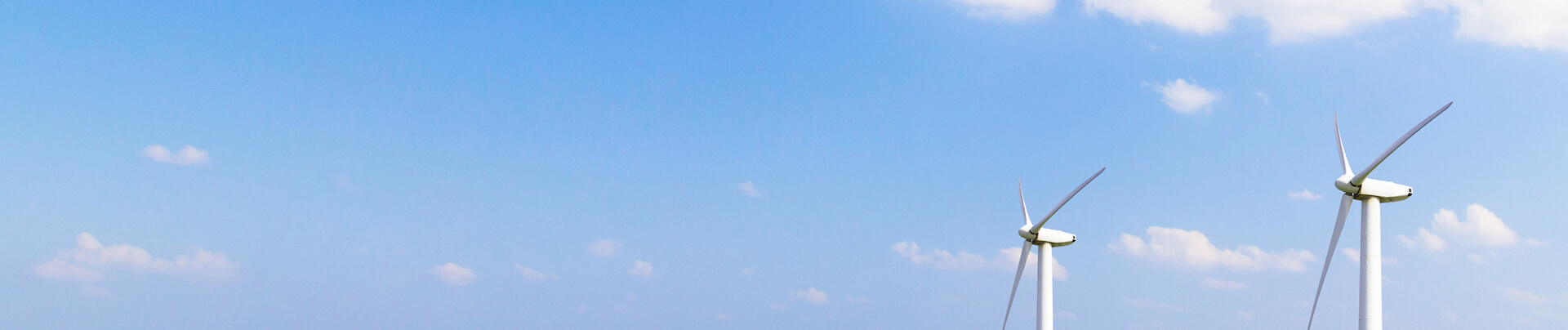
La comunicazione e la condivisione promuovono la crescita
Uniamo le forze per lo sviluppo
Come ingegnere operativo in una fabbrica di produzione di vassoi per batterie, ho partecipato a numerosi progetti per involucri di batterie di veicoli elettrici, sperimentando direttamente il delicato equilibrio tra "leggerezza, sicurezza e costo" nel settore. Questo articolo analizzerà la logica di selezione delle attuali tecnologie e le sfide industriali, suddividendo l’analisi in tre dimensioni: materiali, processi produttivi e tendenze future, con esempi pratici.
1-Percorso dei materiali: Bilanciamento tra leggerezza e costo
La scelta dei materiali per l’involucro della batteria influisce direttamente sulle prestazioni del veicolo e sull’economicità. Le principali opzioni attuali sono leghe di alluminio, acciai ad alta resistenza e materiali compositi, ciascuno con scenari applicativi specifici.
a. Leghe di alluminio: Il pilastro della leggerezza
Profilati in alluminio estruso: Modelli BYD utilizzano profilati estrusi, ottimizzando la forma della sezione per ridurre il peso e aumentare la rigidità strutturale.
Pressofusione integrata: La batteria Tesla 4680 con tecnologia CTC riduce il peso del 50%, ma richiede costi di stampaggio superiori a 200 milioni di RMB, ammortizzabili solo con produzioni annue oltre 500.000 unità, adatto a grandi produttori.
Materiali compositi in alluminio: La Porsche Taycan usa una struttura mista alluminio-fibra di carbonio, riducendo il peso del 15%, ma con un costo incrementale del 30%, limitato ai modelli premium.
b. Acciai ad alta resistenza: La soluzione per mercati sensibili al costo
L’acciaio termoformativo (es. 22MnB5) raggiunge una resistenza a snervamento di 1500 MPa, con una penetrazione del 40% nei veicoli commerciali. Il costo per GWh è inferiore del 40% rispetto all’alluminio, ma la densità energetica si riduce dell’8%. Ideale per modelli sotto i 100.000 RMB, bilanciando costo e sicurezza base.
c. Materiali compositi: Sperimentazioni nel segmento premium
SMC (Sheet Molding Compound): Il guscio superiore della batteria in vetroresina riduce il peso del 30% rispetto all’acciaio, ma richiede spessori maggiori (3mm + rinforzi da 5mm) per compensare la resistenza agli urti.
Fibra di carbonio: L’involucro della BMW i3 è del 50% più leggero dell’alluminio, ma il costo raggiunge 800 RMB/kg, rendendolo adatto solo a modelli di lusso.
