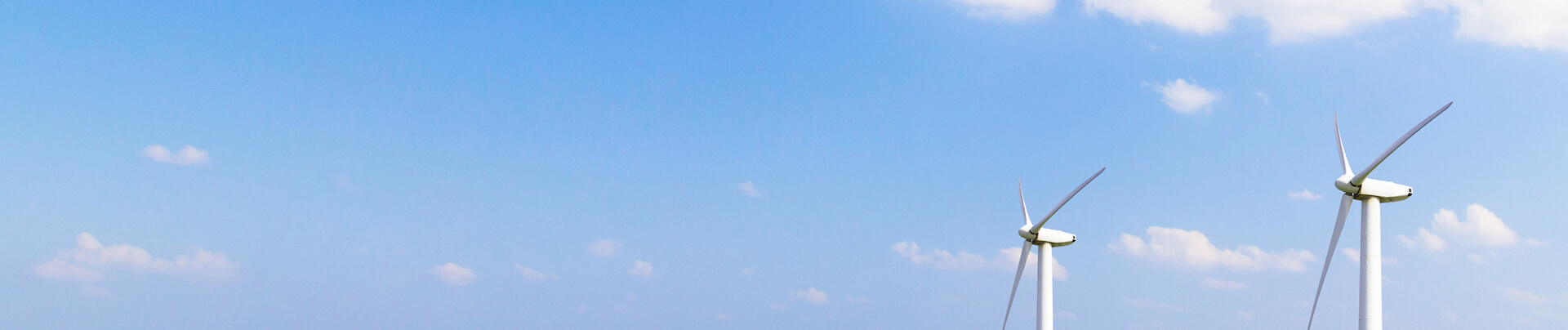
分かち合うことで成長します
手を携えて共に行い共に発展する
CTC(セルツーシャーシ)技術は、電気自動車の航続距離とスペース効率を大幅に向上できるため、多くの注目を集めていますが、従来のバッテリー技術を本当に置き換えることができるかどうかはまだ議論の余地があります。製造側の中心的なボトルネックであるバッテリートレイの溶接プロセスは、この技術の将来を決定する鍵となっています。複雑な構造設計、複数の材料の互換性、厳格な熱管理要件により、従来の溶接技術は大きな試練にさらされています。この記事では、第一線のエンジニアの視点から、業界のトレンドとエンジニアリングの実践を組み合わせて、CTC技術の可能性と限界を分析し、溶接技術がどのようにしてこの技術革命の「試金石」になったかを探ります。
1-CTC技術の「理想と現実」
CTC技術は、理論的にはバッテリーセルをシャーシに直接統合することで冗長な構造部品を減らし、エネルギー密度を向上させることができますが、その大規模適用の実現可能性は現実的な課題に直面しています。
自動車会社の急進性と慎重さ:テスラ、BYDなどの大手企業はCTCソリューションを立ち上げていますが、多くのメーカーはまだ様子見しています。業界データによると、2025年2月時点で、CTC量産モデルは世界の15〜20%を占めており、従来のCTP(Cell-to-Pack)技術が依然として主流です。
バッテリー寿命の向上の「コスト」:CTCはエネルギー密度を15%〜20%向上させることができますが、シャーシ構造の複雑さにより製造コストが30%〜50%増加します(コンサルティング機関による計算)。コストと利益のバランスはまだ明確ではありません。
メンテナンスの経済論争:統合設計により、バッテリーのメンテナンスコストが急騰しました。保険会社のデータによると、CTCモデルの事故後のバッテリーアセンブリの交換率は70%と高く、従来のモデルの25%をはるかに上回っています。
これらの矛盾により、CTC技術の将来は変数に満ちています。市場が20%を突破できるかどうかは、3つの主要な変数に依存します。テスラサイバートラックの量産の進捗状況、中国の自動車メーカー間の価格戦争によりCTCがコスト削減を余儀なくされるかどうか、およびバッテリーの修理可能性に関する欧州規制の妥協の程度です。製造側の溶接技術レベルは、研究室と量産の間のギャップを乗り越えられるかどうかを決定する鍵となります。
2-溶接工程の3つの「生死の壁」
バッテリートレイメーカーにとって、CTC技術の導入は3つの核心問題を克服する必要があります。
a. 「ミクロンレベル」の精度と効率の勝負
従来の溶接工程では0.5mmの誤差を許容できますが、CTCトレイではより多くのバッテリーを搭載する必要があり、継ぎ目の数は3倍以上になり、そのほとんどは湾曲した不規則な部分に分布しています。メーカーのテストによると、溶接位置の誤差が0.15mmを超えると、バッテリーセルアセンブリの歩留まりが99%から82%に急激に低下します。さらに厄介なのは、精度の向上は効率の低下を伴うことが多いことです。レーザー溶接の精度は高いものの、設備コストは従来の溶接の5倍以上です。
b. 混合材料の「水と火」
軽量と強度のバランスをとるために、CTCトレイでは「アルミニウム合金+炭素繊維+特殊鋼」の混合構造がよく使用されます。異なる材料の熱膨張係数の差は最大20倍(アルミニウム23μm/m·K対カーボンファイバー0.8μm/m·Kなど)にもなり、溶接時に内部応力が発生しやすく、割れの原因となります。ある企業がアルミニウムとカーボンファイバーを接合しようとしたところ、溶接部の割れ率は18%にも達し、業界の許容閾値である3%を大きく上回りました。
