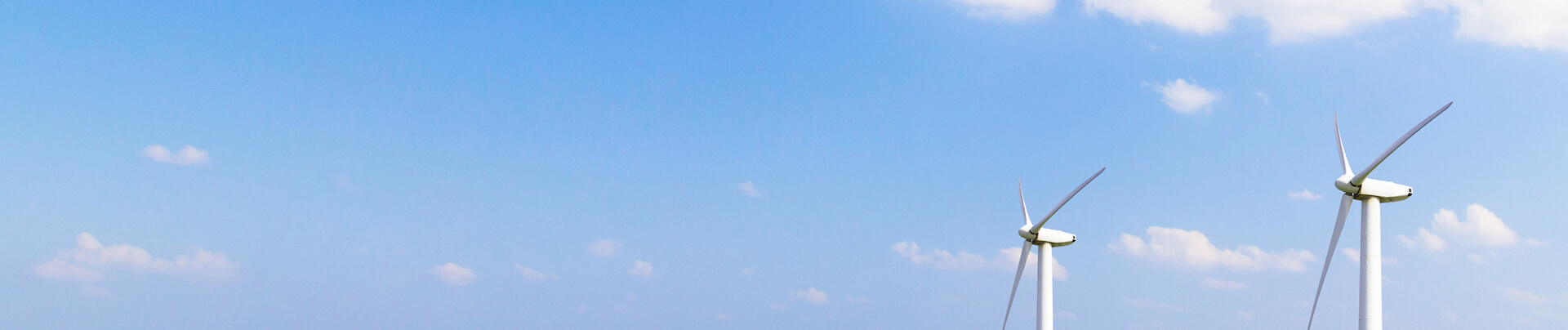
Communication and sharing promote growth
Joining Hands for Development!
In the production process of battery trays and energy storage liquid cold boxes for new energy vehicles, necessary and appropriate surface treatment is a key step, such as: using coating, oxidation treatment, etc. to form a protective layer on the metal surface to resist the erosion of corrosive media; Components that require electrical isolation, such as battery cells, water-cooling plates, module walls, etc., need to establish an insulating protective film. Insulation is generally achieved by spraying insulating powder or insulating paint. Choosing the appropriate surface treatment technology can not only improve the performance of the tray/liquid cooling box Durability and safety can also meet the needs of different application scenarios. This article summarizes common surface treatment technologies for reference.
1-Cleaning and polishing
During the production process, impurities such as processing oil, engine oil residue, powder, and dust may accumulate on the surface of the pallet. Not only do these impurities affect the service life of the battery tray, they may also adversely affect the performance and safety of the battery. Through cleaning and polishing, these impurities can be effectively removed to ensure the cleanliness of the pallet surface. Cleaning and grinding can effectively remove surface impurities, burrs, and welding slag, making the surface smooth and flat, thus improving the overall quality of the battery tray/box.
a.chemical cleaning
Alkali cleaning: Alkaline cleaning mainly uses alkaline solutions (such as sodium hydroxide, sodium carbonate, etc.) to remove grease, dirt and other organic matter on the surface of aluminum alloys. Alkaline washing removes grease through saponification, emulsification and penetration and wetting, and at the same time generates water-soluble precipitates, thereby achieving a cleaning effect. Alkaline cleaning is usually used to remove grease, dust and organic contaminants from the surface of aluminum alloys.
Pickling: Pickling uses acidic solutions (such as nitric acid, hydrochloric acid, etc.) to remove oxide scale, rust and other inorganic deposits on the surface of aluminum alloys. Pickling converts the oxides on the metal surface into soluble salts through the reaction of acid with the oxides on the metal surface, thereby removing surface impurities. Pickling is mainly used to remove oxide film, rust and inorganic salt scale on the surface of aluminum alloys. Pickling is often used for the final treatment of metal surfaces to improve their finish and flatness.
b.Mechanical grinding
During production, the grinding process can remove processing allowances, correct shape errors, ensure the smoothness and accuracy of the pallet/box surface, meet assembly requirements, and thus improve overall performance and service life.
The cleaned and polished surface can be treated with coating materials or other materials, which is very important for the subsequent construction of anti-corrosion, sealing, thermal conductivity, insulation, thermal insulation and other coatings, and plays a key role in the firm attachment of these materials to the pallet/box.
2-Coating and protective film establishment
In addition to basic cleaning and polishing, the production of pallets/boxes uses a spraying process for surface treatment to form a protective layer to prevent oxidation and corrosion and to meet the needs of different scenarios such as thermal insulation, insulation and voltage resistance.
a.Thermal insulation
Anti-condensation and thermal insulation of battery trays can be achieved through comprehensive design of thermal insulation systems, use of high-efficiency thermal insulation materials, application of aerogels, battery pack insulation design, and spraying of foam insulation materials.
Bottom surface sprayed with PVC and foam material
b.Insulation withstand voltage
The insulation of the battery pack casing and the liquid cooling components is primarily to prevent current leakage, protect personnel from electric shocks, and ensure the normal operation of the battery system. Insulation is typically achieved through two main methods: powder spraying and film lamination. The mainstream film lamination processes include room temperature lamination, hot pressing, and UV exposure.
Internal spraying of insulation powder and insulation paint
3-Logos and Signage
A nameplate or label is set in a prominent position on the battery tray, generally through laser, mechanical engraving, etc. These logos are usually made of wear-resistant and corrosion-resistant media to ensure that they are not easily erased during the entire service life.
We will regularly update you on technologies and information related to thermal design and lightweighting, sharing them for your reference.
Thank you for your attention to Walmate.