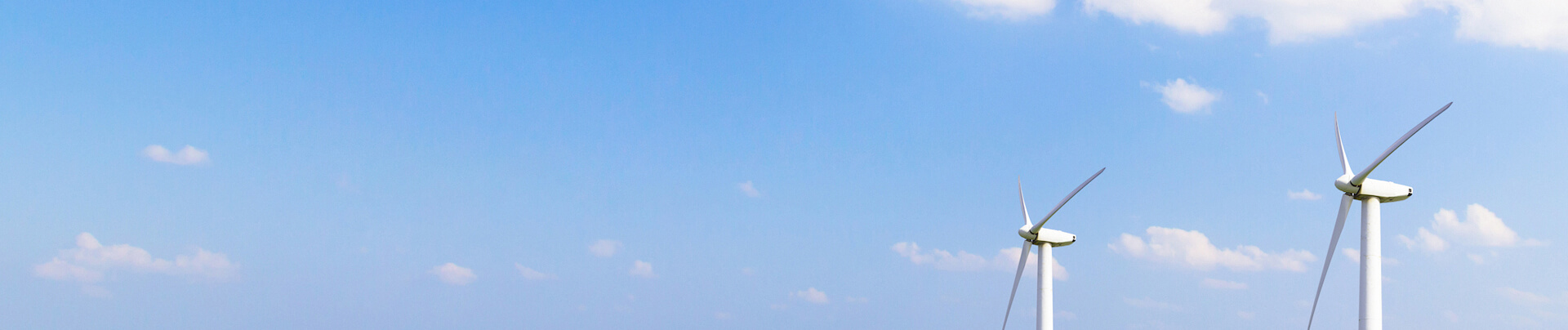
プロジェクトの効果を高めるために精一杯的なプッシュします
エネルギー貯蔵業界における安全性の進化は、技術革新と安全基準の相乗効果によって推進される体系的な変化です。放熱経路の再構築、材料と構造の協調的な保護、統合的な熱管理に至るまで、このプロセスは、受動的な防御から能動的な抑制へ、そして単一次元から多層的な結合のアップグレードへと、業界における熱暴走防止の根底にあるロジックを反映しています。
1-エネルギー貯蔵技術における「不可能の三角形」と中核的な矛盾を解決するための戦略
a. エネルギー貯蔵技術における「不可能の三角形」の矛盾は、主に複数の側面における相互牽制と均衡に表れています。
エネルギー貯蔵技術の開発は、エネルギー密度、安全性、コストの間で複雑なバランスをとる必要があります。高活性材料はエネルギー密度を向上させることができますが、同時に熱暴走のリスクを大幅に高めます。システムレベルの安全設計(液体冷却温度制御技術など)はリスクを低減できますが、多くの場合、エネルギー密度の低下を伴います。さらに、能動保護システムや本質安全技術の導入は安全性を向上させることができますが、バッテリー以外の部品のコストを大幅に増加させます。これらの矛盾は、エネルギー貯蔵技術の進化において解決すべき複数の制約を明らかにしています。
b. 中核的な矛盾を解決するための戦略
材料イノベーション:新しい電解質材料の適用により、高エネルギー密度を考慮しながら、熱暴走の伝播時間を大幅に遅延させることができます。ナトリウムイオン電池は、負極材料の最適化により、適切なエネルギー密度を維持しながらコストを削減しています。ナノ複合材料の導入により、理論容量が大幅に向上しています。
システム最適化:高度な液体冷却技術は、精密な温度制御により放熱効率を大幅に向上させ、運用・保守コストを削減します。動的再構成可能なバッテリーネットワークは、迅速なトポロジー調整によりシステムの可用性を高めます。
インテリジェント制御:人工知能早期警報システムは、多次元データ融合を通じてリスク予測の精度を大幅に向上させ、エネルギー変換技術の進歩はシステム効率を大幅に向上させました。政策とビジネスモデルの革新は、技術導入を加速させています。例えば、共有エネルギー貯蔵モデルは単一投資のプレッシャーを軽減し、カスケード利用はライフサイクル全体のコストをさらに最適化しました。
2-進化のルール
a. 技術パスの融合イノベーション
マルチソースデータに基づくインテリジェントな早期警報:新世代の監視システムは、ガス、圧力、音響信号などの多次元センサーデータを統合し、動的故障モデルと履歴データ分析を組み合わせることで、誤報率を大幅に低減し、警報時間を短縮します。
熱管理と火災連動設計:液体冷却技術と動的温度調整アルゴリズムを組み合わせることで、精密な温度制御を実現し、防火システムとバッテリー管理を深く統合することで、多層的な連動戦略を構築し、熱暴走の拡大を効果的に抑制します。
材料と構造の協調的最適化:従来の耐火材料に代わり、耐熱断熱コーティングを採用することで、熱拡散遮断時間を大幅に延長します。また、構造設計に衝突防止補強と方向性圧力緩和チャネルを導入することで、機械的衝撃への耐性を向上させます。
b. 保護レベルの段階的深化
バッテリーセルからシステムへの段階的な保護:バッテリーセルレベルに埋め込まれたセンサーにより、早期のリスク監視を実現します。モジュールレベルでは複合検出器と相変化材料を用いることで局所的な熱蓄積を抑制し、システムレベルでは協調型監視プラットフォームを構築することでライフサイクル全体にわたる保護を実現します。
受動的な対応から能動的な防御へ:新規格は、能動的な防御技術の開発を促進します。例えば、インテリジェントなバッテリー管理システムは、動的インピーダンス解析によって充電開始時にリスク経路を遮断し、能動的な結露防止技術は環境ハザードを排除します。
多次元的な協調型保護:熱・電気・機械の協調設計によりシステム全体の安全性を強化します。防火および運用・保守の協調型監視は、製造・輸送の全工程を網羅し、誤報のリスクを低減します。
3-進化のプロセス
a. 放熱技術の進化
液冷技術が主流に:液冷システムは効率的な温度均一化によりバッテリークラスターの温度差を大幅に低減し、寿命を延ばし、安全性を向上させます。浸漬液冷技術は放熱限界をさらに突破し、高レート充放電シナリオをサポートします。
構造最適化による放熱効率の向上:マルチチャネル並列設計により冷却剤の均一な流れを実現し、断熱機能と冷却機能の統合により熱拡散経路を遮断します。
b. 材料と構造の革新
高安全材料システム:耐高温ダイヤフラムとセラミックコーティングにより、熱暴走の連鎖反応を大幅に遅延します。軽量複合材料は、構造強度と保護性能を向上させながら軽量化を図ります。
バッテリーセルとモジュールの革新:新しいバッテリーセル設計は、内部構造の最適化により循環を低減し、寿命を延ばします。また、モジュール統合技術により、スペース利用率と放熱効率を向上させます。
c.熱管理の統合
システムレベルの統合設計:この統合ソリューションは、バッテリー管理、防火、熱管理を高度に統合し、柔軟な導入をサポートし、過酷な環境にも適応します。
インテリジェンスと協調制御:人工知能モデルがバッテリーの状態をリアルタイムで予測し、エネルギー配分を最適化します。また、防火システムと熱管理が連携し、迅速な対応を実現します。
ライフサイクル全体の管理:設計から廃棄までのクローズドループ管理に加え、デジタル監視とクラウドベースの健全性評価を組み合わせることで、システムの信頼性を大幅に向上させます。
結論
エネルギー貯蔵技術の安全性におけるイノベーションは、技術革新の成果であるだけでなく、エネルギーシステムの基礎ロジックの再構築でもあります。材料、構造、インテリジェンスの深層統合により、エネルギー密度、安全性、コストといった様々な制約を打破し、マイクロセルからマクロシステムに至るまでの3次元的な保護ネットワークを構築しています。液体冷却技術と動的早期警報の相乗効果、耐高温材料と軽量設計の相補性、そしてライフサイクル全体にわたる閉ループロジックは、高安全性・高効率エネルギー貯蔵システムの将来ビジョンを描き出します。量子材料や固体電池といった最先端技術の飛躍的進歩により、エネルギー貯蔵業界は本質安全と大規模応用の新時代へと加速し、世界のエネルギーシステムの低炭素化とインテリジェント化に永続的な力をもたらすでしょう。
ご参考になるために、定期に熱設計及び軽量化に関する技術と情報を更新させていただきます。当社にご関心をお持ちいただき、ありがとうございます。
エネルギー貯蔵システムが大容量化、高エネルギー密度化に向かって進化するにつれ、エネルギー貯蔵蓄電池パック筐体のサイズマッチングと互換性設計が、システム効率と信頼性の向上における中核的な課題となっています。この記事では、最新のエンジニアリング設計事例、特許技術、業界動向を組み合わせて、スペース利用、モジュールの互換性、バッテリーセルの配置とサポート設計という 3 つの側面から分析を行います。
1-スペース利用を最適化する
統合エネルギー貯蔵システムの空間利用率の向上は、本質的には、技術の反復とシナリオ要件からの双方向の推進力です。大容量バッテリーセル、モジュール型アーキテクチャ、液体冷却統合などの技術の共同イノベーションを通じて、業界は「大規模なスタッキング」から「極端な空間再利用」へと移行しています。
a.大容量バッテリーセルの応用:エネルギー密度と効率の飛躍的向上
アイデアの要約: 大容量バッテリーセルを適用する本質は、バッテリーパックの内部構造レベルを削減し、バッテリーセルからバッテリーパックまでのスペース利用率を直接向上させることです。従来のバッテリーパックは、「バッテリーセル→モジュール→バッテリーパック」の3段階の統合モードを採用しており、モジュール構造(横梁、縦梁、ボルトなど)によりスペース利用率が低くなります。大容量バッテリーセルは、単一セルを長くしたり体積を増やしたりすることでモジュールレベルをスキップし、CTP (Cell to Pack) 技術を使用してバッテリーセルをバッテリーパックに直接統合することができます。
技術的コア: 600Ah 以上の超大型バッテリーセルを使用することで、バッテリーセルと接続ポイントの数を減らし、単一セルの容量を増加させます。
b.空間再利用とコスト最適化:「コンポーネントスタッキング」から「多次元再利用」へ
アイデアの概要: 空間の再利用とコストの最適化は表裏一体であり、その根底にある論理は、構造の簡素化、機能の統合、材料の反復、標準化された設計を通じて、従来のエネルギー貯蔵システムの物理的およびコスト的な限界を打ち破ることです。
空間再利用の核となるのは、構造階層を極限まで簡素化することで中間リンクを削減することです。たとえば、2 in 1 の高電圧ボックス設計: 江蘇省トリナエネルギーストレージの特許取得済み技術は、2 つの高電圧ボックスを 1 つに統合し、正/負のリレーと電気接続をすべて共有することで、占有する水平スペースを 30% 削減し、電気部品のコストを 15% 削減します。
機能モジュールのクロスドメイン再利用、構造部品と放熱チャネルの統合、例えば液体冷却プレートをボックスの底板と統合し、液体冷却パイプと構造サポート間のスペースを共有することで、独立した放熱部品を 15% 削減します。バッテリーセル本体を構造部品として採用: BYD ブレード バッテリーは、長くて薄いバッテリーセルの側壁によって支持強度を確保し、モジュール フレームを排除することで、スペース利用率を 60%~80% に向上させます。
高電圧カスケードトポロジーなどの電気トポロジーの徹底的な最適化により、単一セルの容量と電圧レベルを高めることで並列回路の数を減らし(Huawei のスマートストリングエネルギーストレージなど)、バッテリースタックの物理的なスペースを 20% 削減し、システム応答時間を 50% 短縮します。 ;共有リレー設計、江蘇省トリナエネルギーストレージの2イン1高電圧ボックスは、2つのラインで同じリレーを共有できるため、リレーの数とケーブルの長さが50%削減され、設置効率が30%向上します。
2-バッテリーセルの配置と支持設計:耐荷重、放熱性、耐振動性のバランス
セル配置の本質は、空間の利用、熱の分散、および機械的安定性の間のゲームです。セルの物理的形状と配置方向は、空間充填効率に直接影響します。
a.バッテリーセルの配置を最適化
逆バッテリーセル設計:バッテリーセルの防爆バルブが下向きになっているため、熱暴走排気口と底部の防球スペースが共有され、バッテリーセルの高さスペースが解放され、体積利用率が向上します。
横向きセルレイアウト: バッテリーパックの高さ方向のスペース利用を最適化し、活性材料の割合を増やし、垂直セルよりも大幅に高い体積利用率を実現します。
超長薄型バッテリーセル:バッテリーセルを長く、薄く設計することで、単位体積あたりのバッテリーセル数を削減し、グループ化の効率を向上させます。
b.放熱と耐荷重の結合設計:構造、材料、プロセスの共同イノベーションを通じて、効率的な放熱と構造強度の二重の最適化を実現することを目指します。
構造設計パス:
液体冷却プレートと支持梁の適合設計などの一体構造:液体冷却チャネルをアルミニウム合金支持梁に埋め込み、独立した部品を減らし、スペース利用率を向上させます。
バッテリーパック、液体冷却システム、BMS を層状に積み重ねて、熱流と機械的ストレスの相互干渉を低減する、階層化および区画化されたレイアウト。
ハニカム/波形構造などのバイオニック機械最適化、アルミニウム合金サポートフレーム内のハニカムまたは波形コア層の設計(Mufeng.comの特許取得済みソリューションなど)、変形により振動エネルギーを吸収し、放熱経路を最適化します。
材料イノベーションの道筋:
熱伝導性と耐荷重性の一体化、例えばアルミニウム合金複合繊維材料(熱伝導率 ≥ 200 W/m·K、強度 +30%)。スマート材料、相変化充填層(PCM)は熱を吸収し、ゆっくりと放出します。温度差は±1.5℃です。軽量ダンピング:弾性シリコンクッション層が振動を吸収します(ダンピング+40%)。
プロセス実装パス:
押し出し成形などの精密成形プロセス:複雑な流路を持つアルミニウム合金液冷ビームの製造に使用されます。
アルミニウム合金の表面にセラミック酸化物層を生成して耐食性を向上させる(塩水噴霧試験 ≥ 1000 時間)とともに放熱効率を高める(表面放射率 20% 増加)などの表面処理技術。
インテリジェントな組み立てプロセスと動的なプリロード調整。圧力センサーと電動アクチュエータを統合してボルトのプリロード (5 ~ 20kN) をリアルタイムで調整し、バッテリーセルへの過圧による損傷を回避します。
c.支持構造の耐荷重性と耐振動性の協調設計: 支持システムは、静的耐荷重性 (バッテリーセルの重量 + 積み重ね圧力) と動的耐振動性 (輸送/地震の影響) という 2 つの要件を満たす必要があります。
3- モジュール性と互換性:標準化されたインターフェースとスケーラブルなアーキテクチャ
標準化されたインターフェースを使用してマルチサイズのバッテリーセルに適応することの本質は、機械、電気、熱管理の共同イノベーションを通じて、統一されたプラットフォーム上でバッテリーセル仕様の柔軟な拡張を実現することです。現在のテクノロジーは静的な互換性から動的な調整へと移行しており、将来的にはインテリジェンス、軽量、シナリオ間の統合へと進化していきます。
a.機械構造の協働イノベーション:
機械インターフェースの標準化: 統一された接続デバイスの寸法を定義します。
モジュラー バッテリー パック/キャビネット設計: スケーラブルなモジュールとバッテリー キャビネットは、標準化されたバッテリー ユニット (280Ah セルや 314Ah セルなど) を通じて構築され、さまざまな容量要件との柔軟な組み合わせをサポートします。
図1-280Ahエネルギー貯蔵蓄電池パック筐体
b.電気システムの動的調整
BMS 互換性などの標準化された通信プロトコルとインターフェース: 異なるメーカーの PCS およびバッテリー セルとのシームレスな接続をサポートするために、統一された BMS (バッテリー管理システム) 通信プロトコルを策定します。動的電力調整は、仮想慣性制御とマルチタイムスケール最適化アルゴリズムを通じて、有効電力と無効電力のリアルタイム調整を実現します。適応型電気パラメータマッチング設計。
c.熱管理システムのインテリジェントな適応
階層的な熱管理ソリューション。難燃性高反発フォーム、熱伝導性接着剤、その他の材料をセル レベルで使用して、断熱性と放熱性の要件のバランスを取り、熱の拡散を抑制します。モジュールレベルの統合液体冷却プレートと断熱層の統合設計により、サイクル寿命が向上しました。システムレベルでは、可変周波数コンプレッサーと複数の冷却ブランチを通じて冷却能力を動的に調整します。
インテリジェントな監視と予測、マルチセンサーの融合。高精度な温度取得を実現するために、温度センサーをバッテリーセルの極や広い表面などの重要な場所に配置し、デジタルツインテクノロジーは、クラウド監視と予測メンテナンスを通じて、熱放散戦略をリアルタイムで最適化します。
4- 結論
エネルギー貯蔵蓄電池パック筐体の最適化は、単一の構造改善から多次元の共同イノベーションへと移行しました。
カーボンファイバーボックス+CTP技術+AIレイアウトアルゴリズムの組み合わせなど、材料、構造、アルゴリズムの融合が主流になるでしょう。
モジュール化と標準化が加速しており、Pack を最小の機能単位とする標準化された設計により、業界はコストを削減し、効率性を高めることになります。
熱管理と空間利用が深く統合され、液浸液体冷却と動的温度制御技術により、宇宙の潜在能力がさらに発揮されます。
ご参考になるために、定期に熱設計及び軽量化に関する技術と情報を更新させていただきます。当社にご関心をお持ちいただき、ありがとうございます。
AIコンピューティング能力の爆発的な成長とデータセンターの電力密度の継続的な増加により、従来の空冷技術ではもはや放熱ニーズを満たすことができなくなりました。効率的な放熱、省エネ、消費電力削減といった利点を持つ液冷技術は、もはや必須の技術となっています。液冷技術において、コールドプレートと液浸冷却の競争は特に熾烈です。本稿では、技術的特徴、適用シナリオ、費用対効果、将来の動向といった観点から、両者の長所と短所を分析し、今後の主流となる方向性を探ります。
1- 技術的特徴の比較:コールドプレート型は高い互換性を持ち、液浸型はより高い放熱効率を持つ
a. コールドプレート液冷:スムーズな移行を実現する「改革派」
高い互換性:サーバー構造を大幅に変更する必要がなく、既存の空冷式データセンターのインフラと互換性があり、改修コストが低く、サイクルも短い。
高い安全性:冷媒が電子部品に直接接触しないため、漏洩のリスクが低く、モジュール設計(クイックチェンジジョイントや冗長配管など)によってさらにリスクを低減できる。
高い成熟度:コールドプレート技術は、Alibaba Cloud Qiandao LakeデータセンターやIntelとの連携プロジェクトなどで広く採用されており、現在の液冷市場の90%を占めている。
限界:コールドプレート型はCPUやGPUなどの一部の高電力コンポーネントしかカバーできず、残りの熱は依然として空冷による放熱に頼る必要がある。 PUE値は通常1.1~1.2で、液浸型よりもわずかに高くなります。
b. 液浸液冷:効率的な放熱を実現する革新的技術
液浸液冷は、サーバー全体を断熱性のある冷却剤に浸漬し、直接接触させることでデバイスの放熱を最大限に高めます。主な利点は以下のとおりです。
優れたエネルギー効率:液体の熱伝導率は空気の20~30倍で、PUEは1.05まで低下し、放熱効率は3倍以上向上します。
省スペース:冷却システムの容積は空気冷却のわずか3分の1で、1筐体あたりの電力密度は50kW以上に達します。これは、AIスーパーコンピューティングなどの高密度環境に適しています。
静音性と環境への配慮:ファンが不要で、騒音は90%以上低減され、粉塵汚染も発生しないため、機器の寿命が長くなります。
課題:液浸にはカスタマイズされたサーバーが必要であり、冷媒のコストが最大 60% を占め (フッ素系液体など)、初期投資が高く、環境適合性を向上させる必要があります。
2-アプリケーションシナリオの差別化:中短期的にはコールドプレート型が主流、長期的には液浸型の可能性が発揮される
a. コールドプレート型:既存データセンターの改修および新規IDC構築における「費用対効果の高い選択肢」
旧式データセンターの改修:コールドプレート型は、既存の空冷アーキテクチャに迅速に適応でき、改修サイクルが短く、コストも制御可能です。例えば、IntelとBihが共同で開発したモジュール型ソリューションは、標準化されたコールドプレート設計により導入の難易度を軽減します。
中高密度コンピューティングパワーシナリオ:コールドプレート型は既に1筐体あたり130~250kWの電力をサポートしており(NVIDIA BシリーズGPUなど)、ほとんどのAIトレーニングニーズに対応しています。
b. 液浸型:スーパーコンピューティングおよびグリーンデータセンター向けの「究極のソリューション」
超高密度コンピューティングパワー:次世代チップ(NVIDIA Rubinシリーズなど)の筐体電力は1000kWを超え、液浸型が唯一の実現可能なソリューションとなるでしょう。
グリーン省エネニーズ:液浸型のPUEは1.05に近づき、廃熱回収効率は90%に達します(Lenovoのソリューションなど)。これは「デュアルカーボン」目標政策と一致しています。
c. 現在の市場状況
コールドプレート型が現在の市場を支配しています。2025年には、コールドプレート型が液体冷却市場の80%~90%を占め、液浸型は10%未満になります。さらに、標準化されたインターフェース(IntelのOCPコールドプレート設計など)が形成されており、InspurやSugonなどのメーカーのソリューションは高い互換性を備えています。国内の「東西データコンピューティング」プロジェクトでは、新規データセンターのPUEを1.25以下に抑えることが求められており、コールドプレート型は移行における第一選択肢となっています。
液浸型の準備が整いました:Sugon Digital C8000相変化液浸ソリューションはPUE 1.04を達成し、Alibaba Cloudの「Kirin」データセンターは単相液浸の実現可能性を検証しました。NVIDIA B200 GPU(1000W+)などの高出力チップは液浸型アプリケーションを強制し、液体冷却のコンピューティング電力密度は30%~50%増加します。EUは2028年にフッ素系液体の使用禁止を計画しており、国内の炭化水素/シリコンオイル冷却剤の研究開発が加速しています(Sinopecの「Kunlun」シリーズなど)。
3-権威ある意見 PK
コールドプレート派:コールドプレートは液体冷却普及の「砕氷船」であり、今後5年間で増分液体冷却市場の80%を占め続けるだろう。液浸型は、チップの消費電力が臨界点を突破するまで待つ必要がある。
液浸型派:相変化液浸は液体冷却の究極の形態であり、コールドプレートは過渡的なソリューションに過ぎない。チップ単体の消費電力が800Wを超えると、液浸型が唯一の選択肢となる。
中立派:技術ルートの分化は、コンピューティングパワー需要の階層化を反映している。コールドプレートは「東洋のデータ」を、液浸型は「西洋のコンピューティング」を支える。今後10年間は、この二本の並行開発が主要なテーマとなるだろう。
4-業界の機会と戦略
コストとエコシステム:コールドプレートは短期的な優位性を有しており、液浸型はコスト削減によって膠着状態を打破する必要がある。
コールドプレート:材料の最適化(銅アルミニウム複合材)、加工精度の向上(リーク防止プロセス)、モジュール化・標準化設計の推進。
液浸:費用対効果の高い冷却剤(単相液浸液など)、互換性のあるキャビネットの開発、そしてチップメーカーとの協力による冷却ソリューションのカスタマイズ。
技術予備:将来の高電力需要に対応するため、二相流コールドプレートとインテリジェント監視システム(AIダイナミックフロー調整など)の検討。
5-結論
短期(2025~2027年):コールドプレート型が一般的なシナリオを席巻し、液浸型普及率は15~20%に上昇。長期(2030年以降):相変化液浸型は高コンピューティングパワー分野で主流となり、コールドプレート型は中低密度市場へと後退。
優位性:冷却剤コスト、チップ消費電力の急上昇、国際的な環境保護政策。
ご参考になるために、定期に熱設計及び軽量化に関する技術と情報を更新させていただきます。当社にご関心をお持ちいただき、ありがとうございます。
新エネルギー自動車やエネルギー貯蔵産業の急速な発展に伴い、軽量化、高い安全性、効率的な熱管理が中核的なニーズとなっています。当社はアルミニウム合金材料の加工分野に深く関わっており、高度な材料選定、成形プロセス、溶接技術を駆使して、バッテリートレイ、液体冷却プレート、エネルギー貯蔵パックボックス、ラジエーターなどの研究開発と製造に注力しています。アルミニウム合金は、低密度(約2.7g/cm³)、高強度、耐腐食性、優れた熱伝導率(熱伝導率約150~220W/m·K)を特徴としており、新エネルギー機器の軽量化と熱管理に最適な選択肢となっています。
1- アルミニウム合金材料の選定と重要な考慮事項
製品によってアルミニウム合金に対する性能要件は大きく異なるため、強度、耐食性、溶接性、プロセス適応性などを考慮して材料を総合的に選定する必要があります。
a. バッテリートレイ
一般的なグレード:6061-T6、6005A-T6、6063-T6
選定基準:
·引張強度240MPa以上(例:6061-T6)で、国家標準の押出試験、落下試験、ボール衝撃試験に合格する必要があります。
·溶接性が高く、熱割れが発生しにくいこと(Mg/Si強化型6xxxシリーズが推奨されます)。
·耐食性は、陽極酸化処理またはアルミニウムクラッド処理によって向上します。
図1-アルミニウム合金バッテリートレイ
b. エネルギー貯蔵パックボックス
一般的なブランド:5083、6061-T6(強度と耐食性の両方)。
選定基準:
・振動および衝撃荷重に耐える必要があり、降伏強度は200MPa以上である必要があります。
・電気化学的腐食を防ぐため、高度な表面処理が必要です。
c. 液体冷却プレート
一般的なブランド:3003、6061/6063、6082。
選定基準:
・高い熱伝導性と耐食性。
・液体冷却チャネルは複雑な成形を必要とするため、優れた押出性能を持つ6xxxシリーズが推奨されます。
2- プロセス性能の違いと加工上の難しさ
アルミニウム合金の加工は、特に切削、CNC加工、溶接、表面処理において、その物理的特性に適応する必要があります。
a. 切削とCNC加工
難しさ:
· 高精度穴加工では、材料の延性によりバリや変形(段付き穴の縁の突起など)が発生しやすくなります。
· 薄肉構造(液体冷却プレートの流路など)では、反りを防止するために切削抵抗を制御する必要があります。
解決策:
· ダイヤモンドコーティング工具を使用することで、刃先の切れ味を向上させ、押し出し変形を低減します。
· 加工パラメータ(高速・低送りなど)を最適化し、一般的なCNC装置と連携させることで、安定した加工を実現します。
b. 溶接プロセス
主な課題:
· 酸化膜(Al₂O₃ 融点 2050℃)は溶融を阻害し、気孔やスラグ介在物の発生につながります。
· 一部の合金は高温割れが発生しやすいため、溶接線エネルギーと溶接ワイヤの組成を制御する必要があります。
推奨される溶接プロセス:
·TIG溶接(交流電源):薄板に適しており、「陰極クリーニング」によって酸化膜を除去します。
·MIG溶接(高電流+ヘリウム混合ガス):厚板の溶接効率が高く、入熱量も制御可能です。
図2-バッテリートレイの溶接
c. 表面処理
·絶縁耐圧コーティング:バッテリートレイおよびパックボックス内部に塗布し、高圧試験(3000V DC/1分以上)に合格する必要があります。コーティング厚さは20~50μmで、高電圧環境下における絶縁安全性を確保します。
·絶縁・除湿コーティング:エネルギー貯蔵パックボックスには、内部結露のリスクを低減するため、疎水性材料(フッ素樹脂など)を使用し、ダイン値は34以上で接着性を確保します。
·衝突防止コーティング:バッテリートレイの外壁には、ポリウレタンエラストマー(硬度80ショアA以上)を選択し、耐衝撃性を30%以上向上させます。
·陽極酸化処理:従来の防錆処理で、膜厚誤差は3μm以下で、複雑な構造に適しています。
3- 検証検査と設備適応性
新エネルギー産業の規格(GB/T31467.3、UL2580など)を満たすには、多次元検証とプロセス適応が必要です。
a. 検証検査
・構造強度:有限要素法シミュレーション(最大応力≤材料降伏強度)を用いて、トレイの耐荷重性、押し出し性、ボール衝撃性を検証します。
・シーリング試験:液体冷却システムは、ヘリウムリーク検出(リーク速度≤1×10⁻⁶ mbar·L/s)とサイクル圧力試験(0.5~1.5MPa/5000回)を実施します。
・コーティング性能検証:
絶縁コーティング耐電圧試験(5000V DC/60秒間、破壊なし)
衝突防止コーティングは、落下ボール衝撃試験(1kg鋼球、高さ1m)および塩水噴霧試験(1000時間、剥離なし)に合格します。
b.設備適応性の最適化
・CNC設備の汎用化:高精度治具設計と動的補正アルゴリズムにより、薄肉部品の加工変形を0.1mm以下に抑えます。
・溶接パラメータライブラリ:様々なアルミニウム合金グレードに対応した標準溶接パラメータ(電流値やワイヤ送給速度など)を確立し、デバッグサイクルを短縮します。
・自動コーティングスプレー:多軸ロボットスプレーと赤外線硬化技術を組み合わせることで、コーティング均一性誤差を5%以下に抑えます。
結論
新エネルギー機器におけるアルミニウム合金の広範な応用は、材料科学の成果であるだけでなく、プロセスイノベーションの成果でもあります。当社は、高強度、耐腐食性、加工性に優れた新たなアルミニウム合金の開発を継続し、プロセスイノベーションを通じてバッテリートレイや液体冷却プレートなどの製品の性能向上を推進し、業界が効率化と軽量化を実現できるよう貢献していきます。
ご参考になるために、定期に熱設計及び軽量化に関する技術と情報を更新させていただきます。当社にご関心をお持ちいただき、ありがとうございます。
電子機器の電力密度が高まり続ける中、放熱設計はシステムの信頼性と寿命を左右する重要な要素となっています。19年にわたる熱管理の経験を持つ専門メーカーとして、当社は典型的なエンジニアリング事例とマルチフィジックスのフィールドシミュレーションの経験を組み合わせ、高電力シナリオにおいてエンジニアが見落としがちな5つの主要な技術的誤解を深く分析し、業界の慣行に準拠したソリューションを提供します。
誤解1:高熱伝導率材料の乱用、インターフェース熱抵抗の計算誤差
典型的な問題:熱伝導性材料の理論値を追求しすぎ、インターフェース接触熱抵抗の工学的現実を無視している。
事例分析:ある車載レーザーレーダー放熱モジュールでは、純銅基板(熱伝導率401W/m·K)を使用していましたが、熱伝導性材料(TIM)のコーティング厚さが正確に制御されておらず(設計値0.1mm、実測値±0.05mm)、測定された接触熱抵抗が0.6°C·cm²/Wに達し、FPGAジャンクション温度が規格値を22%超過しました。そこで、成形サーマルパッド(許容差±0.02mm、熱抵抗<0.03°C·cm²/W)に切り替え、真空焼結プロセスと組み合わせることで、ジャンクション温度は17°C低下し、MTBF(平均故障間隔)は10万時間に向上しました。最適化計画:
材料選定:ASTM D5470規格に基づき、TIMの熱抵抗を測定し、相変化材料または金属充填エラストマーを推奨します。
工程管理:自動塗布装置(精度±3%)を使用し、厚さ公差を10%未満に抑え、エアギャップを回避します。
誤解2:空冷システムにおける気流構成の不一致、局所的なホットスポットの制御不能
典型的な問題:ファンの数を盲目的に積み重ね、流路インピーダンス整合と境界層剥離効果を無視している。
エンジニアリング例:あるデータセンターのGPUクラスターでは、4基の12038ファン(風量200CFM)を使用していましたが、エアガイド角度(90°直角曲げ)の設計が不適切だったため、実際の有効風量は公称値の65%に過ぎず、局所的な温度差は40℃に達しました。CFDシミュレーションによる最適化の後、エアガイドを徐々に拡大する流路(拡散角度<7°)に変更し、フィン間隔の勾配を2mmから3.5mmに増加させるスタッガードフィンレイアウトを採用することで、全体の風圧抵抗を30%削減し、ホットスポットの温度差を8℃以内に抑えることができました。
コア戦略:
流れ場設計:ISO 5801規格に準拠した風洞試験を実施し、入口と出口の面積比を最適化します(推奨:1:1.2)。
動的制御:PWMファンのQ-H曲線に基づき、システムインピーダンス点を最高効率範囲(通常、最大風量の60~80%)に合わせます。
誤解3:環境保護設計の不備が材料の劣化を加速させる
典型的な問題:初期の放熱性能のみを重視し、湿度、熱、粉塵、塩水噴霧などの長期的な環境ストレスの影響を無視している。
事例分析:洋上風力発電コンバータは、6061アルミニウム合金ヒートシンク(表面陽極酸化処理)を使用していました。塩水噴霧環境で6ヶ月間稼働させた後、酸化層が剥離し、接触熱抵抗が50%増加し、IGBTの故障率が急上昇しました。5052アルミニウム合金(耐塩水噴霧性1000時間以上)に切り替え、ポリウレタン耐水性塗料(厚さ50μm、IEC 60068-2-11規格に準拠)を塗布したところ、3年間のフィールド故障率は75%減少しました。
設計ポイント:
コーティング技術:高温環境下でも使用できるよう、プラズマ溶射Al2O3セラミックコーティング(熱伝導率30W/m·K、耐熱温度800℃以上)を採用しています。
シーリング構造:IP69K保護等級(ダブルパスシリコンシール+圧力リリーフバルブ)により、粉塵や水蒸気の侵入を防止します。
誤解4:過渡熱負荷モデリングの欠如と相変化材料の不適切な選択
典型的な問題:定常状態シミュレーションで設計された放熱ソリューションは、ミリ秒レベルの電力パルスに対応できません。
実測データ:5G基地局において、ソリッドステートパワーアンプに2ms@2000Wのパルス負荷が印加されました。従来のアルミニウム基板ソリューションでは過渡温度上昇が55℃に達しましたが、マイクロカプセル型相変化材料(パラフィン/グラフェン複合材、相変化潜熱220J/g)と過渡熱シミュレーション(ANSYS Icepak 過渡ステップ長1ms)を組み合わせることで、温度上昇を18℃に抑え、MIL-STD-810G衝撃試験要件を満たしました。
動的管理技術:
相変化パッケージング:ハニカム構造で相変化材料(多孔度>70%)をカプセル化することで、液漏れを防ぎ、熱拡散効率を向上させました。
モデルキャリブレーション:シミュレーション境界条件は赤外線熱画像(サンプリングレート100Hz)に基づいて補正され、誤差は±1.5°C未満です。
誤解5:TCO評価は一方的で、隠れた運用・保守コストが考慮されていない
典型的な問題:ハードウェアの初期コストのみが比較され、エネルギー消費量、保守コスト、ダウンタイムによる損失が定量化されていない。
コスト比較:ある半導体工場では、当初空冷キャビネット(初期コスト50万元)を使用しており、年間電気代は120万元(PUE=1.8)でした。二相液浸液冷却(初期コスト180万元)にアップグレードした後、年間電気代は45万元(PUE=1.05)にまで低下しました。クリーンルームの空調負荷の削減により、年間の総合的な節約額は90万元に達し、増分投資は2.1年で回収可能(IRR>25%)です。
意思決定モデル:
改良モデリング:モンテカルロシミュレーションを導入し、機器故障率(ワイブル分布)がTCOに与える影響を定量化する。
政策の重ね合わせ:炭素税メカニズム(EU CBAMなど)と組み合わせることで、液体冷却システムのライフサイクル全体にわたる炭素排出量は60%削減され、さらに15%の追加補助金が得られる。
結論:熱設計パラダイムを経験主導からデータ主導へアップグレード
標準化プロセス:概念設計段階でJESD51-14熱試験規格を導入し、後々の手戻りを回避(ある光モジュールのプロジェクトサイクルが30%短縮)。
学際的連携:COMSOL Multiphysicsの電磁損失(HFSS抽出)と熱ひずみ場の連成により、レーダーTRコンポーネントの放熱効率が40%向上。
インテリジェントな運用・保守:ファイバーグレーティング温度センサー(精度±0.1℃)とデジタルツインプラットフォームを導入し、障害予測を実現(スーパーコンピューティングセンターの予期せぬダウンタイムを90%削減)。
厳格なエンジニアリング思考とフルリンクデータ検証により、熱設計エンジニアは「見えないキラー」を正確に回避し、高信頼性システムの基盤を築くことができます。当社は業界の実務家として、材料からシステムまでのクローズドループソリューションを提供することに尽力しており、お客様と共同で熱管理の課題に取り組んでいます。
ご参考になるために、定期に熱設計及び軽量化に関する技術と情報を更新させていただきます。当社にご関心をお持ちいただき、ありがとうございます。
1-主要部品の特別な許容誤差要件
EV バッテリー トレイおよびエネルギー貯蔵用液体冷却バッテリー パック エンクロージャの製造では、主要な接続面とインターフェイスの許容誤差管理が、シーリング、放熱効率、組み立て精度に直接影響します。
a. 液体冷却プレートの取り付け面
液体冷却プレートは、バッテリー熱管理システムのコア コンポーネントです。取り付け面の平坦度は、冷却剤流路のシーリングに直接影響します。平坦度が許容範囲外の場合、シリコン ガスケットの圧縮が不均一になり、局所的な漏れや熱抵抗の増加が発生します。
b. 溶接継ぎ目のずれ
バッテリー トレイでは、多くの場合、アルミニウム合金の溶接構造が使用されています。溶接継ぎ目のずれは、応力集中を引き起こし、疲労寿命を低下させます。特に、バッテリー パック エンクロージャの気密性に対する要件が高いシナリオ (IP67 など) では、ずれを厳密に管理する必要があります。
c. バッテリー モジュールの位置決め穴
位置決め穴は、バッテリー モジュールを正確に固定するために使用されます。許容誤差が大きすぎると、モジュールの位置ずれが発生し、電気接続の障害や機械的振動のリスクが生じます。
d. ボルト穴の位置の固定
ボルト穴は、バッテリー パック エンクロージャをシャーシに接続するために使用されます。位置のずれは、組み立て時のストレスの原因となり、ボルトの破損につながることもあります。
e. バッテリー パック エンクロージャのエッジの真直度
バッテリー パック エンクロージャのエッジの真直度は、上部カバーと下部カバーの組み立てと IP 保護レベルに影響します。特に、レーザー溶接エンクロージャでは、エッジをレーザー ヘッド トラッキングの基準として使用する必要があります。
