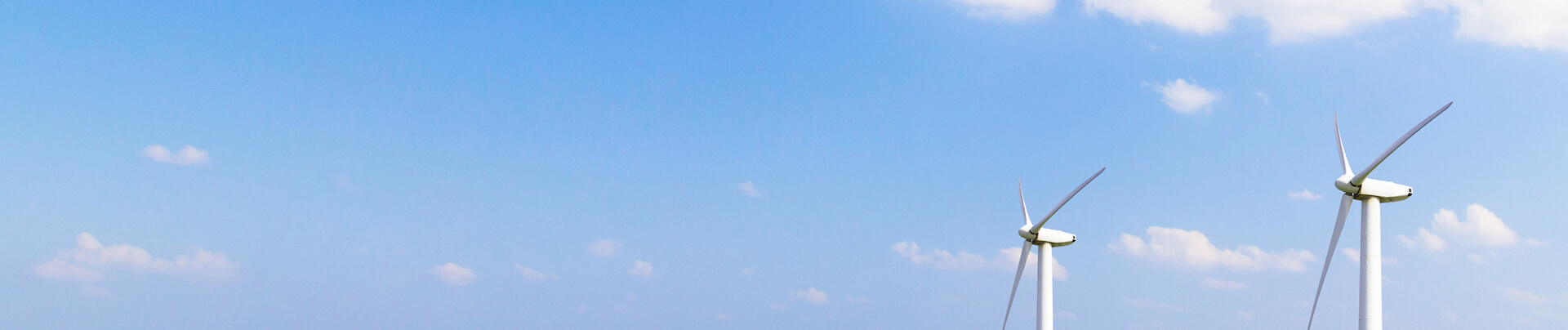
Связи для долгосрочного развития
Рука об руку для общего роста
Технология CTC (Cell-to-Chassis) привлекла большое внимание, поскольку она может значительно улучшить дальность и эффективность использования пространства электромобилей, но может ли она действительно заменить традиционную технологию аккумуляторов, все еще остается спорным вопросом. Основное узкое место на стороне производства — процесс сварки поддона аккумулятора — стало ключом к определению будущего этой технологии: сложная структурная конструкция, совместимость с несколькими материалами и строгие требования к тепловому регулированию подвергли традиционную технологию сварки серьезному испытанию. Начиная с точки зрения передовых инженеров, объединяя отраслевые тенденции и инженерные практики, эта статья анализирует потенциал и ограничения технологии CTC и исследует, как технология сварки стала «пробным камнем» этой технологической революции.
1-«Идеал и реальность» технологии CTC
Технология CTC теоретически может сократить избыточные структурные детали и повысить плотность энергии за счет интеграции аккумуляторной батареи непосредственно в шасси, но осуществимость ее широкомасштабного применения сталкивается с реальными проблемами:
Радикальность и осторожность автомобильных компаний: Tesla, BYD и другие ведущие компании запустили решения CTC, но все больше производителей все еще ждут и наблюдают. Данные отрасли показывают, что по состоянию на февраль 2025 года массовые модели CTC составляют 15–20 % в мире, а традиционная технология CTP (Cell-to-Pack) по-прежнему остается основной.
«Стоимость» улучшенного срока службы батареи: хотя CTC может увеличить плотность энергии на 15–20 %, сложность конструкции шасси приводит к увеличению производственных затрат на 30–50 % (по расчетам консалтингового агентства), а баланс между затратами и выгодами пока не ясен.
Экономические противоречия в обслуживании: Интегрированная конструкция привела к резкому росту затрат на обслуживание батареи. Данные страховых компаний показывают, что частота замены аккумуляторных сборок после аварий моделей CTC достигает 70%, что намного выше, чем 25% традиционных моделей.
Эти противоречия делают будущее технологии CTC полным переменных. Сможет ли рынок преодолеть 20% зависит от трех основных переменных: прогресс массового производства Tesla Cybertruck; заставит ли ценовая война между китайскими автопроизводителями сократить издержки; и степень компромисса европейских правил по ремонтопригодности аккумуляторов. Уровень технологии сварки на производственной стороне будет ключом к определению того, сможет ли он преодолеть разрыв между лабораторным и массовым производством.
