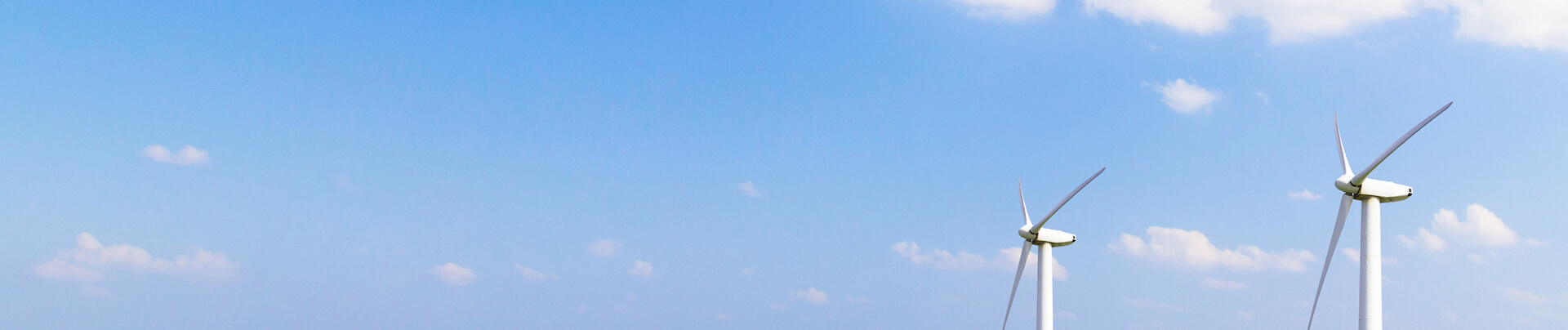
교류와 나눔은 성장을 촉진하고
공동 발전을 위해 협력합니다
실제 생산, 조립 및 사용 과정에서 배터리 트레이의 절연 내전압 고장은 새로운 에너지 산업의 급속한 발전에 숨겨진 암초처럼 종종 발생하여 차량의 주행 안전과 에너지 저장 시스템의 안정적인 작동을 위협합니다. 이 글에서는 제조 관행에 따른 전형적인 고장 모드를 분석하여 관련 실무자에게 피상적인 참고 자료를 제공하고 업계 동료들이 배터리 트레이의 절연 내전압 성능을 개선하는 효과적인 방법을 공동으로 모색하도록 돕습니다.
배터리 트레이 전기 절연 안전 | 3부 - 일반적인 고장 분석
그림 1 절연내압 시험
1- 일반적인 고장 메커니즘 분석
에너지 저장 및 신에너지 자동차용 배터리 트레이의 적용 시나리오는 서로 다르기 때문에 절연 내전압 요구 사항과 고장 조건에 공통점과 차이점이 모두 있습니다.다음과 같습니다.
a. 차이점
동적 부하: 신에너지 자동차는 20-2000Hz의 고주파 기계적 진동을 처리해야 하는 반면, 에너지 저장 시스템은 주로 장기 정적 변형에 직면하며 누적 변형 시간은 10년을 초과합니다.
전압 레벨: 신에너지 자동차 배터리 트레이의 절연 내전압은 3000VDC 이상(GB 38031 기준)에 도달해야 하는 반면, 에너지 저장 시스템은 4200VAC 이상의 절연 내전압이 필요합니다(IEC 61439 기준).
고장 가속 요인: 신에너지 자동차는 연간 2000회 이상의 충전 및 방전 사이클로 인해 열 응력을 발생시켜 절연 고장이 가속화됩니다. 에너지 저장 시스템은 24시간 연중무휴로 작동하며, 연간 평균 작동 시간은 8000시간 이상으로 전기화학적 노화가 발생하여 절연 고장이 가속화됩니다.
b. 공통점
둘 다 절연 저항 모니터링(차가운 상태에서는 100MΩ 이상, 뜨거운 상태에서는 1MΩ/kV 이상)과 부분 방전 제어(5pC 미만)를 통해 절연 고장에 대한 조기 경고를 달성해야 합니다.
2- 배터리 트레이의 절연 내전압 고장을 일으키는 일반적인 제조 결함
(1) 절연 내전압 시공 단계
a. 잠재적 고장 및 원인 분석
· 재료 결함:
원인: 절연 재료 내전압 레벨이 부족하거나, 습기 또는 표면 오염(오일 얼룩, 금속 파편)으로 인해 노화됨.