2-寸法公差が製造効率に与える影響
寸法公差が製造効率に与える影響は、主に加工フロー、コスト管理、製品品質のバランスに反映されます。合理的な公差設計は、製品の機能を保証するだけでなく、生産リズムを最適化することもできます。寸法公差の合理的な管理が製造効率に与える影響は、主に次の側面に反映されます。
a. 加工精度と生産コストのバランス
· 寸法公差を厳密にすると、シーリングと組み立ての精度が向上しますが、高精度の加工設備と複雑なプロセスが必要になり、設備投資と加工時間が大幅に増加します。
· 精度を過度に追求すると、加工コストが増加する可能性があります。重要な機能部品には厳格な公差を設定する必要があり、重要でない領域では公差を適切に緩和してコストを削減する必要があります。
b. 再加工率とスクラップ率の管理
· 合理的な公差設計により、寸法偏差による再加工を減らすことができます。
· バッテリートレイの製造では、溶接変形が主な問題です。 CMT 冷間溶接プロセスを使用すると、入熱を最適化し、溶接後の変形を減らし、再作業サイクルを短縮できます。
c. モジュール化および標準化された生産
· 標準化されたコンポーネントにより、許容誤差要件がローカル交換部品に集中し、全体的な処理の難しさが軽減されます。
· 標準化された許容誤差設計により、複数モデルの互換性もサポートされ、カスタマイズされた処理の必要性が軽減されます。
3-平坦度制御の業界標準と実用化
新エネルギー車のバッテリートレイの場合、業界標準には厳しい要件があります。
a. 平坦度基準:液体冷却プレートの設置面の平坦度は≤0.2mm、底部支持プレートの平坦度は≤0.5mm/m²、溶接後のフレームの平坦度誤差は≤0.8mm6でなければなりません。
b. 製造プロセスの最適化:CNC精密フライス加工、CMT冷間溶接、振動老化処理(VSR)をレーザー干渉計オンライン検出と組み合わせることで、変形のリスクを軽減します。
c. 材料の選択:軽量性と構造安定性の両方を考慮して、降伏強度が≥1180MPaの6061などの高強度アルミニウム合金の使用をお勧めします。
4-材料とプロセスによる許容差調整戦略
a. 材料の革新が軽量化を推進
軽量の高強度アルミニウム合金(6061など)と複合材料(炭化ケイ素強化アルミニウムマトリックス)を使用し、陽極酸化処理と絶縁コーティングを組み合わせることで、30%の軽量化と耐腐食性の向上を実現し、液体冷却システムの放熱要件に適応します。
b. プロセスのコラボレーションにより製造精度が向上
一体型押し出し成形+攪拌摩擦溶接(FSW)により溶接回数が削減され、CMT冷間溶接とレーザー溶接により熱変形が制御されます。
c. 信頼性を確保するためのシミュレーション検出クローズドループ
CAEシミュレーションにより補強リブのレイアウトが最適化され、レーザースキャンとヘリウム漏れ検出技術により完全なプロセス監視が実現され、モジュール設計は±5mmの許容差に対応し、コストを削減して効率を高めます。
ご参考になるために、定期に熱設計及び軽量化に関する技術と情報を更新させていただきます。当社にご関心をお持ちいただき、ありがとうございます。
1- バッテリートレイ/エネルギー貯蔵パックボックスのアルミニウム合金溶接プロセスの特徴
新エネルギー液体冷却パックボックス、バッテリートレイなどの製品の製造では、液体冷却チャネルとマルチキャビティ構造が典型的な複雑な設計機能です(図1を参照)。このような構造には、多くの場合、次の機能が含まれます。
図1: バッテリートレイの典型的な設計
3 次元空間のインターレース: 流路は蛇行状に分布し、多数の空間的転換点があります。
多段接続: メインキャビティとサブキャビティは薄壁の仕切り (厚さ 2 ~ 3 mm) で接続されています。
小型化の特徴: 流路の断面積が小さく (アルミニウム プロファイル流路の最小壁厚は 1.2 mm)、溶接のアクセス性が悪い。
2- バッテリートレイ製造における複数の溶接技術の組み合わせの難しさ分析
バッテリートレイ製造の実践では、摩擦撹拌溶接 (FSW)、冷間金属遷移溶接 (CMT)、従来の溶融溶接 (TIG/MIG) などの技術の協調適用など、複数の溶接技術を組み合わせる必要があります。この組み合わせは、軽量、強度、密閉、生産効率を考慮することを目的としていますが、次のような中核的な困難にも直面しています。
a. 複数のプロセスの熱入力の協調の問題
異なる溶接技術 (FSW やレーザー溶接など) は熱入力に大きな違いがあり、材料の性能の変化や熱変形を引き起こしやすいため、溶接シーケンスとパラメータ調整を最適化することで解決する必要があります。
b. 機器の互換性と効率のボトルネック
機器の切り替えは複雑で、パラメータ同期の精度要件は高くなります。共同作業の効率を向上させ、サイクル時間を短縮するには、モジュラーワークステーションの設計とインテリジェント溶接機が必要です。
c.シール強度とコストのバランスをとる課題
複数の溶接の交差部での漏れのリスクが高く(欠陥の70%を占める)、冗長シール+トポロジー最適化設計が必要です。
3-エンジニアリングの実践:バッテリートレイ、エネルギー貯蔵液体冷却PACKボックスのマルチ溶接プロセス調整
a. 溶接痕の位置計画
· 溶接位置の最適化:製品設計段階では、溶接位置の合理性を十分に考慮し、製品の機能に影響を与える重要な部分や領域に溶接痕が現れないようにする必要があります。たとえば、フロントフレームとウォーターノズルの隙間を調整して溶接痕の干渉を防ぎ、ウォーターノズルの溶接位置を最適化して製品のパフォーマンスへの影響を減らします。
· 製品構造とのマッチング:溶接位置は製品構造と一致し、製品の使用中に溶接がさまざまな負荷とストレスに耐えられるようにする必要があります。たとえば、液体冷却プレートプロジェクトでは、溶接位置を合理的に計画することで、製品の構造的安定性と信頼性が向上します。
· 操作と検出が容易:溶接位置は、オペレーターが溶接操作とその後の品質検査を実行するのに便利なものでなければなりません。たとえば、手の届きにくい場所や視界の悪い場所での溶接を避けて、溶接の効率と品質を向上させます。
b.溶接痕の制御
· 溶接痕のサイズ:溶接痕のサイズは厳密に制御する必要があります。一般的に、溶接痕の高さは4/6mmの範囲内である必要があり、製品の外観と組み立て精度を確保するために、溶接痕は平面を超えないようにする必要があります。たとえば、液体冷却プレートプロジェクトでは、溶接パラメータとプロセスを調整することで溶接痕のサイズをうまく制御し、溶接痕が製品の性能と品質に与える影響を回避しました。
· 溶接痕の形状:溶接痕の形状は、過度の溶融や不完全な融合を避けるために、できるだけ規則的である必要があります。溶接パラメータと操作技術を最適化することで、溶接痕の形状を効果的に改善し、溶接品質を向上させることができます。
· 研磨処理:摩擦溶接位置で生成される凹状の溶接痕には、研磨処理を使用して滑らかな表面を確保し、製品の外観と性能の要件を満たします。
c. 溶接シーケンスの最適化
· パーティション溶接:大型製品の場合、パーティション溶接法は全体の変形を効果的に制御できます。製品をいくつかの領域に分割し、それらを順番に溶接することで、溶接プロセス中の熱集中を減らし、熱変形のリスクを減らすことができます。
· ステップバイステップの修正:溶接プロセス中に、ステップバイステップの修正方法を使用して、溶接変形を時間内に調整します。溶接プロセス中に製品の変形を継続的に測定して修正することにより、最終製品の寸法精度と形状が設計要件を満たすことが保証されます。
· 溶接パスの最適化:同じ領域での繰り返し溶接を回避し、熱入力を減らすために、溶接パスを合理的に計画します。たとえば、液体冷却プレートプロジェクトでは、溶接パスを最適化することで、溶接プロセス中の熱入力が減り、溶接品質が向上しました。
d. 変形の協調制御
液体冷却プレートは溶接プロセス中に熱変形を起こし、製品の寸法精度が低下します。
最適化対策:
· パーティション溶接と段階的な修正方法を使用して、全体的な変形を制御します。
· 溶接パラメータを最適化し、電流と電圧を減らし、熱入力を減らします。
· 固定具を使用して製品を固定し、溶接中の動きと変形を減らします。
· 対称溶接方法を使用して、溶接熱を均等に分散します。
ご参考になるために、定期に熱設計及び軽量化に関する技術と情報を更新させていただきます。当社にご関心をお持ちいただき、ありがとうございます。
CTC(セルツーシャーシ)技術は、電気自動車の航続距離とスペース効率を大幅に向上できるため、多くの注目を集めていますが、従来のバッテリー技術を本当に置き換えることができるかどうかはまだ議論の余地があります。製造側の中心的なボトルネックであるバッテリートレイの溶接プロセスは、この技術の将来を決定する鍵となっています。複雑な構造設計、複数の材料の互換性、厳格な熱管理要件により、従来の溶接技術は大きな試練にさらされています。この記事では、第一線のエンジニアの視点から、業界のトレンドとエンジニアリングの実践を組み合わせて、CTC技術の可能性と限界を分析し、溶接技術がどのようにしてこの技術革命の「試金石」になったかを探ります。
1-CTC技術の「理想と現実」
CTC技術は、理論的にはバッテリーセルをシャーシに直接統合することで冗長な構造部品を減らし、エネルギー密度を向上させることができますが、その大規模適用の実現可能性は現実的な課題に直面しています。
自動車会社の急進性と慎重さ:テスラ、BYDなどの大手企業はCTCソリューションを立ち上げていますが、多くのメーカーはまだ様子見しています。業界データによると、2025年2月時点で、CTC量産モデルは世界の15〜20%を占めており、従来のCTP(Cell-to-Pack)技術が依然として主流です。
バッテリー寿命の向上の「コスト」:CTCはエネルギー密度を15%〜20%向上させることができますが、シャーシ構造の複雑さにより製造コストが30%〜50%増加します(コンサルティング機関による計算)。コストと利益のバランスはまだ明確ではありません。
メンテナンスの経済論争:統合設計により、バッテリーのメンテナンスコストが急騰しました。保険会社のデータによると、CTCモデルの事故後のバッテリーアセンブリの交換率は70%と高く、従来のモデルの25%をはるかに上回っています。
これらの矛盾により、CTC技術の将来は変数に満ちています。市場が20%を突破できるかどうかは、3つの主要な変数に依存します。テスラサイバートラックの量産の進捗状況、中国の自動車メーカー間の価格戦争によりCTCがコスト削減を余儀なくされるかどうか、およびバッテリーの修理可能性に関する欧州規制の妥協の程度です。製造側の溶接技術レベルは、研究室と量産の間のギャップを乗り越えられるかどうかを決定する鍵となります。
2-溶接工程の3つの「生死の壁」
バッテリートレイメーカーにとって、CTC技術の導入は3つの核心問題を克服する必要があります。
a. 「ミクロンレベル」の精度と効率の勝負
従来の溶接工程では0.5mmの誤差を許容できますが、CTCトレイではより多くのバッテリーを搭載する必要があり、継ぎ目の数は3倍以上になり、そのほとんどは湾曲した不規則な部分に分布しています。メーカーのテストによると、溶接位置の誤差が0.15mmを超えると、バッテリーセルアセンブリの歩留まりが99%から82%に急激に低下します。さらに厄介なのは、精度の向上は効率の低下を伴うことが多いことです。レーザー溶接の精度は高いものの、設備コストは従来の溶接の5倍以上です。
b. 混合材料の「水と火」
軽量と強度のバランスをとるために、CTCトレイでは「アルミニウム合金+炭素繊維+特殊鋼」の混合構造がよく使用されます。異なる材料の熱膨張係数の差は最大20倍(アルミニウム23μm/m·K対カーボンファイバー0.8μm/m·Kなど)にもなり、溶接時に内部応力が発生しやすく、割れの原因となります。ある企業がアルミニウムとカーボンファイバーを接合しようとしたところ、溶接部の割れ率は18%にも達し、業界の許容閾値である3%を大きく上回りました。
c. 熱影響部の「見えないキラー」
溶接温度が高いと、バッテリーセル周辺の絶縁材やセンサー回路が損傷する可能性があります。ある自動車会社は、溶接入熱の不適切な制御により、バッテリーモジュールの自己放電率が50%増加したことがありました。エンジニアは、溶接温度の変動を0.1秒以内に±15℃以内に制御する必要があります。これは、溶接ガンに「高精度温度ブレーキ」を取り付けるのと同じです。
3-解決策:特効薬はなく、システム革新のみ
これらの課題に直面して、業界は3つの突破口を模索しています:
a. プロセス組み合わせの「カクテルセラピー」
レーザーアークハイブリッド溶接:レーザー溶接の精度とアーク溶接の浸透の利点を組み合わせることで、アルミニウム合金の溶接速度が40%向上します。
冷間金属遷移技術(CMT):正確な入熱制御により、熱影響部の面積が60%減少します。
ロボットインテリジェント補正システム:リアルタイムの溶接スキャンデータに基づいて溶接ガンのパスを自動的に調整し、複雑な曲面溶接の合格率を75%から95%に向上します。
b. 材料面での「事前妥協」
一部の企業は、材料サプライヤーと共同で「溶接に適した」複合材料の開発を開始しています。例えば、国内の改良アルミ合金(物理的、化学的、またはプロセス手段によって調整されたアルミ合金材料)の溶接割れ感受性は、レベル7からレベル3(ISO規格による)に低下しました。軽量化効果は5%犠牲になりますが、溶接歩留まりは98%に向上します。
c. 検出次元の「デジタルツイン」
溶接プロセスのすべてのデータ(電流、温度、速度など)を収集し、AIモデルと組み合わせて欠陥の確率を予測します。ある工場がこの技術を導入した後、溶接欠陥のオンライン検出率は80%から97%に向上し、スクラップコストは45%削減されました。
4- エンジニアの新たな提案:不確実性の中に確実性を見出す
a. CTC 技術をめぐる論争は、本質的には「システム最適化」と「局所的限界」の間のゲームです。
溶接プロセスのブレークスルー速度が自動車会社のコスト削減期待よりも遅い場合、CTC はニッチな技術になる可能性があります。
材料、プロセス、テスト技術が協調してブレークスルーを達成した場合、電気自動車の構造設計の新しい時代が到来すると予想されます。
b. エンジニアにとって、次の 2 つの側面から能力を再構築する必要があります。
クロスドメイン知識の統合:溶接熱入力に対する電気化学特性の敏感な閾値を理解する。
アジャイル対応能力:ヨーロッパのサプライヤーのケーススタディでは、新しい合金材料の溶接パラメータの最適化を 1 週間以内に完了できるチームは、受注の確率が 3 倍に増加することが示されています。
CTC 技術は、「破壊的イノベーション」と「大量生産の罠」の岐路に立っています。既存の技術を完全に置き換えることはできないかもしれませんが、溶接プロセスをより高い精度、より強力な互換性、よりインテリジェントな制御に向けて進化させています。この技術マラソンで本当の勝者は、最も早くこの技術を開発した自動車会社ではなく、製造側で「不可能な溶接」を「標準化されたインターフェース」に変えるエンジニアリング チームかもしれません。
ご参考になるために、定期に熱設計及び軽量化に関する技術と情報を更新させていただきます。当社にご関心をお持ちいただき、ありがとうございます。
CTP(セル・トゥ・パック)技術が従来のバッテリーパック構造を完全に覆すにつれて、バッテリートレイの「役割」は受動的な荷重支持から能動的な統合へと移行しました。溶接技術は安全性と性能の中核となっています。軽量(壁厚はわずか1.5mm)、気孔ゼロの密閉、マルチマテリアル(アルミニウム/銅/カーボンファイバー)統合の要件により、従来の溶接は変形と欠陥のジレンマに陥っています。業界は、材料の革新、インテリジェントな品質検査、プロセスの反復を通じて飛躍的な進歩を遂げています。この記事では、CTPが溶接にもたらす破壊的な課題を分析し、高精度と高信頼性への技術的な道を探ります。
1-CTP技術によるバッテリートレイの構造設計要件の変化の分析
CTP(Cell to Pack)技術は、従来のバッテリーパックのモジュール構造を排除し、バッテリーセルをバッテリーパックに直接統合します。この技術革新は、バッテリートレイの構造設計に対する全面的かつ多次元的なアップグレード要件を提示しています。以下は、材料、性能、プロセス、統合などの観点からの具体的な分析です。
(1)構造強度と耐衝撃性能の総合的な向上
a. モジュールを排除した後の機械的支持要件:
CTP技術によりモジュール構造が排除された後、バッテリートレイはバッテリーセルのサポート、固定、外力緩衝機能を直接担う必要があります。従来のモジュールは機械的負荷を分散しますが、CTPトレイは充電および放電中にバッテリーセルの膨張変形を全体として吸収する必要があります(たとえば、角型バッテリーセルの膨張力は10〜20kNに達することがあります)。また、車両走行中の振動、押し出し、衝撃負荷に耐えます。
b.材料と構造の最適化方向
· 高強度アルミ合金の優位性:初期の鋼は重量が重いため徐々に置き換えられ、6061-T6が主流になりました。比強度が高く、耐腐食性が強く、軽量と高剛性の2つの要件を満たすことができます。
· 複合構造設計:たとえば、Leapmotorの「ダブルフレームリングビーム」構造は、縦方向と横方向のビームコンパートメントを通じて局所的な耐衝撃性を高めると同時に、押し出し技術を使用して材料の分布を最適化し、余分な重量を減らします。
· マグネシウムアルミニウム合金と炭素繊維の探求:マグネシウムアルミニウム合金は従来のアルミニウム材料よりも30%軽量で、炭素繊維複合材料は高強度と軽量の両方の特性を備えていますが、コストとプロセスの成熟度のため、現在はハイエンドモデルにのみ使用されています。
(2)統合気密性と熱管理の要件
a. 密閉性能の向上
モジュールを取り外した後、バッテリーパックの内部冷却剤循環とガス密閉は完全にトレイに依存し、溶接欠陥(気孔や亀裂など)により漏れのリスクが生じる可能性があります。
図1-バッテリートレイの気密性テスト
b. 熱管理機能の統合
CTP トレイには、液体冷却プレートや熱伝導性接着剤などのコンポーネントを統合する必要があります。たとえば、構造用接着剤はバッテリー セルを固定して膨張応力を伝達するために使用され、ポリウレタン熱伝導性接着剤 (熱伝導率 > 1.5 W/m·K) はバッテリー セル間および液体冷却チューブとの熱伝導に使用されます。1 つの PACK で使用される接着剤の量は、従来の構造よりも 50% 以上多くなります。トレイ内に流路を設計して冷却効率を最適化し、溶接の熱影響部によるシーリングの損傷を回避する必要があります。
(3) 軽量化と材料の革新
a. 材料選択の傾向
アルミニウム合金の押し出しおよびダイカスト プロセス: 押し出しアルミニウム プロファイルはフレーム構造 (Tesla の 4680 バッテリー トレイなど) に使用され、ダイカスト プロセス (統合ダイカストなど) は溶接プロセスを簡素化し、重量を 15% ~ 20% 削減します。
プラスチック複合材料の応用:例えば、非荷重部品にはガラス繊維強化PA6材料を使用し、さらなる軽量化を図っていますが、金属接続インターフェースとの互換性の問題を解決する必要があります。
b. 軽量設計戦略
トポロジー最適化:CAEシミュレーションにより冗長材料を削減し、強度を確保しながらトレイの重量を削減します。
薄肉・一体化:トレイの壁厚を3mmから1.5~2mmに減らし、BMSブラケットやワイヤーハーネスチャネルなどの機能部品を一体化して部品点数を削減します。
(4)一体化・モジュール設計
a. 機能部品の高一体化
CTPトレイには、バッテリー管理システム(BMS)、高電圧コネクタ、耐火絶縁層などのモジュールを一体化する必要があります。
b. モジュール化・互換設計
溶接生産ラインは、複数モデルのトレイの混合生産をサポートし、「ワンクリックタイプ変更」を実現でき、異なるバッテリーセルサイズ(角型や円筒型など)のトレイ構造と互換性がある必要があります。
2-CTP 技術革新による溶接プロセスへの特有の課題
CTP (Cell to Pack) 技術は、スペース利用率とエネルギー密度を大幅に向上させましたが、溶接プロセスに前例のない課題ももたらしました。
(1) 溶接欠陥の制御の難しさが急激に増加
a. 気孔とシーリングの課題
CTP 技術によってモジュールがなくなった後、バッテリー トレイはシーリング機能を直接担う必要があります。溶接気孔 (アルミニウム合金溶接でよく見られる欠陥) は、冷却剤の漏れやガスの浸透のリスクに直接つながります。
b. 亀裂と材料の適合性
亜鉛含有量の高いアルミニウム合金 (7 シリーズなど) は、溶接時の熱応力により亀裂が生じやすくなります。
c. ギャップと組み立てエラー
複数のセルを直接統合すると、トレイ構造の接合点の数が増えます。組み立てエラーが蓄積すると、溶接ギャップが ±1mm を超える可能性があります。
(2) 材料システムのアップグレードによってもたらされるプロセス適応の問題
a.軽量材料の溶接の課題
CTPトレイの材料は、鋼からアルミニウム合金(6061-T6、7075-T6)、マグネシウムアルミニウム合金(30%軽量化)、炭素繊維複合材料に移行しています。アルミニウム合金の溶接では、酸化膜の溶融の難しさと高い熱伝導率によって引き起こされる浸透不足の問題を解決する必要があります。
b. 異種材料接続技術
トレイに液体冷却プレート(銅/アルミニウム)や耐火層(セラミックマトリックス複合材料)などの機能部品を統合すると、異種材料の界面に脆い金属間化合物が発生しやすくなります。
(3)構造の複雑さと精度要件の向上
a. 大型薄肉構造の変形制御
CTPトレイの壁厚は3mmから1.5〜2mmに減少し、溶接熱変形の感度が大幅に増加します。
b.高密度のはんだ接合部とプロセス効率
1 つのトレイ上のはんだ接合部の数は、従来のモジュールの 2,000 個から 5,000 個以上に増加しました。
図2-バッテリートレイの溶接
3-生産プロセスと品質管理のアップグレード
CTP技術は、バッテリートレイ溶接の「単一プロセス」から「マルチテクノロジーコラボレーション、インテリジェント化、グリーン化」への変革を促進します。メーカーは、次の3つの主要な方向に重点を置く必要があります。
技術アップグレード:気孔や亀裂などの欠陥の制御を突破し、軽量材料に適応します。
インテリジェント移行:プロセス全体のデジタル化とAI品質検査により、高精度の生産を実現します。
エコロジカルコラボレーション:材料サプライヤー、機器サプライヤー、OEMと共同で技術標準を構築します。
ご参考になるために、定期に熱設計及び軽量化に関する技術と情報を更新させていただきます。当社にご関心をお持ちいただき、ありがとうございます。
アルミニウム合金などの軽量材料は、その優れた性能により主流となっています。しかし、薄板溶接における入熱制御、変形抑制、プロセス安定性などの課題は、従来の溶接技術にとって大きな障害となっています。コールドメタルトランスファー(CMT)溶接は、入熱が低く、スパッタのない移行、インテリジェントなパラメータ制御という利点があり、バッテリートレイ製造に革新的なソリューションを提供します。
この記事では、バッテリートレイの薄板溶接におけるCMT技術の精密制御戦略を詳しく調べ、その適応性、プロセスの課題、複合アプリケーションシナリオを分析し、効率的で高品質な生産のための理論的かつ実践的なガイダンスを提供することを目指しています。
図1: 104Sエネルギー貯蔵バッテリー液体冷却下部筐体のCMT溶接
1-バッテリートレイ溶接要件とCMT適応性
CMT技術は、低入熱、スパッタフリーの伝達、インテリジェントなパラメータ制御を備えており、バッテリートレイ溶接の高精度、低変形、効率の要求に完全に適合しています。
(1)バッテリートレイ溶接のコアプロセス要件
a. 材料の適合性と軽量化のニーズ
バッテリートレイでは、主に軽量アルミニウム合金(6xxxシリーズ、6061など)または高級モデル用の炭素繊維複合材が使用され、高強度(ベース材料の引張強度の60%~70%)と低密度(アルミニウム合金:2.7g/cm³)が求められます。
異種材料の接合:ハイブリッドスチールアルミニウム構造の場合、変形を最小限に抑えるために熱膨張係数の違いに対処する必要があります。
b. 溶接品質とパフォーマンスメトリクス
低入熱と変形制御:薄板(0.3~3mm)の場合、変形は≤2mmである必要があります。長い直線溶接には、セグメント溶接または変形防止設計が必要です。
シーリングと強度: 電解液の漏れを防ぎ、せん断試験に合格するために、溶接は完全に密封する必要があります (例: T/CWAN 0027-2022 規格)。
気孔率の制御: アルミニウム合金の溶接は気孔が発生しやすいため、気孔率は 0.5% 以下である必要があります。
c. 生産効率と自動化の要件
バッチ生産では、溶接速度が 7mm/s 以上である必要があり、シングルトレイ溶接の時間が 5~10 分に短縮されます。
自動化されたワークステーションは、デュアルステーション設計 (同時組み立てと溶接) とマルチロボットのコラボレーションをサポートする必要があります。
(2)バッテリートレイ溶接におけるCMTの主な利点
a. 高精度の低入熱制御
CMTは、溶滴短絡時に溶接ワイヤを後退させて電流を遮断することで、従来のMIG溶接に比べて入熱を33%削減し、極薄プレート(0.3mm)の溶損リスクを排除します。
交互の冷熱サイクル(アーク加熱-溶滴移動-ワイヤ後退)により、熱蓄積を最小限に抑え、変形を≤1.5mmに制御します(BYDおよびBAICのケーススタディ)。
b. プロセスの安定性と品質の向上
スパッタフリー溶接:機械的な後退により、溶滴のスパッタがなくなり、手直しが減ります。
気孔率の最適化:Ar+30%Heシールドガスを使用すると、気孔サイズが≤0.3mmで、純粋なArに比べて気孔率が50%削減されます。
高いギャップ許容度:最大1.5mmのアセンブリギャップに対応し、固定具の精度要件を下げます。
c.自動化の統合と効率の向上
デュアルステーションワークステーション(例:Taixiang Tech 設計)により、並行溶接と組み立てが可能になり、効率が 2 倍になります。
変形防止設計による対称ロボット溶接(デュアルロボット同期)により、サイクル時間が 10 分以下に短縮されます。
2-バッテリートレイのCMTプロセスにおける課題
図2: CMT溶接プロセスフロー
(1)材料特性と溶接欠陥制御
a. アルミニウム合金溶接における気孔感受性
アルミニウム合金トレイ(例:6061、6063)は、急速凝固と水素溶解度の変化により気孔が発生しやすくなります。シールドガスの組成は重要です。純粋なArでは気孔率は約5%ですが、Ar+30%Heでは気孔率は≤0.5%に低下します。インダクタンス調整(例:ネガティブチューニング)により溶融池の流れが最適化され、気孔サイズが最小限に抑えられます。
b. 高温割れと組成偏析
アルミニウム合金中のMg、Siなどの偏析は粒界脆化を引き起こす可能性があります。CMTの低入熱によりHAZは減少しますが、不十分な溶け込みや局所的な過熱を回避するには、溶接速度とワイヤ供給を正確に制御する必要があります。
c.異種材料溶接における冶金適合性
Al-鋼またはAl-複合材料接合部(クラッシュビームやエンクロージャなど)の界面では、脆性相(FeAl₃など)とZn蒸気の干渉を軽減する必要があります。
(2)プロセスパラメータ最適化の課題
a. 溶け込みと入熱のバランス
溶接は、溶け込み深さ(≥0.8mm)に関するT/CWAN 0027規格を満たす必要があります。CMTの入熱が低いと溶け込みが不十分になる可能性があり、溶け込みを強化するためにアーク長の調整またはパルス電流が必要になります。
b. 速度と安定性のトレードオフ
自動化ラインでは1.2m/分以上の速度が必要ですが、高速ではアークが不安定になったり、溶滴が不均一に転移したりするリスクがあります。
c. 複雑な溶接におけるギャップブリッジ
トレイには、大きなギャップ(0.5~1.5mm)や不規則なジョイント(Tジョイントなど)がよく見られます。
(3)構造設計と製造プロセスの互換性
a. 薄板溶接の変形制御
アルミ合金パレットの壁厚は通常2〜3mmです。従来のMAG溶接の変形は1.2mmに達することがありますが、CMT溶接は低入熱により変形を0.3mm未満に抑えることができます。ただし、精度をさらに向上させるには、変形防止ツール設計とロボット対称溶接(ダブルステーションワークステーション)との連携が必要です。
b. 長い溶接の連続性と密閉
バッテリートレイの密閉溶接の長さは数メートルに達することがあり、アークの破断や溶融池の変動を避ける必要があります。CMT技術は、1秒あたり70回以上のアーク再点火サイクルを通じて溶接の均一性を確保し、レーザー追跡システムにより気密性合格率を99%まで高めることができます。
c.マルチプロセス複合アプリケーションの相乗効果
高級パレットでは、CMT+FSW(摩擦攪拌接合)複合プロセスがよく使用されます。CMTは複雑な構造(フレームと底板の接続など)に使用されます。FSWは高負荷領域(縦梁など)で強度を向上させるために使用されます。2つのプロセスの接続パラメータ(予熱温度や溶接後の熱処理など)のマッチングの問題を解決する必要があります。
3-バッテリートレイ製造におけるCMTプロセスの典型的な適用シナリオ
(1) バッテリートレイの主要構造の接続
a. フレームと底板の溶接
CMTプロセスは、アルミニウム合金バッテリートレイのフレームと底板の接続に広く使用されており、特に長い溶接部と薄いプレート(厚さ2〜3mm)に使用されます
b. ビームと底板の接続
CTPバッテリートレイの設計では、ビームの数が少なく構造が複雑なため、CMTプロセスは次の目的で使用されます:高精度の位置決め溶接:ビームと底板(Tジョイントなど)のローカル接続では、浸透不足を回避する必要があります。CMTは、デジタルアーク長制御(Fonis CMT Advancedテクノロジーなど)により、安定した浸透≥ 0.8mmを実現します。マルチマテリアル適応:ビームがアルミニウムマグネシウム合金(6061など)で作られ、底板が高強度アルミニウムである場合、CMTはAr+He混合ガス保護を通じて気孔を減らし、異なる材料の熱伝導率の違いに適応できます。
(2) 薄板および複雑な幾何学的構造の溶接
a. 薄壁アルミ合金溶接 (2-3mm)
バッテリートレイの軽量化の要求により薄板の適用が促進されますが、従来の MIG 溶接は変形しやすい傾向があります。CMT プロセスの利点は次のとおりです。
b. 超薄板溶接: Taixiang Automation は CMT 技術を使用して、バッテリートレイのエッジシール構造用の 0.3mm の超薄板のスパッタフリー溶接を実現します。
c. 特殊形状溶接のブリッジ: トレイの内部補強リブや衝突防止ビームなどの特殊形状構造の場合、CMT ギャップブリッジモードは、ワイヤの引き込みとアークの方向転換により 0.5-1.5mm のギャップを埋め、未融合欠陥を回避できます。
d. 高いシール要件の溶接: バッテリートレイのシールは、バッテリーの安全性に直接関係しています。 CMT プロセスは、次の方法でこれを保証します:
· 連続した長い溶接: 1 秒あたり 70 回以上のアーク再点火サイクル (Fronius LaserHybrid テクノロジーなど) を使用して、数メートルの溶接の連続性を確保し、気密合格率は 99% です。
· 低入熱制御: レーザー溶接と比較して、CMT は入熱が低いため、溶融池の変動によるシーラント層への熱影響が軽減され、接着剤コーティング プロセスに適しています。
(3) マルチプロセス複合製造シナリオ
a. CMT+FSW 複合プロセス
ハイエンドのバッテリートレイ生産ラインでは、CMT は摩擦撹拌溶接 (FSW) と連携することがよくあります。
分業と協力: CMT は複雑な構造 (フレームや特殊形状のジョイントなど) の柔軟な溶接に使用され、FSW は高負荷領域 (縦梁など) に使用され、強度が向上します。たとえば、上海 Weisheng の自動化生産ラインでは、CMT+FSW+CNC の組み合わせを使用して、トレイの生産効率を 30% 向上させています。
プロセス接続の最適化: Huashu Jinming の生産ラインはモジュール設計を採用しており、予熱パラメータのマッチング (CMT 溶接後の 150°C への局所加熱など) により、FSW とのシームレスな接続を実現しています。
b. FDS/SPRリベット技術との組み合わせ
第2世代CTP技術では、CMTは摩擦セルフタイトニング(FDS)とセルフピアスリベット(SPR)技術と連携しています。ハイブリッド接続ソリューション:たとえば、フレームと底板の耐荷重領域にはFSWを採用し、取り外し可能な部品(水冷プレートや絶縁層など)はCMT溶接で事前配置してからFDSリベットで固定し、強度とメンテナンスの利便性の両方を考慮しています。
ご参考になるために、定期に熱設計及び軽量化に関する技術と情報を更新させていただきます。当社にご関心をお持ちいただき、ありがとうございます。
新エネルギー車およびエネルギー貯蔵分野の爆発的成長により、電池トレイ溶接技術は製造プロセスの核心戦場に位置づけられています。アルミニウム合金の軽量化と複雑構造という二重の課題に直面する中、本稿ではプロセスの本質から工学的実践までを深掘りし、従来の溶融溶接、摩擦攪拌接合(FSW)、レーザー溶接の原理、性能指標、適用シーンを比較します。熱影響域(HAZ)、接合強度、耐食性などの多角的分析を通じて、各溶接技術の優劣を明らかにします。
1-技術原理の比較
a. 従来の溶融溶接
原理: アークやプラズマアークなどの熱源により接合部を局所加熱し、溶融状態の溶融池を形成。冷却後に凝固して溶接ビードを形成します。保護ガス(CO₂、アルゴンなど)やフラックスを用いて酸化を防止し、必要に応じて溶加材(ワイヤやロッド)を添加します。
特徴: 溶融池の温度が高く冷却速度が速いため、粗大な柱状晶が発生。熱影響域(HAZ)が広く、冶金反応が不十分で、気孔や割れなどの欠陥が生じやすい。
b. 摩擦攪拌接合(FSW)
原理: 高速回転する攪拌ピンとワークの摩擦熱を利用し、材料を熱可塑状態にします。機械的な攪拌と塑性流動により固相接合を実現。溶融池を形成せず、溶加材も不要です。
特徴: 材料の融点より約80%低い温度で接合。動的再結晶により微細な等軸晶が形成され、気孔のない緻密な溶接部を実現。熱入力が低く変形が小さい。
c. レーザー溶接
原理: 高エネルギー密度のレーザービームをワーク表面に集中照射し、熱伝導(出力密度<10⁵ W/cm²)または深熔融溶接(出力密度≥10⁵ W/cm²、キーホール効果)により材料を溶融・接合します。
特徴: 熱影響域(HAZ)が極めて狭く、溶込み深さが大きく、高速溶接が可能。ただし材料表面の反射率に敏感で、プロセスパラメータの厳密な制御が必要。
a-従来の溶融溶接 b-摩擦攪拌接合 c-レーザー溶接
図1 電池トレイの主要溶接技術の原理
2-性能指標の比較
a. 熱影響域(HAZ)の比較
キーポイント分析:
従来の溶融溶接: 高熱入力によりHAZが広く、結晶粒の粗大化や冶金欠陥(気孔)が材料性能を低下させる。
FSW: 固相接合により溶融池がなく、HAZはTMAZとHAZに分かれ、微細結晶(NZ)と局所変形(TMAZ)が共存。
レーザー溶接: 高エネルギー密度と急速冷却によりHAZ幅が極狭(約0.1-0.5mm)。ただしキーホール効果による組織均一性への影響に注意。
b.接合強度の比較
キーポイント分析:
従来の溶融溶接: 急速凝固による粗大結晶と欠陥で接合強度が低下(例:MIG溶接のアルミ合金は母材強度の72.8%)。
FSW: 動的再結晶で微細結晶(NZ)を形成するが、TMAZの結晶粒変形やHAZの強化相溶解が弱点に。
レーザー溶接: 高冷却速度により結晶粒粗大化を抑制、母材に近い強度を実現。
c. 耐食性の比較
キーポイント分析:
従来の溶融溶接: 粗大結晶と欠陥によりHAZや溶融線で腐食が優先発生。
FSW: NZは微細結晶と均質化で耐食性が高いが、HAZの結晶粗大化や第二相析出(Fe含有相など)が腐食の弱点に。
レーザー溶接: 狭いHAZと均一組織で腐食活性点が少ないが、表面酸化層の影響に注意。
3-適用シーン
a. 従来の溶融溶接
・ 適用部位:
フレームと底板の接合: 電池トレイの主要構造(例:BYD、北汽の車種でアルミ型材フレームと底板を断続溶接または全溶接)。
補助部品の補修溶接: 複雑構造や空間制限のある辺梁・補強材などで他技術(FSWなど)と併用。
・ 適用工件:
厚板溶接(鋼製トレイやアルミ厚板)。
非密閉性の補助構造(電池パックの角部固定部品など)。
・ 適用材料:
アルミニウム合金: 6061-T6などの6シリーズ厚板(接合強度は母材の70%-80%)。
鋼材: 鋼製トレイのフレーム溶接(コスト低但し重量大)。
