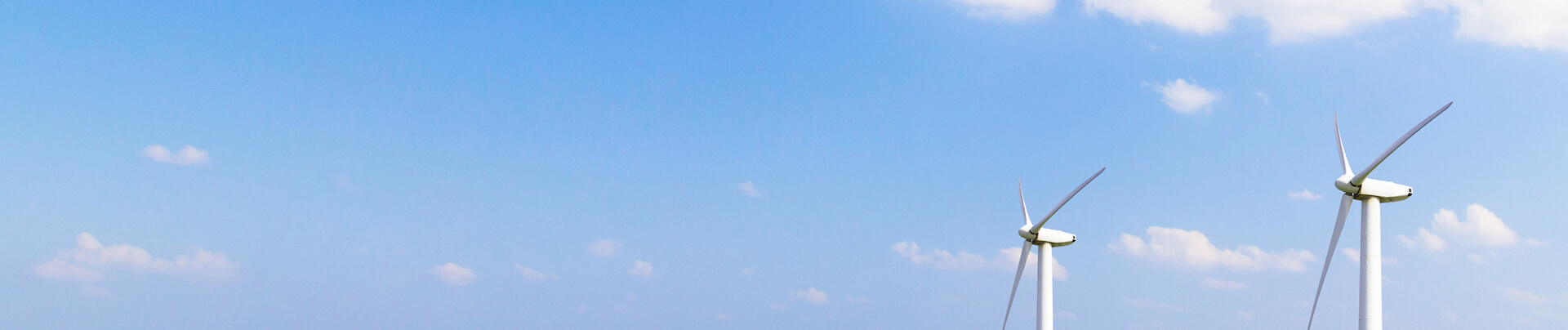
교류와 나눔은 성장을 촉진하고
공동 발전을 위해 협력합니다
배터리 트레이 제조업체의 일선 엔지니어로서 저는 여러 신에너지 자동차 배터리 셸 프로젝트에 참여했으며 "경량-안전-비용"의 삼각형 관계에서 산업의 게임에 대해 깊이 이해하고 있습니다. 이 글에서는 현재 기술 경로의 선택 논리와 산업화 과제를 재료 경로, 제조 공정 및 미래 추세의 세 가지 차원에서 분석하고 실제 사례를 결합합니다.
1-소재 경로: 경량과 비용 간의 균형
배터리 셸 소재의 선택은 전체 차량의 성능과 경제성에 직접적인 영향을 미칩니다. 현재 주류 경로는 알루미늄 합금, 고강도 강철 및 복합 재료의 세 가지 범주로 요약할 수 있으며 각각 적용 가능한 시나리오가 있습니다.
a. 알루미늄 합금 경로: 경량의 주요 힘
· 압출 알루미늄 프로파일: BYD의 많은 모델의 배터리 셸은 압출 알루미늄 프로파일로 만들어져 단면 형상을 최적화하고 구조적 강성을 개선하여 중량을 줄였습니다.
· 다이캐스팅 통합: 테슬라의 4680 배터리는 CTC 기술과 결합하여 중량을 50% 이상 줄였지만 금형 비용은 2억 위안을 초과하고 비용을 희석하려면 연간 50만 개 이상의 생산이 필요하므로 주요 자동차 회사의 대량 생산에 적합합니다.
· 복합 알루미늄: 포르쉐 타이칸은 알루미늄-탄소 섬유 하이브리드 구조를 채택하여 무게를 15% 더 줄였지만 비용은 30% 증가하여 고급 모델에 국한되었습니다.
b. 고강도 강철 경로: 비용에 민감한 시장에서의 반격
열간 성형 강철(예: 22MnB5)은 항복 강도가 1500MPa이고 상용차에서 침투율이 40% 이상이며 단일 GWh 비용은 알루미늄보다 40% 낮지만 에너지 밀도는 약 8% 희생됩니다. 따라서 고강도 강철은 일반적으로 비용과 기본 안전을 모두 고려하여 10만 위안 미만의 모델에 사용됩니다.
c. 복합 재료: 고급의 시도
· SMC 재료: 배터리 팩의 상단 셸은 강철보다 30% 가벼운 유리 섬유 강화 복합 재료를 사용하지만 충격 저항 단점은 두께를 늘려(3mm+5mm 보강) 보상해야 합니다.
· 탄소섬유: BMW i3의 셸은 알루미늄보다 50% 가볍지만, 비용은 kg당 800위안으로 높고 대량 생산이 어렵습니다. 현재는 고급 모델에만 사용됩니다.
실무 요약: 소재 선택은 모델 포지셔닝과 일치해야 합니다. 중간 시장(200,000-300,000위안)은 주로 알루미늄 기반 소재이고, 로우엔드 시장은 고강도 강철에 의존하며, 고급 모델은 탄소섬유 복합 솔루션을 모색합니다.
