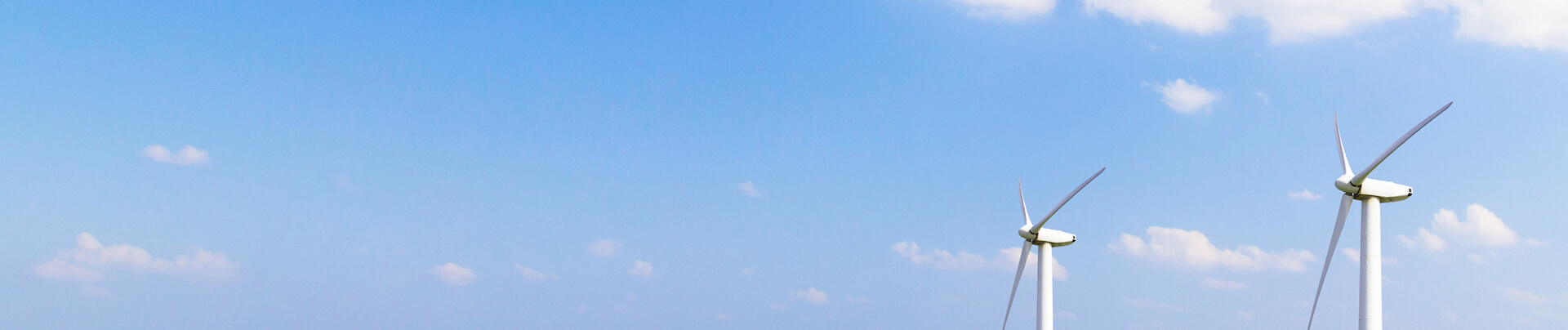
Communication and sharing promote growth
Joining Hands for Development!
The most popular water blocks are basically pure copper microchannel type. The copper bottom plate is directly processed with skived, and the fins are integrated with the bottom plate to reduce thermal resistance. The bottom plate and the cover plate are brazed or diffused to ensure the reliability of the seal.
1- Advantages of using skiving process to manufacture water blocks
l Integrated design: The skiving process can integrate the floor and fins, which is helpful to reduce contact thermal resistance and improve thermal conductivity. In addition, the integrated bottom plate and fin design can also improve structural strength.
l High-precision processing: The skiving process can produce a very fine tooth structure, and the tooth height, tooth thickness and tooth pitch can be precisely controlled, which makes the heat sink fins denser, the heat dissipation area larger, and the heat dissipation more efficient. At the same time, it can also better meet the personalized needs of different customers for shape, size, etc.
l The production efficiency is high, and the skiving process can be mass-produced. Compared with traditional CNC, the skiving process can process multiple gear pieces at the same time, which greatly improves the production efficiency.
Figure 1: Water block base with different processing technologies a-Skiving b-CNC c-Cold Forging
2- Cost structure of skiving water block
l Design and development costs: The design complexity of the skiving water blockis relatively high, especially when high heat dissipation performance requirements are required, which requires complex process design and optimization.
l Material cost: The materials used in the skiving process are mainly aluminum and copper alloy. The design of combining aluminum plate and copper alloy is more common in radiator manufacturing and has a higher cost performance, so the quality of aluminum and copper directly affects the cost.
l Processing cost:
Skiving process cost: The skiving process involves high-precision CNC machining equipment, such as three-axis CNC machine tools. The use of such equipment requires a high investment cost, and the technical requirements for operators are also high, which will increase production costs.
Welding process cost: In the manufacturing process of water blocks, welding process is also an important cost factor. Vacuum brazing and diffusion welding are two commonly used welding methods. Brazing can weld multiple joints at the same time, has high production efficiency, requires brazing materials, has high requirements for process conditions, and is difficult to control quality; diffusion welding equipment has a large one-time investment, and diffusion welding does not require fillers, but has high requirements for the surface processing of the workpiece.
Surface treatment cost: Common surface treatment methods include anodizing, plating, etc. For aluminum alloy water blocks, anodizing can improve surface hardness, wear resistance and corrosion resistance, while increasing the aesthetics of the product; copper water blocks will be plated, such as nickel plating, to prevent copper oxidation and corrosion, and increase product life and reliability.
l Other costs: inspection and testing, packaging and transportation, etc.
3-Cost optimization suggestions
l Optimizing material usage
Choose the right material: For example, copper has high thermal conductivity, high unit density, and high unit price; aluminum has light weight, low unit price, and slightly poor thermal conductivity.
Material usage: Ensure efficient use of materials and reduce material waste by accurately calculating material thickness and margin.
Figure 2: Schematic diagram of material consumption calculation
l Optimizing production processes
Simplify molds: Design simple molds to reduce mold complexity and cost.
Reduce scrap rate: Reduce scrap rate through precise process control and quality inspection.
One-step molding: Optimize process routes, reduce multiple processing steps, and improve production efficiency.
We will regularly update you on technologies and information related to thermal design and lightweighting, sharing them for your reference.Thank you for your attention to Walmate.