성능: 절연 저항이 낮음(<100MΩ), 누설 전류가 표준을 초과하거나 내전압 시험 중 직접 고장.
· 공정 문제:
원인: 잔류 금속 파편(거친 용접/절단 공정), 절연 코팅 두께가 고르지 않거나 경화되지 않음.
성능: 부분 방전, 절연층 손상으로 인해 단락이 발생함.
· 환경 간섭:
원인: 고온 및 고습으로 인해 재료의 수분 흡수 및 화학적 부식이 발생함.
성능: 절연 성능이 환경에 따라 저하되고 응축수로 인해 크리피지가 발생함.
· 테스트 오류:
원인: 잘못된 테스트 전압/시간 설정(GB/T 38661 표준에 따르지 않음 등), 접지 불량.
성능: 부품에 대한 적격 또는 과전압 손상에 대한 잘못된 판단.
b. 대응 전략
· 재료 최적화: 내전압 ≥1000V DC의 방습 재료(예: 탄소 섬유 복합 재료)를 선택하고 방오 코팅을 적용합니다.
· 공정 제어: 자동 용접/분무 장비를 사용하고 깨끗한 작업장을 설정합니다.
· 환경 관리: 시공 전에 온도 및 습도 모니터링 및 사전 건조 재료를 설치합니다.
· 테스트 사양: 세분화된 테스트(500V 사전 테스트 + 1000V 공식 테스트), 계측기 교정 및 데이터 기록.
(2) 모듈 설치 단계
a. 잠재적 고장 및 원인 분석
· 조립 오류:
원인: 절연 라이너가 없고 볼트가 너무 조여져 절연 층이 손상됨.
성능: 모듈과 셸 사이의 절연 저항이 낮고 내전압 파괴.
· 기계적 손상
원인: 취급 도구의 긁힘, 절연 필름을 뚫은 금속 파편.
성능: 작동 중 국부 단락 또는 갑작스러운 고장.
· 설계 호환성
원인: 모듈과 트레이 사이의 크기 편차로 인한 전기적 여유 공간 부족.
성능: 기생 커패시턴스로 인해 전압 중첩 파괴.
· 전기적 연결 위험
원인: 배선 하네스가 고정되지 않아 커넥터 씰이 마모 및 고장.
성능: 고전압 배선 하네스 절연 층이 마모 및 누출.
b. 대책
· 오류 방지 설계: 위치 지정 핀 툴링을 사용하여 설치 누락을 방지하고 볼트 길이를 사용자 정의하여 과도한 조임을 방지합니다.
· 청소 작업: 설치 전 진공 청소하고, 도구를 긁힘 방지 실리콘으로 감싼다.
· 허용 오차 시뮬레이션: CAE를 통해 모듈과 트레이의 일치 정도를 검증하여 틈새가 ≥10mm인지 확인한다.
· 공정 검사: 설치 후 메가옴계(≥100MΩ)로 무작위 검사를 수행하고 세그먼트 내전압 시험을 수행하여 고장 지점을 찾는다.
(2) 모듈 설치 단계
a. 잠재적 고장 및 원인 분석
· 조립 오류:
원인: 절연 라이너가 없고 볼트가 너무 조여져 절연 층이 손상됨.
성능: 모듈과 셸 사이의 절연 저항이 낮고 내전압 파괴.
· 기계적 손상
원인: 취급 도구의 긁힘, 절연 필름을 뚫은 금속 파편.
성능: 작동 중 국부 단락 또는 갑작스러운 고장.
· 설계 호환성
원인: 모듈과 트레이 사이의 크기 편차로 인한 전기적 여유 공간 부족.
성능: 기생 커패시턴스로 인해 전압 중첩 파괴.
· 전기적 연결 위험
원인: 배선 하네스가 고정되지 않아 커넥터 씰이 마모 및 고장.
성능: 고전압 배선 하네스 절연 층이 마모 및 누출.
b. 대책
· 오류 방지 설계: 위치 지정 핀 툴링을 사용하여 설치 누락을 방지하고 볼트 길이를 사용자 정의하여 과도한 조임을 방지합니다.
· 청소 작업: 설치 전 진공 청소하고, 도구를 긁힘 방지 실리콘으로 감싼다.