・ 制約:
高熱入力による変形が大きく、高精度・薄板溶接には不向き。
b. 摩擦攪拌接合(FSW)
・ 適用部位:
底板の長手継ぎ: アルミ合金トレイの底板の長い溶接継手、水冷チャネルの一体構造など(例:Guangdong Walmate Tech の水冷チャンネル一体構造)。
高密閉性領域: 電池トレイと箱体の接合部(FSWの気孔なし溶接で密閉性確保、吉利・Xpeng車種の両面FSW構造)。
複雑型材接合: アルミ押出型材のT型接合・中空型材溶接(両軸ショルダーFSW技術で自立溶接可能)。
・ 適用工件:
アルミ押出型材(例:底板厚10mm・壁厚2mmの二重断面設計)。
異種材料接合(Al/Cu、Al/Mgなど、特殊プロセス調整必要)。
・ 適用材料:
アルミニウム合金: 6061-T6、6005A-T6、6063-T6が主流(接合強度は母材の80%-90%)。
マグネシウム合金: 軽量トレイ(例:瑞松科技事例)但し結晶粒粗大化防止のため熱入力制御要。
・ 技術優位性:
溶融欠陥を回避した固相接合で、軽量化・高密閉性シーンに適す。
c-レーザー溶接
・ 適用部位:
高強度鋼トレイの重要接合部: 車体との接合など高応力領域。
精密シールピン溶接: トレイ蓋板のシールピン溶接(速度40mm/s、HAZ極狭)。
薄板接合: アルミ/鋼製トレイの薄板(<3mm)高効率接合(変形低減)。
・ 適用工件:
高精度・自動化ライン(ロボットレーザー溶接システム)。
曲面溶接など異形構造(高速位置決めシステム併用要)。
・ 適用材料:
高強度鋼: 引張強度≥1000MPa(母材強度の95%保持)。
アルミニウム合金: 反射率低減のため表面処理(陽極酸化など)必要(コスト高)。
・ 制約:
厚板溶接(例:アルミ>8mm)は多パス必要でFSWより効率低下。
ご参考になるために、定期に熱設計及び軽量化に関する技術と情報を更新させていただきます。当社にご関心をお持ちいただき、ありがとうございます。
私はバッテリートレイメーカーの第一線エンジニアとして、複数の新エネルギー車用バッテリーシェルプロジェクトに参加し、「軽量・安全・コスト」の三角関係における業界の駆け引きを深く理解しています。この記事では、材料ルート、製造プロセス、将来の動向という3つの側面から、現在の技術ルートの選択ロジックと産業化の課題を分析し、実際の事例を組み合わせます。
1-材料ルート:軽量化とコストのトレードオフ
バッテリーシェルの材料の選択は、車両全体の性能と経済性に直接影響します。現在の主流ルートは、アルミニウム合金、高強度鋼、複合材料の3つのカテゴリにまとめられ、それぞれに独自の適用シナリオがあります。
a. アルミニウム合金ルート:軽量化の主力
· 押し出しアルミプロファイル:BYDの多くのモデルのバッテリーシェルは押し出しアルミプロファイルで作られており、断面形状を最適化することで軽量化を実現し、構造剛性を向上させています。
· ダイカスト統合:テスラの4680バッテリーはCTC技術と組み合わせて50%以上の軽量化を実現していますが、金型コストは2億元を超え、コストを希釈するには年間50万個以上の生産が必要であり、大手自動車会社の大規模生産に適しています。
· 複合アルミニウム:ポルシェ タイカンはアルミニウムと炭素繊維のハイブリッド構造を採用し、重量がさらに 15% 軽減されますが、コストが 30% 増加し、高級モデルに限定されます。
b. 高強度鋼ルート:コストに敏感な市場での反撃
熱間成形鋼(22MnB5 など)は、降伏強度が 1500MPa、商用車への浸透率が 40% を超え、1GWh あたりのコストがアルミニウムより 40% 低くなりますが、エネルギー密度が約 8% 犠牲になります。そのため、コストと基本的な安全性の両方を考慮して、10 万元未満のモデルでは高強度鋼が一般的に使用されます。
c.複合材料:ハイエンドの試み
· SMC材料:バッテリーパックの上部シェルはガラス繊維強化複合材料を使用しており、スチールより30%軽量ですが、耐衝撃性の欠点は厚さを増やすことで補う必要があります(3mm+5mmの補強)。
· 炭素繊維:BMW i3のシェルはアルミニウムより50%軽量ですが、コストは800元/ kgと高く、大量生産は困難です。現在は高級モデルにのみ使用されています。
実践の要約:材料の選択はモデルの位置付けに合わせる必要があります。ミッドレンジ市場(20万〜30万元)は主にアルミニウムベースの材料であり、ローエンド市場は高強度鋼に依存し、高級モデルは炭素繊維複合ソリューションを模索しています。
2- 製造プロセス:効率と信頼性のバランス
バッテリーシェルの製造プロセスは、生産効率と製品の信頼性に直接影響します。現在主流の技術ルートには、ダイカスト、押し出し溶接、構造統合技術が含まれます。
a. ダイカストvs.押し出し溶接
· 押し出しアルミプロファイル(GMボルトが使用):1個あたりのコストは約800元で、大量生産に適していますが、プロセスが複雑です。
· ダイカストアルミ(NIO ET5):1個あたりのコストは1,500元ですが、生産効率は5倍に向上し、急速な生産需要に適しています。
· 摩擦撹拌溶接(FSW):従来のアーク溶接と比較して、変形が50%減少し、耐疲労性が30%向上しますが、設備投資を40%増やす必要があり、寿命要件の高い商用車に適しています。
b.構造統合技術
· CTPモジュール化(CATL Kirinバッテリー):スペース利用率が72%から85%に向上し、コストが15〜20%削減されましたが、熱暴走防止設計を強化する必要があります。
· CTCシャーシ統合(Tesla Model Y):部品が370個削減され、バッテリー寿命が54%増加しましたが、メンテナンスコストが300%増加し、アフターサービス体制に課題が生じています。
主要データの比較
生産ラインの経験:CTP 技術は互換性が高いため、現在でも主流ですが、CTC は自動車会社とバッテリーメーカーの緊密な連携が必要であり、短期間で普及する可能性は低いです。
3- 将来の動向:技術統合とインテリジェントアップグレード
a. 材料複合
アルミニウム/カーボンファイバーハイブリッドシェル(ポルシェタイカンコンセプトなど)は、重量を15%削減し、800MPaの圧縮強度を達成できますが、界面の結合強度は25MPa以上である必要があり(トヨタbZ4Xの量産認定率はわずか65%)、プロセスの安定性を突破する必要があります。
b. 機能統合イノベーション
· 液体冷却プレートとシェルの統合(GACマガジンバッテリー):冷却接触面積が50%増加し、温度差制御が<5℃ですが、アルミニウムと銅の異種溶接多孔度をレーザースイング溶接で最適化する必要があります。
· 組み込み光ファイバーセンサー(コンチネンタルグループのソリューション):シェルのひずみと温度をリアルタイムで監視し、BMS応答速度が30%向上しましたが、センサーの耐久性の問題を解決する必要があります。
c.グリーン循環システム
BMWのリサイクルアルミニウムの閉ループリサイクル技術は、炭素排出量を60%削減しますが、リサイクル材料の性能損失を10%以内に抑える必要があります。さらに、大型薄肉ダイカスト(LK 9000Tダイカストマシンなど)では、金型温度差(±5℃)の精密制御が必要であり、バリ洗浄効率が量産のボトルネックになります。
プロセスのブレークスルーの方向性:
·複合材料成形サイクルの圧縮(LGF-PP射出成形サイクルを180秒から90秒に短縮する必要があるなど)
·デジタルツイン技術を適用して衝突シミュレーションエラーを±20%から±5%に削減し、設計の信頼性を向上します。
4- 市場の階層化と産業化の見通し
短期(1~3年):CTP+押し出しアルミプロファイルは依然として主流であり、CATLは34%の市場シェアで引き続きリードしています。
中期(5~10年):CTCと炭素繊維はハイエンド市場への浸透を加速しており、2030年には炭素繊維が25%を占めると予想されています。
長期目標:エネルギー密度は400Wh/kgを突破し、同時に国家標準の30分間の熱暴走保護に基づいて、安全性の冗長性をさらに向上させます。
5-結論
バッテリーハウジングの技術ルートを選択する際の本質は「シナリオに基づく適応」であり、自動車会社の位置付け、コスト閾値、サプライチェーンの成熟度を総合的に考慮する必要があります。エンジニアとして、私たちは材料とプロセスの革新を受け入れ、大量生産の実現可能性にも焦点を当て、軽量化、安全性、コストの動的なバランスの中で最適なソリューションを見つけなければなりません。将来、インテリジェントでグリーンな製造技術の成熟に伴い、バッテリーハウジングは徐々に「受動的な保護」から「能動的な安全」へと移行し、新エネルギー車の完全な普及にしっかりとしたサポートを提供します。
ご参考になるために、定期に熱設計及び軽量化に関する技術と情報を更新させていただきます。当社にご関心をお持ちいただき、ありがとうございます。
実際の製造、組み立て、使用のプロセスでは、バッテリートレイの絶縁耐電圧障害が頻繁に発生し、新エネルギー産業の急速な発展に隠れた暗礁のように、車両の運転安全性とエネルギー貯蔵システムの信頼性の高い動作を脅かしています。この記事では、製造の実践に基づいて典型的な障害モードを分析し、関連する実務者に表面的な参考資料を提供し、業界の同僚が共同でバッテリートレイの絶縁耐電圧性能を向上させる効果的な方法を模索するのに役立ちます。
パート 3 - 一般的な故障分析
図1 絶縁耐電圧試験
1- 一般的な故障メカニズムの分析
エネルギー貯蔵用バッテリートレイと新エネルギー自動車用バッテリートレイの適用シナリオは異なり、絶縁耐電圧要件と故障条件には共通点と相違点の両方があります。次のようになります。
a. 相違点
動的負荷: 新エネルギー自動車は 20~2000Hz の高周波機械的振動に対処する必要がありますが、エネルギー貯蔵システムは主に長期の静的変形に直面し、累積変形時間は 10 年を超えます。
電圧レベル: 新エネルギー自動車用バッテリートレイの絶縁耐電圧は 3000VDC 以上 (GB 38031 に基づく) に達する必要がありますが、エネルギー貯蔵システムには 4200VAC 以上の絶縁耐電圧が必要です (IEC 61439 に基づく)。
故障加速要因: 新エネルギー自動車は年間 2000 回以上の充放電サイクルにより熱応力を生じ、絶縁故障を加速します。エネルギー貯蔵システムは24時間365日稼働し、年間平均稼働時間は8000時間を超えているため、電気化学的劣化が起こり、絶縁不良が加速します。
b. 共通点
どちらも、絶縁抵抗モニタリング(低温状態で100MΩ以上、高温状態で1MΩ/kV以上)と部分放電制御(5pC未満)を通じて、絶縁不良の早期警告を実現する必要があります。
2- バッテリートレイの絶縁耐電圧不良を引き起こす一般的な製造欠陥
(1) 絶縁耐電圧構築段階
a. 潜在的な不良と原因分析
· 材料欠陥:
原因: 絶縁材料の耐電圧レベルが不十分、湿気または表面汚染 (油汚れ、金属片) による劣化。
性能: 絶縁抵抗が低い (<100MΩ)、漏れ電流が標準を超える、または耐電圧テスト中に直接破壊。
· プロセスの問題:
原因: 残留金属片 (粗い溶接/切断プロセス)、絶縁コーティングの厚さが不均一または未硬化。
性能: 部分放電、絶縁層の損傷により短絡が発生する。
· 環境干渉:
原因: 高温と高湿度により、材料の吸湿と化学腐食が発生する。
性能: 環境によって絶縁性能が低下し、凝縮水により沿面距離が長くなる。
· テストエラー:
原因: テスト電圧/時間の設定が間違っている (GB/T 38661 規格に準拠していないなど)、接地が不十分。
パフォーマンス: 適格性の判断ミス、またはコンポーネントへの過電圧による損傷。
b. 対応戦略
· 材料の最適化: 耐電圧が 1000V DC 以上の防湿材料 (炭素繊維複合材料など) を選択し、防汚コーティングを施します。
· プロセス管理: 自動溶接/スプレー装置を使用し、クリーンな作業場を準備します。
· 環境管理: 建設前に温度と湿度の監視装置を設置し、材料を事前に乾燥させます。
· テスト仕様: セグメント化されたテスト (500V 事前テスト + 1000V 正式テスト)、機器の校正、データの記録。
(2) モジュール設置段階
a. 潜在的な障害と原因の分析
· 組み立てエラー:
原因: 絶縁ライナーが欠落しており、ボルトが締めすぎているため絶縁層が損傷しています。
性能: モジュールとシェル間の絶縁抵抗が低く、耐電圧破壊が発生しています。
· 機械的損傷
原因: 取り扱いツールの傷、金属片が絶縁フィルムを突き刺しています。
性能: 動作中に局所的な短絡または突然の故障が発生します。
· 設計の互換性
原因: モジュールとトレイのサイズ偏差による電気的クリアランス不足。
性能: 寄生容量により電圧重畳破壊が発生します。
· 電気接続の危険性:
原因: 配線ハーネスが固定されていないためにコネクタシールが摩耗および故障します。
性能: 高電圧配線ハーネスの絶縁層が摩耗および漏れます。
b. 対策
· エラー防止設計: 位置決めピンツールを使用して取り付けミスを防ぎ、ボルトの長さをカスタマイズして締めすぎを防ぎます。
· 清掃作業: 取り付け前に掃除機で掃除し、傷防止シリコンでツールを包みます。
· 許容差シミュレーション: CAE でモジュールとトレイのマッチング度を検証し、ギャップが 10mm 以上であることを確認します。
· プロセス検査: 取り付け後、メガオームメーター (≥100MΩ) でランダム検査を行い、セグメント耐電圧テストを実行して障害点を特定します。
(3) システム統合フェーズ
a. 潜在的な障害と原因分析
· システム間インターフェース障害:
原因: コンポーネントの絶縁パラメータが一致しない (コネクタの耐電圧定格の違いなど)。
パフォーマンス: 高電圧バスバー接続の故障または BMS 干渉。
· 寄生容量の重なり:
原因: 複数のモジュールを並列接続すると、寄生容量の合計が増加し、容量上昇の影響が大きくなります。
パフォーマンス: システムレベルのテスト漏れ電流が標準を超えています。
· 環境ストレス障害:
原因: 振動により絶縁疲労が発生し、高電圧インターフェースに冷却剤が浸透します。
パフォーマンス: 動作中に絶縁抵抗が定期的に低下します。
· テストの盲点:
原因: 実際の動作条件 (高温/振動/湿度) をシミュレートできませんでした。
パフォーマンス: 実験室では合格しましたが、実際の動作では不合格でした。
b. 対策
· 互換性設計: サプライヤのコンポーネント標準を統一します。
· 寄生容量制御: ポリイミド絶縁層を追加し、SPICE シミュレーションでレイアウトを最適化します。
· 動作条件シミュレーションテスト: 「-40℃~85℃サイクル + 5Hz~200Hz振動 + 耐電圧」複合テストを実行します。
· インテリジェント監視: 統合オンライン絶縁監視モジュール、AIが潜在的なリスクを予測します。
3-絶縁耐電圧試験
絶縁耐電圧試験は安全対策であると同時に故障の原因となる可能性があります。絶縁耐電圧試験自体が不適切な操作、機器の問題、設計上の欠陥により故障を引き起こし、試験対象機器に二次的な損傷を引き起こすこともあります。
(1)試験中の一般的な故障の種類
(2)対応戦略は次のとおりです
a. テストパラメータの正確な制御
· 電圧と時間:標準に従って設定し、容量性負荷(バッテリーモジュールなど)の動的補正アルゴリズムを有効にして、容量増加の影響を抑制します。
· リーク電流しきい値:機器の仕様(≤10mAなど)に従って設定し、DC/ACモードを区別します(DCテストではより低いしきい値が必要です)。
b. 機器と操作の仕様
· 機器の校正:耐電圧テスターは6か月ごとに校正され、高電圧ラインの絶縁層は毎日目視検査されます。
· 安全な操作:テスト前に低電圧回路を強制的に切断し、ロボットアームまたは自動固定具を使用して高電圧領域に手動で触れないようにします。
c. 故障の予防と修復
· セグメント化されたテスト:モジュール内の複雑なシステムをテストし(最初に高電圧バスをテストし、次にモジュール絶縁をテストするなど)、故障ポイントを特定します。
· 故障修復: 故障後にエポキシ樹脂を使用して損傷領域を充填し、修復後に再度全電圧勾配テストに合格する必要があります (500V→1000V のステップ圧力など)。
d. 環境とデータ管理
· 環境制御: テストエリアの湿度が 75% を超えると除湿器を起動するか、環境が基準を満たすまでテストを延期します。
· データトレーサビリティ: テスト電圧、漏れ電流曲線、環境パラメータを記録し、MES システムを使用して製造バッチ番号を関連付けます。
ご参考になるために、定期に熱設計及び軽量化に関する技術と情報を更新させていただきます。当社にご関心をお持ちいただき、ありがとうございます。
バッテリートレイは、主に漏電を防止し、人員の安全を守り、バッテリーシステムの正常な動作を確保するために絶縁材料を使用します。選択する際には、材料の絶縁特性、耐熱性、化学的安定性、機械的強度を考慮する必要があります。これらの要素が組み合わさって、バッテリートレイ内の絶縁材料の適用効果が決まり、バッテリーシステム全体の安全性と信頼性に影響を与えます。
バッテリートレイの電気絶縁安全性 | パート 2 - 耐圧性能保証
図1 電気自動車のバッテリートレイ
1-絶縁材料の選択とソリューション設計
バッテリートレイの絶縁材料の選択では、材料の誘電特性、環境耐性、および機械的特性に重点が置かれます。以下は、バッテリートレイで一般的に使用される 6 つの絶縁材料とその関連情報です:
ソリューションを設計する際には、通常、アプリケーション シナリオ、パフォーマンス要件、コスト予算という 3 つの重要な要素を総合的に考慮して、適切な絶縁材料を選択する必要があります。例:
(1) アプリケーション シナリオに応じて選択: 高電圧、高電流のエネルギー貯蔵バッテリー システムでは、バッテリー トレイ側に高性能絶縁材料が必要な場合は、PI フィルム アタッチメント ソリューションを使用することをお勧めします。絶縁パフォーマンス要件が高くない場合は、絶縁パウダー スプレー ソリューションを選択できます。バッテリー トレイ底板の場合、低コストの絶縁ソリューションが求められる場合は、絶縁パウダー スプレーまたは絶縁ペイント コーティング ソリューションがより適しています。
(2) パフォーマンス要件に応じて選択: 絶縁パフォーマンス、耐高温性、耐化学腐食性などの要件が高い場合は、PI フィルム アタッチメント ソリューションがより適しています。これらのパフォーマンス要件が比較的低い場合は、絶縁パウダー スプレーまたは絶縁ペイント コーティング ソリューションでニーズを満たすことができます。
(3) コスト予算に応じて選択: コスト予算が限られている場合は、絶縁パウダー スプレーまたは絶縁ペイント コーティング ソリューションの方が経済的です。コスト予算が十分であれば、PIフィルム貼り付けソリューションを選択できます。
2-バッテリートレイ用PIフィルムの技術要件
(1) 材質: PI、ベースフィルムの厚さ0.1-0.14mm、裏面接着剤の厚さ0.03mm、PIフィルムの熱伝導率> 0.3W/(m·k);
(2) 耐圧性: AC 3000V、60S、漏れ電流≤0.5mA;
(3) (コールドペースト) 180°剥離強度≥15N/24mm;
(4) 絶縁性: DC 1500V、60S、絶縁抵抗>1000MΩ;
(5) 耐熱性および耐電解液性絶縁性能: 500℃、700V DC電圧で2mlの電解液を追加(試験面積13000mm<H>2<H>)、1時間保持、破壊なし、火花なし; (6)耐熱性と絶縁性能:500±2℃で、0.5時間連続ベーキング(マッフル炉)を行い、サンプルの全体的な形態変化プロセスは自然発火せず、サンプルは2回合格しました。表面にAC1000Vを印加し、電圧を0Vから3000Vまで10秒間増加させ、その後60秒間継続します。試験したサンプルには破壊や火花は発生しません。
(7)難燃性グレード:UL94 V-0。
(8)高温高湿:85℃、85%湿度の試験を1000時間行った後、サンプルに亀裂や変形はなく、絶縁抵抗、耐電圧値、電気強度に関する国家規格「GBT 13542.6-2006電気絶縁フィルムパート6:電気絶縁用ポリイミドフィルム」の要件を満たしています。未老化材料と比較して、引張強度、破断伸び、剥離強度は30%未満低下しています。
(9) 高温および低温衝撃: 85℃で1時間、-40℃で1時間切り替え、その後85℃で切り替えて高温および低温サイクルを実施します。切り替え時間は1時間に含まれ、切り替え時間は≤3分です。1000時間の高温および低温サイクル後、サンプルにはひび割れや変形がなく、絶縁抵抗、耐電圧値、および電気強度の要件に関する国家標準「GBT 13542.6-2006電気絶縁フィルムパート6:電気絶縁用ポリイミドフィルム」を満たしています。未老化材料と比較して、引張強度、破断伸び、剥離強度は30%未満低下しています。
(10)塩水噴霧試験:GB/T 10125規格の中性塩水噴霧試験(NSS)試験、温度35℃、湿度≥85%RH、試験溶液は(5±0.1%)(質量分率)NaCl、PH=6.5〜7.2、72時間連続噴霧。塩水噴霧試験後、サンプルにはひび割れや変形がなく、絶縁抵抗、耐電圧値、電気強度の要件について国家規格「GBT 13542.6-2006電気絶縁フィルムパート6:電気絶縁用ポリイミドフィルム」を満たしています。引張強度、破断伸び、剥離強度は、老化していない材料と比較して30%未満に低下しています。
(11)製品はRoHSに準拠しています。
図2 バッテリートレイ用PIフィルム
3-絶縁耐電圧試験方法とよくある問題の解決策
(1) 絶縁耐電圧試験方法
絶縁耐電圧試験は、電気機器の絶縁性能を評価する重要な手段であり、主にDC耐電圧試験とAC耐電圧試験が含まれます。DC耐電圧試験は、DC高電圧を印加して、絶縁材料が指定時間内に破壊されるかどうかを検出します。機器には、DC高電圧発生器、電圧計などが含まれます。手順は、電圧の印加、電圧の維持、電圧の低下です。AC耐電圧試験は、AC高電圧を印加します。機器と手順はDC試験に似ています。どちらの方法も、試験前に準備が必要であり、機器が適切に接地されていること、試験中に絶縁材料の表面状態が注意深く観察されていることを確認する必要があります。
(2) よくある問題と解決策
絶縁耐電圧試験でよくある問題には、絶縁破壊、過度の漏れ電流、試験機器の故障などがあります。絶縁破壊は、絶縁材料の性能不足、内部欠陥、または湿気が原因である可能性があります。解決策には、高品質の材料の選択、メンテナンスの強化、絶縁構造の改善などがあります。過度の漏れ電流は、絶縁抵抗の低下、表面の汚染、またはテスト機器の精度不足によって発生することがあります。解決策としては、絶縁材を清潔で乾燥した状態に保ち、テスト機器を校正することなどが挙げられます。テスト機器の故障は、機器の老朽化、不適切なメンテナンス、または不適切な操作によって発生することがあります。解決策としては、定期的なメンテナンス、正しい操作、およびタイムリーな修理などが挙げられます。
ご参考になるために、定期に熱設計及び軽量化に関する技術と情報を更新させていただきます。当社にご関心をお持ちいただき、ありがとうございます。
新エネルギー車やエネルギー貯蔵技術の急速な発展に伴い、中核的なエネルギーキャリアとしてのバッテリーシステムの安全性と信頼性が大きな注目を集めています。バッテリーモジュールの支持および保護構造として、バッテリートレイの電気絶縁性能は、車両の安全な操作、バッテリーの寿命、およびユーザーの個人の安全に直接関係しています。バッテリートレイの電気安全設計は、バッテリーシステムの安全性の要です。絶縁、構造、熱、監視などの多層保護により、複雑な作業条件下でのバッテリーの安定した動作を保証し、電気故障による火災、爆発、感電のリスクを軽減し、バッテリー寿命を延ばし、システムの信頼性を向上させます。
この記事では、バッテリートレイの電気絶縁安全性に焦点を当て、その設計原理、耐圧性能の検証方法、および典型的な故障ケースの根本原因分析と改善戦略を体系的に説明し、バッテリーシステムの高安全設計に理論的サポートと実用的なリファレンスを提供します。
パート1 - デザインのポイント
バッテリーシステムの電気安全設計の核心は、「予防-制御-緊急」の三位一体にあります。絶縁分離、信頼性の高い接続、熱管理などの対策により故障を防止し、センサーとBMSの助けを借りてリアルタイム制御を実現し、火災防止、圧力緩和などの設計を使用して極端な状況に対処します。メンテナンス性とコンプライアンスを考慮しながら、バッテリーシステムのライフサイクル全体にわたって安全性と信頼性を確保するには、すべての重要なポイントが連携して機能する必要があります。バッテリートレイは、バッテリーシステムの構造サポートであるだけでなく、電気絶縁、熱管理、滑り止め、機械保護、接地、モジュール設計などの複数の機能を備えており、バッテリーシステムの電気安全を確保するために不可欠です。
1-構造サポートにより電気接続の信頼性を確保
バッテリー トレイは、バッテリー モジュールを固定し、機械的ストレスを軽減し、振動と衝撃に耐え、位置合わせを維持し、環境保護と熱管理を統合することで、複雑な動作条件下での電気接続の信頼性と安全性を確保します。
図1 バッテリートレイ
A.物理的なサポートと固定により、電気接続ポイント(バスバー、配線ハーネス、コネクタなど)の正確な位置合わせが保証され、構造の変形や変位による接触不良を回避できます。バッテリーモジュールとコネクタを固定するための剛性フレームを提供し、振動や衝撃による緩みや破損を防止します。
B.環境隔離と保護:密閉設計(IP67/IP68など)により、水蒸気、ほこり、塩水噴霧などの侵入を防ぎ、腐食や絶縁不良による短絡を回避します。外部からの機械的衝撃や異物による衝撃を遮断し、高電圧接続コンポーネントを保護します。
C.熱管理の相乗効果:統合された放熱構造(液体冷却プレート、サーマルパッドなど)が温度のバランスを取り、局所的な過熱による接続ポイントの酸化や溶接を防止します。断熱設計により、隣接するモジュール間の熱干渉を減らし、温度勾配による材料の膨張差を回避します。
D.電磁両立性(EMC)サポート:金属シールド層または導電性コーティングにより電磁干渉を抑制し、低電圧信号線(BMS通信線など)を高電圧回路干渉から保護します。
2-絶縁保護により効率的な絶縁環境を構築
バッテリーの電気絶縁設計の焦点は、高電圧電気を効果的に絶縁し、システムの効率的な動作を確保できる環境を作成し、バッテリーモジュールがあらゆる動作条件下で安全にパッケージ化され、電気エネルギーの偶発的な放出を防ぎ、潜在的な電気的リスクを回避することです。
A.バッテリー トレイの構造は、耐荷重性と絶縁保護の両方を考慮しています:
l 軽量化を図りながら、高い剛性と耐衝撃性を維持するには、押し出しアルミニウム合金などのアルミニウム合金材料が好まれます。外枠は、バッテリーシステム全体の重量と外部からの衝撃を支えるために使用されます。閉断面プロファイルは、構造強度を高めるために使用されます。内枠は、バッテリーモジュールや水冷プレートなどを支えるように設計されており、それらの安定性と放熱要件を確保します。
l 絶縁材は、バッテリーモジュールとトレイ間の良好な電気的絶縁を確保するために、パッドまたはコーティングとして使用されます。高電圧配線ハーネスには、トレイとの電気的クリアランスと沿面距離を確保するために、専用の管理パスと絶縁シースが必要です。
l 攪拌摩擦溶接などの高度な溶接技術を使用して、接続強度を向上させながら、熱影響部を減らし、変形や潜在的な亀裂を回避します。溶接が不便な部品については、ボルト接続またはリベットを使用し、シーラントと組み合わせて、機械的接続と電気的絶縁の信頼性を確保します。
l 全体の構造の安定性に影響を与えずにバッテリーの交換とメンテナンスを容易にするために、設計時にモジュール性を考慮します。
図2 電気的クリアランスと沿面距離の概略図
B.高電圧および低電圧絶縁設計の重要なポイント:
l バッテリーシステムのプラスとマイナスのポイントは、低電圧電源システムとバッテリートレイから分離する必要があります。これにより、高電圧回路と低電圧制御回路の間に十分な電気的クリアランスと沿面距離が確保され、安全基準を満たし、低電圧システムへの高電圧漏洩を防止できます。
l 高低電圧分離設計では、電磁両立性 (EMC) を考慮して、分離対策によって干渉が生じず、システムが安定して動作し続けるようにする必要があります。
l 高インピーダンス接続では、高システムと低システムが高インピーダンスで接続され、車体アース (バッテリートレイ) のみが電流の流れを制限して、高電圧システムの障害が低電圧システムに広がるのを防ぎます。
l 物理的分離対策では、バッテリートレイを設計する際に、高電圧コンポーネントと低電圧コンポーネントを異なる密閉チャンバーに配置して、物理的な分離によって相互影響を減らすことができます。バッテリーモジュールとトレイの間には、ポリマープラスチックやゴムなどの絶縁材をパッドとして使用して、物理的および電気的分離を確保します。
l 設計時に隔離手段の保守性を考慮し、必要に応じて安全に修理または交換できるようにします。
C.接触保護設計の重要なポイント:
l 高電圧ハーネスの管理:高電圧ハーネスは、露出を避け、直接接触するリスクを減らすために、絶縁シースで適切に包まれ、固定クリップまたはワイヤトラフを介して整然と管理される必要があります。
l 安全パーティション:バッテリーモジュール間、およびバッテリーモジュールとトレイの壁の間に絶縁パーティションが設置され、バッテリーが損傷したときに電解液が漏れて間接的な感電のリスクを防ぎます。
l 高電圧コンポーネントのパッケージ:高電圧コネクタやリレーなどの主要コンポーネントは、トレイ内でもこれらのコンポーネントが誤って直接触れないようにパッケージ化されています。
l 密閉設計:バッテリートレイは、内部の高電圧コンポーネントが露出しないように金属または複合シェルを使用して全体的に密閉構造として設計されており、シェル自体も優れた絶縁特性を備えている必要があります。
l ロック機構:メンテナンス可能な高電圧接続ポイントには、非専門家による操作中に簡単に開かないようにロック機構が使用され、偶発的な接触のリスクが軽減されます。
l 絶縁材料の適用: 絶縁材料は、バッテリー トレイとバッテリー モジュールの間の絶縁層として使用され、トレイが損傷した場合でも、人体が通電部分に直接接触するのを防ぎます。これらの材料には、ポリマー プラスチック、ゴム ガスケット、コーティングなどが含まれますが、これらに限定されません。
3-電気ロゴデザイン
バッテリートレイの電気的識別により、操作の安全性が向上するだけでなく、メンテナンスプロセスが簡素化され、誤操作のリスクも軽減されます。
A.明確な識別
l バッテリー トレイと周囲の高電圧部品に「高電圧危険」や「触れないでください」などの警告サインをはっきりと表示して、緊急時でもすぐに識別できるようにします。
l 高電圧領域には赤やオレンジ、直流には青など、国際的に認められた色分けを使用して、さまざまな電気特性を直感的に区別します。
l 高電圧、接地、電源オフ ポイントなどを示すために、IEC 60417 のグラフィック シンボルなどの標準化された電気安全シンボルを適用して、情報の世界的な理解可能性を確保します。
l バッテリー トレイのシリアル番号、製造日、バッチ情報を含めて、追跡とリコール管理を容易にします。
l 耐摩耗性と耐腐食性のある素材と印刷技術を選択して、バッテリー トレイのライフサイクル全体にわたってラベルが明瞭で読みやすい状態を維持できるようにします。
B.警告サイン
l バッテリートレイと周囲のエリアには高電圧の危険が明確に表示されており、保守担当者が電気の安全性に注意し、操作手順に従うよう促しています。
l 特に高電圧コネクタの近くや露出している場所では、安全な操作距離を示して、適切な距離を保つよう注意を促します。
C.操作ガイド
l 接地対策が適切に実施されるように、バッテリー システムとトレイの接地位置を明確にマークします。
l 安全なテスト ポイントとメンテナンス アクセス ポイントを特定します。これらは、低電圧または無電源状態で動作するように設計する必要があります。
l トレイの重要でない領域に、正しい操作手順をガイドするための基本的な操作および安全に関する指示を簡単に記載できます。
ご参考になるために、定期に熱設計及び軽量化に関する技術と情報を更新させていただきます。当社にご関心をお持ちいただき、ありがとうございます。
最も人気のあるウォーターブロックは、基本的に純銅のマイクロチャネルタイプです。銅製の底板は直接スカイビング加工され、フィンは底板と一体化して熱抵抗を減らします。底板とカバープレートはろう付けまたは拡散接合されており、シールの信頼性を確保しています。
パート3:スカイビング加工によるウォーターブロックの主なコスト構造
1- スカイビングプロセスを使用してウォーターブロックを製造する利点
l 統合設計:スカイビングプロセスは、床とフィンを統合できるため、接触熱抵抗を減らし、熱伝導率を向上させるのに役立ちます。さらに、底板とフィンを統合した設計により、構造強度も向上します。
l 高精度加工:スカイビングプロセスでは非常に細かい歯構造を生成でき、歯の高さ、歯の厚さ、歯のピッチを正確に制御できるため、ヒートシンクフィンの密度が高くなり、放熱面積が大きくなり、放熱効率が向上します。同時に、形状、サイズなど、さまざまな顧客の個別のニーズにもよりよく対応できます。
l 生産効率が高く、スカイビングプロセスは大量生産できます。従来のCNCと比較して、スカイビングプロセスでは複数のギアピースを同時に処理できるため、生産効率が大幅に向上します。
図1: 異なる加工技術を用いたウォーターブロックベース a-スカイビング b-CNC c-冷間鍛造
2-スカイビングウォーターブロックのコスト構造
l 設計開発コスト: スカイビングウォーターブロックの設計の複雑さは比較的高く、特に高い放熱性能が求められる場合は、複雑なプロセス設計と最適化が必要になります。
l 材料コスト: スカイビングプロセスで使用される材料は主にアルミニウムと銅合金です。ラジエーター製造では、アルミニウム板と銅合金を組み合わせた設計がより一般的で、コストパフォーマンスが高いため、アルミニウムと銅の品質がコストに直接影響します。
l 加工コスト:
スカイビング工程コスト:スカイビング工程には、3軸CNC工作機械などの高精度CNC加工設備が必要です。このような設備の使用には高い投資コストが必要であり、オペレーターの技術要件も高く、生産コストが増加します。
溶接工程コスト:ウォーターブロックの製造工程では、溶接工程も重要なコスト要因です。真空ろう付けと拡散溶接は、一般的に使用される2つの溶接方法です。ろう付けは複数のジョイントを同時に溶接でき、生産効率が高く、ろう付け材料が必要で、プロセス条件に対する要件が高く、品質管理が困難です。拡散溶接設備は1回限りの投資が大きく、拡散溶接はフィラーを必要としませんが、ワークピースの表面処理に対する要件が高くなります。
表面処理コスト:一般的な表面処理方法には、陽極酸化、メッキなどがあります。アルミニウム合金ウォーターブロックの場合、陽極酸化により表面硬度、耐摩耗性、耐腐食性が向上し、製品の美観が向上します。銅製ウォーターブロックにはニッケルメッキなどのメッキが施され、銅の酸化や腐食を防ぎ、製品の寿命と信頼性を高めます。
l その他の費用: 検査およびテスト、梱包および輸送など。
3-コスト最適化の提案
l 材料使用の最適化
適切な材料を選択します:たとえば、銅は熱伝導率が高く、単位密度が高く、単価も高いです。アルミニウムは軽量で単価が低く、熱伝導率がやや悪いです。
材料使用: 材料の厚さとマージンを正確に計算することで、材料を効率的に使用し、材料の無駄を減らします。
図2: 材料消費量計算の概略図
l 生産プロセスの最適化
金型の簡素化: 金型の複雑さとコストを削減するために、シンプルな金型を設計します。
スクラップ率の削減: 正確なプロセス制御と品質検査によりスクラップ率を削減します。
ワンステップ成形: プロセスルートを最適化し、複数の処理ステップを削減し、生産効率を向上させます。
ご参考になるために、定期に熱設計及び軽量化に関する技術と情報を更新させていただきます。当社にご関心をお持ちいただき、ありがとうございます。
ウォーターブロックは液体冷却システムの重要なコンポーネントであるため、その設計では、熱交換性能、構造強度、耐腐食性、耐漏洩性、コスト管理など、さまざまな要素を考慮する必要があります。ウォーターブロックは通常、複雑な熱交換スロット構造(つまり、流路)で設計されており、その内部の流路設計の品質がシステム全体の熱交換効率を直接決定します。
パート2:ウォーターブロックの設計、加工技術、課題
1-さまざまなシナリオにおけるウォーターブロックの設計要件
l 高性能コンピューティング:
高性能コンピューティングデバイス(高性能CPU、GPUなど)は動作中に大量の熱を発生するため、ウォーターブロックには効率的な放熱機能が必要です。高熱流束密度の放熱要件を満たすために、ウォーターブロックは通常、高密度マイクロチャネル設計を採用して熱交換面積を増やし、放熱効率を向上させます。さらに、一部の設計ではウォーターブロックをCPUに直接統合し、シリコングリースを塗布する手順を排除することで、組み立てプロセスを簡素化するだけでなく、放熱性能をさらに向上させます。信頼性の面では、ウォーターブロックは漏れを防ぎ、長期にわたる安定した動作を確保するために、優れた密閉性能を備えている必要があります。
l グラフィックカードの冷却:
グラフィック カードは発熱量が多い部分なので、ウォーター ブロックはグラフィック カード上の発熱部品すべてを効果的に冷却できるよう、全面カバー設計にする必要があります。同時に、グラフィック カードの冷却には高流量の冷却剤が必要なので、ウォーター ブロックの内部構造は高流量に対応して熱を素早く除去する必要があります。
l データセンター:
データセンターでは、データセンターの安定した動作と効率的な放熱を確保するために、ウォーターブロックの構造設計は、効率的な放熱、低騒音、高信頼性、高電力密度への適応性、インテリジェントな管理、環境適応性など、複数の要件を満たす必要があります。
2-ウォーターブロック構造の進化の傾向
ウォーターブロックの構造設計の進化の傾向は、技術革新と性能向上の二重の追求を反映しており、主に以下の側面に反映されています。
l 放熱性能の向上:
接触面積を増やす:一部のウォーターブロック設計では、発熱体との接触面積を増やすことで放熱性能を向上させています。たとえば、大面積の銅ベース設計では、良好な接触と熱伝導を実現できます。
内部構造の最適化:内部の水路を最適化します。1つのアイデアは、通常のフィンからステアリングフィンに変更し、長いストリップフローチャネルを提示し、フロー境界層の分離を促進し、境界層の厚さを減らし、熱交換効率を向上させるなど、流体の流れを最適化することです。もう1つのアイデアは、従来の粗い水路からマイクロチャネル設計に変更するなど、熱容量領域を増やすことです。これにより、冷却剤とベースプレートの接触面積が大幅に増加し、放熱効率が向上します。一部の設計では、冷却剤をガイドプレートを介してマイクロチャネルベースプレートに噴霧して、局所的な流速と乱流を増加させ、熱吸収効率を大幅に向上させます。
l 統合されたインテリジェントなデザイン:
統合設計:統合設計では、ウォーターポンプ、ヒートシンクフィン、熱伝導ベースなどのコンポーネントを統合して、接続ポイントの数を減らし、システムの安定性と放熱効率を向上させます。
多機能統合:放熱性能に加えて、最新のウォーターブロックには温度表示と監視機能もあります。
モジュラー設計:モジュラーバックル構造により、整理の利便性と自由度が向上します。
図1: フィンの厚さが異なるウォーターブロックベース
l 高性能な素材と仕上げ:
純銅ベースなどの高性能材料の使用とニッケルメッキなどの表面処理技術の組み合わせにより、熱伝導性と耐腐食性が向上します。
3-加工技術と課題
l 材料特性は処理に影響します:
材料の硬度と靭性の問題: 銅、アルミニウム、およびそれらの合金などの異なる材料で作られたラジエーターは、硬度と靭性が異なり、加工ツールとプロセスに対する要件も異なります。硬度が高い材料は摩耗が早く、ツールの交換頻度も高くなります。靭性が高い材料は、切削中に変形やバリが発生しやすくなります。
銅アルミニウム複合材料の加工は複雑です。銅アルミニウム複合材料のシャベル歯ヒートシンクは、まず連続鋳造半溶融状態プレス技術を使用して複合材料にしてから、シャベル歯加工を行う必要があります。このプロセスはより複雑で、設備とプロセスに高い精度が求められます。
l 高い寸法精度要件
歯の高さと厚さの一貫性を確保するのが難しい:一部の高密度歯ヒートシンクでは、ヒートシンクの性能と均一性を確保するために、各歯の高さと厚さに高い一貫性が求められます。歯の高さと歯の厚さの差が大きすぎると、熱伝達が不均一になり、放熱効果に影響します。加工中は、高精度の設備と自動制御システムを使用して、各歯の仕様が一貫していることを確認する必要があります。
歯間隔の制御が難しい:ヒートシンクの歯が密集しすぎると、その密度と間隔によって加工プロセスが複雑になり、歯の均一性を維持するために加工設備の速度と精度を高める必要があります。たとえば、歯間隔が小さすぎると、切削中に工具が干渉しやすくなり、加工精度と表面品質に影響します。
l 厳しい表面品質要件
バリの問題: 加工中にバリが発生しやすく、ラジエーターの美観に影響を与えるだけでなく、空気の流れを妨げ、放熱効果を低下させる可能性があります。バリの発生は、材料の切断精度が低いこと、加工ツールの摩耗などによって引き起こされる可能性があり、バリの解決には対応するバリ取りプロセスを採用する必要があります。
表面粗さ: ラジエーターの表面粗さは、放熱性能とその後の表面処理効果に影響を与えます。表面粗さが大きすぎると、空気の流れに対する抵抗が増加し、放熱効率が低下します。粗さを減らすには追加の表面処理が必要であり、加工コストと時間が増加します。
l 高度な処理設備とプロセス要件
設備の精度と安定性:ギアショベルには高精度のギアショベルマシンが必要であり、設備の精度は歯の寸法精度と表面品質に直接影響します。同時に、長期加工中の寸法の一貫性を確保するために、設備は良好な安定性を備えている必要があります。
工具の選択と摩耗:適切な工具は加工品質にとって重要です。工具の材質、形状パラメータなどは、材料特性に応じて選択する必要があります。加工プロセス中に工具が摩耗すると、切削力が増加し、寸法精度が低下し、表面粗さが増加するため、工具を適時に調整または交換する必要があります。
送り速度と切削深さ:送り速度と切削深さの不合理な設定は、加工不良につながりやすくなります。送り速度が速すぎて切削深さが大きすぎると、工具に過負荷がかかり、工具のひっかかり、工具の跳ね返り、工具の落下などが発生し、加工精度と表面品質に影響します。
図2: スカイビングプロセス
l 高度なカスタマイズ要件
さまざまなアプリケーション シナリオでは、ラジエーターのサイズ、形状、歯の高さ、歯の厚さ、歯の間隔などのパラメーターに対する要件が異なり、特定のニーズに応じてカスタマイズする必要があります。これにより、加工メーカーは、多様なカスタマイズ ニーズを満たすために、柔軟なプロセス調整機能と豊富な経験を備えている必要があります。
ご参考になるために、定期に熱設計及び軽量化に関する技術と情報を更新させていただきます。当社にご関心をお持ちいただき、ありがとうございます。
世界の人工知能コンピューティング能力の急速な成長とチップの熱設計消費電力(TDP)の継続的な増加により、データセンターの冷却需要は前例のない課題に直面しています。同時に、世界中でますます厳しくなる省エネおよび炭素削減政策は、冷却技術の革新をさらに促進しました。このような状況において、従来の空冷ソリューションは、効率的な放熱と省エネという2つの要件を満たすことが徐々に困難になってきました。液体冷却技術は、その優れた放熱性能と大幅な省エネの利点により急速に台頭し、データセンター冷却ソリューションの主流の選択肢になりつつあります。データ処理とストレージの中核機器であるサーバーのパフォーマンスと安定性は、システム全体の動作効率に直接関係しています。マザーボード、CPU、メモリ、ハードディスク、グラフィックカードなどのサーバーのコアコンポーネントは、継続的な高負荷動作下で大量の熱を発生します。熱を適時に効果的に放散できない場合、サーバーのパフォーマンスと寿命に深刻な影響を及ぼします。このため、高度な液体冷却システムがサーバー冷却ソリューションに導入され、CPU やグラフィック カードなどの主要な熱源に直接取り付けられ、放熱効率が大幅に向上しました。
パート1:水冷ブロックの構造と動作原理
液体冷却システムのコアコンポーネントの 1 つはウォーターブロックです。ウォーターブロックは通常、熱伝導率の高い銅またはアルミニウム材料で作られ、精密な水路とヒートシンク構造で設計されています。これらのウォーターブロックは、CPU や GPU などの熱源の表面にぴったりフィットし、内部を循環する冷却水を通じて熱をすばやく吸収して伝達します。その後、熱はヒートシンクに運ばれ、水冷システムを通じて循環し、最終的に周囲の空気中に放散されます。
図1: 主流チップメーカーのチップ熱消費電力の傾向
1- 一般的なウォーターブロックの種類と特徴
l マイクロチャネルウォーターブロック
特徴:マイクロチャネルウォーターブロックは、精密なマイクロ水チャネル設計を採用しています。水チャネル構造は細かく複雑で、冷却剤と発熱部品との接触面積を大幅に増やすことができ、放熱効率が大幅に向上します。マイクロ水チャネル設計は、冷却剤の流れ中に強い乱流効果を生み出し、対流熱伝達係数をさらに高め、効率的な熱伝達を実現します。
適用シナリオ:特に、非常に高い放熱要件を持つ高性能コンピューティング、オーバークロック、データセンターなど、発熱量の多いCPUやGPUに適しています。
l 大流量ウォーターブロック
特徴: 大流量ウォーターブロックの内部構造は比較的シンプルで、通常は銅板またはエッチング溝設計を使用しており、製造コストが低くなっています。その主な利点は、高速水流を利用して熱を素早く除去し、大流量水冷システムでの使用に適していることです。構造はシンプルですが、効率的な放熱能力により、非常にコスト効率の高い選択肢となっています。
適用シナリオ: 中高級DIYコンピュータシステムや中小規模のサーバークラスターなど、放熱効率に一定の要件があるが予算が限られているシナリオに適しています。
l ジェット式水冷ヘッド
特徴:ジェット式水冷ブロックは、ガイドプレートを介して狭いノズルからマイクロチャネル底板に冷却剤を高速で噴射し、強力な乱流効果を形成して放熱効率を大幅に向上させます。この設計により、冷却剤とベースとの接触面積が増加するだけでなく、高速流によって熱交換性能がさらに最適化されます。
適用シナリオ:高性能CPUおよびGPUに適しており、特にオーバークロックコンピューティング、人工知能トレーニング、グラフィックスレンダリングなど、高放熱要件と高流量シナリオに適しています。
2-ウォーターブロックの一般的な構造
ウォーターブロックは、内部に水路を備えた金属ブロックで、通常は銅またはアルミニウムで作られています。CPU、グラフィックカード、その他の熱発生デバイスと接触することはありません。その構造設計は、放熱性能の品質を直接決定します。一般的なウォーターブロックは、通常、次の主要部品で構成されています。
l ベースは通常、銅やアルミニウム合金などの高熱伝導性材料で作られており、表面は発熱部品との密着性を確保するために細かく加工されており、ベースには複雑な流路設計が施されており、冷却剤とベースの接触面積が増加します。
l カバー プレートは、ベースと一緒になってフロー チャネル シーリング キャビティを形成し、ウォーター ブロック内のフロー チャネル、シール、およびその他のコンポーネントをほこり、不純物、外部の物理的損傷から保護します。
l 水の入口と出口は、冷却剤が水冷ヘッドに出入りするためのインターフェースです。これらは通常、冷却剤がスムーズに出入りできるように、水冷ヘッドの側面または上部に設計されています。位置設計では、流体の流路を考慮して、流動抵抗を減らし、冷却剤の流量を増やす必要があります。
l クリップは、水冷ヘッドを CPU やその他の発熱部品にしっかりと固定し、しっかりとした基礎を確保して効率的な熱伝導を実現するために使用されます。
図2: ウォーターブロックの典型的な構造
3- 放熱性能の総合的な最適化
l 流路設計の最適化
流路の接触面積を増やす:より狭く、より高密度の流路を設計することで、冷却剤とベースとの接触面積を大幅に増やすことができ、対流熱伝達係数を向上させることができます。たとえば、マイクロチャネル設計には微細な水路構造があります。マイクロチャネル水ブロックの設計パラメータ(チャネル幅、高さ、間隔など)は、その放熱効率に決定的な影響を及ぼします。チャネル幅が狭くなると、狭いチャネル内の冷却剤の流れの乱流効果が強化されるため、熱伝達係数が大幅に増加し、熱交換効率が向上します。チャネルの高さが高いほど、冷却剤の流路スペースが広がり、熱伝達性能が向上します。チャネル間隔が狭いほど、冷却剤と熱源との接触面積が増え、放熱効率が向上します。
また、流路レイアウトを最適化し、流路の曲がりを減らすことで最適化することもできます。合理的な流路レイアウトにより、冷却剤が発熱部品の表面を均一に覆い、局所的な温度差を減らすことができます。流路の曲がりにより、ヘッド損失と内部流動抵抗が増加し、冷却効率が低下します。設計では曲がりの数を最小限に抑える必要があります。避けられない場合は、圧力降下を減らして流動性能を最適化するために、曲がりを滑らかな遷移として設計する必要があります。
l 高熱伝導性材料: ウォーターブロックのベースは通常、純銅やアルミニウム合金などの高熱伝導性材料で作られています。これらの材料は、熱源から冷却剤に熱を効率的に伝達し、全体的な放熱性能を向上させます。
l ベース基板の厚さ、フィン、スポイラー構造などの構造パラメータの最適化。基板の厚さが増加すると最高温度が上昇するため、設計では放熱効果と構造強度の最適なバランスを見つける必要があります。フィンの高さ、厚さ、間隔を増やすことで放熱性能を向上させることができますが、同時に流動抵抗も増加します。放熱性能を最大限に高めるには、最適なフィン設計の組み合わせを見つけてください。スポイラー柱の形状は、乱流効果を効果的に高め、熱交換効率を向上させることができます。
ご参考になるために、定期に熱設計及び軽量化に関する技術と情報を更新させていただきます。当社にご関心をお持ちいただき、ありがとうございます。
本文从生产实际出发,总结了搅拌摩擦焊焊接过程中常见的问题、产生原因及改善方法,供大家参考。
この記事では、実際の生産に基づいて、攪拌摩擦接合プロセスにおける一般的な問題、原因、改善方法をまとめ、参考として提供します。
1-表面欠陥
(1)表面溝
l 問題の説明: 表面溝はプラウイング欠陥とも呼ばれ、通常は溶接部の上面に現れ、溶接部の前進端に向かう傾向があり、溝の形をしています。
l 原因: 溶接部の周囲の熱可塑性金属の流れが不十分で、溶接部のプラスチック金属が攪拌針の移動中に残る瞬間的な空洞を完全に満たすことができません。
l 改善方法:ショルダー径を大きくし、圧力を上げて、溶接速度を下げます。
図1: 溝
(2)エッジバリ
l 問題の説明: 溶接部の外側の端にフラッシュバリが発生し、形状が波状になっています。
l 原因:回転速度と溶接速度の不一致、下向きの圧力が大きすぎる。
l 改善方法:溶接パラメータを最適化し、圧力の量を減らします。
図2: エッジバリ
(3)表面剥離
l 問題の説明: 表面の剥離またはねじれが、皮膚またはねじ山の形で溶接の表面に現れます。
l 原因: 金属の摩擦によって発生した大量の熱が溶接部の表面金属に蓄積され、表面の局所的な金属が溶融状態になります。
l 改善方法:溶接パラメータを最適化し、回転速度を下げ、溶接速度を上げます。
図3: 表面剥離
(4)バックウェルドノジュール
l 問題の説明: 溶接の裏側に溶接ビードが形成されます。
l 原因: 溶接時の撹拌ヘッドの深さと圧力の不適切な制御。
l 改善方法:ミキシングヘッドの深さと圧力の設定を最適化します。
2-内部欠陥
(1)不完全な浸透
l 問題の説明: 溶接底部が接続されていないか、完全に接続されていない場合に、「亀裂のような」欠陥が発生します。
l 原因: 撹拌針の長さが足りないため、溶接部の底部の材料が十分に撹拌されません。
l 改善方法:溶接厚さの材料が十分に撹拌されるように、適切な撹拌針の長さを選択します。
図4: 不完全な貫通
(2)穴
l 問題の説明: 溶接底部が接続されていないか、完全に接続されていない場合に、「亀裂のような」欠陥が発生します。
l 原因: 溶接プロセス中に、摩擦熱入力が不十分なため、十分な材料が可塑化状態に達しず、材料の流れが不十分になり、溶接領域が完全に閉じられなくなります。
l 改善方法:溶接パラメータを最適化し、撹拌針の設計を改善し、溶接速度と回転速度を制御します。
図5: 穴
ご参考になるために、定期に熱設計及び軽量化に関する技術と情報を更新させていただきます。当社にご関心をお持ちいただき、ありがとうございます。
最近、編集者は多くの企業が液浸液冷却エネルギー貯蔵に注目し、計画していることに気付きました。しばらく沈黙していた液浸液冷却技術は再び注目を集め、再び人気が出ているようです。多くの同業者もこの発展に注目していると思います。
1- 液浸液冷却技術の特徴
エネルギー貯蔵セルは300Ah以上に向かっており、エネルギー貯蔵システムは5MWh以上に向かっています。セルが大きくなるほど発熱量が多くなり、放熱が難しくなり、温度の一貫性を確保することが難しくなります。また、エネルギー貯蔵システムは多数の積層セルで構成されており、動作条件が複雑で変化しやすいため、発熱の不均一や温度分布の不均一が発生しやすくなります。放熱と温度均一性の問題が適切に解決されないと、バッテリーの充放電性能、容量、寿命が低下し、システム全体の性能に影響を及ぼします。さらに、安全性は常にリチウム電池のエネルギー貯蔵にかかっている「ダモクレスの剣」であり、安全性を向上させる最も一般的な方法は、本質的安全性、能動的安全性、受動的安全性の3つの側面に向かうことです。
浸漬液冷却は、バッテリーセルを絶縁性、無毒、放熱性の液体に浸すことです。冷却剤は、より高い熱伝導率と比熱容量を持っています。この直接接触方式は、非常に高い熱伝達効率を提供すると同時に、温度均一性も向上させます。また、冷却剤は温度制御媒体であることに加えて、エネルギー貯蔵システムの消火液としても使用でき、温度制御と防火を兼ね備えており、これも浸漬液冷却技術の重要な特徴です。より高い放熱性能とより強力な安全性が求められる業界では、浸漬液冷却が間違いなくより多くの利点を持つことになります。
図1: 浸漬型液冷式エネルギー貯蔵バッテリーパックボックス
2- 浸漬液冷却エネルギー貯蔵システムソリューション
液冷技術の1分野として、浸漬液冷技術はエネルギー貯蔵業界で初めて使用されたわけではありません。最初は高性能コンピューティングの分野で使用され、その後、データセンター、人工知能、暗号通貨などに徐々に拡大しました。
浸漬液冷エネルギー貯蔵システムの設計の本来の意図は、従来の空冷と間接液冷の冷却効率とバッテリー温度差制御の欠点を解決することです。南方電力網梅州宝湖プロジェクトの正式な稼働は、最先端技術である浸漬液冷が新しいエネルギー貯蔵工学の分野でうまく応用されたことを示しています。
l 冷却方式と冷媒循環方式
冷却方式は単相と相変化に分かれています。単相浸漬液冷却が使用され、主に鉱油、シリコーン油、天然エステルなどが含まれます。他の方式では、主にハイドロフルオロエーテルに代表される二相浸漬液冷却が使用され、相変化潜熱を利用して放熱し、放熱効率を向上させます。不完全な統計によると、「単相浸漬液冷却」方式は、現在リリースされている浸漬液冷却エネルギー貯蔵システムの中で最も一般的です。
冷却剤の循環モードの違いにより、単相浸漬液冷却には、自然対流、ポンプ駆動、浸漬結合コールドプレート液冷却の3つの技術ルートがあります。自然対流は、加熱後の液体の体積膨張と密度低下の特性を利用して、高温の冷却剤の浮上と冷却後の沈降を実現し、循環放熱を完了します。ポンプ駆動システムの核心は、液体冷却ユニットが冷却剤を駆動して液体冷却パイプラインとバッテリー浸漬ボックスの間で循環させ、循環放熱プロセス全体を完了することです。浸漬結合プレート液体冷却方式では、バッテリーを誘電液に浸し、誘電液と接触する冷却プレートを使用して熱を取り除き、誘電液を冷却するための複雑な二次回路の使用を回避します。
l 製品形態と統合ソリューション
浸漬液冷式エネルギー貯蔵システムの統合ソリューションの反復は、全体から部分、そして細部へと進むプロセスです。各ステップは、前の段階に基づいて最適化および改善され、より高いパフォーマンスと安全性を実現します。
キャビンレベルからパックレベルまで、システム統合テクノロジーはシーンのカスタマイズの特徴を示しています。エネルギー貯蔵シナリオの多様化により、エネルギー貯蔵システムに対する需要が異なります。単一の製品では市場の需要を満たすことはできません。モジュール設計により、プロジェクトの規模と電力需要に応じてエネルギー貯蔵製品を最適化および拡張でき、さまざまなアプリケーションシナリオとニーズに応じてエネルギー貯蔵ソリューションを迅速に調整および展開できます。
3-工業化プロセスにおける課題と実装シナリオ
浸漬型液体冷却エネルギー貯蔵システムは、商業化プロセスにおいて、経済的実現可能性、技術的な複雑さ、市場での受け入れ、業界チェーンの成熟度など、多くの課題に直面します。
l 技術的な複雑さ: コールドプレート液体冷却システムと比較すると、浸漬液体冷却システムは設計と実装がより複雑です。
l 産業チェーンの成熟度: 液浸液体冷却技術の産業チェーンはまだ十分に成熟しておらず、より幅広い分野への応用が制限されています。産業チェーンの成熟度は、技術の推進と商業化に直接影響します。
l 経済的課題: エネルギー貯蔵業界はまだ商業開発の初期段階にあり、収益性の欠如により、高コストの技術ルートが市場に受け入れられることは困難です。多くの企業が一時的な注文に対して低価格で競争しているため、浸漬液冷却の浸透が制限されています。
現在、エネルギー貯蔵産業の主な市場は依然として空冷とコールドプレート液体冷却が主流であり、浸漬液体冷却はまだ市場に完全に受け入れられていません。浸漬液体冷却技術の市場浸透率と受け入れ度は高くありませんが、次のような特殊なシナリオでは大きな可能性を示さない可能性があります。
l 危険化学品業界: 危険化学品会社は、エネルギー貯蔵設備に対して極めて厳格な安全管理を実施しています。これは、製造・保管する化学物質のほとんどが、可燃性、爆発性、毒性、腐食性が非常に高いためです。事故が発生すると、会社自体に重大な損失をもたらすだけでなく、環境汚染や周辺地域への被害を引き起こす可能性もあります。
l 基地局とデータセンター: 基地局とデータセンターは、熱暴走に対する許容度が低いです。データセンターのエネルギー貯蔵システムは、システムの安全性を確保するために、安定した性能を持ち、熱暴走を起こしにくいバッテリーを備えている必要があります。電力品質に対する要件は高く、エネルギー貯蔵システムは迅速な応答能力を備えている必要があります。グリッド障害や停電などの緊急事態が発生した場合、エネルギー貯蔵システムは、電力の継続性と安定性を確保するために、直接放電モードに切り替えることができなければなりません。
l 急速充電ステーション: 高速充電と放電を行うと、バッテリーは短時間で大量の熱を発生します。これにより、バッテリーの温度が高くなりすぎて不均一になり、バッテリーの性能、寿命、安全性に脅威を与えます。つまり、高速充電と放電のシナリオでは、バッテリーの熱管理が特に重要になります。
ご参考になるために、定期に熱設計及び軽量化に関する技術と情報を更新させていただきます。当社にご関心をお持ちいただき、ありがとうございます。
バッテリーパックの気密性は、電気自動車やエネルギー貯蔵システムにおいて重要な指標です。バッテリーパックの気密性テストは、主にバッテリーパックのシェル、インターフェース、コネクタ、冷却アセンブリなどに対して行われ、バッテリーパックの内部が外部環境からのほこりや湿気などの不純物によって汚染または侵入されないこと、冷却アセンブリが漏れないことを確認します。これにより、バッテリーパックが正常な性能と寿命を維持し、短絡や爆発などの安全事故を引き起こさないことが保証されます。
1-バッテリーパックの保護レベルと気密性試験標準の策定
国際保護等級(IEC60529)、異物保護等級またはIPコードとも呼ばれます。IP(侵入保護)保護等級システムは、国際電気標準会議(IEC)によって制定された規格で、異物の侵入や水の侵入に対する電気機器ハウジングの保護等級を分類します。バッテリーパックケースの気密性は通常、IP67またはIP68に達する必要があります。つまり、バッテリーパックケースは、ほこりの侵入から完全に保護され(防塵レベル6)、一定時間、一定の圧力で水に浸しても有害なレベルまで水が浸入しない(防水レベル7)必要があります。より厳しい要件は、バッテリーパックを1mの深さの水に60分間浸しても水が浸入しないことです(防水レベル8)。IP保護等級は通常、2桁で構成されます。図1に示すように、数字が大きいほど保護レベルが高くなります。
図1: IP保護レベルの説明
バッテリーパックが IP67 および IP68 の要件を満たしていることを確認するには、バッテリーパックを水中に沈める必要があります。この方法は時間がかかり、パワーバッテリーパックを破壊し、一定の安全上のリスクがあります。パワーバッテリーのオフラインテストとしては適していません。そのため、業界では気密テストを使用してバッテリーパックが IP67 および IP68 の要件を満たしていることを確認するのが一般的な方法になっています。気密テスト規格の策定では、圧力降下値と漏水率の関係、および開口部と漏水の関係を考慮する必要があります。気密テスト規格の策定には、理論的な極限から実験検証までの一連の手順が含まれており、IP レベルから気密テスト規格への変換を実現します。たとえば、IP68 を例に挙げます:
図2: 気密試験基準策定の手順
2- 気密性試験方法の選択と試験の難しさの分析
バッテリーパックの設計と製造品質は、バッテリーボックスカバーの靭性と強度、バッテリーパックシェルの密閉、インターフェースとコネクタ、防爆ベント、電気コネクタ自体の密閉など、気密性に影響を与える重要な要素です。さらに、熱膨張と収縮の問題、材料の老化、振動と衝撃など、使用中に気密性に影響を与えるいくつかの問題があります。バッテリーパックシェルの生産と製造では、溶接点の不均一、溶接の弱さやひび割れ、エアギャップ、ジョイント接続の密閉不良など、溶接点や接合品質などの問題によって引き起こされる気密性の低下にさらに注意を払います。
バッテリーパックの気密性テストは、主に上部シェル、下部シェル、および組み立て部品の気密性テストに分かれています。上部シェルと下部シェルの気密性テストは、組み立て後の気密漏れ要件を満たす必要があります。バッテリーパックの気密性テスト方法を選択するときは、通常、バッテリーパックの特性、テスト精度要件、生産効率、およびコストが総合的に考慮されます。
エンジニアリングにおけるバッテリーパックのシェルテストは、一般的にプロセス気密性テストと出荷気密性テストに分けられます。さらに、上部シェルと下部シェルの気密性テストは、組み立て後の気密漏れ要件を満たす必要があり、テスト標準に対してより厳しい要件が提示されています。気密性が要件を満たしていることを保証するために、実際の操作で次の困難を克服する必要があります。
l 製品構造の安定性:プラグ溶接、蛇口溶接、梁溶接、フレーム底板溶接、フレーム前後カバープレート溶接などの溶接品質。溶接漏れの問題は、主にアーク開始点とアーク終了点に集中しており、溶け落ちによる欠陥、溶接変形応力による割れ、例えば底板キャビティ側壁溶接、底板キャビティ材料の層化、溶接変形応力に耐えられないことなどです。
l 気密固定具の適応性と安定性: 固定具の設計は、テスト対象のコンポーネントの形状と寸法に厳密に一致している必要があります。これにより、テスト プロセス中にコンポーネントを固定具にしっかりと固定でき、位置のずれや振動によるテスト エラーが削減されます。ただし、実際には、バッテリー パックのサイズと形状は大きく異なるため、複数の異なるテスト固定具の設計と製造が必要になり、コストと操作の複雑さが増します。汎用的な固定具を設計すると、設計プロセスがさらに複雑になります。
l 気密性テスト結果の再現性: 空気圧、温度、テストワークピース/固定具の乾燥度などの要因が気密性テスト結果に影響します。
l 貫通しない微細な亀裂が多数存在するワークピースの場合、検出装置の精度や検出パラメータなどの影響により、漏洩源を発見できず、検出漏れが発生する可能性があります。
図3: 気密性試験ツール
3-エンジニアリングで一般的に使用されるバッテリーパックの気密性検出ソリューションの組み合わせ
バッテリーパックのシェル工程の気密性試験には、一般的に気密性試験と浸水試験が含まれます。気密性試験では、バッテリーボックスの上部カバーを密閉し、コネクタポートのみを空気入口として残します。バッテリーパックの気密性は、空気圧を制御し、空気漏れがあるかどうかを観察することで判断します。浸水試験は、バッテリーボックス全体を完全に水に浸し、ボックス内に水があるかどうかを確認して気密性を判断するものです。
ヘリウム漏れ検出は、ヘリウムをトレーサーガスとして使用し、漏れ箇所のヘリウム濃度を検出することで漏れを検出する技術です。漏れがある可能性のあるテスト対象デバイスの内部または外部にヘリウムが侵入すると、漏れがある場合は、ヘリウムは漏れを通じてすぐにシステム内に侵入または流出し、質量分析計によって検出されます。ヘリウム漏れ検出方法は、特に小さな漏れを検出する場合に高い検出効率を備えています。
図4: 漏れ検出方法の比較
実際の生産では、通常、複数の検出方法を組み合わせて検出効率と精度を向上させます。たとえば、ヘリウム漏れ検出方法は高精度で小さな漏れの検出に適しており、差圧法は高精度で応答が速いという特徴があります。また、従来の水検出方法は検出精度が低いですが、直感的で低コストであり、漏れを見つけるのに便利な方法です。
ご参考になるために、定期に熱設計及び軽量化に関する技術と情報を更新させていただきます。当社にご関心をお持ちいただき、ありがとうございます。
エネルギー貯蔵液体冷却パックの液密性の潜在的な故障には、漏れ、腐食と堆積、結露水、その他の故障モードなど、複数の側面が関係します。
1- 流体の相互接続と構成
エネルギー貯蔵液体冷却システムでは、流体相互接続がさまざまなコンポーネント間で冷却剤を移動させる役割を果たします。効果的な流体相互接続により、冷却剤がシステム内で効率的に循環し、バッテリーの充電および放電プロセス中に発生する余分な熱が除去されます。
密閉性の高いシステムは、冷却剤の漏れを効果的に防ぐことができます。漏れがあると、冷却剤が失われ、頻繁に補充が必要になるだけでなく、システムの放熱性能と安定性にも影響します。エネルギー貯蔵では、冷却剤の漏れによりバッテリーの短絡が発生し、安全上の問題が発生する可能性があります。
2-流体相互接続システムの液密設計
流体相互接続システムの液密設計は、システムが密閉を維持し、さまざまな動作条件下で流体の漏れを防ぐための重要なリンクです。
図1: エネルギー貯蔵液体冷却システムの典型的な展開
(1)システム内の漏洩の可能性のある源とリスクポイントを分析する。
l 液体冷却アセンブリの自己シール特性。たとえば、液体冷却チャネル システムとパック ボックスの統合設計では、コンポーネントは溶接によって接続されます。溶接品質の欠陥、溶接不良、気孔、亀裂などはすべて、液体の浸透の問題につながる可能性があります。
l 構造設計が不合理です。例えば、液体冷却ボックスの位置決め穴やネジ穴が流路に近すぎるため、溶接不良の部分が液体の浸出経路になりやすくなります。
l 接続部品: 液体冷却システムのパイプ接続、バルブ、ジョイントは、漏れが発生しやすい箇所です。接続構造が適切に設計されていなかったり、製造プロセスが洗練されていない場合、ジョイント内部に小さな欠陥が生じ、そこから冷却剤が漏れることもあります。
l 不適切な取り付け、材料の老朽化や損傷などにより生じた漏れ。
(2)シール構造設計:
l 液冷式パックは、乾湿分離型冷却板冷却方式を採用しています。通常の作業条件下では、バッテリーセルは冷却剤と接触しないため、バッテリーセルの正常な動作を確保できます。エネルギー貯蔵液体冷却器の1つの解決策は、押し出し加工で形成し、冷却板に直接流路を統合し、機械加工で冷却循環経路を開くことです。このプロセスでは、適切な溶接プロセスを選択することが、密閉を確保するための重要なステップです。詳細については、「エネルギー貯蔵用下部ボックスの溶接プロセスの設計」を参照してください。
l 液体冷却パイプラインは、主に液体冷却源と機器の間、機器間、機器とパイプラインの間の移行的なソフト(ハード)パイプ接続に使用されます。主な接続方法は次のとおりです。
クイック接続: エネルギー貯蔵液体冷却システムの接続方法の 1 つは、VDA または CQC クイック接続を使用することです。
ねじ接続:接続構造の両端はパイプでスライド接続され、内部のねじリングとねじスリーブ間のねじ接続により、接続の堅牢性が向上します。
制限管とナットの接続:パイプの一端に接続管を締め付け、接続管の両側に制限管を固定して取り付けます。制限管の内側にはゴムワッシャーと凸リングが固定されており、接続管の頭の表面には制限リング溝が開けられています。ナットは制限管の上部に回転可能に接続され、ねじを介して制限管に回転可能に接続されています。
シールリング接続:シールリングは強力な接着剤でねじスリーブの内壁に接着され、シールリングの内壁はパイプの外面に可動に接続され、使用中の漏れを防止します。
(3)PACK液冷プレート、キャビンインターフェース、キャビンパイプライン等は、共通の冷却剤、共通の温度、流量条件下での長期腐食防止設計となっており、腐食のない長期運転を保証します。運転条件による液密性への影響:
l 温度。高温の影響:温度が上昇すると、液体の粘度は一般的に低下し、液体のシール性能が低下し、液密性に影響を及ぼします。たとえば、特定のシール材は高温で変形または劣化し、漏れを引き起こす可能性があります。低温の影響:低温環境では、液体が粘性になり、流れにくくなる可能性がありますが、シール材の性能が向上し、液密性がある程度向上する可能性もあります。
l 圧力。高圧環境:高圧下では、液体の密度と粘度が増加し、液体の密封性能が向上する可能性があります。ただし、過度の圧力はシール材を損傷し、漏れを引き起こす可能性もあります。低圧環境:低圧下では、液体の密封性能が比較的弱くなる可能性があり、特にシール材自体に欠陥があったり、老朽化している場合は、漏れが発生する可能性が高くなります。
l 流量。高流量: 液体が高速で流れると、シール面に大きな衝撃力が生じ、シール材の摩耗や変形を引き起こし、液密性に影響を及ぼします。低流量: 低流量では、液体のシール性能は比較的良好ですが、軽微な材料欠陥などの潜在的なシールの問題が隠れてしまうこともあります。
3-腐食と堆積の問題
l ブロックによる機密性への影響:
冷却剤、堆積物、またはボイラーの成長により、内部の詰まり、冷却剤の流れの悪化、冷却効率の低下が発生する可能性があります。
汚れとスケール: 長期間の使用後、冷却剤内のミネラルがパイプの内壁に堆積することがあります。これを「スケール」と呼びます。汚れは、固体粒子の沈殿、結晶化、腐食、微生物の活動によっても形成されることがあります。これらの汚れはパイプやコールドプレートを詰まらせ、流れの抵抗を増やし、熱伝達効率を低下させます。
泡の問題:液体冷却システムで泡が発生することがあります。泡は冷却プレートの表面に付着し、熱伝達効果が低下し、システム動作時の抵抗が増加し、ポンプなどにキャビテーション腐食を引き起こし、機器を損傷する可能性があります。
l 渦電流が気密性に与える影響:
流体がパイプや隙間を流れるとき、速度の変化によって渦が形成されることがあります。特に、流体が狭い部分や障害物を通過するときに、渦が形成されやすくなります。流体の粘度と密度も渦の発生に影響します。粘度の高い流体は渦を形成しやすく、密度の高い流体は渦の形成を弱める可能性があります。
漏れ経路: 渦電流は接触面に渦を形成し、隙間や不規則な表面に小さな漏れ経路を形成し、ガスや液体の漏れを引き起こす可能性があります。
表面の摩耗: 渦流は、特に高速流の状態で接触面の摩耗を引き起こす可能性があります。摩耗した表面では新たな漏れ経路が形成される可能性が高くなるため、この摩耗により気密性がさらに低下する可能性があります。
熱の影響: 渦電流により熱が発生し、接触面の材料が変形したり熱膨張したりして、特に温度変化が大きいシステムでは気密性に影響を及ぼします。
4-結露水の問題
特定の条件下では、液体冷却ラインに結露が発生し、機器が損傷したり、効率が低下したりする可能性があります。 断熱不良:パイプの断熱材が損傷したり老朽化したりすると、熱が失われ、冷却効果に影響します。特に低温環境では、断熱不良によりパイプ表面に霜や氷が形成される可能性があります。 凍結割れ:寒冷環境では、適切な凍結防止対策を講じないと、パイプ内の冷却剤が凍結してパイプが破裂する可能性があります。
ソリューション
l 密閉対策: 外部の湿った空気がバッテリー コンパートメント内に入らないように、液体冷却パイプラインの入口と出口が完全に遮断されていることを確認します。
l 除湿装置:除湿エアコンを設置するか、除湿機能を使用してバッテリー室内の湿度を適切な範囲に維持します。