Sintesi pratica: La scelta del materiale deve allinearsi al posizionamento del veicolo. Il mercato mid-range (200.000-300.000 RMB) privilegia l’alluminio, quello entry-level l’acciaio, mentre i modelli premium esplorano soluzioni composite.
2-Processi produttivi: Equilibrio tra efficienza e affidabilità
I processi di produzione influenzano direttamente efficienza e affidabilità. Le principali tecnologie includono pressofusione, saldatura di profilati e integrazione strutturale.
a. Pressofusione VS saldatura di profilati
Profilati in alluminio estruso (es. Chevrolet Bolt): Costo unitario ~800 RMB, adatto a grandi volumi, ma processi complessi.
Pressofusione in alluminio (es. NIO ET5): Costo unitario 1500 RMB, ma efficienza produttiva quintuplicata, ideale per produzioni rapide.
Saldatura a attrito (FSW): Riduzione del 50% delle deformazioni rispetto alla saldatura ad arco, con resistenza a fatica migliorata del 30%, ma richiede un investimento in macchinari superiore del 40%, adatto a veicoli commerciali.
b. Tecnologie di integrazione strutturale
CTP (Cell to Pack) - Batteria CATL Qilin: L’utilizzo dello spazio passa dal 72% all’85%, con riduzione dei costi del 15-20%, ma richiede miglioramenti nella protezione termica.
CTC (Cell to Chassis) - Tesla Model Y: Riduzione di 370 componenti, autonomia +54%, ma costi di riparazione +300%, sfidando i sistemi post-vendita.
Confronto dei dati chiave
Esperienza nella linea di produzione: la tecnologia CTP è ancora quella più diffusa grazie alla sua elevata compatibilità; la tecnologia CTC invece richiede una collaborazione approfondita tra le case automobilistiche e i produttori di batterie ed è improbabile che venga diffusa nel breve termine.
3-Tendenze future: Fusione tecnologica e innovazione intelligente
a. Materiali ibridi
Strutture miste alluminio-fibra di carbonio (es. concept Porsche Taycan) riducono il peso del 15% con resistenza a compressione di 800 MPa, ma la stabilità del processo è critica (es. Toyota bZ4X ha una resa del 65%).
b. Integrazione funzionale
Piastre di raffreddamento integrate (es. batteria "Magazine" di GAC): Superficie di contatto +50%, controllo della temperatura entro ±5°C, ma richiede ottimizzazione della saldatura laser per ridurre la porosità.
Sensori a fibra ottica (Continental): Monitoraggio in tempo reale di deformazioni e temperatura, con tempi di risposta BMS +30%, ma necessità di migliorare la durata dei sensori.
c. Sostenibilità e riciclo
La tecnologia BMW di riciclo in ciclo chiuso riduce le emissioni del 60%, ma la perdita di prestazioni dei materiali riciclati deve rimanere sotto il 10%. La pressofusione di grandi componenti (es. pressa da 9000T di LK) richiede controllo termico preciso (±5°C), con la rimozione delle sbavature come collo di bottiglia.
Direzioni di innovazione:
Riduzione del ciclo di formatura dei compositi (es. LGF-PP da 180 a 90 secondi).
Applicazione di gemelli digitali per ridurre l’errore di simulazione da ±20% a ±5%, migliorando l’affidabilità progettuale.
4-Stratificazione del mercato e prospettive
Breve termine (1-3 anni): CTP + profilati in alluminio restano dominanti, con CATL leader (34% di quota).
Medio termine (5-10 anni): CTC e fibra di carbonio accelerano nel premium, raggiungendo il 25% di quota entro il 2030.
Lungo termine: Densità energetica verso 400 Wh/kg, miglioramento della sicurezza oltre gli standard attuali (30 minuti di protezione termica).
5-Conclusione
La scelta del percorso tecnologico per gli involucri delle batterie è una questione di "adattamento allo scenario", bilanciando posizionamento del produttore, soglie di costo e maturità della supply chain. Come ingegneri, dobbiamo abbracciare l’innovazione mantenendo la fattibilità industriale, cercando l’equilibrio dinamico tra leggerezza, sicurezza e costo. Con l’avanzamento di tecnologie intelligenti e sostenibili, gli involucri evolveranno da "protezione passiva" a "sicurezza attiva", supportando la diffusione globale dei veicoli elettrici.
Condivideremo regolarmente aggiornamenti e informazioni su tecniche di progettazione termica e alleggerimento, per la vostra consultazione. Grazie per l'interesse verso Walmate.