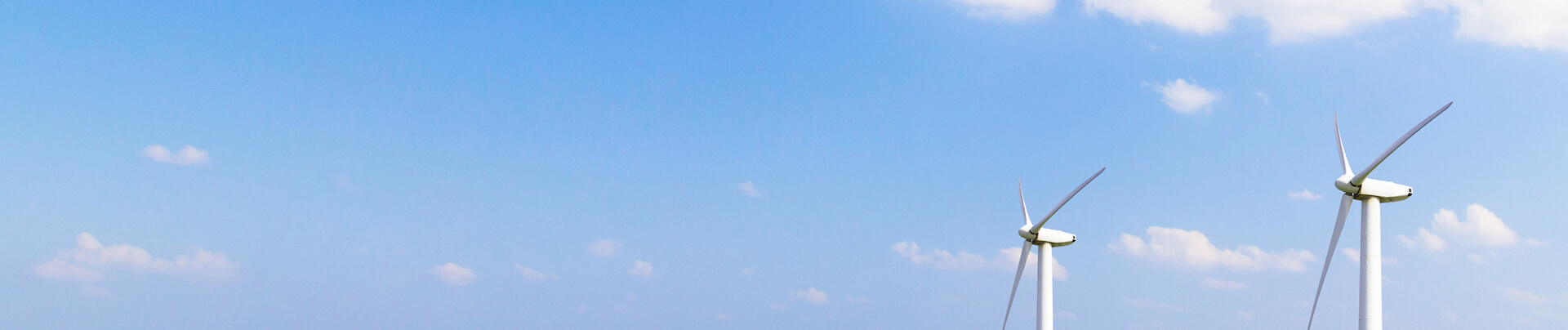
Связи для долгосрочного развития
Рука об руку для общего роста
Будучи инженером-практиком на заводе по производству аккумуляторных поддонов, участвовавшим в нескольких проектах корпусов аккумуляторов для электромобилей, я глубоко осознаю баланс между «легким весом — безопасностью — стоимостью» в отрасли. В этой статье, на основе реальных кейсов, будут проанализированы логика выбора текущих технологических направлений и вызовы индустриализации через три аспекта: материалы, производственные процессы и будущие тренды.
1-Материалы: баланс между легким весом и стоимостью
Выбор материала корпуса напрямую влияет на производительность и экономичность автомобиля. Основные направления: алюминиевые сплавы, высокопрочная сталь и композиты.
a. Алюминиевые сплавы: основа легковесности
Экструдированные профили (BYD): В корпусах аккумуляторов BYD используются профили с оптимизированным сечением для снижения веса и повышения жесткости.
Интегральное литье (Tesla): Технология CTC с аккумулятором 4680 снижает вес на 50%, но требует затрат на пресс-формы свыше 200 млн юаней. Окупаемо только при производстве 500 тыс. единиц в год.
Гибридные материалы (Porsche Taycan): Комбинация алюминия и углеволокна снижает вес на 15%, но увеличивает стоимость на 30%, что приемлемо только для премиум-сегмента.
b. Высокопрочная сталь: выбор бюджетного рынка
Термообработанная сталь (например, 22MnB5) с пределом текучести 1500 МПа применяется в 40% коммерческих авто. Стоимость на 40% ниже алюминия, но плотность энергии снижается на 8%. Популярна в моделях до 100 тыс. юаней.
c. Композиты: эксперименты для премиума
SMC-материалы: Стеклопластик снижает вес на 30%, но требует увеличения толщины (3 мм + 5 мм ребер жесткости) для защиты от ударов.
Углеволокно (BMW i3): На 50% легче алюминия, но стоимость — 800 юаней/кг, что ограничивает применение люксовыми моделями.
Практический вывод: выбор материала зависит от позиционирования авто. Средний сегмент (200–300 тыс. юаней) — алюминий, бюджетный — сталь, премиум — углеволокно.
2-Производственные процессы: баланс эффективности и надежности
a. Литье vs. экструзия
Экструзия (Chevrolet Bolt): Себестоимость ~800 юаней, подходит для массового производства.
Литье под давлением (NIO ET5): Себестоимость 1500 юаней, но скорость производства выше в 5 раз.
Сварка трением (FSW): Деформация на 50% меньше, усталостная прочность +30%, но требует +40% инвестиций в оборудование.
b. Технологии интеграции
CTP (CATL): Утилизация пространства повышается с 72% до 85%, снижение затрат на 15–20%, но требуется усиленная защита от теплового разгона.
CTC (Tesla Model Y): На 370 деталей меньше, запас хода +54%, но ремонт дороже на 300%.
Сравнение ключевых данных
Опыт производства: CTP доминирует благодаря совместимости. CTC требует глубокой интеграции и пока не массово.
3-Будущие тренды: гибридизация и интеллектуализация
a. Гибридные материалы
Алюминий/углеволокно (Porsche Taycan) обеспечивают прочность 800 МПа, но стабильность соединения (требуется >25 МПа) остается проблемой (у Toyota bZ4X выход годных 65%).
b. Интеграция функций
Объединение корпуса и системы охлаждения (GAC): Площадь контакта +50%, перепад температур <5°C, но требуется оптимизация сварки алюминия и меди.
Встроенные датчики (Continental): Скорость реакции BMS +30%, но нужна долговечность сенсоров.
c. Экологичность
Замкнутый цикл переработки алюминия (BMW) снижает выбросы CO₂ на 60%, но потери свойств материала должны быть <10%. Тонкостенное литье (прессы 9000T) требует контроля температуры пресс-форм (±5°C).
[Направления развития:]
Сокращение цикла формования композитов (например, LGF-PP с 180 до 90 секунд).
Цифровые двойники для снижения погрешности моделирования ударов с ±20% до ±5%.
4-Перспективы стратификации рынка и индустриализации
Краткосрочная перспектива (1–3 года): профили из экструдированного алюминия CTP+ по-прежнему являются основными, а CATL продолжает лидировать с долей рынка 34%;
Среднесрочная перспектива (5–10 лет): CTC и углеродное волокно ускоряют свое проникновение на рынок высокого класса, и ожидается, что доля углеродного волокна составит 25% в 2030 году;
Долгосрочная цель: плотность энергии превысит 400 Вт·ч/кг, и в то же время, на основе национального стандарта защиты от теплового разгона в течение 30 минут, еще больше повысится уровень избыточности безопасности.
5-Заключение
Выбор технологии корпуса аккумулятора — это адаптация к сценарию использования. Инженеры должны сочетать инновации с реалиями массового производства, находя баланс между весом, безопасностью и стоимостью. С развитием интеллектуальных и «зеленых» технологий корпуса перейдут от пассивной защиты к активной безопасности, поддерживая переход на электромобили.
Мы будем регулярно обновлять технологии и информацию о тепловых проектах и оптимизации, и делиться этой информацией с вами для справки. Благодарим вас за интерес к компании Walmate.