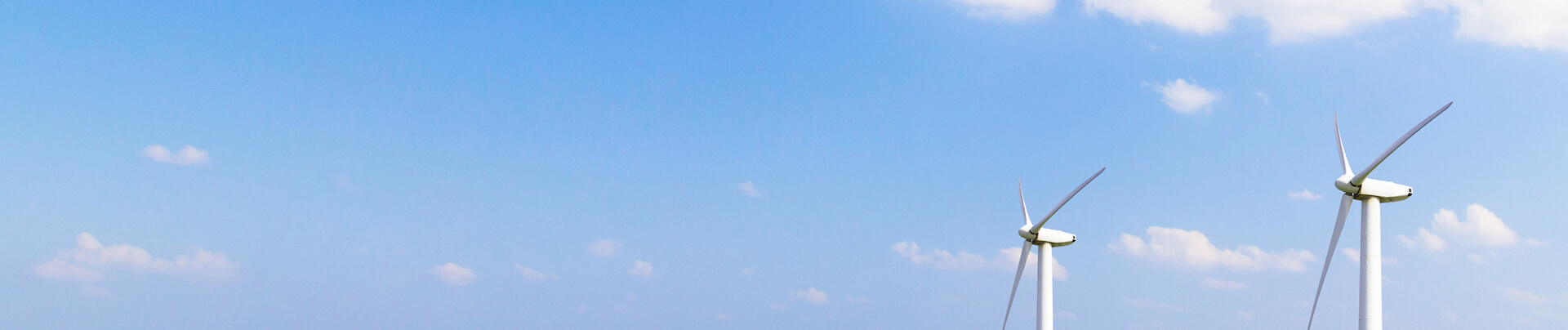
La comunicazione e la condivisione promuovono la crescita
Uniamo le forze per lo sviluppo
Con il continuo aumento della densità di potenza dei dispositivi elettronici, la progettazione della dissipazione del calore è diventata un elemento chiave che influenza l'affidabilità e la durata del sistema. In qualità di produttore professionale con 19 anni di esperienza nella gestione termica, combiniamo casi ingegneristici tipici con l'esperienza nella simulazione multifisica sul campo per analizzare a fondo i cinque principali malintesi tecnici che gli ingegneri tendono a trascurare negli scenari ad alta potenza e fornire soluzioni conformi alle prassi del settore.
Equivoco 1: Abuso di materiali ad alta conduttività termica, deviazione di calcolo della resistenza termica di interfaccia
Problema tipico: Ricerca eccessiva di valori teorici per i materiali termoconduttivi, ignorando la realtà ingegneristica della resistenza termica di contatto dell'interfaccia.
Analisi del caso: Un modulo di dissipazione del calore per radar laser per autoveicoli utilizza un substrato di rame puro (conduttività termica 401 W/m·K), ma lo spessore del rivestimento del materiale di interfaccia termica (TIM) non è controllato con precisione (0,1 mm di progetto, fluttuazione effettiva ±0,05 mm) e la resistenza termica di contatto misurata raggiunge 0,6 °C·cm²/W, causando un superamento del 22% della temperatura di giunzione dell'FPGA rispetto allo standard. Dopo il passaggio ai pad termici preformati (tolleranza ±0,02 mm, resistenza termica <0,03 °C·cm²/W) e la combinazione con il processo di sinterizzazione sotto vuoto, la temperatura di giunzione si riduce di 17 °C e l'MTBF (tempo medio tra guasti) aumenta a 100.000 ore.
Piano di ottimizzazione:
Selezione del materiale: secondo lo standard ASTM D5470, viene misurata la resistenza termica del TIM e si preferiscono materiali a cambiamento di fase o elastomeri caricati con metallo.
Controllo di processo: utilizzare apparecchiature di dosaggio automatiche (precisione ±3%) per garantire una tolleranza di spessore <10% ed evitare vuoti d'aria.
Equivoco 2: Incongruenza nell'organizzazione del flusso d'aria nel sistema di raffreddamento ad aria, punti caldi locali fuori controllo
Problema tipico: sovrapposizione cieca del numero di ventole, ignorando l'adattamento di impedenza del canale di flusso e l'effetto di separazione dello strato limite.
Esempio ingegneristico: un cluster GPU di un data center utilizza 4 ventole da 12.038 (volume d'aria 200 CFM), ma a causa di una progettazione non corretta dell'angolo di guida dell'aria (piegatura ad angolo retto di 90°), il volume d'aria effettivo effettivo è solo il 65% del valore nominale e la differenza di temperatura locale raggiunge i 40 °C. Dopo l'ottimizzazione della simulazione CFD, il canale di guida dell'aria viene modificato in un canale di flusso a espansione graduale (angolo di diffusione <7°) e viene adottato un layout a alette sfalsate (il gradiente di spaziatura aumenta da 2 mm a 3,5 mm), la resistenza al vento complessiva viene ridotta del 30% e la differenza di temperatura del punto caldo viene controllata entro 8 °C. Strategia di base:
Progettazione del campo di flusso: i test in galleria del vento vengono eseguiti secondo la norma ISO 5801 per ottimizzare il rapporto tra le aree di ingresso e di uscita (consigliato 1:1,2).
Controllo dinamico: in base alla curva Q-H della ventola PWM, il punto di impedenza del sistema viene abbinato all'intervallo di efficienza più elevato (solitamente 60-80% del volume d'aria massimo).
Equivoco 3: Un difetto nella progettazione della protezione ambientale accelera l'invecchiamento dei materiali
Problema tipico: concentrarsi solo sulle prestazioni iniziali di dissipazione del calore, ignorando gli effetti di stress ambientali a lungo termine come umidità, calore, polvere e nebbia salina.