l 温度制御: 空調または換気システムを設置することで、エネルギー貯蔵キャビネットが設置されている環境の温度と湿度を制御できます。たとえば、温度を 20 ~ 25 ℃ に保ち、相対湿度を 40% ~ 60% に制御できます。
l 隔離対策: 空のバッテリー ラックを単純に隔離して、バッテリー クラスターを含むコンパートメントに湿気が入るのを防ぎます。
ご参考になるために、定期に熱設計及び軽量化に関する技術と情報を更新させていただきます。当社にご関心をお持ちいただき、ありがとうございます。
流体シミュレーション
ラジエーターと冷板の放熱性能をシミュレーションソフトで解析します。
応用シーン
工況:熱流密度が高い状況です
取り付け配置:片面取り付け
典型応用:顧客定制
持ち前:放熱効果が高い
応用シーン
工況:0.5-1C
組み立て配置:ボトル液冷
典型応用:36s,48s,52s,104s
持ち前:クーリング効果が高い
冷媒は電池の冷板が吸収した熱を蒸発器を通して放出し、ポンプの運行で発生した電力を冷板の吸収装置で発生した熱に送ります。
液冷技術は液体をばいしつとして熱交換を行うことで、空気に比べて、液体はより大きな熱を運ぶことができて、低い流れ抵抗、速い放熱速度、高い放熱効率を提供することができます.液冷システムは風道を設計する必要がなく、ファンなどの机械部品の使用を減らし、故障率が低く、騒音が少なく、環境にも友好的で、敷地面積が節約できます。将来はMW級以上の大型エネルギー貯蔵所に適しています。
電池貯蔵システムは、エネルギー貯蔵媒体として電池を使うエネルギー貯蔵システムです。従来の化石燃料とは異なり、太陽光や風力などの再生可能エネルギーを貯蔵し、エネルギー需給のバランスを取る必要があれば放出することができます。
DFMの最適化提案
潜在的な生産過程でのミスや欠陥を減らし、製品が設計要求の品質基準を満たすことを保証します。
応用シーン
工況:熱流密度が高い状況です
取り付け配置:片面取り付け
典型応用:顧客定制
持ち前:放熱効果が高い
エネルギー貯蔵業界における安全性の進化は、技術革新と安全基準の相乗効果によって推進される体系的な変化です。放熱経路の再構築、材料と構造の協調的な保護、統合的な熱管理に至るまで、このプロセスは、受動的な防御から能動的な抑制へ、そして単一次元から多層的な結合のアップグレードへと、業界における熱暴走防止の根底にあるロジックを反映しています。
1-エネルギー貯蔵技術における「不可能の三角形」と中核的な矛盾を解決するための戦略
a. エネルギー貯蔵技術における「不可能の三角形」の矛盾は、主に複数の側面における相互牽制と均衡に表れています。
エネルギー貯蔵技術の開発は、エネルギー密度、安全性、コストの間で複雑なバランスをとる必要があります。高活性材料はエネルギー密度を向上させることができますが、同時に熱暴走のリスクを大幅に高めます。システムレベルの安全設計(液体冷却温度制御技術など)はリスクを低減できますが、多くの場合、エネルギー密度の低下を伴います。さらに、能動保護システムや本質安全技術の導入は安全性を向上させることができますが、バッテリー以外の部品のコストを大幅に増加させます。これらの矛盾は、エネルギー貯蔵技術の進化において解決すべき複数の制約を明らかにしています。
b. 中核的な矛盾を解決するための戦略
材料イノベーション:新しい電解質材料の適用により、高エネルギー密度を考慮しながら、熱暴走の伝播時間を大幅に遅延させることができます。ナトリウムイオン電池は、負極材料の最適化により、適切なエネルギー密度を維持しながらコストを削減しています。ナノ複合材料の導入により、理論容量が大幅に向上しています。
システム最適化:高度な液体冷却技術は、精密な温度制御により放熱効率を大幅に向上させ、運用・保守コストを削減します。動的再構成可能なバッテリーネットワークは、迅速なトポロジー調整によりシステムの可用性を高めます。
インテリジェント制御:人工知能早期警報システムは、多次元データ融合を通じてリスク予測の精度を大幅に向上させ、エネルギー変換技術の進歩はシステム効率を大幅に向上させました。政策とビジネスモデルの革新は、技術導入を加速させています。例えば、共有エネルギー貯蔵モデルは単一投資のプレッシャーを軽減し、カスケード利用はライフサイクル全体のコストをさらに最適化しました。
2-進化のルール
a. 技術パスの融合イノベーション
マルチソースデータに基づくインテリジェントな早期警報:新世代の監視システムは、ガス、圧力、音響信号などの多次元センサーデータを統合し、動的故障モデルと履歴データ分析を組み合わせることで、誤報率を大幅に低減し、警報時間を短縮します。
熱管理と火災連動設計:液体冷却技術と動的温度調整アルゴリズムを組み合わせることで、精密な温度制御を実現し、防火システムとバッテリー管理を深く統合することで、多層的な連動戦略を構築し、熱暴走の拡大を効果的に抑制します。
材料と構造の協調的最適化:従来の耐火材料に代わり、耐熱断熱コーティングを採用することで、熱拡散遮断時間を大幅に延長します。また、構造設計に衝突防止補強と方向性圧力緩和チャネルを導入することで、機械的衝撃への耐性を向上させます。
b. 保護レベルの段階的深化
バッテリーセルからシステムへの段階的な保護:バッテリーセルレベルに埋め込まれたセンサーにより、早期のリスク監視を実現します。モジュールレベルでは複合検出器と相変化材料を用いることで局所的な熱蓄積を抑制し、システムレベルでは協調型監視プラットフォームを構築することでライフサイクル全体にわたる保護を実現します。
受動的な対応から能動的な防御へ:新規格は、能動的な防御技術の開発を促進します。例えば、インテリジェントなバッテリー管理システムは、動的インピーダンス解析によって充電開始時にリスク経路を遮断し、能動的な結露防止技術は環境ハザードを排除します。
多次元的な協調型保護:熱・電気・機械の協調設計によりシステム全体の安全性を強化します。防火および運用・保守の協調型監視は、製造・輸送の全工程を網羅し、誤報のリスクを低減します。
3-進化のプロセス
a. 放熱技術の進化
液冷技術が主流に:液冷システムは効率的な温度均一化によりバッテリークラスターの温度差を大幅に低減し、寿命を延ばし、安全性を向上させます。浸漬液冷技術は放熱限界をさらに突破し、高レート充放電シナリオをサポートします。
構造最適化による放熱効率の向上:マルチチャネル並列設計により冷却剤の均一な流れを実現し、断熱機能と冷却機能の統合により熱拡散経路を遮断します。
b. 材料と構造の革新
高安全材料システム:耐高温ダイヤフラムとセラミックコーティングにより、熱暴走の連鎖反応を大幅に遅延します。軽量複合材料は、構造強度と保護性能を向上させながら軽量化を図ります。
バッテリーセルとモジュールの革新:新しいバッテリーセル設計は、内部構造の最適化により循環を低減し、寿命を延ばします。また、モジュール統合技術により、スペース利用率と放熱効率を向上させます。
c.熱管理の統合
システムレベルの統合設計:この統合ソリューションは、バッテリー管理、防火、熱管理を高度に統合し、柔軟な導入をサポートし、過酷な環境にも適応します。
インテリジェンスと協調制御:人工知能モデルがバッテリーの状態をリアルタイムで予測し、エネルギー配分を最適化します。また、防火システムと熱管理が連携し、迅速な対応を実現します。
ライフサイクル全体の管理:設計から廃棄までのクローズドループ管理に加え、デジタル監視とクラウドベースの健全性評価を組み合わせることで、システムの信頼性を大幅に向上させます。
結論
エネルギー貯蔵技術の安全性におけるイノベーションは、技術革新の成果であるだけでなく、エネルギーシステムの基礎ロジックの再構築でもあります。材料、構造、インテリジェンスの深層統合により、エネルギー密度、安全性、コストといった様々な制約を打破し、マイクロセルからマクロシステムに至るまでの3次元的な保護ネットワークを構築しています。液体冷却技術と動的早期警報の相乗効果、耐高温材料と軽量設計の相補性、そしてライフサイクル全体にわたる閉ループロジックは、高安全性・高効率エネルギー貯蔵システムの将来ビジョンを描き出します。量子材料や固体電池といった最先端技術の飛躍的進歩により、エネルギー貯蔵業界は本質安全と大規模応用の新時代へと加速し、世界のエネルギーシステムの低炭素化とインテリジェント化に永続的な力をもたらすでしょう。
ご参考になるために、定期に熱設計及び軽量化に関する技術と情報を更新させていただきます。当社にご関心をお持ちいただき、ありがとうございます。
エネルギー貯蔵システムが大容量化、高エネルギー密度化に向かって進化するにつれ、エネルギー貯蔵蓄電池パック筐体のサイズマッチングと互換性設計が、システム効率と信頼性の向上における中核的な課題となっています。この記事では、最新のエンジニアリング設計事例、特許技術、業界動向を組み合わせて、スペース利用、モジュールの互換性、バッテリーセルの配置とサポート設計という 3 つの側面から分析を行います。
1-スペース利用を最適化する
統合エネルギー貯蔵システムの空間利用率の向上は、本質的には、技術の反復とシナリオ要件からの双方向の推進力です。大容量バッテリーセル、モジュール型アーキテクチャ、液体冷却統合などの技術の共同イノベーションを通じて、業界は「大規模なスタッキング」から「極端な空間再利用」へと移行しています。
a.大容量バッテリーセルの応用:エネルギー密度と効率の飛躍的向上
アイデアの要約: 大容量バッテリーセルを適用する本質は、バッテリーパックの内部構造レベルを削減し、バッテリーセルからバッテリーパックまでのスペース利用率を直接向上させることです。従来のバッテリーパックは、「バッテリーセル→モジュール→バッテリーパック」の3段階の統合モードを採用しており、モジュール構造(横梁、縦梁、ボルトなど)によりスペース利用率が低くなります。大容量バッテリーセルは、単一セルを長くしたり体積を増やしたりすることでモジュールレベルをスキップし、CTP (Cell to Pack) 技術を使用してバッテリーセルをバッテリーパックに直接統合することができます。
技術的コア: 600Ah 以上の超大型バッテリーセルを使用することで、バッテリーセルと接続ポイントの数を減らし、単一セルの容量を増加させます。
b.空間再利用とコスト最適化:「コンポーネントスタッキング」から「多次元再利用」へ
アイデアの概要: 空間の再利用とコストの最適化は表裏一体であり、その根底にある論理は、構造の簡素化、機能の統合、材料の反復、標準化された設計を通じて、従来のエネルギー貯蔵システムの物理的およびコスト的な限界を打ち破ることです。
空間再利用の核となるのは、構造階層を極限まで簡素化することで中間リンクを削減することです。たとえば、2 in 1 の高電圧ボックス設計: 江蘇省トリナエネルギーストレージの特許取得済み技術は、2 つの高電圧ボックスを 1 つに統合し、正/負のリレーと電気接続をすべて共有することで、占有する水平スペースを 30% 削減し、電気部品のコストを 15% 削減します。
機能モジュールのクロスドメイン再利用、構造部品と放熱チャネルの統合、例えば液体冷却プレートをボックスの底板と統合し、液体冷却パイプと構造サポート間のスペースを共有することで、独立した放熱部品を 15% 削減します。バッテリーセル本体を構造部品として採用: BYD ブレード バッテリーは、長くて薄いバッテリーセルの側壁によって支持強度を確保し、モジュール フレームを排除することで、スペース利用率を 60%~80% に向上させます。
高電圧カスケードトポロジーなどの電気トポロジーの徹底的な最適化により、単一セルの容量と電圧レベルを高めることで並列回路の数を減らし(Huawei のスマートストリングエネルギーストレージなど)、バッテリースタックの物理的なスペースを 20% 削減し、システム応答時間を 50% 短縮します。 ;共有リレー設計、江蘇省トリナエネルギーストレージの2イン1高電圧ボックスは、2つのラインで同じリレーを共有できるため、リレーの数とケーブルの長さが50%削減され、設置効率が30%向上します。
2-バッテリーセルの配置と支持設計:耐荷重、放熱性、耐振動性のバランス
セル配置の本質は、空間の利用、熱の分散、および機械的安定性の間のゲームです。セルの物理的形状と配置方向は、空間充填効率に直接影響します。
a.バッテリーセルの配置を最適化
逆バッテリーセル設計:バッテリーセルの防爆バルブが下向きになっているため、熱暴走排気口と底部の防球スペースが共有され、バッテリーセルの高さスペースが解放され、体積利用率が向上します。
横向きセルレイアウト: バッテリーパックの高さ方向のスペース利用を最適化し、活性材料の割合を増やし、垂直セルよりも大幅に高い体積利用率を実現します。
超長薄型バッテリーセル:バッテリーセルを長く、薄く設計することで、単位体積あたりのバッテリーセル数を削減し、グループ化の効率を向上させます。
b.放熱と耐荷重の結合設計:構造、材料、プロセスの共同イノベーションを通じて、効率的な放熱と構造強度の二重の最適化を実現することを目指します。
構造設計パス:
液体冷却プレートと支持梁の適合設計などの一体構造:液体冷却チャネルをアルミニウム合金支持梁に埋め込み、独立した部品を減らし、スペース利用率を向上させます。
バッテリーパック、液体冷却システム、BMS を層状に積み重ねて、熱流と機械的ストレスの相互干渉を低減する、階層化および区画化されたレイアウト。
ハニカム/波形構造などのバイオニック機械最適化、アルミニウム合金サポートフレーム内のハニカムまたは波形コア層の設計(Mufeng.comの特許取得済みソリューションなど)、変形により振動エネルギーを吸収し、放熱経路を最適化します。
材料イノベーションの道筋:
熱伝導性と耐荷重性の一体化、例えばアルミニウム合金複合繊維材料(熱伝導率 ≥ 200 W/m·K、強度 +30%)。スマート材料、相変化充填層(PCM)は熱を吸収し、ゆっくりと放出します。温度差は±1.5℃です。軽量ダンピング:弾性シリコンクッション層が振動を吸収します(ダンピング+40%)。
プロセス実装パス:
押し出し成形などの精密成形プロセス:複雑な流路を持つアルミニウム合金液冷ビームの製造に使用されます。
アルミニウム合金の表面にセラミック酸化物層を生成して耐食性を向上させる(塩水噴霧試験 ≥ 1000 時間)とともに放熱効率を高める(表面放射率 20% 増加)などの表面処理技術。
インテリジェントな組み立てプロセスと動的なプリロード調整。圧力センサーと電動アクチュエータを統合してボルトのプリロード (5 ~ 20kN) をリアルタイムで調整し、バッテリーセルへの過圧による損傷を回避します。
c.支持構造の耐荷重性と耐振動性の協調設計: 支持システムは、静的耐荷重性 (バッテリーセルの重量 + 積み重ね圧力) と動的耐振動性 (輸送/地震の影響) という 2 つの要件を満たす必要があります。
3- モジュール性と互換性:標準化されたインターフェースとスケーラブルなアーキテクチャ
標準化されたインターフェースを使用してマルチサイズのバッテリーセルに適応することの本質は、機械、電気、熱管理の共同イノベーションを通じて、統一されたプラットフォーム上でバッテリーセル仕様の柔軟な拡張を実現することです。現在のテクノロジーは静的な互換性から動的な調整へと移行しており、将来的にはインテリジェンス、軽量、シナリオ間の統合へと進化していきます。
a.機械構造の協働イノベーション:
機械インターフェースの標準化: 統一された接続デバイスの寸法を定義します。
モジュラー バッテリー パック/キャビネット設計: スケーラブルなモジュールとバッテリー キャビネットは、標準化されたバッテリー ユニット (280Ah セルや 314Ah セルなど) を通じて構築され、さまざまな容量要件との柔軟な組み合わせをサポートします。
図1-280Ahエネルギー貯蔵蓄電池パック筐体
b.電気システムの動的調整
BMS 互換性などの標準化された通信プロトコルとインターフェース: 異なるメーカーの PCS およびバッテリー セルとのシームレスな接続をサポートするために、統一された BMS (バッテリー管理システム) 通信プロトコルを策定します。動的電力調整は、仮想慣性制御とマルチタイムスケール最適化アルゴリズムを通じて、有効電力と無効電力のリアルタイム調整を実現します。適応型電気パラメータマッチング設計。
c.熱管理システムのインテリジェントな適応
階層的な熱管理ソリューション。難燃性高反発フォーム、熱伝導性接着剤、その他の材料をセル レベルで使用して、断熱性と放熱性の要件のバランスを取り、熱の拡散を抑制します。モジュールレベルの統合液体冷却プレートと断熱層の統合設計により、サイクル寿命が向上しました。システムレベルでは、可変周波数コンプレッサーと複数の冷却ブランチを通じて冷却能力を動的に調整します。
インテリジェントな監視と予測、マルチセンサーの融合。高精度な温度取得を実現するために、温度センサーをバッテリーセルの極や広い表面などの重要な場所に配置し、デジタルツインテクノロジーは、クラウド監視と予測メンテナンスを通じて、熱放散戦略をリアルタイムで最適化します。
4- 結論
エネルギー貯蔵蓄電池パック筐体の最適化は、単一の構造改善から多次元の共同イノベーションへと移行しました。
カーボンファイバーボックス+CTP技術+AIレイアウトアルゴリズムの組み合わせなど、材料、構造、アルゴリズムの融合が主流になるでしょう。
モジュール化と標準化が加速しており、Pack を最小の機能単位とする標準化された設計により、業界はコストを削減し、効率性を高めることになります。
熱管理と空間利用が深く統合され、液浸液体冷却と動的温度制御技術により、宇宙の潜在能力がさらに発揮されます。
ご参考になるために、定期に熱設計及び軽量化に関する技術と情報を更新させていただきます。当社にご関心をお持ちいただき、ありがとうございます。
AIコンピューティング能力の爆発的な成長とデータセンターの電力密度の継続的な増加により、従来の空冷技術ではもはや放熱ニーズを満たすことができなくなりました。効率的な放熱、省エネ、消費電力削減といった利点を持つ液冷技術は、もはや必須の技術となっています。液冷技術において、コールドプレートと液浸冷却の競争は特に熾烈です。本稿では、技術的特徴、適用シナリオ、費用対効果、将来の動向といった観点から、両者の長所と短所を分析し、今後の主流となる方向性を探ります。
1- 技術的特徴の比較:コールドプレート型は高い互換性を持ち、液浸型はより高い放熱効率を持つ
a. コールドプレート液冷:スムーズな移行を実現する「改革派」
高い互換性:サーバー構造を大幅に変更する必要がなく、既存の空冷式データセンターのインフラと互換性があり、改修コストが低く、サイクルも短い。
高い安全性:冷媒が電子部品に直接接触しないため、漏洩のリスクが低く、モジュール設計(クイックチェンジジョイントや冗長配管など)によってさらにリスクを低減できる。
高い成熟度:コールドプレート技術は、Alibaba Cloud Qiandao LakeデータセンターやIntelとの連携プロジェクトなどで広く採用されており、現在の液冷市場の90%を占めている。
限界:コールドプレート型はCPUやGPUなどの一部の高電力コンポーネントしかカバーできず、残りの熱は依然として空冷による放熱に頼る必要がある。 PUE値は通常1.1~1.2で、液浸型よりもわずかに高くなります。
b. 液浸液冷:効率的な放熱を実現する革新的技術
液浸液冷は、サーバー全体を断熱性のある冷却剤に浸漬し、直接接触させることでデバイスの放熱を最大限に高めます。主な利点は以下のとおりです。
優れたエネルギー効率:液体の熱伝導率は空気の20~30倍で、PUEは1.05まで低下し、放熱効率は3倍以上向上します。
省スペース:冷却システムの容積は空気冷却のわずか3分の1で、1筐体あたりの電力密度は50kW以上に達します。これは、AIスーパーコンピューティングなどの高密度環境に適しています。
静音性と環境への配慮:ファンが不要で、騒音は90%以上低減され、粉塵汚染も発生しないため、機器の寿命が長くなります。
課題:液浸にはカスタマイズされたサーバーが必要であり、冷媒のコストが最大 60% を占め (フッ素系液体など)、初期投資が高く、環境適合性を向上させる必要があります。
2-アプリケーションシナリオの差別化:中短期的にはコールドプレート型が主流、長期的には液浸型の可能性が発揮される
a. コールドプレート型:既存データセンターの改修および新規IDC構築における「費用対効果の高い選択肢」
旧式データセンターの改修:コールドプレート型は、既存の空冷アーキテクチャに迅速に適応でき、改修サイクルが短く、コストも制御可能です。例えば、IntelとBihが共同で開発したモジュール型ソリューションは、標準化されたコールドプレート設計により導入の難易度を軽減します。
中高密度コンピューティングパワーシナリオ:コールドプレート型は既に1筐体あたり130~250kWの電力をサポートしており(NVIDIA BシリーズGPUなど)、ほとんどのAIトレーニングニーズに対応しています。
b. 液浸型:スーパーコンピューティングおよびグリーンデータセンター向けの「究極のソリューション」
超高密度コンピューティングパワー:次世代チップ(NVIDIA Rubinシリーズなど)の筐体電力は1000kWを超え、液浸型が唯一の実現可能なソリューションとなるでしょう。
グリーン省エネニーズ:液浸型のPUEは1.05に近づき、廃熱回収効率は90%に達します(Lenovoのソリューションなど)。これは「デュアルカーボン」目標政策と一致しています。
c. 現在の市場状況
コールドプレート型が現在の市場を支配しています。2025年には、コールドプレート型が液体冷却市場の80%~90%を占め、液浸型は10%未満になります。さらに、標準化されたインターフェース(IntelのOCPコールドプレート設計など)が形成されており、InspurやSugonなどのメーカーのソリューションは高い互換性を備えています。国内の「東西データコンピューティング」プロジェクトでは、新規データセンターのPUEを1.25以下に抑えることが求められており、コールドプレート型は移行における第一選択肢となっています。
液浸型の準備が整いました:Sugon Digital C8000相変化液浸ソリューションはPUE 1.04を達成し、Alibaba Cloudの「Kirin」データセンターは単相液浸の実現可能性を検証しました。NVIDIA B200 GPU(1000W+)などの高出力チップは液浸型アプリケーションを強制し、液体冷却のコンピューティング電力密度は30%~50%増加します。EUは2028年にフッ素系液体の使用禁止を計画しており、国内の炭化水素/シリコンオイル冷却剤の研究開発が加速しています(Sinopecの「Kunlun」シリーズなど)。
3-権威ある意見 PK
コールドプレート派:コールドプレートは液体冷却普及の「砕氷船」であり、今後5年間で増分液体冷却市場の80%を占め続けるだろう。液浸型は、チップの消費電力が臨界点を突破するまで待つ必要がある。
液浸型派:相変化液浸は液体冷却の究極の形態であり、コールドプレートは過渡的なソリューションに過ぎない。チップ単体の消費電力が800Wを超えると、液浸型が唯一の選択肢となる。
中立派:技術ルートの分化は、コンピューティングパワー需要の階層化を反映している。コールドプレートは「東洋のデータ」を、液浸型は「西洋のコンピューティング」を支える。今後10年間は、この二本の並行開発が主要なテーマとなるだろう。
4-業界の機会と戦略
コストとエコシステム:コールドプレートは短期的な優位性を有しており、液浸型はコスト削減によって膠着状態を打破する必要がある。
コールドプレート:材料の最適化(銅アルミニウム複合材)、加工精度の向上(リーク防止プロセス)、モジュール化・標準化設計の推進。
液浸:費用対効果の高い冷却剤(単相液浸液など)、互換性のあるキャビネットの開発、そしてチップメーカーとの協力による冷却ソリューションのカスタマイズ。
技術予備:将来の高電力需要に対応するため、二相流コールドプレートとインテリジェント監視システム(AIダイナミックフロー調整など)の検討。
5-結論
短期(2025~2027年):コールドプレート型が一般的なシナリオを席巻し、液浸型普及率は15~20%に上昇。長期(2030年以降):相変化液浸型は高コンピューティングパワー分野で主流となり、コールドプレート型は中低密度市場へと後退。
優位性:冷却剤コスト、チップ消費電力の急上昇、国際的な環境保護政策。
ご参考になるために、定期に熱設計及び軽量化に関する技術と情報を更新させていただきます。当社にご関心をお持ちいただき、ありがとうございます。
新エネルギー自動車やエネルギー貯蔵産業の急速な発展に伴い、軽量化、高い安全性、効率的な熱管理が中核的なニーズとなっています。当社はアルミニウム合金材料の加工分野に深く関わっており、高度な材料選定、成形プロセス、溶接技術を駆使して、バッテリートレイ、液体冷却プレート、エネルギー貯蔵パックボックス、ラジエーターなどの研究開発と製造に注力しています。アルミニウム合金は、低密度(約2.7g/cm³)、高強度、耐腐食性、優れた熱伝導率(熱伝導率約150~220W/m·K)を特徴としており、新エネルギー機器の軽量化と熱管理に最適な選択肢となっています。
1- アルミニウム合金材料の選定と重要な考慮事項
製品によってアルミニウム合金に対する性能要件は大きく異なるため、強度、耐食性、溶接性、プロセス適応性などを考慮して材料を総合的に選定する必要があります。
a. バッテリートレイ
一般的なグレード:6061-T6、6005A-T6、6063-T6
選定基準:
·引張強度240MPa以上(例:6061-T6)で、国家標準の押出試験、落下試験、ボール衝撃試験に合格する必要があります。
·溶接性が高く、熱割れが発生しにくいこと(Mg/Si強化型6xxxシリーズが推奨されます)。
·耐食性は、陽極酸化処理またはアルミニウムクラッド処理によって向上します。
図1-アルミニウム合金バッテリートレイ
b. エネルギー貯蔵パックボックス
一般的なブランド:5083、6061-T6(強度と耐食性の両方)。
選定基準:
・振動および衝撃荷重に耐える必要があり、降伏強度は200MPa以上である必要があります。
・電気化学的腐食を防ぐため、高度な表面処理が必要です。
c. 液体冷却プレート
一般的なブランド:3003、6061/6063、6082。
選定基準:
・高い熱伝導性と耐食性。
・液体冷却チャネルは複雑な成形を必要とするため、優れた押出性能を持つ6xxxシリーズが推奨されます。
2- プロセス性能の違いと加工上の難しさ
アルミニウム合金の加工は、特に切削、CNC加工、溶接、表面処理において、その物理的特性に適応する必要があります。
a. 切削とCNC加工
難しさ:
· 高精度穴加工では、材料の延性によりバリや変形(段付き穴の縁の突起など)が発生しやすくなります。
· 薄肉構造(液体冷却プレートの流路など)では、反りを防止するために切削抵抗を制御する必要があります。
解決策:
· ダイヤモンドコーティング工具を使用することで、刃先の切れ味を向上させ、押し出し変形を低減します。
· 加工パラメータ(高速・低送りなど)を最適化し、一般的なCNC装置と連携させることで、安定した加工を実現します。
b. 溶接プロセス
主な課題:
· 酸化膜(Al₂O₃ 融点 2050℃)は溶融を阻害し、気孔やスラグ介在物の発生につながります。
· 一部の合金は高温割れが発生しやすいため、溶接線エネルギーと溶接ワイヤの組成を制御する必要があります。
推奨される溶接プロセス:
·TIG溶接(交流電源):薄板に適しており、「陰極クリーニング」によって酸化膜を除去します。
·MIG溶接(高電流+ヘリウム混合ガス):厚板の溶接効率が高く、入熱量も制御可能です。
図2-バッテリートレイの溶接
c. 表面処理
·絶縁耐圧コーティング:バッテリートレイおよびパックボックス内部に塗布し、高圧試験(3000V DC/1分以上)に合格する必要があります。コーティング厚さは20~50μmで、高電圧環境下における絶縁安全性を確保します。
·絶縁・除湿コーティング:エネルギー貯蔵パックボックスには、内部結露のリスクを低減するため、疎水性材料(フッ素樹脂など)を使用し、ダイン値は34以上で接着性を確保します。
·衝突防止コーティング:バッテリートレイの外壁には、ポリウレタンエラストマー(硬度80ショアA以上)を選択し、耐衝撃性を30%以上向上させます。
·陽極酸化処理:従来の防錆処理で、膜厚誤差は3μm以下で、複雑な構造に適しています。
3- 検証検査と設備適応性
新エネルギー産業の規格(GB/T31467.3、UL2580など)を満たすには、多次元検証とプロセス適応が必要です。
a. 検証検査
・構造強度:有限要素法シミュレーション(最大応力≤材料降伏強度)を用いて、トレイの耐荷重性、押し出し性、ボール衝撃性を検証します。
・シーリング試験:液体冷却システムは、ヘリウムリーク検出(リーク速度≤1×10⁻⁶ mbar·L/s)とサイクル圧力試験(0.5~1.5MPa/5000回)を実施します。
・コーティング性能検証:
絶縁コーティング耐電圧試験(5000V DC/60秒間、破壊なし)
衝突防止コーティングは、落下ボール衝撃試験(1kg鋼球、高さ1m)および塩水噴霧試験(1000時間、剥離なし)に合格します。
b.設備適応性の最適化
・CNC設備の汎用化:高精度治具設計と動的補正アルゴリズムにより、薄肉部品の加工変形を0.1mm以下に抑えます。
・溶接パラメータライブラリ:様々なアルミニウム合金グレードに対応した標準溶接パラメータ(電流値やワイヤ送給速度など)を確立し、デバッグサイクルを短縮します。
・自動コーティングスプレー:多軸ロボットスプレーと赤外線硬化技術を組み合わせることで、コーティング均一性誤差を5%以下に抑えます。
結論
新エネルギー機器におけるアルミニウム合金の広範な応用は、材料科学の成果であるだけでなく、プロセスイノベーションの成果でもあります。当社は、高強度、耐腐食性、加工性に優れた新たなアルミニウム合金の開発を継続し、プロセスイノベーションを通じてバッテリートレイや液体冷却プレートなどの製品の性能向上を推進し、業界が効率化と軽量化を実現できるよう貢献していきます。
ご参考になるために、定期に熱設計及び軽量化に関する技術と情報を更新させていただきます。当社にご関心をお持ちいただき、ありがとうございます。
電子機器の電力密度が高まり続ける中、放熱設計はシステムの信頼性と寿命を左右する重要な要素となっています。19年にわたる熱管理の経験を持つ専門メーカーとして、当社は典型的なエンジニアリング事例とマルチフィジックスのフィールドシミュレーションの経験を組み合わせ、高電力シナリオにおいてエンジニアが見落としがちな5つの主要な技術的誤解を深く分析し、業界の慣行に準拠したソリューションを提供します。
誤解1:高熱伝導率材料の乱用、インターフェース熱抵抗の計算誤差
典型的な問題:熱伝導性材料の理論値を追求しすぎ、インターフェース接触熱抵抗の工学的現実を無視している。
事例分析:ある車載レーザーレーダー放熱モジュールでは、純銅基板(熱伝導率401W/m·K)を使用していましたが、熱伝導性材料(TIM)のコーティング厚さが正確に制御されておらず(設計値0.1mm、実測値±0.05mm)、測定された接触熱抵抗が0.6°C·cm²/Wに達し、FPGAジャンクション温度が規格値を22%超過しました。そこで、成形サーマルパッド(許容差±0.02mm、熱抵抗<0.03°C·cm²/W)に切り替え、真空焼結プロセスと組み合わせることで、ジャンクション温度は17°C低下し、MTBF(平均故障間隔)は10万時間に向上しました。最適化計画:
材料選定:ASTM D5470規格に基づき、TIMの熱抵抗を測定し、相変化材料または金属充填エラストマーを推奨します。
工程管理:自動塗布装置(精度±3%)を使用し、厚さ公差を10%未満に抑え、エアギャップを回避します。
誤解2:空冷システムにおける気流構成の不一致、局所的なホットスポットの制御不能
典型的な問題:ファンの数を盲目的に積み重ね、流路インピーダンス整合と境界層剥離効果を無視している。
エンジニアリング例:あるデータセンターのGPUクラスターでは、4基の12038ファン(風量200CFM)を使用していましたが、エアガイド角度(90°直角曲げ)の設計が不適切だったため、実際の有効風量は公称値の65%に過ぎず、局所的な温度差は40℃に達しました。CFDシミュレーションによる最適化の後、エアガイドを徐々に拡大する流路(拡散角度<7°)に変更し、フィン間隔の勾配を2mmから3.5mmに増加させるスタッガードフィンレイアウトを採用することで、全体の風圧抵抗を30%削減し、ホットスポットの温度差を8℃以内に抑えることができました。
コア戦略:
流れ場設計:ISO 5801規格に準拠した風洞試験を実施し、入口と出口の面積比を最適化します(推奨:1:1.2)。
動的制御:PWMファンのQ-H曲線に基づき、システムインピーダンス点を最高効率範囲(通常、最大風量の60~80%)に合わせます。
誤解3:環境保護設計の不備が材料の劣化を加速させる
典型的な問題:初期の放熱性能のみを重視し、湿度、熱、粉塵、塩水噴霧などの長期的な環境ストレスの影響を無視している。
事例分析:洋上風力発電コンバータは、6061アルミニウム合金ヒートシンク(表面陽極酸化処理)を使用していました。塩水噴霧環境で6ヶ月間稼働させた後、酸化層が剥離し、接触熱抵抗が50%増加し、IGBTの故障率が急上昇しました。5052アルミニウム合金(耐塩水噴霧性1000時間以上)に切り替え、ポリウレタン耐水性塗料(厚さ50μm、IEC 60068-2-11規格に準拠)を塗布したところ、3年間のフィールド故障率は75%減少しました。
設計ポイント:
コーティング技術:高温環境下でも使用できるよう、プラズマ溶射Al2O3セラミックコーティング(熱伝導率30W/m·K、耐熱温度800℃以上)を採用しています。
シーリング構造:IP69K保護等級(ダブルパスシリコンシール+圧力リリーフバルブ)により、粉塵や水蒸気の侵入を防止します。
誤解4:過渡熱負荷モデリングの欠如と相変化材料の不適切な選択
典型的な問題:定常状態シミュレーションで設計された放熱ソリューションは、ミリ秒レベルの電力パルスに対応できません。
実測データ:5G基地局において、ソリッドステートパワーアンプに2ms@2000Wのパルス負荷が印加されました。従来のアルミニウム基板ソリューションでは過渡温度上昇が55℃に達しましたが、マイクロカプセル型相変化材料(パラフィン/グラフェン複合材、相変化潜熱220J/g)と過渡熱シミュレーション(ANSYS Icepak 過渡ステップ長1ms)を組み合わせることで、温度上昇を18℃に抑え、MIL-STD-810G衝撃試験要件を満たしました。
動的管理技術:
相変化パッケージング:ハニカム構造で相変化材料(多孔度>70%)をカプセル化することで、液漏れを防ぎ、熱拡散効率を向上させました。
モデルキャリブレーション:シミュレーション境界条件は赤外線熱画像(サンプリングレート100Hz)に基づいて補正され、誤差は±1.5°C未満です。
誤解5:TCO評価は一方的で、隠れた運用・保守コストが考慮されていない
典型的な問題:ハードウェアの初期コストのみが比較され、エネルギー消費量、保守コスト、ダウンタイムによる損失が定量化されていない。
コスト比較:ある半導体工場では、当初空冷キャビネット(初期コスト50万元)を使用しており、年間電気代は120万元(PUE=1.8)でした。二相液浸液冷却(初期コスト180万元)にアップグレードした後、年間電気代は45万元(PUE=1.05)にまで低下しました。クリーンルームの空調負荷の削減により、年間の総合的な節約額は90万元に達し、増分投資は2.1年で回収可能(IRR>25%)です。
意思決定モデル:
改良モデリング:モンテカルロシミュレーションを導入し、機器故障率(ワイブル分布)がTCOに与える影響を定量化する。
政策の重ね合わせ:炭素税メカニズム(EU CBAMなど)と組み合わせることで、液体冷却システムのライフサイクル全体にわたる炭素排出量は60%削減され、さらに15%の追加補助金が得られる。
結論:熱設計パラダイムを経験主導からデータ主導へアップグレード
標準化プロセス:概念設計段階でJESD51-14熱試験規格を導入し、後々の手戻りを回避(ある光モジュールのプロジェクトサイクルが30%短縮)。
学際的連携:COMSOL Multiphysicsの電磁損失(HFSS抽出)と熱ひずみ場の連成により、レーダーTRコンポーネントの放熱効率が40%向上。
インテリジェントな運用・保守:ファイバーグレーティング温度センサー(精度±0.1℃)とデジタルツインプラットフォームを導入し、障害予測を実現(スーパーコンピューティングセンターの予期せぬダウンタイムを90%削減)。
厳格なエンジニアリング思考とフルリンクデータ検証により、熱設計エンジニアは「見えないキラー」を正確に回避し、高信頼性システムの基盤を築くことができます。当社は業界の実務家として、材料からシステムまでのクローズドループソリューションを提供することに尽力しており、お客様と共同で熱管理の課題に取り組んでいます。