c. 熱影響部の「見えないキラー」
溶接温度が高いと、バッテリーセル周辺の絶縁材やセンサー回路が損傷する可能性があります。ある自動車会社は、溶接入熱の不適切な制御により、バッテリーモジュールの自己放電率が50%増加したことがありました。エンジニアは、溶接温度の変動を0.1秒以内に±15℃以内に制御する必要があります。これは、溶接ガンに「高精度温度ブレーキ」を取り付けるのと同じです。
3-解決策:特効薬はなく、システム革新のみ
これらの課題に直面して、業界は3つの突破口を模索しています:
a. プロセス組み合わせの「カクテルセラピー」
レーザーアークハイブリッド溶接:レーザー溶接の精度とアーク溶接の浸透の利点を組み合わせることで、アルミニウム合金の溶接速度が40%向上します。
冷間金属遷移技術(CMT):正確な入熱制御により、熱影響部の面積が60%減少します。
ロボットインテリジェント補正システム:リアルタイムの溶接スキャンデータに基づいて溶接ガンのパスを自動的に調整し、複雑な曲面溶接の合格率を75%から95%に向上します。
b. 材料面での「事前妥協」
一部の企業は、材料サプライヤーと共同で「溶接に適した」複合材料の開発を開始しています。例えば、国内の改良アルミ合金(物理的、化学的、またはプロセス手段によって調整されたアルミ合金材料)の溶接割れ感受性は、レベル7からレベル3(ISO規格による)に低下しました。軽量化効果は5%犠牲になりますが、溶接歩留まりは98%に向上します。
c. 検出次元の「デジタルツイン」
溶接プロセスのすべてのデータ(電流、温度、速度など)を収集し、AIモデルと組み合わせて欠陥の確率を予測します。ある工場がこの技術を導入した後、溶接欠陥のオンライン検出率は80%から97%に向上し、スクラップコストは45%削減されました。
4- エンジニアの新たな提案:不確実性の中に確実性を見出す
a. CTC 技術をめぐる論争は、本質的には「システム最適化」と「局所的限界」の間のゲームです。
溶接プロセスのブレークスルー速度が自動車会社のコスト削減期待よりも遅い場合、CTC はニッチな技術になる可能性があります。
材料、プロセス、テスト技術が協調してブレークスルーを達成した場合、電気自動車の構造設計の新しい時代が到来すると予想されます。
b. エンジニアにとって、次の 2 つの側面から能力を再構築する必要があります。
クロスドメイン知識の統合:溶接熱入力に対する電気化学特性の敏感な閾値を理解する。
アジャイル対応能力:ヨーロッパのサプライヤーのケーススタディでは、新しい合金材料の溶接パラメータの最適化を 1 週間以内に完了できるチームは、受注の確率が 3 倍に増加することが示されています。
CTC 技術は、「破壊的イノベーション」と「大量生産の罠」の岐路に立っています。既存の技術を完全に置き換えることはできないかもしれませんが、溶接プロセスをより高い精度、より強力な互換性、よりインテリジェントな制御に向けて進化させています。この技術マラソンで本当の勝者は、最も早くこの技術を開発した自動車会社ではなく、製造側で「不可能な溶接」を「標準化されたインターフェース」に変えるエンジニアリング チームかもしれません。
ご参考になるために、定期に熱設計及び軽量化に関する技術と情報を更新させていただきます。当社にご関心をお持ちいただき、ありがとうございます。