2- 제조 공정: 효율성과 신뢰성의 균형
배터리 쉘의 제조 공정은 생산 효율성과 제품 신뢰성에 직접적인 영향을 미칩니다. 현재 주류 기술 경로에는 다이캐스팅, 압출 용접 및 구조 통합 기술이 포함됩니다.
a. 다이캐스팅 대 압출 용접
· 압출 알루미늄 프로파일(GM Bolt에서 사용): 단품 비용은 약 800위안으로 대량 생산에 적합하지만 공정이 복잡합니다.
· 다이캐스트 알루미늄(NIO ET5): 단품 비용은 1,500위안이지만 생산 효율성이 5배 증가하여 신속한 생산 수요에 적합합니다.
· 마찰 교반 용접(FSW): 기존 아크 용접에 비해 변형이 50% 감소하고 피로 저항성이 30% 향상되지만 장비 투자는 40% 증가해야 하며 수명 요구 사항이 높은 상용차에 적합합니다.
b. 구조적 통합 기술
· CTP 모듈화(CATL 기린 배터리): 공간 활용률이 72%에서 85%로 증가하고 비용은 15-20% 감소하지만 열 폭주 보호 설계를 강화해야 합니다.
· CTC 섀시 통합(테슬라 모델 Y): 부품 370개가 감소하고 배터리 수명은 54% 증가하지만 유지 관리 비용은 300% 증가하여 애프터 세일즈 시스템에 도전합니다.
주요 데이터 비교
생산 라인 경험: CTP 기술은 높은 호환성으로 인해 여전히 현재 주류를 이루고 있는 반면, CTC는 자동차 회사와 배터리 제조업체 간의 심층적인 협업이 필요하기 때문에 단기적으로 대중화되기 어려울 것으로 보입니다.
3- 미래 트렌드: 기술 통합 및 지능형 업그레이드
a. 재료 복합재
알루미늄/탄소 섬유 하이브리드 쉘(예: 포르쉐 타이칸 컨셉트)은 무게를 15% 줄이고 800MPa 압축 강도를 달성할 수 있지만 인터페이스 접합 강도는 25MPa 이상이어야 하며(도요타 bZ4X 양산 적격률은 65%에 불과함) 공정 안정성을 돌파해야 합니다.
b. 기능 통합 혁신
· 액체 냉각판과 쉘 통합(GAC 매거진 배터리): 냉각 접촉 면적이 50% 증가하고 온도 차이 제어는 <5℃이지만 알루미늄-구리 이종 용접 기공은 레이저 스윙 용접으로 최적화해야 합니다.
· 내장형 광섬유 센서(Continental Group 솔루션): 쉘 변형률 및 온도를 실시간으로 모니터링하고 BMS 응답 속도가 30% 증가했지만 센서 내구성 문제를 해결해야 합니다.
c. 녹색 순환 시스템
BMW의 재활용 알루미늄 기술의 폐쇄 루프 재활용은 탄소 배출량을 60% 줄이지만 재활용 재료의 성능 손실은 10% 이내로 제어해야 합니다. 또한 대형 박벽 다이캐스팅(예: LK 9000T 다이캐스팅 머신)은 금형 온도 차이(±5℃)를 정밀하게 제어해야 하며, 버 세척 효율은 대량 생산의 병목 현상이 됩니다.
프로세스 혁신 방향:
· 복합 재료 성형 사이클 압축(예: LGF-PP 사출 성형 사이클은 180초에서 90초로 단축해야 함);
· 디지털 트윈 기술을 적용하여 충돌 시뮬레이션 오류를 ±20%에서 ±5%로 줄여 설계 신뢰성을 향상시킵니다.
4- 시장 계층화 및 산업화 전망
단기(1~3년): CTP+ 압출 알루미늄 프로파일이 여전히 주류이며, CATL은 34%의 시장 점유율로 계속해서 선두를 달리고 있습니다.
중기(5~10년): CTC와 탄소섬유가 고급시장에 빠르게 침투할 것으로 예상되며, 2030년에는 탄소섬유가 25%를 차지할 것으로 예상된다.
장기 목표: 에너지 밀도를 400Wh/kg으로 획기적인 수준으로 끌어올리는 동시에 국가 표준인 30분 열 폭주 보호 기능을 기반으로 안전 중복성을 더욱 강화하는 것입니다.
5- 결론
배터리 케이싱 기술 경로의 선택은 본질적으로 "시나리오 적응"이며, 이를 위해서는 자동차 기업의 위치, 비용 한계, 공급망 성숙도 등을 종합적으로 고려해야 합니다. 엔지니어로서 우리는 대량 생산의 실현 가능성에 초점을 맞추는 동시에 재료 및 공정의 혁신을 수용해야 하며, 경량성, 안전성 및 비용 간의 역동적인 균형을 통해 최적의 솔루션을 찾아야 합니다. 미래에는 지능형, 친환경 제조 기술이 성숙함에 따라 배터리 케이스는 점차 '수동적 보호'에서 '능동적 안전'으로 전환되어 신에너지 자동차의 광범위한 보급을 위한 견고한 지원을 제공할 것입니다.
당사는 열설계와 경량화에 관한 기술과 정보를 정기적으로 업데이트하여 참고할 수 있도록 공유해 드리겠습니다
Walmate에 관심을 가져주셔서 대단히 감사합니다