ご参考になるために、定期に熱設計及び軽量化に関する技術と情報を更新させていただきます。当社にご関心をお持ちいただき、ありがとうございます。
1-主要部品の特別な許容誤差要件
EV バッテリー トレイおよびエネルギー貯蔵用液体冷却バッテリー パック エンクロージャの製造では、主要な接続面とインターフェイスの許容誤差管理が、シーリング、放熱効率、組み立て精度に直接影響します。
a. 液体冷却プレートの取り付け面
液体冷却プレートは、バッテリー熱管理システムのコア コンポーネントです。取り付け面の平坦度は、冷却剤流路のシーリングに直接影響します。平坦度が許容範囲外の場合、シリコン ガスケットの圧縮が不均一になり、局所的な漏れや熱抵抗の増加が発生します。
b. 溶接継ぎ目のずれ
バッテリー トレイでは、多くの場合、アルミニウム合金の溶接構造が使用されています。溶接継ぎ目のずれは、応力集中を引き起こし、疲労寿命を低下させます。特に、バッテリー パック エンクロージャの気密性に対する要件が高いシナリオ (IP67 など) では、ずれを厳密に管理する必要があります。
c. バッテリー モジュールの位置決め穴
位置決め穴は、バッテリー モジュールを正確に固定するために使用されます。許容誤差が大きすぎると、モジュールの位置ずれが発生し、電気接続の障害や機械的振動のリスクが生じます。
d. ボルト穴の位置の固定
ボルト穴は、バッテリー パック エンクロージャをシャーシに接続するために使用されます。位置のずれは、組み立て時のストレスの原因となり、ボルトの破損につながることもあります。
e. バッテリー パック エンクロージャのエッジの真直度
バッテリー パック エンクロージャのエッジの真直度は、上部カバーと下部カバーの組み立てと IP 保護レベルに影響します。特に、レーザー溶接エンクロージャでは、エッジをレーザー ヘッド トラッキングの基準として使用する必要があります。
2-寸法公差が製造効率に与える影響
寸法公差が製造効率に与える影響は、主に加工フロー、コスト管理、製品品質のバランスに反映されます。合理的な公差設計は、製品の機能を保証するだけでなく、生産リズムを最適化することもできます。寸法公差の合理的な管理が製造効率に与える影響は、主に次の側面に反映されます。
a. 加工精度と生産コストのバランス
· 寸法公差を厳密にすると、シーリングと組み立ての精度が向上しますが、高精度の加工設備と複雑なプロセスが必要になり、設備投資と加工時間が大幅に増加します。
· 精度を過度に追求すると、加工コストが増加する可能性があります。重要な機能部品には厳格な公差を設定する必要があり、重要でない領域では公差を適切に緩和してコストを削減する必要があります。
b. 再加工率とスクラップ率の管理
· 合理的な公差設計により、寸法偏差による再加工を減らすことができます。
· バッテリートレイの製造では、溶接変形が主な問題です。 CMT 冷間溶接プロセスを使用すると、入熱を最適化し、溶接後の変形を減らし、再作業サイクルを短縮できます。
c. モジュール化および標準化された生産
· 標準化されたコンポーネントにより、許容誤差要件がローカル交換部品に集中し、全体的な処理の難しさが軽減されます。
· 標準化された許容誤差設計により、複数モデルの互換性もサポートされ、カスタマイズされた処理の必要性が軽減されます。
3-平坦度制御の業界標準と実用化
新エネルギー車のバッテリートレイの場合、業界標準には厳しい要件があります。
a. 平坦度基準:液体冷却プレートの設置面の平坦度は≤0.2mm、底部支持プレートの平坦度は≤0.5mm/m²、溶接後のフレームの平坦度誤差は≤0.8mm6でなければなりません。
b. 製造プロセスの最適化:CNC精密フライス加工、CMT冷間溶接、振動老化処理(VSR)をレーザー干渉計オンライン検出と組み合わせることで、変形のリスクを軽減します。
c. 材料の選択:軽量性と構造安定性の両方を考慮して、降伏強度が≥1180MPaの6061などの高強度アルミニウム合金の使用をお勧めします。
4-材料とプロセスによる許容差調整戦略
a. 材料の革新が軽量化を推進
軽量の高強度アルミニウム合金(6061など)と複合材料(炭化ケイ素強化アルミニウムマトリックス)を使用し、陽極酸化処理と絶縁コーティングを組み合わせることで、30%の軽量化と耐腐食性の向上を実現し、液体冷却システムの放熱要件に適応します。
b. プロセスのコラボレーションにより製造精度が向上
一体型押し出し成形+攪拌摩擦溶接(FSW)により溶接回数が削減され、CMT冷間溶接とレーザー溶接により熱変形が制御されます。
c. 信頼性を確保するためのシミュレーション検出クローズドループ
CAEシミュレーションにより補強リブのレイアウトが最適化され、レーザースキャンとヘリウム漏れ検出技術により完全なプロセス監視が実現され、モジュール設計は±5mmの許容差に対応し、コストを削減して効率を高めます。
ご参考になるために、定期に熱設計及び軽量化に関する技術と情報を更新させていただきます。当社にご関心をお持ちいただき、ありがとうございます。
1- バッテリートレイ/エネルギー貯蔵パックボックスのアルミニウム合金溶接プロセスの特徴
新エネルギー液体冷却パックボックス、バッテリートレイなどの製品の製造では、液体冷却チャネルとマルチキャビティ構造が典型的な複雑な設計機能です(図1を参照)。このような構造には、多くの場合、次の機能が含まれます。
図1: バッテリートレイの典型的な設計
3 次元空間のインターレース: 流路は蛇行状に分布し、多数の空間的転換点があります。
多段接続: メインキャビティとサブキャビティは薄壁の仕切り (厚さ 2 ~ 3 mm) で接続されています。
小型化の特徴: 流路の断面積が小さく (アルミニウム プロファイル流路の最小壁厚は 1.2 mm)、溶接のアクセス性が悪い。
2- バッテリートレイ製造における複数の溶接技術の組み合わせの難しさ分析
バッテリートレイ製造の実践では、摩擦撹拌溶接 (FSW)、冷間金属遷移溶接 (CMT)、従来の溶融溶接 (TIG/MIG) などの技術の協調適用など、複数の溶接技術を組み合わせる必要があります。この組み合わせは、軽量、強度、密閉、生産効率を考慮することを目的としていますが、次のような中核的な困難にも直面しています。
a. 複数のプロセスの熱入力の協調の問題
異なる溶接技術 (FSW やレーザー溶接など) は熱入力に大きな違いがあり、材料の性能の変化や熱変形を引き起こしやすいため、溶接シーケンスとパラメータ調整を最適化することで解決する必要があります。
b. 機器の互換性と効率のボトルネック
機器の切り替えは複雑で、パラメータ同期の精度要件は高くなります。共同作業の効率を向上させ、サイクル時間を短縮するには、モジュラーワークステーションの設計とインテリジェント溶接機が必要です。
c.シール強度とコストのバランスをとる課題
複数の溶接の交差部での漏れのリスクが高く(欠陥の70%を占める)、冗長シール+トポロジー最適化設計が必要です。
3-エンジニアリングの実践:バッテリートレイ、エネルギー貯蔵液体冷却PACKボックスのマルチ溶接プロセス調整
a. 溶接痕の位置計画
· 溶接位置の最適化:製品設計段階では、溶接位置の合理性を十分に考慮し、製品の機能に影響を与える重要な部分や領域に溶接痕が現れないようにする必要があります。たとえば、フロントフレームとウォーターノズルの隙間を調整して溶接痕の干渉を防ぎ、ウォーターノズルの溶接位置を最適化して製品のパフォーマンスへの影響を減らします。
· 製品構造とのマッチング:溶接位置は製品構造と一致し、製品の使用中に溶接がさまざまな負荷とストレスに耐えられるようにする必要があります。たとえば、液体冷却プレートプロジェクトでは、溶接位置を合理的に計画することで、製品の構造的安定性と信頼性が向上します。
· 操作と検出が容易:溶接位置は、オペレーターが溶接操作とその後の品質検査を実行するのに便利なものでなければなりません。たとえば、手の届きにくい場所や視界の悪い場所での溶接を避けて、溶接の効率と品質を向上させます。
b.溶接痕の制御
· 溶接痕のサイズ:溶接痕のサイズは厳密に制御する必要があります。一般的に、溶接痕の高さは4/6mmの範囲内である必要があり、製品の外観と組み立て精度を確保するために、溶接痕は平面を超えないようにする必要があります。たとえば、液体冷却プレートプロジェクトでは、溶接パラメータとプロセスを調整することで溶接痕のサイズをうまく制御し、溶接痕が製品の性能と品質に与える影響を回避しました。
· 溶接痕の形状:溶接痕の形状は、過度の溶融や不完全な融合を避けるために、できるだけ規則的である必要があります。溶接パラメータと操作技術を最適化することで、溶接痕の形状を効果的に改善し、溶接品質を向上させることができます。
· 研磨処理:摩擦溶接位置で生成される凹状の溶接痕には、研磨処理を使用して滑らかな表面を確保し、製品の外観と性能の要件を満たします。
c. 溶接シーケンスの最適化
· パーティション溶接:大型製品の場合、パーティション溶接法は全体の変形を効果的に制御できます。製品をいくつかの領域に分割し、それらを順番に溶接することで、溶接プロセス中の熱集中を減らし、熱変形のリスクを減らすことができます。
· ステップバイステップの修正:溶接プロセス中に、ステップバイステップの修正方法を使用して、溶接変形を時間内に調整します。溶接プロセス中に製品の変形を継続的に測定して修正することにより、最終製品の寸法精度と形状が設計要件を満たすことが保証されます。
· 溶接パスの最適化:同じ領域での繰り返し溶接を回避し、熱入力を減らすために、溶接パスを合理的に計画します。たとえば、液体冷却プレートプロジェクトでは、溶接パスを最適化することで、溶接プロセス中の熱入力が減り、溶接品質が向上しました。
d. 変形の協調制御
液体冷却プレートは溶接プロセス中に熱変形を起こし、製品の寸法精度が低下します。
最適化対策:
· パーティション溶接と段階的な修正方法を使用して、全体的な変形を制御します。
· 溶接パラメータを最適化し、電流と電圧を減らし、熱入力を減らします。
· 固定具を使用して製品を固定し、溶接中の動きと変形を減らします。
· 対称溶接方法を使用して、溶接熱を均等に分散します。
ご参考になるために、定期に熱設計及び軽量化に関する技術と情報を更新させていただきます。当社にご関心をお持ちいただき、ありがとうございます。
CTC(セルツーシャーシ)技術は、電気自動車の航続距離とスペース効率を大幅に向上できるため、多くの注目を集めていますが、従来のバッテリー技術を本当に置き換えることができるかどうかはまだ議論の余地があります。製造側の中心的なボトルネックであるバッテリートレイの溶接プロセスは、この技術の将来を決定する鍵となっています。複雑な構造設計、複数の材料の互換性、厳格な熱管理要件により、従来の溶接技術は大きな試練にさらされています。この記事では、第一線のエンジニアの視点から、業界のトレンドとエンジニアリングの実践を組み合わせて、CTC技術の可能性と限界を分析し、溶接技術がどのようにしてこの技術革命の「試金石」になったかを探ります。
1-CTC技術の「理想と現実」
CTC技術は、理論的にはバッテリーセルをシャーシに直接統合することで冗長な構造部品を減らし、エネルギー密度を向上させることができますが、その大規模適用の実現可能性は現実的な課題に直面しています。
自動車会社の急進性と慎重さ:テスラ、BYDなどの大手企業はCTCソリューションを立ち上げていますが、多くのメーカーはまだ様子見しています。業界データによると、2025年2月時点で、CTC量産モデルは世界の15〜20%を占めており、従来のCTP(Cell-to-Pack)技術が依然として主流です。
バッテリー寿命の向上の「コスト」:CTCはエネルギー密度を15%〜20%向上させることができますが、シャーシ構造の複雑さにより製造コストが30%〜50%増加します(コンサルティング機関による計算)。コストと利益のバランスはまだ明確ではありません。
メンテナンスの経済論争:統合設計により、バッテリーのメンテナンスコストが急騰しました。保険会社のデータによると、CTCモデルの事故後のバッテリーアセンブリの交換率は70%と高く、従来のモデルの25%をはるかに上回っています。
これらの矛盾により、CTC技術の将来は変数に満ちています。市場が20%を突破できるかどうかは、3つの主要な変数に依存します。テスラサイバートラックの量産の進捗状況、中国の自動車メーカー間の価格戦争によりCTCがコスト削減を余儀なくされるかどうか、およびバッテリーの修理可能性に関する欧州規制の妥協の程度です。製造側の溶接技術レベルは、研究室と量産の間のギャップを乗り越えられるかどうかを決定する鍵となります。
2-溶接工程の3つの「生死の壁」
バッテリートレイメーカーにとって、CTC技術の導入は3つの核心問題を克服する必要があります。
a. 「ミクロンレベル」の精度と効率の勝負
従来の溶接工程では0.5mmの誤差を許容できますが、CTCトレイではより多くのバッテリーを搭載する必要があり、継ぎ目の数は3倍以上になり、そのほとんどは湾曲した不規則な部分に分布しています。メーカーのテストによると、溶接位置の誤差が0.15mmを超えると、バッテリーセルアセンブリの歩留まりが99%から82%に急激に低下します。さらに厄介なのは、精度の向上は効率の低下を伴うことが多いことです。レーザー溶接の精度は高いものの、設備コストは従来の溶接の5倍以上です。
b. 混合材料の「水と火」
軽量と強度のバランスをとるために、CTCトレイでは「アルミニウム合金+炭素繊維+特殊鋼」の混合構造がよく使用されます。異なる材料の熱膨張係数の差は最大20倍(アルミニウム23μm/m·K対カーボンファイバー0.8μm/m·Kなど)にもなり、溶接時に内部応力が発生しやすく、割れの原因となります。ある企業がアルミニウムとカーボンファイバーを接合しようとしたところ、溶接部の割れ率は18%にも達し、業界の許容閾値である3%を大きく上回りました。
c. 熱影響部の「見えないキラー」
溶接温度が高いと、バッテリーセル周辺の絶縁材やセンサー回路が損傷する可能性があります。ある自動車会社は、溶接入熱の不適切な制御により、バッテリーモジュールの自己放電率が50%増加したことがありました。エンジニアは、溶接温度の変動を0.1秒以内に±15℃以内に制御する必要があります。これは、溶接ガンに「高精度温度ブレーキ」を取り付けるのと同じです。
3-解決策:特効薬はなく、システム革新のみ
これらの課題に直面して、業界は3つの突破口を模索しています:
a. プロセス組み合わせの「カクテルセラピー」
レーザーアークハイブリッド溶接:レーザー溶接の精度とアーク溶接の浸透の利点を組み合わせることで、アルミニウム合金の溶接速度が40%向上します。
冷間金属遷移技術(CMT):正確な入熱制御により、熱影響部の面積が60%減少します。
ロボットインテリジェント補正システム:リアルタイムの溶接スキャンデータに基づいて溶接ガンのパスを自動的に調整し、複雑な曲面溶接の合格率を75%から95%に向上します。
b. 材料面での「事前妥協」
一部の企業は、材料サプライヤーと共同で「溶接に適した」複合材料の開発を開始しています。例えば、国内の改良アルミ合金(物理的、化学的、またはプロセス手段によって調整されたアルミ合金材料)の溶接割れ感受性は、レベル7からレベル3(ISO規格による)に低下しました。軽量化効果は5%犠牲になりますが、溶接歩留まりは98%に向上します。
c. 検出次元の「デジタルツイン」
溶接プロセスのすべてのデータ(電流、温度、速度など)を収集し、AIモデルと組み合わせて欠陥の確率を予測します。ある工場がこの技術を導入した後、溶接欠陥のオンライン検出率は80%から97%に向上し、スクラップコストは45%削減されました。
4- エンジニアの新たな提案:不確実性の中に確実性を見出す
a. CTC 技術をめぐる論争は、本質的には「システム最適化」と「局所的限界」の間のゲームです。
溶接プロセスのブレークスルー速度が自動車会社のコスト削減期待よりも遅い場合、CTC はニッチな技術になる可能性があります。
材料、プロセス、テスト技術が協調してブレークスルーを達成した場合、電気自動車の構造設計の新しい時代が到来すると予想されます。
b. エンジニアにとって、次の 2 つの側面から能力を再構築する必要があります。
クロスドメイン知識の統合:溶接熱入力に対する電気化学特性の敏感な閾値を理解する。
アジャイル対応能力:ヨーロッパのサプライヤーのケーススタディでは、新しい合金材料の溶接パラメータの最適化を 1 週間以内に完了できるチームは、受注の確率が 3 倍に増加することが示されています。
CTC 技術は、「破壊的イノベーション」と「大量生産の罠」の岐路に立っています。既存の技術を完全に置き換えることはできないかもしれませんが、溶接プロセスをより高い精度、より強力な互換性、よりインテリジェントな制御に向けて進化させています。この技術マラソンで本当の勝者は、最も早くこの技術を開発した自動車会社ではなく、製造側で「不可能な溶接」を「標準化されたインターフェース」に変えるエンジニアリング チームかもしれません。
ご参考になるために、定期に熱設計及び軽量化に関する技術と情報を更新させていただきます。当社にご関心をお持ちいただき、ありがとうございます。
CTP(セル・トゥ・パック)技術が従来のバッテリーパック構造を完全に覆すにつれて、バッテリートレイの「役割」は受動的な荷重支持から能動的な統合へと移行しました。溶接技術は安全性と性能の中核となっています。軽量(壁厚はわずか1.5mm)、気孔ゼロの密閉、マルチマテリアル(アルミニウム/銅/カーボンファイバー)統合の要件により、従来の溶接は変形と欠陥のジレンマに陥っています。業界は、材料の革新、インテリジェントな品質検査、プロセスの反復を通じて飛躍的な進歩を遂げています。この記事では、CTPが溶接にもたらす破壊的な課題を分析し、高精度と高信頼性への技術的な道を探ります。
1-CTP技術によるバッテリートレイの構造設計要件の変化の分析
CTP(Cell to Pack)技術は、従来のバッテリーパックのモジュール構造を排除し、バッテリーセルをバッテリーパックに直接統合します。この技術革新は、バッテリートレイの構造設計に対する全面的かつ多次元的なアップグレード要件を提示しています。以下は、材料、性能、プロセス、統合などの観点からの具体的な分析です。
(1)構造強度と耐衝撃性能の総合的な向上
a. モジュールを排除した後の機械的支持要件:
CTP技術によりモジュール構造が排除された後、バッテリートレイはバッテリーセルのサポート、固定、外力緩衝機能を直接担う必要があります。従来のモジュールは機械的負荷を分散しますが、CTPトレイは充電および放電中にバッテリーセルの膨張変形を全体として吸収する必要があります(たとえば、角型バッテリーセルの膨張力は10〜20kNに達することがあります)。また、車両走行中の振動、押し出し、衝撃負荷に耐えます。
b.材料と構造の最適化方向
· 高強度アルミ合金の優位性:初期の鋼は重量が重いため徐々に置き換えられ、6061-T6が主流になりました。比強度が高く、耐腐食性が強く、軽量と高剛性の2つの要件を満たすことができます。
· 複合構造設計:たとえば、Leapmotorの「ダブルフレームリングビーム」構造は、縦方向と横方向のビームコンパートメントを通じて局所的な耐衝撃性を高めると同時に、押し出し技術を使用して材料の分布を最適化し、余分な重量を減らします。
· マグネシウムアルミニウム合金と炭素繊維の探求:マグネシウムアルミニウム合金は従来のアルミニウム材料よりも30%軽量で、炭素繊維複合材料は高強度と軽量の両方の特性を備えていますが、コストとプロセスの成熟度のため、現在はハイエンドモデルにのみ使用されています。
(2)統合気密性と熱管理の要件
a. 密閉性能の向上
モジュールを取り外した後、バッテリーパックの内部冷却剤循環とガス密閉は完全にトレイに依存し、溶接欠陥(気孔や亀裂など)により漏れのリスクが生じる可能性があります。
図1-バッテリートレイの気密性テスト
b. 熱管理機能の統合
CTP トレイには、液体冷却プレートや熱伝導性接着剤などのコンポーネントを統合する必要があります。たとえば、構造用接着剤はバッテリー セルを固定して膨張応力を伝達するために使用され、ポリウレタン熱伝導性接着剤 (熱伝導率 > 1.5 W/m·K) はバッテリー セル間および液体冷却チューブとの熱伝導に使用されます。1 つの PACK で使用される接着剤の量は、従来の構造よりも 50% 以上多くなります。トレイ内に流路を設計して冷却効率を最適化し、溶接の熱影響部によるシーリングの損傷を回避する必要があります。
(3) 軽量化と材料の革新
a. 材料選択の傾向
アルミニウム合金の押し出しおよびダイカスト プロセス: 押し出しアルミニウム プロファイルはフレーム構造 (Tesla の 4680 バッテリー トレイなど) に使用され、ダイカスト プロセス (統合ダイカストなど) は溶接プロセスを簡素化し、重量を 15% ~ 20% 削減します。
プラスチック複合材料の応用:例えば、非荷重部品にはガラス繊維強化PA6材料を使用し、さらなる軽量化を図っていますが、金属接続インターフェースとの互換性の問題を解決する必要があります。
b. 軽量設計戦略
トポロジー最適化:CAEシミュレーションにより冗長材料を削減し、強度を確保しながらトレイの重量を削減します。
薄肉・一体化:トレイの壁厚を3mmから1.5~2mmに減らし、BMSブラケットやワイヤーハーネスチャネルなどの機能部品を一体化して部品点数を削減します。
(4)一体化・モジュール設計
a. 機能部品の高一体化
CTPトレイには、バッテリー管理システム(BMS)、高電圧コネクタ、耐火絶縁層などのモジュールを一体化する必要があります。
b. モジュール化・互換設計
溶接生産ラインは、複数モデルのトレイの混合生産をサポートし、「ワンクリックタイプ変更」を実現でき、異なるバッテリーセルサイズ(角型や円筒型など)のトレイ構造と互換性がある必要があります。
2-CTP 技術革新による溶接プロセスへの特有の課題
CTP (Cell to Pack) 技術は、スペース利用率とエネルギー密度を大幅に向上させましたが、溶接プロセスに前例のない課題ももたらしました。
(1) 溶接欠陥の制御の難しさが急激に増加
a. 気孔とシーリングの課題
CTP 技術によってモジュールがなくなった後、バッテリー トレイはシーリング機能を直接担う必要があります。溶接気孔 (アルミニウム合金溶接でよく見られる欠陥) は、冷却剤の漏れやガスの浸透のリスクに直接つながります。
b. 亀裂と材料の適合性
亜鉛含有量の高いアルミニウム合金 (7 シリーズなど) は、溶接時の熱応力により亀裂が生じやすくなります。
c. ギャップと組み立てエラー
複数のセルを直接統合すると、トレイ構造の接合点の数が増えます。組み立てエラーが蓄積すると、溶接ギャップが ±1mm を超える可能性があります。
(2) 材料システムのアップグレードによってもたらされるプロセス適応の問題
a.軽量材料の溶接の課題
CTPトレイの材料は、鋼からアルミニウム合金(6061-T6、7075-T6)、マグネシウムアルミニウム合金(30%軽量化)、炭素繊維複合材料に移行しています。アルミニウム合金の溶接では、酸化膜の溶融の難しさと高い熱伝導率によって引き起こされる浸透不足の問題を解決する必要があります。
b. 異種材料接続技術
トレイに液体冷却プレート(銅/アルミニウム)や耐火層(セラミックマトリックス複合材料)などの機能部品を統合すると、異種材料の界面に脆い金属間化合物が発生しやすくなります。
(3)構造の複雑さと精度要件の向上
a. 大型薄肉構造の変形制御
CTPトレイの壁厚は3mmから1.5〜2mmに減少し、溶接熱変形の感度が大幅に増加します。
b.高密度のはんだ接合部とプロセス効率
1 つのトレイ上のはんだ接合部の数は、従来のモジュールの 2,000 個から 5,000 個以上に増加しました。
図2-バッテリートレイの溶接
3-生産プロセスと品質管理のアップグレード
CTP技術は、バッテリートレイ溶接の「単一プロセス」から「マルチテクノロジーコラボレーション、インテリジェント化、グリーン化」への変革を促進します。メーカーは、次の3つの主要な方向に重点を置く必要があります。
技術アップグレード:気孔や亀裂などの欠陥の制御を突破し、軽量材料に適応します。
インテリジェント移行:プロセス全体のデジタル化とAI品質検査により、高精度の生産を実現します。
エコロジカルコラボレーション:材料サプライヤー、機器サプライヤー、OEMと共同で技術標準を構築します。
ご参考になるために、定期に熱設計及び軽量化に関する技術と情報を更新させていただきます。当社にご関心をお持ちいただき、ありがとうございます。
アルミニウム合金などの軽量材料は、その優れた性能により主流となっています。しかし、薄板溶接における入熱制御、変形抑制、プロセス安定性などの課題は、従来の溶接技術にとって大きな障害となっています。コールドメタルトランスファー(CMT)溶接は、入熱が低く、スパッタのない移行、インテリジェントなパラメータ制御という利点があり、バッテリートレイ製造に革新的なソリューションを提供します。
この記事では、バッテリートレイの薄板溶接におけるCMT技術の精密制御戦略を詳しく調べ、その適応性、プロセスの課題、複合アプリケーションシナリオを分析し、効率的で高品質な生産のための理論的かつ実践的なガイダンスを提供することを目指しています。
図1: 104Sエネルギー貯蔵バッテリー液体冷却下部筐体のCMT溶接
1-バッテリートレイ溶接要件とCMT適応性
CMT技術は、低入熱、スパッタフリーの伝達、インテリジェントなパラメータ制御を備えており、バッテリートレイ溶接の高精度、低変形、効率の要求に完全に適合しています。
(1)バッテリートレイ溶接のコアプロセス要件
a. 材料の適合性と軽量化のニーズ
バッテリートレイでは、主に軽量アルミニウム合金(6xxxシリーズ、6061など)または高級モデル用の炭素繊維複合材が使用され、高強度(ベース材料の引張強度の60%~70%)と低密度(アルミニウム合金:2.7g/cm³)が求められます。
異種材料の接合:ハイブリッドスチールアルミニウム構造の場合、変形を最小限に抑えるために熱膨張係数の違いに対処する必要があります。
b. 溶接品質とパフォーマンスメトリクス
低入熱と変形制御:薄板(0.3~3mm)の場合、変形は≤2mmである必要があります。長い直線溶接には、セグメント溶接または変形防止設計が必要です。
シーリングと強度: 電解液の漏れを防ぎ、せん断試験に合格するために、溶接は完全に密封する必要があります (例: T/CWAN 0027-2022 規格)。
気孔率の制御: アルミニウム合金の溶接は気孔が発生しやすいため、気孔率は 0.5% 以下である必要があります。
c. 生産効率と自動化の要件
バッチ生産では、溶接速度が 7mm/s 以上である必要があり、シングルトレイ溶接の時間が 5~10 分に短縮されます。
自動化されたワークステーションは、デュアルステーション設計 (同時組み立てと溶接) とマルチロボットのコラボレーションをサポートする必要があります。
(2)バッテリートレイ溶接におけるCMTの主な利点
a. 高精度の低入熱制御
CMTは、溶滴短絡時に溶接ワイヤを後退させて電流を遮断することで、従来のMIG溶接に比べて入熱を33%削減し、極薄プレート(0.3mm)の溶損リスクを排除します。
交互の冷熱サイクル(アーク加熱-溶滴移動-ワイヤ後退)により、熱蓄積を最小限に抑え、変形を≤1.5mmに制御します(BYDおよびBAICのケーススタディ)。
b. プロセスの安定性と品質の向上
スパッタフリー溶接:機械的な後退により、溶滴のスパッタがなくなり、手直しが減ります。
気孔率の最適化:Ar+30%Heシールドガスを使用すると、気孔サイズが≤0.3mmで、純粋なArに比べて気孔率が50%削減されます。
高いギャップ許容度:最大1.5mmのアセンブリギャップに対応し、固定具の精度要件を下げます。
c.自動化の統合と効率の向上
デュアルステーションワークステーション(例:Taixiang Tech 設計)により、並行溶接と組み立てが可能になり、効率が 2 倍になります。
変形防止設計による対称ロボット溶接(デュアルロボット同期)により、サイクル時間が 10 分以下に短縮されます。
2-バッテリートレイのCMTプロセスにおける課題
図2: CMT溶接プロセスフロー
(1)材料特性と溶接欠陥制御
a. アルミニウム合金溶接における気孔感受性
アルミニウム合金トレイ(例:6061、6063)は、急速凝固と水素溶解度の変化により気孔が発生しやすくなります。シールドガスの組成は重要です。純粋なArでは気孔率は約5%ですが、Ar+30%Heでは気孔率は≤0.5%に低下します。インダクタンス調整(例:ネガティブチューニング)により溶融池の流れが最適化され、気孔サイズが最小限に抑えられます。
b. 高温割れと組成偏析
アルミニウム合金中のMg、Siなどの偏析は粒界脆化を引き起こす可能性があります。CMTの低入熱によりHAZは減少しますが、不十分な溶け込みや局所的な過熱を回避するには、溶接速度とワイヤ供給を正確に制御する必要があります。
c.異種材料溶接における冶金適合性
Al-鋼またはAl-複合材料接合部(クラッシュビームやエンクロージャなど)の界面では、脆性相(FeAl₃など)とZn蒸気の干渉を軽減する必要があります。
(2)プロセスパラメータ最適化の課題
a. 溶け込みと入熱のバランス
溶接は、溶け込み深さ(≥0.8mm)に関するT/CWAN 0027規格を満たす必要があります。CMTの入熱が低いと溶け込みが不十分になる可能性があり、溶け込みを強化するためにアーク長の調整またはパルス電流が必要になります。
b. 速度と安定性のトレードオフ
自動化ラインでは1.2m/分以上の速度が必要ですが、高速ではアークが不安定になったり、溶滴が不均一に転移したりするリスクがあります。
c. 複雑な溶接におけるギャップブリッジ
トレイには、大きなギャップ(0.5~1.5mm)や不規則なジョイント(Tジョイントなど)がよく見られます。
(3)構造設計と製造プロセスの互換性
a. 薄板溶接の変形制御
アルミ合金パレットの壁厚は通常2〜3mmです。従来のMAG溶接の変形は1.2mmに達することがありますが、CMT溶接は低入熱により変形を0.3mm未満に抑えることができます。ただし、精度をさらに向上させるには、変形防止ツール設計とロボット対称溶接(ダブルステーションワークステーション)との連携が必要です。
b. 長い溶接の連続性と密閉
バッテリートレイの密閉溶接の長さは数メートルに達することがあり、アークの破断や溶融池の変動を避ける必要があります。CMT技術は、1秒あたり70回以上のアーク再点火サイクルを通じて溶接の均一性を確保し、レーザー追跡システムにより気密性合格率を99%まで高めることができます。
c.マルチプロセス複合アプリケーションの相乗効果
高級パレットでは、CMT+FSW(摩擦攪拌接合)複合プロセスがよく使用されます。CMTは複雑な構造(フレームと底板の接続など)に使用されます。FSWは高負荷領域(縦梁など)で強度を向上させるために使用されます。2つのプロセスの接続パラメータ(予熱温度や溶接後の熱処理など)のマッチングの問題を解決する必要があります。
3-バッテリートレイ製造におけるCMTプロセスの典型的な適用シナリオ
(1) バッテリートレイの主要構造の接続
a. フレームと底板の溶接
CMTプロセスは、アルミニウム合金バッテリートレイのフレームと底板の接続に広く使用されており、特に長い溶接部と薄いプレート(厚さ2〜3mm)に使用されます
b. ビームと底板の接続
CTPバッテリートレイの設計では、ビームの数が少なく構造が複雑なため、CMTプロセスは次の目的で使用されます:高精度の位置決め溶接:ビームと底板(Tジョイントなど)のローカル接続では、浸透不足を回避する必要があります。CMTは、デジタルアーク長制御(Fonis CMT Advancedテクノロジーなど)により、安定した浸透≥ 0.8mmを実現します。マルチマテリアル適応:ビームがアルミニウムマグネシウム合金(6061など)で作られ、底板が高強度アルミニウムである場合、CMTはAr+He混合ガス保護を通じて気孔を減らし、異なる材料の熱伝導率の違いに適応できます。
(2) 薄板および複雑な幾何学的構造の溶接
a. 薄壁アルミ合金溶接 (2-3mm)
バッテリートレイの軽量化の要求により薄板の適用が促進されますが、従来の MIG 溶接は変形しやすい傾向があります。CMT プロセスの利点は次のとおりです。
b. 超薄板溶接: Taixiang Automation は CMT 技術を使用して、バッテリートレイのエッジシール構造用の 0.3mm の超薄板のスパッタフリー溶接を実現します。
c. 特殊形状溶接のブリッジ: トレイの内部補強リブや衝突防止ビームなどの特殊形状構造の場合、CMT ギャップブリッジモードは、ワイヤの引き込みとアークの方向転換により 0.5-1.5mm のギャップを埋め、未融合欠陥を回避できます。
d. 高いシール要件の溶接: バッテリートレイのシールは、バッテリーの安全性に直接関係しています。 CMT プロセスは、次の方法でこれを保証します:
· 連続した長い溶接: 1 秒あたり 70 回以上のアーク再点火サイクル (Fronius LaserHybrid テクノロジーなど) を使用して、数メートルの溶接の連続性を確保し、気密合格率は 99% です。
· 低入熱制御: レーザー溶接と比較して、CMT は入熱が低いため、溶融池の変動によるシーラント層への熱影響が軽減され、接着剤コーティング プロセスに適しています。
(3) マルチプロセス複合製造シナリオ
a. CMT+FSW 複合プロセス
ハイエンドのバッテリートレイ生産ラインでは、CMT は摩擦撹拌溶接 (FSW) と連携することがよくあります。
分業と協力: CMT は複雑な構造 (フレームや特殊形状のジョイントなど) の柔軟な溶接に使用され、FSW は高負荷領域 (縦梁など) に使用され、強度が向上します。たとえば、上海 Weisheng の自動化生産ラインでは、CMT+FSW+CNC の組み合わせを使用して、トレイの生産効率を 30% 向上させています。
プロセス接続の最適化: Huashu Jinming の生産ラインはモジュール設計を採用しており、予熱パラメータのマッチング (CMT 溶接後の 150°C への局所加熱など) により、FSW とのシームレスな接続を実現しています。
b. FDS/SPRリベット技術との組み合わせ
第2世代CTP技術では、CMTは摩擦セルフタイトニング(FDS)とセルフピアスリベット(SPR)技術と連携しています。ハイブリッド接続ソリューション:たとえば、フレームと底板の耐荷重領域にはFSWを採用し、取り外し可能な部品(水冷プレートや絶縁層など)はCMT溶接で事前配置してからFDSリベットで固定し、強度とメンテナンスの利便性の両方を考慮しています。
ご参考になるために、定期に熱設計及び軽量化に関する技術と情報を更新させていただきます。当社にご関心をお持ちいただき、ありがとうございます。
新エネルギー車およびエネルギー貯蔵分野の爆発的成長により、電池トレイ溶接技術は製造プロセスの核心戦場に位置づけられています。アルミニウム合金の軽量化と複雑構造という二重の課題に直面する中、本稿ではプロセスの本質から工学的実践までを深掘りし、従来の溶融溶接、摩擦攪拌接合(FSW)、レーザー溶接の原理、性能指標、適用シーンを比較します。熱影響域(HAZ)、接合強度、耐食性などの多角的分析を通じて、各溶接技術の優劣を明らかにします。
1-技術原理の比較
a. 従来の溶融溶接
原理: アークやプラズマアークなどの熱源により接合部を局所加熱し、溶融状態の溶融池を形成。冷却後に凝固して溶接ビードを形成します。保護ガス(CO₂、アルゴンなど)やフラックスを用いて酸化を防止し、必要に応じて溶加材(ワイヤやロッド)を添加します。
特徴: 溶融池の温度が高く冷却速度が速いため、粗大な柱状晶が発生。熱影響域(HAZ)が広く、冶金反応が不十分で、気孔や割れなどの欠陥が生じやすい。
b. 摩擦攪拌接合(FSW)
原理: 高速回転する攪拌ピンとワークの摩擦熱を利用し、材料を熱可塑状態にします。機械的な攪拌と塑性流動により固相接合を実現。溶融池を形成せず、溶加材も不要です。
特徴: 材料の融点より約80%低い温度で接合。動的再結晶により微細な等軸晶が形成され、気孔のない緻密な溶接部を実現。熱入力が低く変形が小さい。
c. レーザー溶接
原理: 高エネルギー密度のレーザービームをワーク表面に集中照射し、熱伝導(出力密度<10⁵ W/cm²)または深熔融溶接(出力密度≥10⁵ W/cm²、キーホール効果)により材料を溶融・接合します。
特徴: 熱影響域(HAZ)が極めて狭く、溶込み深さが大きく、高速溶接が可能。ただし材料表面の反射率に敏感で、プロセスパラメータの厳密な制御が必要。
a-従来の溶融溶接 b-摩擦攪拌接合 c-レーザー溶接
図1 電池トレイの主要溶接技術の原理
2-性能指標の比較
