Extrusion+FSW battery tray for ESS
We will regularly update you on technologies and information related to thermal design and lightweighting, sharing them for your reference.
Thank you for your attention to Walmate.