Analisi del caso: un convertitore eolico offshore utilizza un dissipatore di calore in lega di alluminio 6061 (anodizzato superficialmente). Dopo 6 mesi di funzionamento in un ambiente con nebbia salina, lo strato di ossido si è staccato, causando un aumento del 50% della resistenza termica di contatto e un aumento del tasso di guasto degli IGBT. Passando alla lega di alluminio 5052 (resistenza alla nebbia salina >1000 ore) e applicando una vernice poliuretanica a tripla resistenza (spessore 50 μm, in conformità con lo standard IEC 60068-2-11), il tasso di guasto sul campo a 3 anni è diminuito del 75%. Punti di forza:
Tecnologia di rivestimento: Rivestimento ceramico Al2O3 mediante spruzzatura al plasma (conduttività termica 30 W/m·K, resistenza a temperature >800 °C) utilizzato in scenari ad alta temperatura.
Struttura di tenuta: Grado di protezione IP69K (guarnizione in silicone a doppio passaggio + valvola di sicurezza) per garantire l'assenza di infiltrazioni di polvere/vapore acqueo.
Equivoco 4: Mancanza di modellazione del carico termico transitorio e selezione inadeguata dei materiali a cambiamento di fase
Problema tipico: la soluzione di dissipazione del calore progettata tramite simulazione a stato stazionario non è in grado di gestire impulsi di potenza nell'ordine dei millisecondi.
Dati misurati: un amplificatore di potenza a stato solido è sottoposto a un carico impulsivo di 2 ms a 2000 W in una stazione base 5G. L'aumento di temperatura transitorio della soluzione tradizionale con substrato in alluminio raggiunge i 55 °C, mentre il materiale a cambiamento di fase a microcapsula (composito paraffina/grafene, calore latente del cambiamento di fase 220 J/g), combinato con la simulazione termica transitoria (lunghezza del passo transitorio ANSYS Icepak 1 ms), viene utilizzato per controllare l'aumento di temperatura a 18 °C, soddisfacendo i requisiti del test di impatto MIL-STD-810G.
Tecnologia di gestione dinamica:
Imballaggio a cambiamento di fase: la struttura a nido d'ape viene utilizzata per incapsulare il materiale a cambiamento di fase (porosità >70%) per evitare perdite di liquido e migliorare l'efficienza di diffusione del calore. Calibrazione del modello: le condizioni al contorno della simulazione vengono corrette in base all'imaging termico a infrarossi (frequenza di campionamento 100 Hz) e l'errore è <±1,5 °C
Equivoco 5: la valutazione del TCO è unilaterale e ignora i costi operativi e di manutenzione nascosti.
Problema tipico: viene confrontato solo il costo iniziale dell'hardware e non vengono quantificate le perdite dovute a consumo energetico/manutenzione/fermi macchina.
Confronto dei costi: una fabbrica di semiconduttori utilizzava originariamente armadi raffreddati ad aria (costo iniziale di 500.000 yuan), con una bolletta elettrica annua di 1,2 milioni di yuan (PUE = 1,8). Dopo l'aggiornamento al raffreddamento a liquido a immersione bifase (costo iniziale di 1,8 milioni di yuan), la bolletta elettrica annua è scesa a 450.000 yuan (PUE = 1,05) e, grazie alla riduzione del carico di condizionamento dell'aria della camera bianca, il risparmio annuo complessivo ha raggiunto i 900.000 yuan e l'investimento incrementale può essere recuperato in 2,1 anni (IRR > 25%). Modello decisionale:
Modellazione raffinata: introduzione di una simulazione Monte Carlo per quantificare l'impatto del tasso di guasto delle apparecchiature (distribuzione di Weibull) sul TCO.
Sovrapposizione delle politiche: in combinazione con meccanismi di tassazione del carbonio (come il CBAM dell'UE), le emissioni di carbonio dei sistemi di raffreddamento a liquido durante l'intero ciclo di vita vengono ridotte del 60% e si ottiene un sussidio aggiuntivo del 15%.
Conclusione: Aggiornamento del paradigma di progettazione termica da basato sull'esperienza a basato sui dati.
Processo standardizzato: Introduzione dello standard di test termico JESD51-14 nella fase di progettazione concettuale per evitare rilavorazioni successive (il ciclo di progetto di un determinato modulo ottico si riduce del 30%).
Collaborazione multidisciplinare: Grazie all'accoppiamento di perdite elettromagnetiche (estrazione HFSS) e campo di deformazione termica con COMSOL Multiphysics, l'efficienza di dissipazione del calore di un componente radar TR migliora del 40%.
Operatività e manutenzione intelligenti: Implementazione di sensori di temperatura a reticolo in fibra (accuratezza ±0,1 °C) e piattaforme di digital twin per ottenere la previsione dei guasti (i tempi di inattività imprevisti di un centro di supercalcolo si riducono del 90%).
Grazie a un approccio ingegneristico rigoroso e alla verifica completa dei dati, i progettisti termici possono evitare con precisione i "killer invisibili" e gettare le basi per sistemi ad alta affidabilità. Come professionisti del settore, ci impegniamo a fornire soluzioni a ciclo chiuso, dai materiali ai sistemi, e ad affrontare congiuntamente le sfide di gestione termica con i clienti.
Condivideremo regolarmente aggiornamenti e informazioni su tecniche di progettazione termica e alleggerimento, per la vostra consultazione. Grazie per l'interesse verso Walmate.