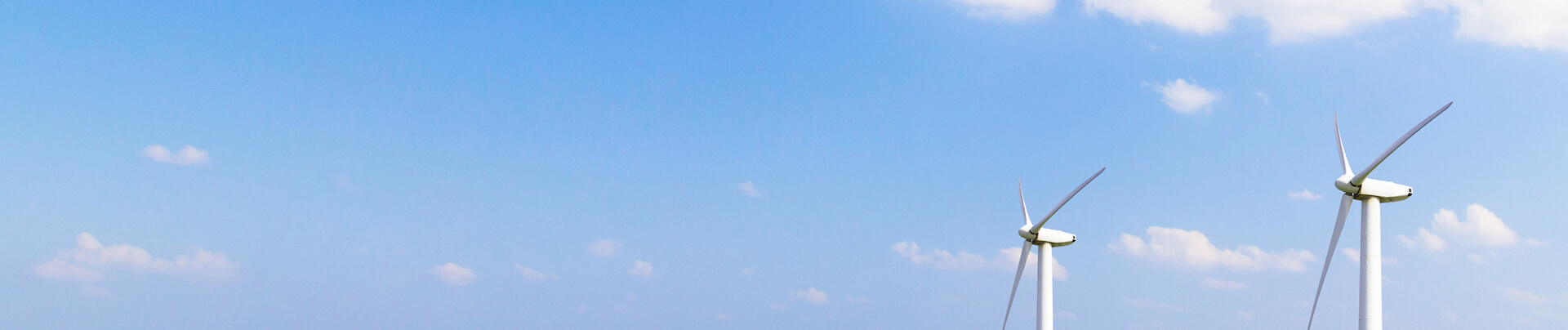
교류와 나눔은 성장을 촉진하고
공동 발전을 위해 협력합니다
CTP(Cell to Pack) 기술이 기존 배터리 팩 구조를 완전히 전복함에 따라 배터리 트레이의 "역할"은 수동적 하중 지지에서 능동적 통합으로 전환되었습니다. 용접 기술은 안전과 성능의 핵심이 되었습니다. 경량(벽 두께는 1.5mm에 불과함), 제로 기공 밀봉, 다중 재료(알루미늄/구리/탄소 섬유) 통합에 대한 요구 사항으로 인해 기존 용접은 변형과 결함의 딜레마에 빠졌습니다. 이 산업은 재료 혁신, 지능형 품질 검사 및 프로세스 반복을 통해 획기적인 진전을 이루고 있습니다. 이 기사에서는 CTP가 용접에 미치는 파괴적 과제를 분석하고 고정밀 및 고신뢰성을 향한 기술적 경로를 탐구합니다.
1- CTP 기술로 인한 배터리 트레이의 구조적 설계 요구 사항의 변화 분석
CTP(Cell to Pack) 기술은 기존 배터리 팩의 모듈 구조를 제거하여 배터리 셀을 배터리 팩에 직접 통합합니다. 이 기술 혁신은 배터리 트레이의 구조적 설계에 대한 전면적이고 다차원적인 업그레이드 요구 사항을 제시합니다. 다음은 재료, 성능, 공정, 통합 등의 관점에서 본 구체적인 분석입니다.
(1) 구조적 강도 및 내충격 성능의 포괄적 개선
a. 모듈 제거 후 기계적 베어링 요구 사항:
CTP 기술이 모듈 구조를 제거한 후 배터리 트레이는 배터리 셀의 지지, 고정 및 외력 완충 기능을 직접 견뎌야 합니다. 기존 모듈은 기계적 하중을 분산하는 반면, CTP 트레이는 충전 및 방전 중에 배터리 셀의 팽창 변형을 전체적으로 흡수해야 하며(예: 정사각형 배터리 셀의 팽창력은 10-20kN에 도달할 수 있음) 차량 주행 중 진동, 압출 및 충격 하중을 견뎌야 합니다.
b. 재료 및 구조 최적화 방향
· 고강도 알루미늄 합금의 우세: 초기 강철은 무거운 무게로 인해 점차 대체되었고 6061-T6가 주류가 되었습니다. 높은 비강도와 강한 내식성을 가지고 있어 경량과 고강성의 이중 요구 사항을 충족할 수 있습니다.
· 복합 구조 설계: 예를 들어, Leapmotor의 "더블 프레임 링 빔" 구조는 세로 및 가로 빔 구획을 통해 국부 충격 저항성을 향상시키는 동시에 압출 기술을 사용하여 재료 분배를 최적화하고 불필요한 무게를 줄입니다.
· 마그네슘-알루미늄 합금 및 탄소 섬유 탐색: 마그네슘-알루미늄 합금은 기존 알루미늄 재료보다 30% 가볍고 탄소 섬유 복합 재료는 고강도와 경량 특성을 모두 가지고 있지만 현재는 비용과 공정 성숙도로 인해 고급 모델에만 사용됩니다.
(2) 통합 기밀성 및 열 관리 요구 사항
a. 밀봉 성능 업그레이드
모듈을 제거한 후 배터리 팩의 내부 냉각수 순환 및 가스 밀봉은 트레이에 완전히 의존하며 용접 결함(기공 및 균열 등)으로 인해 누출 위험이 발생할 수 있습니다.