a. 熱影響域(HAZ)の比較
キーポイント分析:
従来の溶融溶接: 高熱入力によりHAZが広く、結晶粒の粗大化や冶金欠陥(気孔)が材料性能を低下させる。
FSW: 固相接合により溶融池がなく、HAZはTMAZとHAZに分かれ、微細結晶(NZ)と局所変形(TMAZ)が共存。
レーザー溶接: 高エネルギー密度と急速冷却によりHAZ幅が極狭(約0.1-0.5mm)。ただしキーホール効果による組織均一性への影響に注意。
b.接合強度の比較
キーポイント分析:
従来の溶融溶接: 急速凝固による粗大結晶と欠陥で接合強度が低下(例:MIG溶接のアルミ合金は母材強度の72.8%)。
FSW: 動的再結晶で微細結晶(NZ)を形成するが、TMAZの結晶粒変形やHAZの強化相溶解が弱点に。
レーザー溶接: 高冷却速度により結晶粒粗大化を抑制、母材に近い強度を実現。
c. 耐食性の比較
キーポイント分析:
従来の溶融溶接: 粗大結晶と欠陥によりHAZや溶融線で腐食が優先発生。
FSW: NZは微細結晶と均質化で耐食性が高いが、HAZの結晶粗大化や第二相析出(Fe含有相など)が腐食の弱点に。
レーザー溶接: 狭いHAZと均一組織で腐食活性点が少ないが、表面酸化層の影響に注意。
3-適用シーン
a. 従来の溶融溶接
・ 適用部位:
フレームと底板の接合: 電池トレイの主要構造(例:BYD、北汽の車種でアルミ型材フレームと底板を断続溶接または全溶接)。
補助部品の補修溶接: 複雑構造や空間制限のある辺梁・補強材などで他技術(FSWなど)と併用。
・ 適用工件:
厚板溶接(鋼製トレイやアルミ厚板)。
非密閉性の補助構造(電池パックの角部固定部品など)。
・ 適用材料:
アルミニウム合金: 6061-T6などの6シリーズ厚板(接合強度は母材の70%-80%)。
鋼材: 鋼製トレイのフレーム溶接(コスト低但し重量大)。
・ 制約:
高熱入力による変形が大きく、高精度・薄板溶接には不向き。
b. 摩擦攪拌接合(FSW)
・ 適用部位:
底板の長手継ぎ: アルミ合金トレイの底板の長い溶接継手、水冷チャネルの一体構造など(例:Guangdong Walmate Tech の水冷チャンネル一体構造)。
高密閉性領域: 電池トレイと箱体の接合部(FSWの気孔なし溶接で密閉性確保、吉利・Xpeng車種の両面FSW構造)。
複雑型材接合: アルミ押出型材のT型接合・中空型材溶接(両軸ショルダーFSW技術で自立溶接可能)。
・ 適用工件:
アルミ押出型材(例:底板厚10mm・壁厚2mmの二重断面設計)。
異種材料接合(Al/Cu、Al/Mgなど、特殊プロセス調整必要)。
・ 適用材料:
アルミニウム合金: 6061-T6、6005A-T6、6063-T6が主流(接合強度は母材の80%-90%)。
マグネシウム合金: 軽量トレイ(例:瑞松科技事例)但し結晶粒粗大化防止のため熱入力制御要。
・ 技術優位性:
溶融欠陥を回避した固相接合で、軽量化・高密閉性シーンに適す。
c-レーザー溶接
・ 適用部位:
高強度鋼トレイの重要接合部: 車体との接合など高応力領域。
精密シールピン溶接: トレイ蓋板のシールピン溶接(速度40mm/s、HAZ極狭)。
薄板接合: アルミ/鋼製トレイの薄板(<3mm)高効率接合(変形低減)。
・ 適用工件:
高精度・自動化ライン(ロボットレーザー溶接システム)。
曲面溶接など異形構造(高速位置決めシステム併用要)。
・ 適用材料:
高強度鋼: 引張強度≥1000MPa(母材強度の95%保持)。
アルミニウム合金: 反射率低減のため表面処理(陽極酸化など)必要(コスト高)。
・ 制約:
厚板溶接(例:アルミ>8mm)は多パス必要でFSWより効率低下。
ご参考になるために、定期に熱設計及び軽量化に関する技術と情報を更新させていただきます。当社にご関心をお持ちいただき、ありがとうございます。
私はバッテリートレイメーカーの第一線エンジニアとして、複数の新エネルギー車用バッテリーシェルプロジェクトに参加し、「軽量・安全・コスト」の三角関係における業界の駆け引きを深く理解しています。この記事では、材料ルート、製造プロセス、将来の動向という3つの側面から、現在の技術ルートの選択ロジックと産業化の課題を分析し、実際の事例を組み合わせます。
1-材料ルート:軽量化とコストのトレードオフ
バッテリーシェルの材料の選択は、車両全体の性能と経済性に直接影響します。現在の主流ルートは、アルミニウム合金、高強度鋼、複合材料の3つのカテゴリにまとめられ、それぞれに独自の適用シナリオがあります。
a. アルミニウム合金ルート:軽量化の主力
· 押し出しアルミプロファイル:BYDの多くのモデルのバッテリーシェルは押し出しアルミプロファイルで作られており、断面形状を最適化することで軽量化を実現し、構造剛性を向上させています。
· ダイカスト統合:テスラの4680バッテリーはCTC技術と組み合わせて50%以上の軽量化を実現していますが、金型コストは2億元を超え、コストを希釈するには年間50万個以上の生産が必要であり、大手自動車会社の大規模生産に適しています。
· 複合アルミニウム:ポルシェ タイカンはアルミニウムと炭素繊維のハイブリッド構造を採用し、重量がさらに 15% 軽減されますが、コストが 30% 増加し、高級モデルに限定されます。
b. 高強度鋼ルート:コストに敏感な市場での反撃
熱間成形鋼(22MnB5 など)は、降伏強度が 1500MPa、商用車への浸透率が 40% を超え、1GWh あたりのコストがアルミニウムより 40% 低くなりますが、エネルギー密度が約 8% 犠牲になります。そのため、コストと基本的な安全性の両方を考慮して、10 万元未満のモデルでは高強度鋼が一般的に使用されます。
c.複合材料:ハイエンドの試み
· SMC材料:バッテリーパックの上部シェルはガラス繊維強化複合材料を使用しており、スチールより30%軽量ですが、耐衝撃性の欠点は厚さを増やすことで補う必要があります(3mm+5mmの補強)。
· 炭素繊維:BMW i3のシェルはアルミニウムより50%軽量ですが、コストは800元/ kgと高く、大量生産は困難です。現在は高級モデルにのみ使用されています。
実践の要約:材料の選択はモデルの位置付けに合わせる必要があります。ミッドレンジ市場(20万〜30万元)は主にアルミニウムベースの材料であり、ローエンド市場は高強度鋼に依存し、高級モデルは炭素繊維複合ソリューションを模索しています。
2- 製造プロセス:効率と信頼性のバランス
バッテリーシェルの製造プロセスは、生産効率と製品の信頼性に直接影響します。現在主流の技術ルートには、ダイカスト、押し出し溶接、構造統合技術が含まれます。
a. ダイカストvs.押し出し溶接
· 押し出しアルミプロファイル(GMボルトが使用):1個あたりのコストは約800元で、大量生産に適していますが、プロセスが複雑です。
· ダイカストアルミ(NIO ET5):1個あたりのコストは1,500元ですが、生産効率は5倍に向上し、急速な生産需要に適しています。
· 摩擦撹拌溶接(FSW):従来のアーク溶接と比較して、変形が50%減少し、耐疲労性が30%向上しますが、設備投資を40%増やす必要があり、寿命要件の高い商用車に適しています。
b.構造統合技術
· CTPモジュール化(CATL Kirinバッテリー):スペース利用率が72%から85%に向上し、コストが15〜20%削減されましたが、熱暴走防止設計を強化する必要があります。
· CTCシャーシ統合(Tesla Model Y):部品が370個削減され、バッテリー寿命が54%増加しましたが、メンテナンスコストが300%増加し、アフターサービス体制に課題が生じています。
主要データの比較
生産ラインの経験:CTP 技術は互換性が高いため、現在でも主流ですが、CTC は自動車会社とバッテリーメーカーの緊密な連携が必要であり、短期間で普及する可能性は低いです。
3- 将来の動向:技術統合とインテリジェントアップグレード
a. 材料複合
アルミニウム/カーボンファイバーハイブリッドシェル(ポルシェタイカンコンセプトなど)は、重量を15%削減し、800MPaの圧縮強度を達成できますが、界面の結合強度は25MPa以上である必要があり(トヨタbZ4Xの量産認定率はわずか65%)、プロセスの安定性を突破する必要があります。
b. 機能統合イノベーション
· 液体冷却プレートとシェルの統合(GACマガジンバッテリー):冷却接触面積が50%増加し、温度差制御が<5℃ですが、アルミニウムと銅の異種溶接多孔度をレーザースイング溶接で最適化する必要があります。
· 組み込み光ファイバーセンサー(コンチネンタルグループのソリューション):シェルのひずみと温度をリアルタイムで監視し、BMS応答速度が30%向上しましたが、センサーの耐久性の問題を解決する必要があります。
c.グリーン循環システム
BMWのリサイクルアルミニウムの閉ループリサイクル技術は、炭素排出量を60%削減しますが、リサイクル材料の性能損失を10%以内に抑える必要があります。さらに、大型薄肉ダイカスト(LK 9000Tダイカストマシンなど)では、金型温度差(±5℃)の精密制御が必要であり、バリ洗浄効率が量産のボトルネックになります。
プロセスのブレークスルーの方向性:
·複合材料成形サイクルの圧縮(LGF-PP射出成形サイクルを180秒から90秒に短縮する必要があるなど)
·デジタルツイン技術を適用して衝突シミュレーションエラーを±20%から±5%に削減し、設計の信頼性を向上します。
4- 市場の階層化と産業化の見通し
短期(1~3年):CTP+押し出しアルミプロファイルは依然として主流であり、CATLは34%の市場シェアで引き続きリードしています。
中期(5~10年):CTCと炭素繊維はハイエンド市場への浸透を加速しており、2030年には炭素繊維が25%を占めると予想されています。
長期目標:エネルギー密度は400Wh/kgを突破し、同時に国家標準の30分間の熱暴走保護に基づいて、安全性の冗長性をさらに向上させます。
5-結論
バッテリーハウジングの技術ルートを選択する際の本質は「シナリオに基づく適応」であり、自動車会社の位置付け、コスト閾値、サプライチェーンの成熟度を総合的に考慮する必要があります。エンジニアとして、私たちは材料とプロセスの革新を受け入れ、大量生産の実現可能性にも焦点を当て、軽量化、安全性、コストの動的なバランスの中で最適なソリューションを見つけなければなりません。将来、インテリジェントでグリーンな製造技術の成熟に伴い、バッテリーハウジングは徐々に「受動的な保護」から「能動的な安全」へと移行し、新エネルギー車の完全な普及にしっかりとしたサポートを提供します。
ご参考になるために、定期に熱設計及び軽量化に関する技術と情報を更新させていただきます。当社にご関心をお持ちいただき、ありがとうございます。
実際の製造、組み立て、使用のプロセスでは、バッテリートレイの絶縁耐電圧障害が頻繁に発生し、新エネルギー産業の急速な発展に隠れた暗礁のように、車両の運転安全性とエネルギー貯蔵システムの信頼性の高い動作を脅かしています。この記事では、製造の実践に基づいて典型的な障害モードを分析し、関連する実務者に表面的な参考資料を提供し、業界の同僚が共同でバッテリートレイの絶縁耐電圧性能を向上させる効果的な方法を模索するのに役立ちます。
パート 3 - 一般的な故障分析
図1 絶縁耐電圧試験
1- 一般的な故障メカニズムの分析
エネルギー貯蔵用バッテリートレイと新エネルギー自動車用バッテリートレイの適用シナリオは異なり、絶縁耐電圧要件と故障条件には共通点と相違点の両方があります。次のようになります。
a. 相違点
動的負荷: 新エネルギー自動車は 20~2000Hz の高周波機械的振動に対処する必要がありますが、エネルギー貯蔵システムは主に長期の静的変形に直面し、累積変形時間は 10 年を超えます。
電圧レベル: 新エネルギー自動車用バッテリートレイの絶縁耐電圧は 3000VDC 以上 (GB 38031 に基づく) に達する必要がありますが、エネルギー貯蔵システムには 4200VAC 以上の絶縁耐電圧が必要です (IEC 61439 に基づく)。
故障加速要因: 新エネルギー自動車は年間 2000 回以上の充放電サイクルにより熱応力を生じ、絶縁故障を加速します。エネルギー貯蔵システムは24時間365日稼働し、年間平均稼働時間は8000時間を超えているため、電気化学的劣化が起こり、絶縁不良が加速します。
b. 共通点
どちらも、絶縁抵抗モニタリング(低温状態で100MΩ以上、高温状態で1MΩ/kV以上)と部分放電制御(5pC未満)を通じて、絶縁不良の早期警告を実現する必要があります。
2- バッテリートレイの絶縁耐電圧不良を引き起こす一般的な製造欠陥
(1) 絶縁耐電圧構築段階
a. 潜在的な不良と原因分析
· 材料欠陥:
原因: 絶縁材料の耐電圧レベルが不十分、湿気または表面汚染 (油汚れ、金属片) による劣化。
性能: 絶縁抵抗が低い (<100MΩ)、漏れ電流が標準を超える、または耐電圧テスト中に直接破壊。
· プロセスの問題:
原因: 残留金属片 (粗い溶接/切断プロセス)、絶縁コーティングの厚さが不均一または未硬化。
性能: 部分放電、絶縁層の損傷により短絡が発生する。
· 環境干渉:
原因: 高温と高湿度により、材料の吸湿と化学腐食が発生する。
性能: 環境によって絶縁性能が低下し、凝縮水により沿面距離が長くなる。
· テストエラー:
原因: テスト電圧/時間の設定が間違っている (GB/T 38661 規格に準拠していないなど)、接地が不十分。
パフォーマンス: 適格性の判断ミス、またはコンポーネントへの過電圧による損傷。
b. 対応戦略
· 材料の最適化: 耐電圧が 1000V DC 以上の防湿材料 (炭素繊維複合材料など) を選択し、防汚コーティングを施します。
· プロセス管理: 自動溶接/スプレー装置を使用し、クリーンな作業場を準備します。
· 環境管理: 建設前に温度と湿度の監視装置を設置し、材料を事前に乾燥させます。
· テスト仕様: セグメント化されたテスト (500V 事前テスト + 1000V 正式テスト)、機器の校正、データの記録。
(2) モジュール設置段階
a. 潜在的な障害と原因の分析
· 組み立てエラー:
原因: 絶縁ライナーが欠落しており、ボルトが締めすぎているため絶縁層が損傷しています。
性能: モジュールとシェル間の絶縁抵抗が低く、耐電圧破壊が発生しています。
· 機械的損傷
原因: 取り扱いツールの傷、金属片が絶縁フィルムを突き刺しています。
性能: 動作中に局所的な短絡または突然の故障が発生します。
· 設計の互換性
原因: モジュールとトレイのサイズ偏差による電気的クリアランス不足。
性能: 寄生容量により電圧重畳破壊が発生します。
· 電気接続の危険性:
原因: 配線ハーネスが固定されていないためにコネクタシールが摩耗および故障します。
性能: 高電圧配線ハーネスの絶縁層が摩耗および漏れます。
b. 対策
· エラー防止設計: 位置決めピンツールを使用して取り付けミスを防ぎ、ボルトの長さをカスタマイズして締めすぎを防ぎます。
· 清掃作業: 取り付け前に掃除機で掃除し、傷防止シリコンでツールを包みます。
· 許容差シミュレーション: CAE でモジュールとトレイのマッチング度を検証し、ギャップが 10mm 以上であることを確認します。
· プロセス検査: 取り付け後、メガオームメーター (≥100MΩ) でランダム検査を行い、セグメント耐電圧テストを実行して障害点を特定します。
(3) システム統合フェーズ
a. 潜在的な障害と原因分析
· システム間インターフェース障害:
原因: コンポーネントの絶縁パラメータが一致しない (コネクタの耐電圧定格の違いなど)。
パフォーマンス: 高電圧バスバー接続の故障または BMS 干渉。
· 寄生容量の重なり:
原因: 複数のモジュールを並列接続すると、寄生容量の合計が増加し、容量上昇の影響が大きくなります。
パフォーマンス: システムレベルのテスト漏れ電流が標準を超えています。
· 環境ストレス障害:
原因: 振動により絶縁疲労が発生し、高電圧インターフェースに冷却剤が浸透します。
パフォーマンス: 動作中に絶縁抵抗が定期的に低下します。
· テストの盲点:
原因: 実際の動作条件 (高温/振動/湿度) をシミュレートできませんでした。
パフォーマンス: 実験室では合格しましたが、実際の動作では不合格でした。
b. 対策
· 互換性設計: サプライヤのコンポーネント標準を統一します。
· 寄生容量制御: ポリイミド絶縁層を追加し、SPICE シミュレーションでレイアウトを最適化します。
· 動作条件シミュレーションテスト: 「-40℃~85℃サイクル + 5Hz~200Hz振動 + 耐電圧」複合テストを実行します。
· インテリジェント監視: 統合オンライン絶縁監視モジュール、AIが潜在的なリスクを予測します。
3-絶縁耐電圧試験
絶縁耐電圧試験は安全対策であると同時に故障の原因となる可能性があります。絶縁耐電圧試験自体が不適切な操作、機器の問題、設計上の欠陥により故障を引き起こし、試験対象機器に二次的な損傷を引き起こすこともあります。
(1)試験中の一般的な故障の種類
(2)対応戦略は次のとおりです
a. テストパラメータの正確な制御
· 電圧と時間:標準に従って設定し、容量性負荷(バッテリーモジュールなど)の動的補正アルゴリズムを有効にして、容量増加の影響を抑制します。
· リーク電流しきい値:機器の仕様(≤10mAなど)に従って設定し、DC/ACモードを区別します(DCテストではより低いしきい値が必要です)。
b. 機器と操作の仕様
· 機器の校正:耐電圧テスターは6か月ごとに校正され、高電圧ラインの絶縁層は毎日目視検査されます。
· 安全な操作:テスト前に低電圧回路を強制的に切断し、ロボットアームまたは自動固定具を使用して高電圧領域に手動で触れないようにします。
c. 故障の予防と修復
· セグメント化されたテスト:モジュール内の複雑なシステムをテストし(最初に高電圧バスをテストし、次にモジュール絶縁をテストするなど)、故障ポイントを特定します。
· 故障修復: 故障後にエポキシ樹脂を使用して損傷領域を充填し、修復後に再度全電圧勾配テストに合格する必要があります (500V→1000V のステップ圧力など)。
d. 環境とデータ管理
· 環境制御: テストエリアの湿度が 75% を超えると除湿器を起動するか、環境が基準を満たすまでテストを延期します。
· データトレーサビリティ: テスト電圧、漏れ電流曲線、環境パラメータを記録し、MES システムを使用して製造バッチ番号を関連付けます。
ご参考になるために、定期に熱設計及び軽量化に関する技術と情報を更新させていただきます。当社にご関心をお持ちいただき、ありがとうございます。
バッテリートレイは、主に漏電を防止し、人員の安全を守り、バッテリーシステムの正常な動作を確保するために絶縁材料を使用します。選択する際には、材料の絶縁特性、耐熱性、化学的安定性、機械的強度を考慮する必要があります。これらの要素が組み合わさって、バッテリートレイ内の絶縁材料の適用効果が決まり、バッテリーシステム全体の安全性と信頼性に影響を与えます。
バッテリートレイの電気絶縁安全性 | パート 2 - 耐圧性能保証
図1 電気自動車のバッテリートレイ
1-絶縁材料の選択とソリューション設計
バッテリートレイの絶縁材料の選択では、材料の誘電特性、環境耐性、および機械的特性に重点が置かれます。以下は、バッテリートレイで一般的に使用される 6 つの絶縁材料とその関連情報です:
ソリューションを設計する際には、通常、アプリケーション シナリオ、パフォーマンス要件、コスト予算という 3 つの重要な要素を総合的に考慮して、適切な絶縁材料を選択する必要があります。例:
(1) アプリケーション シナリオに応じて選択: 高電圧、高電流のエネルギー貯蔵バッテリー システムでは、バッテリー トレイ側に高性能絶縁材料が必要な場合は、PI フィルム アタッチメント ソリューションを使用することをお勧めします。絶縁パフォーマンス要件が高くない場合は、絶縁パウダー スプレー ソリューションを選択できます。バッテリー トレイ底板の場合、低コストの絶縁ソリューションが求められる場合は、絶縁パウダー スプレーまたは絶縁ペイント コーティング ソリューションがより適しています。
(2) パフォーマンス要件に応じて選択: 絶縁パフォーマンス、耐高温性、耐化学腐食性などの要件が高い場合は、PI フィルム アタッチメント ソリューションがより適しています。これらのパフォーマンス要件が比較的低い場合は、絶縁パウダー スプレーまたは絶縁ペイント コーティング ソリューションでニーズを満たすことができます。
(3) コスト予算に応じて選択: コスト予算が限られている場合は、絶縁パウダー スプレーまたは絶縁ペイント コーティング ソリューションの方が経済的です。コスト予算が十分であれば、PIフィルム貼り付けソリューションを選択できます。
2-バッテリートレイ用PIフィルムの技術要件
(1) 材質: PI、ベースフィルムの厚さ0.1-0.14mm、裏面接着剤の厚さ0.03mm、PIフィルムの熱伝導率> 0.3W/(m·k);
(2) 耐圧性: AC 3000V、60S、漏れ電流≤0.5mA;
(3) (コールドペースト) 180°剥離強度≥15N/24mm;
(4) 絶縁性: DC 1500V、60S、絶縁抵抗>1000MΩ;
(5) 耐熱性および耐電解液性絶縁性能: 500℃、700V DC電圧で2mlの電解液を追加(試験面積13000mm<H>2<H>)、1時間保持、破壊なし、火花なし; (6)耐熱性と絶縁性能:500±2℃で、0.5時間連続ベーキング(マッフル炉)を行い、サンプルの全体的な形態変化プロセスは自然発火せず、サンプルは2回合格しました。表面にAC1000Vを印加し、電圧を0Vから3000Vまで10秒間増加させ、その後60秒間継続します。試験したサンプルには破壊や火花は発生しません。
(7)難燃性グレード:UL94 V-0。
(8)高温高湿:85℃、85%湿度の試験を1000時間行った後、サンプルに亀裂や変形はなく、絶縁抵抗、耐電圧値、電気強度に関する国家規格「GBT 13542.6-2006電気絶縁フィルムパート6:電気絶縁用ポリイミドフィルム」の要件を満たしています。未老化材料と比較して、引張強度、破断伸び、剥離強度は30%未満低下しています。
(9) 高温および低温衝撃: 85℃で1時間、-40℃で1時間切り替え、その後85℃で切り替えて高温および低温サイクルを実施します。切り替え時間は1時間に含まれ、切り替え時間は≤3分です。1000時間の高温および低温サイクル後、サンプルにはひび割れや変形がなく、絶縁抵抗、耐電圧値、および電気強度の要件に関する国家標準「GBT 13542.6-2006電気絶縁フィルムパート6:電気絶縁用ポリイミドフィルム」を満たしています。未老化材料と比較して、引張強度、破断伸び、剥離強度は30%未満低下しています。
(10)塩水噴霧試験:GB/T 10125規格の中性塩水噴霧試験(NSS)試験、温度35℃、湿度≥85%RH、試験溶液は(5±0.1%)(質量分率)NaCl、PH=6.5〜7.2、72時間連続噴霧。塩水噴霧試験後、サンプルにはひび割れや変形がなく、絶縁抵抗、耐電圧値、電気強度の要件について国家規格「GBT 13542.6-2006電気絶縁フィルムパート6:電気絶縁用ポリイミドフィルム」を満たしています。引張強度、破断伸び、剥離強度は、老化していない材料と比較して30%未満に低下しています。
(11)製品はRoHSに準拠しています。
図2 バッテリートレイ用PIフィルム
3-絶縁耐電圧試験方法とよくある問題の解決策
(1) 絶縁耐電圧試験方法
絶縁耐電圧試験は、電気機器の絶縁性能を評価する重要な手段であり、主にDC耐電圧試験とAC耐電圧試験が含まれます。DC耐電圧試験は、DC高電圧を印加して、絶縁材料が指定時間内に破壊されるかどうかを検出します。機器には、DC高電圧発生器、電圧計などが含まれます。手順は、電圧の印加、電圧の維持、電圧の低下です。AC耐電圧試験は、AC高電圧を印加します。機器と手順はDC試験に似ています。どちらの方法も、試験前に準備が必要であり、機器が適切に接地されていること、試験中に絶縁材料の表面状態が注意深く観察されていることを確認する必要があります。
(2) よくある問題と解決策
絶縁耐電圧試験でよくある問題には、絶縁破壊、過度の漏れ電流、試験機器の故障などがあります。絶縁破壊は、絶縁材料の性能不足、内部欠陥、または湿気が原因である可能性があります。解決策には、高品質の材料の選択、メンテナンスの強化、絶縁構造の改善などがあります。過度の漏れ電流は、絶縁抵抗の低下、表面の汚染、またはテスト機器の精度不足によって発生することがあります。解決策としては、絶縁材を清潔で乾燥した状態に保ち、テスト機器を校正することなどが挙げられます。テスト機器の故障は、機器の老朽化、不適切なメンテナンス、または不適切な操作によって発生することがあります。解決策としては、定期的なメンテナンス、正しい操作、およびタイムリーな修理などが挙げられます。
ご参考になるために、定期に熱設計及び軽量化に関する技術と情報を更新させていただきます。当社にご関心をお持ちいただき、ありがとうございます。
新エネルギー車やエネルギー貯蔵技術の急速な発展に伴い、中核的なエネルギーキャリアとしてのバッテリーシステムの安全性と信頼性が大きな注目を集めています。バッテリーモジュールの支持および保護構造として、バッテリートレイの電気絶縁性能は、車両の安全な操作、バッテリーの寿命、およびユーザーの個人の安全に直接関係しています。バッテリートレイの電気安全設計は、バッテリーシステムの安全性の要です。絶縁、構造、熱、監視などの多層保護により、複雑な作業条件下でのバッテリーの安定した動作を保証し、電気故障による火災、爆発、感電のリスクを軽減し、バッテリー寿命を延ばし、システムの信頼性を向上させます。
この記事では、バッテリートレイの電気絶縁安全性に焦点を当て、その設計原理、耐圧性能の検証方法、および典型的な故障ケースの根本原因分析と改善戦略を体系的に説明し、バッテリーシステムの高安全設計に理論的サポートと実用的なリファレンスを提供します。
パート1 - デザインのポイント
バッテリーシステムの電気安全設計の核心は、「予防-制御-緊急」の三位一体にあります。絶縁分離、信頼性の高い接続、熱管理などの対策により故障を防止し、センサーとBMSの助けを借りてリアルタイム制御を実現し、火災防止、圧力緩和などの設計を使用して極端な状況に対処します。メンテナンス性とコンプライアンスを考慮しながら、バッテリーシステムのライフサイクル全体にわたって安全性と信頼性を確保するには、すべての重要なポイントが連携して機能する必要があります。バッテリートレイは、バッテリーシステムの構造サポートであるだけでなく、電気絶縁、熱管理、滑り止め、機械保護、接地、モジュール設計などの複数の機能を備えており、バッテリーシステムの電気安全を確保するために不可欠です。
1-構造サポートにより電気接続の信頼性を確保
バッテリー トレイは、バッテリー モジュールを固定し、機械的ストレスを軽減し、振動と衝撃に耐え、位置合わせを維持し、環境保護と熱管理を統合することで、複雑な動作条件下での電気接続の信頼性と安全性を確保します。
図1 バッテリートレイ
A.物理的なサポートと固定により、電気接続ポイント(バスバー、配線ハーネス、コネクタなど)の正確な位置合わせが保証され、構造の変形や変位による接触不良を回避できます。バッテリーモジュールとコネクタを固定するための剛性フレームを提供し、振動や衝撃による緩みや破損を防止します。
B.環境隔離と保護:密閉設計(IP67/IP68など)により、水蒸気、ほこり、塩水噴霧などの侵入を防ぎ、腐食や絶縁不良による短絡を回避します。外部からの機械的衝撃や異物による衝撃を遮断し、高電圧接続コンポーネントを保護します。
C.熱管理の相乗効果:統合された放熱構造(液体冷却プレート、サーマルパッドなど)が温度のバランスを取り、局所的な過熱による接続ポイントの酸化や溶接を防止します。断熱設計により、隣接するモジュール間の熱干渉を減らし、温度勾配による材料の膨張差を回避します。
D.電磁両立性(EMC)サポート:金属シールド層または導電性コーティングにより電磁干渉を抑制し、低電圧信号線(BMS通信線など)を高電圧回路干渉から保護します。
2-絶縁保護により効率的な絶縁環境を構築
バッテリーの電気絶縁設計の焦点は、高電圧電気を効果的に絶縁し、システムの効率的な動作を確保できる環境を作成し、バッテリーモジュールがあらゆる動作条件下で安全にパッケージ化され、電気エネルギーの偶発的な放出を防ぎ、潜在的な電気的リスクを回避することです。
A.バッテリー トレイの構造は、耐荷重性と絶縁保護の両方を考慮しています:
l 軽量化を図りながら、高い剛性と耐衝撃性を維持するには、押し出しアルミニウム合金などのアルミニウム合金材料が好まれます。外枠は、バッテリーシステム全体の重量と外部からの衝撃を支えるために使用されます。閉断面プロファイルは、構造強度を高めるために使用されます。内枠は、バッテリーモジュールや水冷プレートなどを支えるように設計されており、それらの安定性と放熱要件を確保します。
l 絶縁材は、バッテリーモジュールとトレイ間の良好な電気的絶縁を確保するために、パッドまたはコーティングとして使用されます。高電圧配線ハーネスには、トレイとの電気的クリアランスと沿面距離を確保するために、専用の管理パスと絶縁シースが必要です。
l 攪拌摩擦溶接などの高度な溶接技術を使用して、接続強度を向上させながら、熱影響部を減らし、変形や潜在的な亀裂を回避します。溶接が不便な部品については、ボルト接続またはリベットを使用し、シーラントと組み合わせて、機械的接続と電気的絶縁の信頼性を確保します。
l 全体の構造の安定性に影響を与えずにバッテリーの交換とメンテナンスを容易にするために、設計時にモジュール性を考慮します。
図2 電気的クリアランスと沿面距離の概略図
B.高電圧および低電圧絶縁設計の重要なポイント:
l バッテリーシステムのプラスとマイナスのポイントは、低電圧電源システムとバッテリートレイから分離する必要があります。これにより、高電圧回路と低電圧制御回路の間に十分な電気的クリアランスと沿面距離が確保され、安全基準を満たし、低電圧システムへの高電圧漏洩を防止できます。
l 高低電圧分離設計では、電磁両立性 (EMC) を考慮して、分離対策によって干渉が生じず、システムが安定して動作し続けるようにする必要があります。
l 高インピーダンス接続では、高システムと低システムが高インピーダンスで接続され、車体アース (バッテリートレイ) のみが電流の流れを制限して、高電圧システムの障害が低電圧システムに広がるのを防ぎます。
l 物理的分離対策では、バッテリートレイを設計する際に、高電圧コンポーネントと低電圧コンポーネントを異なる密閉チャンバーに配置して、物理的な分離によって相互影響を減らすことができます。バッテリーモジュールとトレイの間には、ポリマープラスチックやゴムなどの絶縁材をパッドとして使用して、物理的および電気的分離を確保します。
l 設計時に隔離手段の保守性を考慮し、必要に応じて安全に修理または交換できるようにします。
C.接触保護設計の重要なポイント:
l 高電圧ハーネスの管理:高電圧ハーネスは、露出を避け、直接接触するリスクを減らすために、絶縁シースで適切に包まれ、固定クリップまたはワイヤトラフを介して整然と管理される必要があります。
l 安全パーティション:バッテリーモジュール間、およびバッテリーモジュールとトレイの壁の間に絶縁パーティションが設置され、バッテリーが損傷したときに電解液が漏れて間接的な感電のリスクを防ぎます。
l 高電圧コンポーネントのパッケージ:高電圧コネクタやリレーなどの主要コンポーネントは、トレイ内でもこれらのコンポーネントが誤って直接触れないようにパッケージ化されています。
l 密閉設計:バッテリートレイは、内部の高電圧コンポーネントが露出しないように金属または複合シェルを使用して全体的に密閉構造として設計されており、シェル自体も優れた絶縁特性を備えている必要があります。
l ロック機構:メンテナンス可能な高電圧接続ポイントには、非専門家による操作中に簡単に開かないようにロック機構が使用され、偶発的な接触のリスクが軽減されます。
l 絶縁材料の適用: 絶縁材料は、バッテリー トレイとバッテリー モジュールの間の絶縁層として使用され、トレイが損傷した場合でも、人体が通電部分に直接接触するのを防ぎます。これらの材料には、ポリマー プラスチック、ゴム ガスケット、コーティングなどが含まれますが、これらに限定されません。
3-電気ロゴデザイン
バッテリートレイの電気的識別により、操作の安全性が向上するだけでなく、メンテナンスプロセスが簡素化され、誤操作のリスクも軽減されます。
A.明確な識別
l バッテリー トレイと周囲の高電圧部品に「高電圧危険」や「触れないでください」などの警告サインをはっきりと表示して、緊急時でもすぐに識別できるようにします。
l 高電圧領域には赤やオレンジ、直流には青など、国際的に認められた色分けを使用して、さまざまな電気特性を直感的に区別します。
l 高電圧、接地、電源オフ ポイントなどを示すために、IEC 60417 のグラフィック シンボルなどの標準化された電気安全シンボルを適用して、情報の世界的な理解可能性を確保します。
l バッテリー トレイのシリアル番号、製造日、バッチ情報を含めて、追跡とリコール管理を容易にします。
l 耐摩耗性と耐腐食性のある素材と印刷技術を選択して、バッテリー トレイのライフサイクル全体にわたってラベルが明瞭で読みやすい状態を維持できるようにします。
B.警告サイン
l バッテリートレイと周囲のエリアには高電圧の危険が明確に表示されており、保守担当者が電気の安全性に注意し、操作手順に従うよう促しています。
l 特に高電圧コネクタの近くや露出している場所では、安全な操作距離を示して、適切な距離を保つよう注意を促します。
C.操作ガイド
l 接地対策が適切に実施されるように、バッテリー システムとトレイの接地位置を明確にマークします。
l 安全なテスト ポイントとメンテナンス アクセス ポイントを特定します。これらは、低電圧または無電源状態で動作するように設計する必要があります。
l トレイの重要でない領域に、正しい操作手順をガイドするための基本的な操作および安全に関する指示を簡単に記載できます。
ご参考になるために、定期に熱設計及び軽量化に関する技術と情報を更新させていただきます。当社にご関心をお持ちいただき、ありがとうございます。
最も人気のあるウォーターブロックは、基本的に純銅のマイクロチャネルタイプです。銅製の底板は直接スカイビング加工され、フィンは底板と一体化して熱抵抗を減らします。底板とカバープレートはろう付けまたは拡散接合されており、シールの信頼性を確保しています。
パート3:スカイビング加工によるウォーターブロックの主なコスト構造
1- スカイビングプロセスを使用してウォーターブロックを製造する利点
l 統合設計:スカイビングプロセスは、床とフィンを統合できるため、接触熱抵抗を減らし、熱伝導率を向上させるのに役立ちます。さらに、底板とフィンを統合した設計により、構造強度も向上します。
l 高精度加工:スカイビングプロセスでは非常に細かい歯構造を生成でき、歯の高さ、歯の厚さ、歯のピッチを正確に制御できるため、ヒートシンクフィンの密度が高くなり、放熱面積が大きくなり、放熱効率が向上します。同時に、形状、サイズなど、さまざまな顧客の個別のニーズにもよりよく対応できます。
l 生産効率が高く、スカイビングプロセスは大量生産できます。従来のCNCと比較して、スカイビングプロセスでは複数のギアピースを同時に処理できるため、生産効率が大幅に向上します。
図1: 異なる加工技術を用いたウォーターブロックベース a-スカイビング b-CNC c-冷間鍛造
2-スカイビングウォーターブロックのコスト構造
l 設計開発コスト: スカイビングウォーターブロックの設計の複雑さは比較的高く、特に高い放熱性能が求められる場合は、複雑なプロセス設計と最適化が必要になります。
l 材料コスト: スカイビングプロセスで使用される材料は主にアルミニウムと銅合金です。ラジエーター製造では、アルミニウム板と銅合金を組み合わせた設計がより一般的で、コストパフォーマンスが高いため、アルミニウムと銅の品質がコストに直接影響します。
l 加工コスト:
スカイビング工程コスト:スカイビング工程には、3軸CNC工作機械などの高精度CNC加工設備が必要です。このような設備の使用には高い投資コストが必要であり、オペレーターの技術要件も高く、生産コストが増加します。
溶接工程コスト:ウォーターブロックの製造工程では、溶接工程も重要なコスト要因です。真空ろう付けと拡散溶接は、一般的に使用される2つの溶接方法です。ろう付けは複数のジョイントを同時に溶接でき、生産効率が高く、ろう付け材料が必要で、プロセス条件に対する要件が高く、品質管理が困難です。拡散溶接設備は1回限りの投資が大きく、拡散溶接はフィラーを必要としませんが、ワークピースの表面処理に対する要件が高くなります。
