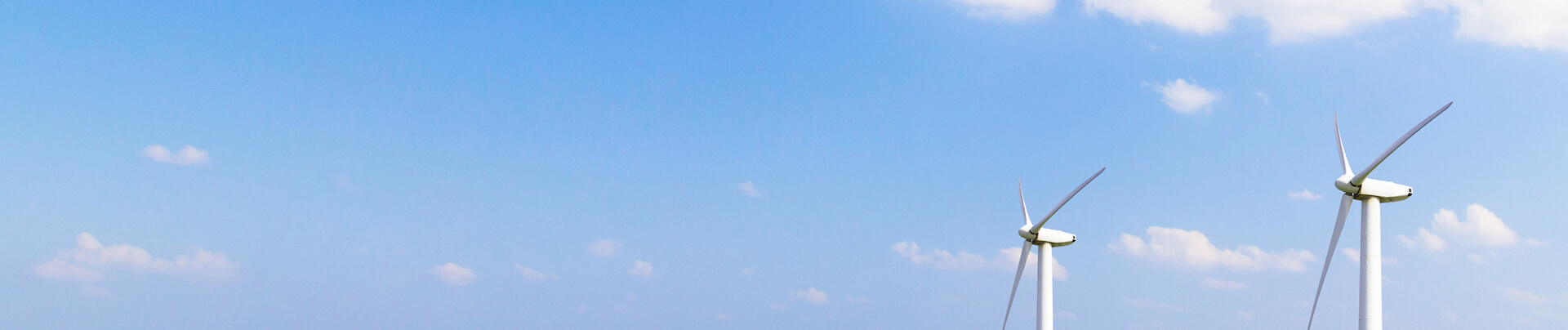
La comunicazione e la condivisione promuovono la crescita
Uniamo le forze per lo sviluppo
1- Requisiti di tolleranza speciali per i componenti chiave
Nella produzione di vassoi batteria per veicoli elettrici e di alloggiamenti per pacchi batteria per accumulo di energia con raffreddamento a liquido, il controllo della tolleranza delle superfici e delle interfacce di collegamento chiave influisce direttamente sulla tenuta, sull'efficienza di dissipazione del calore e sulla precisione di assemblaggio.
a. Superficie di installazione della piastra di raffreddamento a liquido
La piastra di raffreddamento a liquido è il componente principale del sistema di gestione termica della batteria. La planarità della sua superficie di installazione influisce direttamente sulla tenuta del canale di flusso del refrigerante. Se la planarità non rientra nei limiti di tolleranza, causerà una compressione irregolare della guarnizione in silicone, causando perdite localizzate o una maggiore resistenza termica.
b. Disallineamento dei cordoni di saldatura
Il vassoio batteria utilizza spesso una struttura di saldatura in lega di alluminio. Il disallineamento dei cordoni di saldatura causerà una concentrazione di sollecitazioni e ridurrà la durata a fatica. Soprattutto in scenari con elevati requisiti di ermeticità dell'alloggiamento del pacco batteria (come IP67), il disallineamento deve essere rigorosamente controllato.
c. Foro di posizionamento del modulo batteria
Il foro di posizionamento viene utilizzato per fissare con precisione il modulo batteria. Una tolleranza eccessiva causerà il disallineamento del modulo, con conseguenti guasti ai collegamenti elettrici o rischi di vibrazioni meccaniche.
d. Fissaggio della posizione del foro per i bulloni
Il foro per i bulloni viene utilizzato per collegare l'alloggiamento del pacco batteria al telaio. Eventuali deviazioni di posizione causeranno sollecitazioni di assemblaggio e persino la rottura dei bulloni.
e. Rettilineità dei bordi dell'alloggiamento del pacco batteria
La rettilineità dei bordi dell'alloggiamento del pacco batteria influisce sull'assemblaggio dei coperchi superiore e inferiore e sul livello di protezione IP, in particolare per gli alloggiamenti saldati al laser, dove il bordo deve essere utilizzato come riferimento per il tracciamento della testina laser.