그림 1-배터리 트레이 기밀성 테스트
b. 열 관리 기능 통합
CTP 트레이는 액체 냉각판 및 열 전도성 접착제와 같은 구성 요소를 통합해야 합니다. 예를 들어, 구조용 접착제는 배터리 셀을 고정하고 팽창 응력을 전달하는 데 사용되고, 폴리우레탄 열 전도성 접착제(열 전도도 > 1.5 W/m·K)는 배터리 셀 간 및 액체 냉각 튜브와의 열 전도에 사용됩니다. 단일 PACK에 사용되는 접착제의 양은 기존 구조보다 50% 이상 높습니다. 트레이 내부에 흐름 채널을 설계하여 용접의 열 영향 구역으로 인해 발생하는 밀봉 손상을 방지하면서 냉각 효율을 최적화해야 합니다.
(3) 경량화 및 소재 혁신
a. 소재 선택 추세
알루미늄 합금 압출 및 다이캐스팅 공정: 압출 알루미늄 프로파일은 프레임 구조(예: 테슬라의 4680 배터리 트레이)에 사용되고 다이캐스팅 공정(예: 통합 다이캐스팅)은 용접 공정을 단순화하고 무게를 15%-20% 줄입니다.
플라스틱 복합소재 적용: 예를 들어, 유리섬유 강화 PA6 소재는 비하중부하 부품에 사용되어 무게를 더욱 줄이지만, 금속 연결 인터페이스와의 호환성 문제를 해결해야 합니다.
b. 경량 설계 전략
토폴로지 최적화: CAE 시뮬레이션을 통해 중복 소재를 줄이고 강도를 보장하면서 트레이의 무게를 줄입니다.
얇은 벽과 통합: 트레이의 벽 두께를 3mm에서 1.5-2mm로 줄이고 BMS 브래킷 및 배선 하네스 채널과 같은 기능 구성 요소를 통합하여 부품 수를 줄입니다.
(4) 통합 및 모듈형 설계
a. 기능 구성 요소의 높은 통합
CTP 트레이는 배터리 관리 시스템(BMS), 고전압 커넥터, 내화 절연 층과 같은 모듈을 통합해야 합니다.
b. 모듈형 및 호환 설계
용접 생산 라인은 여러 모델의 트레이를 혼합 생산할 수 있어야 하며, "한 번의 클릭으로 유형 변경"을 달성할 수 있어야 하며, 다양한 배터리 셀 크기(예: 정사각형 및 원통형)의 트레이 구조와 호환되어야 합니다.
2- CTP 기술 혁신의 용접 공정에 대한 구체적인 과제
CTP(Cell to Pack) 기술은 공간 활용도와 에너지 밀도를 크게 개선했지만 용접 공정에 전례 없는 과제를 안겨주었습니다.
(1) 용접 결함을 제어하는 데 어려움이 급격히 증가했습니다.
a. 다공성 및 밀봉 과제
CTP 기술이 모듈을 제거한 후 배터리 트레이가 직접 밀봉 기능을 수행해야 합니다. 용접 기공(알루미늄 합금 용접에서 일반적인 결함)은 냉각수 누출 또는 가스 침투 위험으로 직접 이어집니다.
b. 균열 및 재료 호환성
고아연 알루미늄 합금(예: 7 시리즈)은 용접 중 열 응력으로 인해 균열이 발생하기 쉽습니다.
c. 갭 및 조립 오류
여러 셀을 직접 통합하면 트레이 구조의 접합 지점 수가 증가합니다. 조립 오류가 누적되면 용접 갭이 ±1mm를 초과할 수 있습니다.
(2) 재료 시스템 업그레이드로 인한 공정 적응 문제
a. 경량 소재의 용접 과제
CTP 트레이 소재는 강철에서 알루미늄 합금(6061-T6, 7075-T6), 마그네슘-알루미늄 합금(30% 중량 감소) 및 탄소 섬유 복합 소재로 전환되었습니다. 알루미늄 합금 용접은 산화막의 어려운 용융과 높은 열전도도로 인한 불충분한 침투 문제를 해결해야 합니다.
b. 이종 소재 연결 기술
트레이가 액체 냉각판(구리/알루미늄) 및 내화층(세라믹 매트릭스 복합 소재)과 같은 기능적 구성 요소를 통합하는 경우, 취성 금속간 화합물이 이종 소재의 계면에 나타나기 쉽습니다.
(3) 업그레이드된 구조적 복잡성 및 정밀 요구 사항
a. 대형 박벽 구조의 변형 제어
CTP 트레이의 벽 두께는 3mm에서 1.5-2mm로 감소하고 용접 열 변형의 민감성이 급격히 증가합니다.
b. 고밀도 솔더 접합 및 공정 효율성
단일 트레이의 솔더 접합 수는 기존 모듈의 2,000개에서 5,000개 이상으로 증가했습니다.
그림 2- 배터리 트레이 용접
3- 생산 공정 및 품질 관리 업그레이드
CTP 기술은 배터리 트레이 용접을 "단일 공정"에서 "다중 기술 협업, 지능화, 녹색화"로 전환하는 것을 촉진합니다. 제조업체는 세 가지 주요 방향에 집중해야 합니다.
기술 업그레이드: 기공 및 균열과 같은 결함 제어를 돌파하고 경량 소재에 적응합니다.
지능형 전환: 전체 공정 디지털화 및 AI 품질 검사를 통해 고정밀 생산을 달성합니다.
생태적 협업: 자재 공급업체, 장비 공급업체 및 OEM과 함께 기술 표준을 공동으로 구축합니다.
당사는 열설계와 경량화에 관한 기술과 정보를 정기적으로 업데이트하여 참고할 수 있도록 공유해 드리겠습니다
Walmate에 관심을 가져주셔서 대단히 감사합니다