· 허용 오차 시뮬레이션: CAE를 통해 모듈과 트레이의 일치 정도를 검증하여 틈새가 ≥10mm인지 확인한다.
· 공정 검사: 설치 후 메가옴계(≥100MΩ)로 무작위 검사를 수행하고 세그먼트 내전압 시험을 수행하여 고장 지점을 찾는다.
(3) 시스템 통합 단계
a. 잠재적 고장 및 원인 분석
· 교차 시스템 인터페이스 고장:
원인: 구성 요소 절연 매개변수가 일치하지 않음(예: 커넥터 내전압 정격 차이).
성능: 고전압 모선 연결 파손 또는 BMS 간섭.
· 기생 커패시턴스 중첩:
원인: 여러 모듈을 병렬로 연결한 후 총 기생 커패시턴스가 증가하고 커패시턴스 상승 효과가 상당함.
성능: 시스템 수준 테스트 누설 전류가 표준을 초과함.
· 환경 스트레스 고장:
원인: 진동으로 인해 절연 피로가 발생하고 냉각수가 고전압 인터페이스로 스며듬.
성능: 작동 중 절연 저항이 주기적으로 감소함.
· 테스트 사각 지대:
원인: 실제 작업 조건(고온/진동/습도)을 시뮬레이션하지 못함.
성능: 실험실에서는 통과했지만 실제 작동에서는 실패함.
b. 대책
· 호환성 설계: 공급업체 구성 요소 표준을 통합함.
· 기생 커패시턴스 제어: 폴리이미드 절연층을 추가하고 SPICE 시뮬레이션을 통해 레이아웃을 최적화합니다.
· 작업 조건 시뮬레이션 테스트: "-40℃~85℃ 사이클 + 5Hz~200Hz 진동 + 내전압" 복합 테스트를 수행합니다.
· 지능형 모니터링: 통합 온라인 절연 모니터링 모듈, AI가 잠재적 위험을 예측합니다.
3-절연 내전압 시험
절연 내전압 시험은 안전 조치이자 고장의 가능한 원인입니다. 절연 내전압 시험 자체가 부적절한 작동, 장비 문제 또는 설계 결함으로 인해 고장을 일으킬 수 있으며 심지어 시험 대상 장치에 2차 손상을 일으킬 수도 있습니다.
(1) 시험 중 일반적인 고장 유형
(2) 대응 전략은 다음과 같습니다.
a. 테스트 매개변수의 정밀 제어
· 전압 및 시간: 표준에 따라 설정; 용량 증가 효과를 억제하기 위해 용량성 부하(예: 배터리 모듈)에 대한 동적 보상 알고리즘을 활성화합니다.
· 누설 전류 임계값: 장비 사양(예: ≤10mA)에 따라 설정하고 DC/AC 모드를 구분합니다(DC 테스트에는 더 낮은 임계값이 필요함).
b. 장비 및 작동 사양
· 계측기 교정: 내전압 테스터는 6개월마다 교정하고 고전압 라인 절연 층을 매일 시각적으로 검사합니다.
· 안전한 작동: 테스트 전에 저전압 회로를 강제로 분리합니다. 로봇 팔이나 자동 고정 장치를 사용하여 고전압 영역과의 수동 접촉을 피합니다.
c. 고장 방지 및 수리
· 분할 테스트: 모듈의 복잡한 시스템을 테스트하여(예: 먼저 고전압 버스를 테스트한 다음 모듈 절연을 테스트) 고장 지점을 찾습니다.
· 고장 수리: 고장 후 에폭시 수지를 사용하여 손상된 부분을 채우고 수리 후 전체 전압 기울기 시험을 다시 통과해야 합니다(예: 500V→1000V 단계 압력).
d. 환경 및 데이터 관리
· 환경 제어: 시험 구역의 습도가 75% 이상일 때 제습기를 시작하거나 환경이 표준을 충족할 때까지 시험을 지연합니다.
· 데이터 추적성: 시험 전압, 누설 전류 곡선 및 환경 매개변수를 기록하고 MES 시스템을 사용하여 생산 배치 번호를 연관시킵니다.
당사는 열설계와 경량화에 관한 기술과 정보를 정기적으로 업데이트하여 참고할 수 있도록 공유해 드리겠습니다
Walmate에 관심을 가져주셔서 대단히 감사합니다