2- L'impatto della tolleranza dimensionale sull'efficienza produttiva
L'impatto della tolleranza dimensionale sull'efficienza produttiva si riflette principalmente nel suo equilibrio tra flusso di lavorazione, controllo dei costi e qualità del prodotto. Una progettazione con tolleranze ragionevoli può non solo garantire la funzionalità del prodotto, ma anche ottimizzare il ritmo di produzione. L'impatto di un controllo ragionevole della tolleranza dimensionale sull'efficienza produttiva si riflette principalmente nei seguenti aspetti:
a. Equilibrio tra precisione di lavorazione e costi di produzione
· Sebbene una rigorosa tolleranza dimensionale possa migliorare la precisione di sigillatura e assemblaggio, sono necessarie apparecchiature di lavorazione ad alta precisione e processi complessi, il che aumenta significativamente l'investimento in attrezzature e i tempi di lavorazione.
· Un'eccessiva ricerca della precisione può comportare un aumento dei costi di lavorazione. È necessario impostare tolleranze rigorose nei componenti funzionali chiave e le tolleranze dovrebbero essere opportunamente allentate nelle aree non critiche per ridurre i costi.
b. Controllo del tasso di rilavorazione e del tasso di scarto
· Una progettazione con tolleranze ragionevoli può ridurre le rilavorazioni causate da deviazioni dimensionali.
· La deformazione da saldatura è il problema principale nella produzione di vassoi per batterie. L'utilizzo del processo di saldatura a freddo CMT può ottimizzare l'apporto termico, ridurre la deformazione dopo la saldatura e abbreviare il ciclo di rilavorazione.
c. Produzione modulare e standardizzata
· Grazie ai componenti standardizzati, i requisiti di tolleranza si concentrano su parti sostituibili localmente, riducendo la difficoltà di lavorazione complessiva.
· La progettazione con tolleranze standardizzate può inoltre supportare la compatibilità multi-modello e ridurre la necessità di lavorazioni personalizzate.
3-Standard di settore e applicazioni pratiche del controllo della planarità
Per i vassoi batteria dei veicoli a nuova energia, gli standard di settore prevedono requisiti rigorosi:
a. Standard di planarità: la planarità della superficie di installazione della piastra di raffreddamento a liquido deve essere ≤0,2 mm, la planarità della piastra di supporto inferiore deve essere ≤0,5 mm/m² e l'errore di planarità del telaio dopo la saldatura deve essere ≤0,8 mm6.
b. Ottimizzazione del processo di produzione: la fresatura di precisione CNC, la saldatura a freddo CMT e il trattamento di invecchiamento tramite vibrazioni (VSR), combinati con il rilevamento online tramite interferometro laser, riducono il rischio di deformazione.
c. Selezione del materiale: si consiglia di utilizzare leghe di alluminio ad alta resistenza come la 6061, con un limite di snervamento ≥1180 MPa, tenendo conto sia della leggerezza che della stabilità strutturale.
4- Strategia di adeguamento delle tolleranze basata su materiali e processi
a. L'innovazione nei materiali favorisce l'alleggerimento
Utilizzo di leghe di alluminio leggere ad alta resistenza (come la 6061) e materiali compositi (matrice di alluminio rinforzata con carburo di silicio), combinate con anodizzazione e rivestimento isolante, per ottenere una riduzione del peso del 30% e migliorare la resistenza alla corrosione, adattandosi ai requisiti di dissipazione del calore dei sistemi di raffreddamento a liquido.
b. La collaborazione di processo migliora la precisione di produzione
Lo stampaggio per estrusione monoblocco + la saldatura ad attrito e stiramento (FSW) riducono il numero di saldature, la saldatura a freddo CMT e la saldatura laser controllano la deformazione termica.
c. Simulazione a ciclo chiuso per garantire l'affidabilità
La simulazione CAE ottimizza la disposizione delle nervature di rinforzo, la scansione laser e la tecnologia di rilevamento delle perdite di elio consentono il monitoraggio completo del processo, il design modulare è compatibile con tolleranze di ±5 mm, riducendo i costi e aumentando l'efficienza.
Condivideremo regolarmente aggiornamenti e informazioni su tecniche di progettazione termica e alleggerimento, per la vostra consultazione. Grazie per l'interesse verso Walmate.