2-Три «барьера жизни и смерти» процесса сварки
Для производителей аккумуляторных лотков внедрение технологии CTC должно преодолеть три основные проблемы:
a. Игра между точностью «микронного уровня» и эффективностью
Традиционные сварочные процессы могут допускать ошибки в 0,5 мм, но лотки CTC должны переносить больше батарей, а количество швов увеличивается более чем в 3 раза, и большинство из них распределяется по изогнутым и неровным деталям. Испытания, проведенные производителем, показывают, что когда ошибка позиционирования сварки превышает 0,15 мм, выход годных сборок аккумуляторных элементов резко падает с 99% до 82%. Что еще сложнее, так это то, что повышение точности часто сопровождается снижением эффективности — хотя точность лазерной сварки высока, стоимость оборудования более чем в 5 раз выше, чем у традиционной сварки.
b. «Вода и огонь» смешанных материалов
Чтобы сбалансировать легкость и прочность, лотки CTC часто используют смешанную структуру «алюминиевый сплав + углеродное волокно + специальная сталь». Разница в коэффициентах теплового расширения различных материалов может достигать 20 раз (например, алюминий 23 мкм/м·К против углеродного волокна 0,8 мкм/м·К), что легко может привести к возникновению внутреннего напряжения во время сварки и вызвать трещины. Когда компания попыталась соединить алюминий и углеродное волокно, скорость образования трещин в сварном шве достигла 18%, что намного превышает приемлемый для отрасли порог в 3%.
c. «Невидимый убийца» зоны термического влияния
Высокая температура сварки может повредить изоляционные материалы или цепи датчиков вокруг элемента аккумулятора. Однажды автомобильная компания увеличила скорость саморазряда модуля аккумулятора на 50% из-за неправильного контроля подводимого тепла при сварке. Инженеры должны контролировать колебания температуры сварки в пределах ±15℃ в течение 0,1 секунды — это эквивалентно установке «высокоточного температурного тормоза» на сварочный пистолет.
3-Выход: нет серебряной пули, есть только системные инновации
Столкнувшись с этими проблемами, отрасль изучает три прорывных пути:
a. «Коктейльная терапия» комбинирования процессов
Гибридная лазерная дуговая сварка: сочетание точности лазерной сварки с преимуществами проплавления дуговой сварки, скорость сварки алюминиевого сплава увеличивается на 40%;
Технология холодного перехода металла (CMT): благодаря точному контролю подводимого тепла площадь зоны термического влияния уменьшается на 60%;
Интеллектуальная система компенсации робота: автоматически регулирует траекторию сварочного пистолета на основе данных сканирования сварного шва в реальном времени и увеличивает квалифицированную скорость сварки сложных криволинейных поверхностей с 75% до 95%.
b. «Предварительный компромисс» со стороны материала
Некоторые компании начали совместно разрабатывать «сварочные» композитные материалы с поставщиками материалов. Например, чувствительность к трещинам при сварке отечественного модифицированного алюминиевого сплава (материал из алюминиевого сплава, отрегулированный физическими, химическими или технологическими средствами) была снижена с уровня 7 до уровня 3 (согласно стандартам ISO). Хотя это и снижает 5% эффекта легкости, это увеличивает выход сварки до 98%.
c. «Цифровой двойник» в измерении обнаружения
Собирая все данные о процессе сварки (ток, температура, скорость и т. д.) в сочетании с моделями ИИ для прогнозирования вероятности дефектов. После того, как завод внедрил эту технологию, онлайн-уровень обнаружения дефектов сварки увеличился с 80% до 97%, а стоимость лома снизилась на 45%.
4-Новое предложение инженеров: поиск определенности в неопределенности
a. Споры по поводу технологии CTC по сути являются игрой между «системной оптимизацией» и «локальными ограничениями»:
Если прорывная скорость процесса сварки медленнее, чем ожидания автомобильных компаний по снижению затрат, CTC может стать нишевой технологией;
Если материалы, процессы и технологии испытаний совершат прорыв скоординированным образом, ожидается, что это откроет новую эру проектирования конструкций электромобилей.
b. Инженерам необходимо реконструировать возможности из двух измерений:
Интеграция междоменных знаний: понимание порога чувствительности электрохимических свойств к подводимому теплу сварки;
Способность гибкого реагирования: исследование случая европейского поставщика показывает, что команда, которая может завершить оптимизацию параметров сварки новых сплавов в течение недели, имеет в 3 раза больше вероятности получения заказов.
Технология CTC находится на перекрестке «подрывных инноваций» и «ловушки массового производства». Возможно, это не полностью заменит существующие технологии, но это заставляет процесс сварки развиваться в сторону более высокой точности, более сильной совместимости и более интеллектуального управления. В этом технологическом марафоне настоящим победителем может оказаться не самая первая автомобильная компания, а команда инженеров, которая превращает «невозможные сварные швы» в «стандартизированные интерфейсы» на производственной стороне.
Мы будем регулярно обновлять технологии и информацию о тепловых проектах и оптимизации, и делиться этой информацией с вами для справки. Благодарим вас за интерес к компании Walmate.