表面処理コスト:一般的な表面処理方法には、陽極酸化、メッキなどがあります。アルミニウム合金ウォーターブロックの場合、陽極酸化により表面硬度、耐摩耗性、耐腐食性が向上し、製品の美観が向上します。銅製ウォーターブロックにはニッケルメッキなどのメッキが施され、銅の酸化や腐食を防ぎ、製品の寿命と信頼性を高めます。
l その他の費用: 検査およびテスト、梱包および輸送など。
3-コスト最適化の提案
l 材料使用の最適化
適切な材料を選択します:たとえば、銅は熱伝導率が高く、単位密度が高く、単価も高いです。アルミニウムは軽量で単価が低く、熱伝導率がやや悪いです。
材料使用: 材料の厚さとマージンを正確に計算することで、材料を効率的に使用し、材料の無駄を減らします。
図2: 材料消費量計算の概略図
l 生産プロセスの最適化
金型の簡素化: 金型の複雑さとコストを削減するために、シンプルな金型を設計します。
スクラップ率の削減: 正確なプロセス制御と品質検査によりスクラップ率を削減します。
ワンステップ成形: プロセスルートを最適化し、複数の処理ステップを削減し、生産効率を向上させます。
ご参考になるために、定期に熱設計及び軽量化に関する技術と情報を更新させていただきます。当社にご関心をお持ちいただき、ありがとうございます。
ウォーターブロックは液体冷却システムの重要なコンポーネントであるため、その設計では、熱交換性能、構造強度、耐腐食性、耐漏洩性、コスト管理など、さまざまな要素を考慮する必要があります。ウォーターブロックは通常、複雑な熱交換スロット構造(つまり、流路)で設計されており、その内部の流路設計の品質がシステム全体の熱交換効率を直接決定します。
パート2:ウォーターブロックの設計、加工技術、課題
1-さまざまなシナリオにおけるウォーターブロックの設計要件
l 高性能コンピューティング:
高性能コンピューティングデバイス(高性能CPU、GPUなど)は動作中に大量の熱を発生するため、ウォーターブロックには効率的な放熱機能が必要です。高熱流束密度の放熱要件を満たすために、ウォーターブロックは通常、高密度マイクロチャネル設計を採用して熱交換面積を増やし、放熱効率を向上させます。さらに、一部の設計ではウォーターブロックをCPUに直接統合し、シリコングリースを塗布する手順を排除することで、組み立てプロセスを簡素化するだけでなく、放熱性能をさらに向上させます。信頼性の面では、ウォーターブロックは漏れを防ぎ、長期にわたる安定した動作を確保するために、優れた密閉性能を備えている必要があります。
l グラフィックカードの冷却:
グラフィック カードは発熱量が多い部分なので、ウォーター ブロックはグラフィック カード上の発熱部品すべてを効果的に冷却できるよう、全面カバー設計にする必要があります。同時に、グラフィック カードの冷却には高流量の冷却剤が必要なので、ウォーター ブロックの内部構造は高流量に対応して熱を素早く除去する必要があります。
l データセンター:
データセンターでは、データセンターの安定した動作と効率的な放熱を確保するために、ウォーターブロックの構造設計は、効率的な放熱、低騒音、高信頼性、高電力密度への適応性、インテリジェントな管理、環境適応性など、複数の要件を満たす必要があります。
2-ウォーターブロック構造の進化の傾向
ウォーターブロックの構造設計の進化の傾向は、技術革新と性能向上の二重の追求を反映しており、主に以下の側面に反映されています。
l 放熱性能の向上:
接触面積を増やす:一部のウォーターブロック設計では、発熱体との接触面積を増やすことで放熱性能を向上させています。たとえば、大面積の銅ベース設計では、良好な接触と熱伝導を実現できます。
内部構造の最適化:内部の水路を最適化します。1つのアイデアは、通常のフィンからステアリングフィンに変更し、長いストリップフローチャネルを提示し、フロー境界層の分離を促進し、境界層の厚さを減らし、熱交換効率を向上させるなど、流体の流れを最適化することです。もう1つのアイデアは、従来の粗い水路からマイクロチャネル設計に変更するなど、熱容量領域を増やすことです。これにより、冷却剤とベースプレートの接触面積が大幅に増加し、放熱効率が向上します。一部の設計では、冷却剤をガイドプレートを介してマイクロチャネルベースプレートに噴霧して、局所的な流速と乱流を増加させ、熱吸収効率を大幅に向上させます。
l 統合されたインテリジェントなデザイン:
統合設計:統合設計では、ウォーターポンプ、ヒートシンクフィン、熱伝導ベースなどのコンポーネントを統合して、接続ポイントの数を減らし、システムの安定性と放熱効率を向上させます。
多機能統合:放熱性能に加えて、最新のウォーターブロックには温度表示と監視機能もあります。
モジュラー設計:モジュラーバックル構造により、整理の利便性と自由度が向上します。
図1: フィンの厚さが異なるウォーターブロックベース
l 高性能な素材と仕上げ:
純銅ベースなどの高性能材料の使用とニッケルメッキなどの表面処理技術の組み合わせにより、熱伝導性と耐腐食性が向上します。
3-加工技術と課題
l 材料特性は処理に影響します:
材料の硬度と靭性の問題: 銅、アルミニウム、およびそれらの合金などの異なる材料で作られたラジエーターは、硬度と靭性が異なり、加工ツールとプロセスに対する要件も異なります。硬度が高い材料は摩耗が早く、ツールの交換頻度も高くなります。靭性が高い材料は、切削中に変形やバリが発生しやすくなります。
銅アルミニウム複合材料の加工は複雑です。銅アルミニウム複合材料のシャベル歯ヒートシンクは、まず連続鋳造半溶融状態プレス技術を使用して複合材料にしてから、シャベル歯加工を行う必要があります。このプロセスはより複雑で、設備とプロセスに高い精度が求められます。
l 高い寸法精度要件
歯の高さと厚さの一貫性を確保するのが難しい:一部の高密度歯ヒートシンクでは、ヒートシンクの性能と均一性を確保するために、各歯の高さと厚さに高い一貫性が求められます。歯の高さと歯の厚さの差が大きすぎると、熱伝達が不均一になり、放熱効果に影響します。加工中は、高精度の設備と自動制御システムを使用して、各歯の仕様が一貫していることを確認する必要があります。
歯間隔の制御が難しい:ヒートシンクの歯が密集しすぎると、その密度と間隔によって加工プロセスが複雑になり、歯の均一性を維持するために加工設備の速度と精度を高める必要があります。たとえば、歯間隔が小さすぎると、切削中に工具が干渉しやすくなり、加工精度と表面品質に影響します。
l 厳しい表面品質要件
バリの問題: 加工中にバリが発生しやすく、ラジエーターの美観に影響を与えるだけでなく、空気の流れを妨げ、放熱効果を低下させる可能性があります。バリの発生は、材料の切断精度が低いこと、加工ツールの摩耗などによって引き起こされる可能性があり、バリの解決には対応するバリ取りプロセスを採用する必要があります。
表面粗さ: ラジエーターの表面粗さは、放熱性能とその後の表面処理効果に影響を与えます。表面粗さが大きすぎると、空気の流れに対する抵抗が増加し、放熱効率が低下します。粗さを減らすには追加の表面処理が必要であり、加工コストと時間が増加します。
l 高度な処理設備とプロセス要件
設備の精度と安定性:ギアショベルには高精度のギアショベルマシンが必要であり、設備の精度は歯の寸法精度と表面品質に直接影響します。同時に、長期加工中の寸法の一貫性を確保するために、設備は良好な安定性を備えている必要があります。
工具の選択と摩耗:適切な工具は加工品質にとって重要です。工具の材質、形状パラメータなどは、材料特性に応じて選択する必要があります。加工プロセス中に工具が摩耗すると、切削力が増加し、寸法精度が低下し、表面粗さが増加するため、工具を適時に調整または交換する必要があります。
送り速度と切削深さ:送り速度と切削深さの不合理な設定は、加工不良につながりやすくなります。送り速度が速すぎて切削深さが大きすぎると、工具に過負荷がかかり、工具のひっかかり、工具の跳ね返り、工具の落下などが発生し、加工精度と表面品質に影響します。
図2: スカイビングプロセス
l 高度なカスタマイズ要件
さまざまなアプリケーション シナリオでは、ラジエーターのサイズ、形状、歯の高さ、歯の厚さ、歯の間隔などのパラメーターに対する要件が異なり、特定のニーズに応じてカスタマイズする必要があります。これにより、加工メーカーは、多様なカスタマイズ ニーズを満たすために、柔軟なプロセス調整機能と豊富な経験を備えている必要があります。
ご参考になるために、定期に熱設計及び軽量化に関する技術と情報を更新させていただきます。当社にご関心をお持ちいただき、ありがとうございます。
世界の人工知能コンピューティング能力の急速な成長とチップの熱設計消費電力(TDP)の継続的な増加により、データセンターの冷却需要は前例のない課題に直面しています。同時に、世界中でますます厳しくなる省エネおよび炭素削減政策は、冷却技術の革新をさらに促進しました。このような状況において、従来の空冷ソリューションは、効率的な放熱と省エネという2つの要件を満たすことが徐々に困難になってきました。液体冷却技術は、その優れた放熱性能と大幅な省エネの利点により急速に台頭し、データセンター冷却ソリューションの主流の選択肢になりつつあります。データ処理とストレージの中核機器であるサーバーのパフォーマンスと安定性は、システム全体の動作効率に直接関係しています。マザーボード、CPU、メモリ、ハードディスク、グラフィックカードなどのサーバーのコアコンポーネントは、継続的な高負荷動作下で大量の熱を発生します。熱を適時に効果的に放散できない場合、サーバーのパフォーマンスと寿命に深刻な影響を及ぼします。このため、高度な液体冷却システムがサーバー冷却ソリューションに導入され、CPU やグラフィック カードなどの主要な熱源に直接取り付けられ、放熱効率が大幅に向上しました。
パート1:水冷ブロックの構造と動作原理
液体冷却システムのコアコンポーネントの 1 つはウォーターブロックです。ウォーターブロックは通常、熱伝導率の高い銅またはアルミニウム材料で作られ、精密な水路とヒートシンク構造で設計されています。これらのウォーターブロックは、CPU や GPU などの熱源の表面にぴったりフィットし、内部を循環する冷却水を通じて熱をすばやく吸収して伝達します。その後、熱はヒートシンクに運ばれ、水冷システムを通じて循環し、最終的に周囲の空気中に放散されます。
図1: 主流チップメーカーのチップ熱消費電力の傾向
1- 一般的なウォーターブロックの種類と特徴
l マイクロチャネルウォーターブロック
特徴:マイクロチャネルウォーターブロックは、精密なマイクロ水チャネル設計を採用しています。水チャネル構造は細かく複雑で、冷却剤と発熱部品との接触面積を大幅に増やすことができ、放熱効率が大幅に向上します。マイクロ水チャネル設計は、冷却剤の流れ中に強い乱流効果を生み出し、対流熱伝達係数をさらに高め、効率的な熱伝達を実現します。
適用シナリオ:特に、非常に高い放熱要件を持つ高性能コンピューティング、オーバークロック、データセンターなど、発熱量の多いCPUやGPUに適しています。
l 大流量ウォーターブロック
特徴: 大流量ウォーターブロックの内部構造は比較的シンプルで、通常は銅板またはエッチング溝設計を使用しており、製造コストが低くなっています。その主な利点は、高速水流を利用して熱を素早く除去し、大流量水冷システムでの使用に適していることです。構造はシンプルですが、効率的な放熱能力により、非常にコスト効率の高い選択肢となっています。
適用シナリオ: 中高級DIYコンピュータシステムや中小規模のサーバークラスターなど、放熱効率に一定の要件があるが予算が限られているシナリオに適しています。
l ジェット式水冷ヘッド
特徴:ジェット式水冷ブロックは、ガイドプレートを介して狭いノズルからマイクロチャネル底板に冷却剤を高速で噴射し、強力な乱流効果を形成して放熱効率を大幅に向上させます。この設計により、冷却剤とベースとの接触面積が増加するだけでなく、高速流によって熱交換性能がさらに最適化されます。
適用シナリオ:高性能CPUおよびGPUに適しており、特にオーバークロックコンピューティング、人工知能トレーニング、グラフィックスレンダリングなど、高放熱要件と高流量シナリオに適しています。
2-ウォーターブロックの一般的な構造
ウォーターブロックは、内部に水路を備えた金属ブロックで、通常は銅またはアルミニウムで作られています。CPU、グラフィックカード、その他の熱発生デバイスと接触することはありません。その構造設計は、放熱性能の品質を直接決定します。一般的なウォーターブロックは、通常、次の主要部品で構成されています。
l ベースは通常、銅やアルミニウム合金などの高熱伝導性材料で作られており、表面は発熱部品との密着性を確保するために細かく加工されており、ベースには複雑な流路設計が施されており、冷却剤とベースの接触面積が増加します。
l カバー プレートは、ベースと一緒になってフロー チャネル シーリング キャビティを形成し、ウォーター ブロック内のフロー チャネル、シール、およびその他のコンポーネントをほこり、不純物、外部の物理的損傷から保護します。
l 水の入口と出口は、冷却剤が水冷ヘッドに出入りするためのインターフェースです。これらは通常、冷却剤がスムーズに出入りできるように、水冷ヘッドの側面または上部に設計されています。位置設計では、流体の流路を考慮して、流動抵抗を減らし、冷却剤の流量を増やす必要があります。
l クリップは、水冷ヘッドを CPU やその他の発熱部品にしっかりと固定し、しっかりとした基礎を確保して効率的な熱伝導を実現するために使用されます。
図2: ウォーターブロックの典型的な構造
3- 放熱性能の総合的な最適化
l 流路設計の最適化
流路の接触面積を増やす:より狭く、より高密度の流路を設計することで、冷却剤とベースとの接触面積を大幅に増やすことができ、対流熱伝達係数を向上させることができます。たとえば、マイクロチャネル設計には微細な水路構造があります。マイクロチャネル水ブロックの設計パラメータ(チャネル幅、高さ、間隔など)は、その放熱効率に決定的な影響を及ぼします。チャネル幅が狭くなると、狭いチャネル内の冷却剤の流れの乱流効果が強化されるため、熱伝達係数が大幅に増加し、熱交換効率が向上します。チャネルの高さが高いほど、冷却剤の流路スペースが広がり、熱伝達性能が向上します。チャネル間隔が狭いほど、冷却剤と熱源との接触面積が増え、放熱効率が向上します。
また、流路レイアウトを最適化し、流路の曲がりを減らすことで最適化することもできます。合理的な流路レイアウトにより、冷却剤が発熱部品の表面を均一に覆い、局所的な温度差を減らすことができます。流路の曲がりにより、ヘッド損失と内部流動抵抗が増加し、冷却効率が低下します。設計では曲がりの数を最小限に抑える必要があります。避けられない場合は、圧力降下を減らして流動性能を最適化するために、曲がりを滑らかな遷移として設計する必要があります。
l 高熱伝導性材料: ウォーターブロックのベースは通常、純銅やアルミニウム合金などの高熱伝導性材料で作られています。これらの材料は、熱源から冷却剤に熱を効率的に伝達し、全体的な放熱性能を向上させます。
l ベース基板の厚さ、フィン、スポイラー構造などの構造パラメータの最適化。基板の厚さが増加すると最高温度が上昇するため、設計では放熱効果と構造強度の最適なバランスを見つける必要があります。フィンの高さ、厚さ、間隔を増やすことで放熱性能を向上させることができますが、同時に流動抵抗も増加します。放熱性能を最大限に高めるには、最適なフィン設計の組み合わせを見つけてください。スポイラー柱の形状は、乱流効果を効果的に高め、熱交換効率を向上させることができます。
ご参考になるために、定期に熱設計及び軽量化に関する技術と情報を更新させていただきます。当社にご関心をお持ちいただき、ありがとうございます。
本文从生产实际出发,总结了搅拌摩擦焊焊接过程中常见的问题、产生原因及改善方法,供大家参考。
この記事では、実際の生産に基づいて、攪拌摩擦接合プロセスにおける一般的な問題、原因、改善方法をまとめ、参考として提供します。
1-表面欠陥
(1)表面溝
l 問題の説明: 表面溝はプラウイング欠陥とも呼ばれ、通常は溶接部の上面に現れ、溶接部の前進端に向かう傾向があり、溝の形をしています。
l 原因: 溶接部の周囲の熱可塑性金属の流れが不十分で、溶接部のプラスチック金属が攪拌針の移動中に残る瞬間的な空洞を完全に満たすことができません。
l 改善方法:ショルダー径を大きくし、圧力を上げて、溶接速度を下げます。
図1: 溝
(2)エッジバリ
l 問題の説明: 溶接部の外側の端にフラッシュバリが発生し、形状が波状になっています。
l 原因:回転速度と溶接速度の不一致、下向きの圧力が大きすぎる。
l 改善方法:溶接パラメータを最適化し、圧力の量を減らします。
図2: エッジバリ
(3)表面剥離
l 問題の説明: 表面の剥離またはねじれが、皮膚またはねじ山の形で溶接の表面に現れます。
l 原因: 金属の摩擦によって発生した大量の熱が溶接部の表面金属に蓄積され、表面の局所的な金属が溶融状態になります。
l 改善方法:溶接パラメータを最適化し、回転速度を下げ、溶接速度を上げます。
図3: 表面剥離
(4)バックウェルドノジュール
l 問題の説明: 溶接の裏側に溶接ビードが形成されます。
l 原因: 溶接時の撹拌ヘッドの深さと圧力の不適切な制御。
l 改善方法:ミキシングヘッドの深さと圧力の設定を最適化します。
2-内部欠陥
(1)不完全な浸透
l 問題の説明: 溶接底部が接続されていないか、完全に接続されていない場合に、「亀裂のような」欠陥が発生します。
l 原因: 撹拌針の長さが足りないため、溶接部の底部の材料が十分に撹拌されません。
l 改善方法:溶接厚さの材料が十分に撹拌されるように、適切な撹拌針の長さを選択します。
図4: 不完全な貫通
(2)穴
l 問題の説明: 溶接底部が接続されていないか、完全に接続されていない場合に、「亀裂のような」欠陥が発生します。
l 原因: 溶接プロセス中に、摩擦熱入力が不十分なため、十分な材料が可塑化状態に達しず、材料の流れが不十分になり、溶接領域が完全に閉じられなくなります。
l 改善方法:溶接パラメータを最適化し、撹拌針の設計を改善し、溶接速度と回転速度を制御します。
図5: 穴
ご参考になるために、定期に熱設計及び軽量化に関する技術と情報を更新させていただきます。当社にご関心をお持ちいただき、ありがとうございます。
最近、編集者は多くの企業が液浸液冷却エネルギー貯蔵に注目し、計画していることに気付きました。しばらく沈黙していた液浸液冷却技術は再び注目を集め、再び人気が出ているようです。多くの同業者もこの発展に注目していると思います。
1- 液浸液冷却技術の特徴
エネルギー貯蔵セルは300Ah以上に向かっており、エネルギー貯蔵システムは5MWh以上に向かっています。セルが大きくなるほど発熱量が多くなり、放熱が難しくなり、温度の一貫性を確保することが難しくなります。また、エネルギー貯蔵システムは多数の積層セルで構成されており、動作条件が複雑で変化しやすいため、発熱の不均一や温度分布の不均一が発生しやすくなります。放熱と温度均一性の問題が適切に解決されないと、バッテリーの充放電性能、容量、寿命が低下し、システム全体の性能に影響を及ぼします。さらに、安全性は常にリチウム電池のエネルギー貯蔵にかかっている「ダモクレスの剣」であり、安全性を向上させる最も一般的な方法は、本質的安全性、能動的安全性、受動的安全性の3つの側面に向かうことです。
浸漬液冷却は、バッテリーセルを絶縁性、無毒、放熱性の液体に浸すことです。冷却剤は、より高い熱伝導率と比熱容量を持っています。この直接接触方式は、非常に高い熱伝達効率を提供すると同時に、温度均一性も向上させます。また、冷却剤は温度制御媒体であることに加えて、エネルギー貯蔵システムの消火液としても使用でき、温度制御と防火を兼ね備えており、これも浸漬液冷却技術の重要な特徴です。より高い放熱性能とより強力な安全性が求められる業界では、浸漬液冷却が間違いなくより多くの利点を持つことになります。
図1: 浸漬型液冷式エネルギー貯蔵バッテリーパックボックス
2- 浸漬液冷却エネルギー貯蔵システムソリューション
液冷技術の1分野として、浸漬液冷技術はエネルギー貯蔵業界で初めて使用されたわけではありません。最初は高性能コンピューティングの分野で使用され、その後、データセンター、人工知能、暗号通貨などに徐々に拡大しました。
浸漬液冷エネルギー貯蔵システムの設計の本来の意図は、従来の空冷と間接液冷の冷却効率とバッテリー温度差制御の欠点を解決することです。南方電力網梅州宝湖プロジェクトの正式な稼働は、最先端技術である浸漬液冷が新しいエネルギー貯蔵工学の分野でうまく応用されたことを示しています。
l 冷却方式と冷媒循環方式
冷却方式は単相と相変化に分かれています。単相浸漬液冷却が使用され、主に鉱油、シリコーン油、天然エステルなどが含まれます。他の方式では、主にハイドロフルオロエーテルに代表される二相浸漬液冷却が使用され、相変化潜熱を利用して放熱し、放熱効率を向上させます。不完全な統計によると、「単相浸漬液冷却」方式は、現在リリースされている浸漬液冷却エネルギー貯蔵システムの中で最も一般的です。
冷却剤の循環モードの違いにより、単相浸漬液冷却には、自然対流、ポンプ駆動、浸漬結合コールドプレート液冷却の3つの技術ルートがあります。自然対流は、加熱後の液体の体積膨張と密度低下の特性を利用して、高温の冷却剤の浮上と冷却後の沈降を実現し、循環放熱を完了します。ポンプ駆動システムの核心は、液体冷却ユニットが冷却剤を駆動して液体冷却パイプラインとバッテリー浸漬ボックスの間で循環させ、循環放熱プロセス全体を完了することです。浸漬結合プレート液体冷却方式では、バッテリーを誘電液に浸し、誘電液と接触する冷却プレートを使用して熱を取り除き、誘電液を冷却するための複雑な二次回路の使用を回避します。
l 製品形態と統合ソリューション
浸漬液冷式エネルギー貯蔵システムの統合ソリューションの反復は、全体から部分、そして細部へと進むプロセスです。各ステップは、前の段階に基づいて最適化および改善され、より高いパフォーマンスと安全性を実現します。
キャビンレベルからパックレベルまで、システム統合テクノロジーはシーンのカスタマイズの特徴を示しています。エネルギー貯蔵シナリオの多様化により、エネルギー貯蔵システムに対する需要が異なります。単一の製品では市場の需要を満たすことはできません。モジュール設計により、プロジェクトの規模と電力需要に応じてエネルギー貯蔵製品を最適化および拡張でき、さまざまなアプリケーションシナリオとニーズに応じてエネルギー貯蔵ソリューションを迅速に調整および展開できます。
3-工業化プロセスにおける課題と実装シナリオ
浸漬型液体冷却エネルギー貯蔵システムは、商業化プロセスにおいて、経済的実現可能性、技術的な複雑さ、市場での受け入れ、業界チェーンの成熟度など、多くの課題に直面します。
l 技術的な複雑さ: コールドプレート液体冷却システムと比較すると、浸漬液体冷却システムは設計と実装がより複雑です。
l 産業チェーンの成熟度: 液浸液体冷却技術の産業チェーンはまだ十分に成熟しておらず、より幅広い分野への応用が制限されています。産業チェーンの成熟度は、技術の推進と商業化に直接影響します。
l 経済的課題: エネルギー貯蔵業界はまだ商業開発の初期段階にあり、収益性の欠如により、高コストの技術ルートが市場に受け入れられることは困難です。多くの企業が一時的な注文に対して低価格で競争しているため、浸漬液冷却の浸透が制限されています。
現在、エネルギー貯蔵産業の主な市場は依然として空冷とコールドプレート液体冷却が主流であり、浸漬液体冷却はまだ市場に完全に受け入れられていません。浸漬液体冷却技術の市場浸透率と受け入れ度は高くありませんが、次のような特殊なシナリオでは大きな可能性を示さない可能性があります。
l 危険化学品業界: 危険化学品会社は、エネルギー貯蔵設備に対して極めて厳格な安全管理を実施しています。これは、製造・保管する化学物質のほとんどが、可燃性、爆発性、毒性、腐食性が非常に高いためです。事故が発生すると、会社自体に重大な損失をもたらすだけでなく、環境汚染や周辺地域への被害を引き起こす可能性もあります。
l 基地局とデータセンター: 基地局とデータセンターは、熱暴走に対する許容度が低いです。データセンターのエネルギー貯蔵システムは、システムの安全性を確保するために、安定した性能を持ち、熱暴走を起こしにくいバッテリーを備えている必要があります。電力品質に対する要件は高く、エネルギー貯蔵システムは迅速な応答能力を備えている必要があります。グリッド障害や停電などの緊急事態が発生した場合、エネルギー貯蔵システムは、電力の継続性と安定性を確保するために、直接放電モードに切り替えることができなければなりません。
l 急速充電ステーション: 高速充電と放電を行うと、バッテリーは短時間で大量の熱を発生します。これにより、バッテリーの温度が高くなりすぎて不均一になり、バッテリーの性能、寿命、安全性に脅威を与えます。つまり、高速充電と放電のシナリオでは、バッテリーの熱管理が特に重要になります。
ご参考になるために、定期に熱設計及び軽量化に関する技術と情報を更新させていただきます。当社にご関心をお持ちいただき、ありがとうございます。
バッテリーパックの気密性は、電気自動車やエネルギー貯蔵システムにおいて重要な指標です。バッテリーパックの気密性テストは、主にバッテリーパックのシェル、インターフェース、コネクタ、冷却アセンブリなどに対して行われ、バッテリーパックの内部が外部環境からのほこりや湿気などの不純物によって汚染または侵入されないこと、冷却アセンブリが漏れないことを確認します。これにより、バッテリーパックが正常な性能と寿命を維持し、短絡や爆発などの安全事故を引き起こさないことが保証されます。
1-バッテリーパックの保護レベルと気密性試験標準の策定
国際保護等級(IEC60529)、異物保護等級またはIPコードとも呼ばれます。IP(侵入保護)保護等級システムは、国際電気標準会議(IEC)によって制定された規格で、異物の侵入や水の侵入に対する電気機器ハウジングの保護等級を分類します。バッテリーパックケースの気密性は通常、IP67またはIP68に達する必要があります。つまり、バッテリーパックケースは、ほこりの侵入から完全に保護され(防塵レベル6)、一定時間、一定の圧力で水に浸しても有害なレベルまで水が浸入しない(防水レベル7)必要があります。より厳しい要件は、バッテリーパックを1mの深さの水に60分間浸しても水が浸入しないことです(防水レベル8)。IP保護等級は通常、2桁で構成されます。図1に示すように、数字が大きいほど保護レベルが高くなります。
図1: IP保護レベルの説明
バッテリーパックが IP67 および IP68 の要件を満たしていることを確認するには、バッテリーパックを水中に沈める必要があります。この方法は時間がかかり、パワーバッテリーパックを破壊し、一定の安全上のリスクがあります。パワーバッテリーのオフラインテストとしては適していません。そのため、業界では気密テストを使用してバッテリーパックが IP67 および IP68 の要件を満たしていることを確認するのが一般的な方法になっています。気密テスト規格の策定では、圧力降下値と漏水率の関係、および開口部と漏水の関係を考慮する必要があります。気密テスト規格の策定には、理論的な極限から実験検証までの一連の手順が含まれており、IP レベルから気密テスト規格への変換を実現します。たとえば、IP68 を例に挙げます:
図2: 気密試験基準策定の手順
2- 気密性試験方法の選択と試験の難しさの分析
バッテリーパックの設計と製造品質は、バッテリーボックスカバーの靭性と強度、バッテリーパックシェルの密閉、インターフェースとコネクタ、防爆ベント、電気コネクタ自体の密閉など、気密性に影響を与える重要な要素です。さらに、熱膨張と収縮の問題、材料の老化、振動と衝撃など、使用中に気密性に影響を与えるいくつかの問題があります。バッテリーパックシェルの生産と製造では、溶接点の不均一、溶接の弱さやひび割れ、エアギャップ、ジョイント接続の密閉不良など、溶接点や接合品質などの問題によって引き起こされる気密性の低下にさらに注意を払います。
バッテリーパックの気密性テストは、主に上部シェル、下部シェル、および組み立て部品の気密性テストに分かれています。上部シェルと下部シェルの気密性テストは、組み立て後の気密漏れ要件を満たす必要があります。バッテリーパックの気密性テスト方法を選択するときは、通常、バッテリーパックの特性、テスト精度要件、生産効率、およびコストが総合的に考慮されます。
エンジニアリングにおけるバッテリーパックのシェルテストは、一般的にプロセス気密性テストと出荷気密性テストに分けられます。さらに、上部シェルと下部シェルの気密性テストは、組み立て後の気密漏れ要件を満たす必要があり、テスト標準に対してより厳しい要件が提示されています。気密性が要件を満たしていることを保証するために、実際の操作で次の困難を克服する必要があります。
l 製品構造の安定性:プラグ溶接、蛇口溶接、梁溶接、フレーム底板溶接、フレーム前後カバープレート溶接などの溶接品質。溶接漏れの問題は、主にアーク開始点とアーク終了点に集中しており、溶け落ちによる欠陥、溶接変形応力による割れ、例えば底板キャビティ側壁溶接、底板キャビティ材料の層化、溶接変形応力に耐えられないことなどです。
l 気密固定具の適応性と安定性: 固定具の設計は、テスト対象のコンポーネントの形状と寸法に厳密に一致している必要があります。これにより、テスト プロセス中にコンポーネントを固定具にしっかりと固定でき、位置のずれや振動によるテスト エラーが削減されます。ただし、実際には、バッテリー パックのサイズと形状は大きく異なるため、複数の異なるテスト固定具の設計と製造が必要になり、コストと操作の複雑さが増します。汎用的な固定具を設計すると、設計プロセスがさらに複雑になります。
l 気密性テスト結果の再現性: 空気圧、温度、テストワークピース/固定具の乾燥度などの要因が気密性テスト結果に影響します。
l 貫通しない微細な亀裂が多数存在するワークピースの場合、検出装置の精度や検出パラメータなどの影響により、漏洩源を発見できず、検出漏れが発生する可能性があります。
図3: 気密性試験ツール
3-エンジニアリングで一般的に使用されるバッテリーパックの気密性検出ソリューションの組み合わせ
バッテリーパックのシェル工程の気密性試験には、一般的に気密性試験と浸水試験が含まれます。気密性試験では、バッテリーボックスの上部カバーを密閉し、コネクタポートのみを空気入口として残します。バッテリーパックの気密性は、空気圧を制御し、空気漏れがあるかどうかを観察することで判断します。浸水試験は、バッテリーボックス全体を完全に水に浸し、ボックス内に水があるかどうかを確認して気密性を判断するものです。
ヘリウム漏れ検出は、ヘリウムをトレーサーガスとして使用し、漏れ箇所のヘリウム濃度を検出することで漏れを検出する技術です。漏れがある可能性のあるテスト対象デバイスの内部または外部にヘリウムが侵入すると、漏れがある場合は、ヘリウムは漏れを通じてすぐにシステム内に侵入または流出し、質量分析計によって検出されます。ヘリウム漏れ検出方法は、特に小さな漏れを検出する場合に高い検出効率を備えています。
図4: 漏れ検出方法の比較
実際の生産では、通常、複数の検出方法を組み合わせて検出効率と精度を向上させます。たとえば、ヘリウム漏れ検出方法は高精度で小さな漏れの検出に適しており、差圧法は高精度で応答が速いという特徴があります。また、従来の水検出方法は検出精度が低いですが、直感的で低コストであり、漏れを見つけるのに便利な方法です。
ご参考になるために、定期に熱設計及び軽量化に関する技術と情報を更新させていただきます。当社にご関心をお持ちいただき、ありがとうございます。
エネルギー貯蔵液体冷却パックの液密性の潜在的な故障には、漏れ、腐食と堆積、結露水、その他の故障モードなど、複数の側面が関係します。
1- 流体の相互接続と構成
エネルギー貯蔵液体冷却システムでは、流体相互接続がさまざまなコンポーネント間で冷却剤を移動させる役割を果たします。効果的な流体相互接続により、冷却剤がシステム内で効率的に循環し、バッテリーの充電および放電プロセス中に発生する余分な熱が除去されます。
密閉性の高いシステムは、冷却剤の漏れを効果的に防ぐことができます。漏れがあると、冷却剤が失われ、頻繁に補充が必要になるだけでなく、システムの放熱性能と安定性にも影響します。エネルギー貯蔵では、冷却剤の漏れによりバッテリーの短絡が発生し、安全上の問題が発生する可能性があります。
2-流体相互接続システムの液密設計
流体相互接続システムの液密設計は、システムが密閉を維持し、さまざまな動作条件下で流体の漏れを防ぐための重要なリンクです。
図1: エネルギー貯蔵液体冷却システムの典型的な展開
(1)システム内の漏洩の可能性のある源とリスクポイントを分析する。
l 液体冷却アセンブリの自己シール特性。たとえば、液体冷却チャネル システムとパック ボックスの統合設計では、コンポーネントは溶接によって接続されます。溶接品質の欠陥、溶接不良、気孔、亀裂などはすべて、液体の浸透の問題につながる可能性があります。
l 構造設計が不合理です。例えば、液体冷却ボックスの位置決め穴やネジ穴が流路に近すぎるため、溶接不良の部分が液体の浸出経路になりやすくなります。
l 接続部品: 液体冷却システムのパイプ接続、バルブ、ジョイントは、漏れが発生しやすい箇所です。接続構造が適切に設計されていなかったり、製造プロセスが洗練されていない場合、ジョイント内部に小さな欠陥が生じ、そこから冷却剤が漏れることもあります。
l 不適切な取り付け、材料の老朽化や損傷などにより生じた漏れ。
(2)シール構造設計:
l 液冷式パックは、乾湿分離型冷却板冷却方式を採用しています。通常の作業条件下では、バッテリーセルは冷却剤と接触しないため、バッテリーセルの正常な動作を確保できます。エネルギー貯蔵液体冷却器の1つの解決策は、押し出し加工で形成し、冷却板に直接流路を統合し、機械加工で冷却循環経路を開くことです。このプロセスでは、適切な溶接プロセスを選択することが、密閉を確保するための重要なステップです。詳細については、「エネルギー貯蔵用下部ボックスの溶接プロセスの設計」を参照してください。
l 液体冷却パイプラインは、主に液体冷却源と機器の間、機器間、機器とパイプラインの間の移行的なソフト(ハード)パイプ接続に使用されます。主な接続方法は次のとおりです。
クイック接続: エネルギー貯蔵液体冷却システムの接続方法の 1 つは、VDA または CQC クイック接続を使用することです。
ねじ接続:接続構造の両端はパイプでスライド接続され、内部のねじリングとねじスリーブ間のねじ接続により、接続の堅牢性が向上します。
制限管とナットの接続:パイプの一端に接続管を締め付け、接続管の両側に制限管を固定して取り付けます。制限管の内側にはゴムワッシャーと凸リングが固定されており、接続管の頭の表面には制限リング溝が開けられています。ナットは制限管の上部に回転可能に接続され、ねじを介して制限管に回転可能に接続されています。
シールリング接続:シールリングは強力な接着剤でねじスリーブの内壁に接着され、シールリングの内壁はパイプの外面に可動に接続され、使用中の漏れを防止します。
(3)PACK液冷プレート、キャビンインターフェース、キャビンパイプライン等は、共通の冷却剤、共通の温度、流量条件下での長期腐食防止設計となっており、腐食のない長期運転を保証します。運転条件による液密性への影響:
l 温度。高温の影響:温度が上昇すると、液体の粘度は一般的に低下し、液体のシール性能が低下し、液密性に影響を及ぼします。たとえば、特定のシール材は高温で変形または劣化し、漏れを引き起こす可能性があります。低温の影響:低温環境では、液体が粘性になり、流れにくくなる可能性がありますが、シール材の性能が向上し、液密性がある程度向上する可能性もあります。
l 圧力。高圧環境:高圧下では、液体の密度と粘度が増加し、液体の密封性能が向上する可能性があります。ただし、過度の圧力はシール材を損傷し、漏れを引き起こす可能性もあります。低圧環境:低圧下では、液体の密封性能が比較的弱くなる可能性があり、特にシール材自体に欠陥があったり、老朽化している場合は、漏れが発生する可能性が高くなります。
l 流量。高流量: 液体が高速で流れると、シール面に大きな衝撃力が生じ、シール材の摩耗や変形を引き起こし、液密性に影響を及ぼします。低流量: 低流量では、液体のシール性能は比較的良好ですが、軽微な材料欠陥などの潜在的なシールの問題が隠れてしまうこともあります。
3-腐食と堆積の問題
l ブロックによる機密性への影響:
冷却剤、堆積物、またはボイラーの成長により、内部の詰まり、冷却剤の流れの悪化、冷却効率の低下が発生する可能性があります。
汚れとスケール: 長期間の使用後、冷却剤内のミネラルがパイプの内壁に堆積することがあります。これを「スケール」と呼びます。汚れは、固体粒子の沈殿、結晶化、腐食、微生物の活動によっても形成されることがあります。これらの汚れはパイプやコールドプレートを詰まらせ、流れの抵抗を増やし、熱伝達効率を低下させます。
泡の問題:液体冷却システムで泡が発生することがあります。泡は冷却プレートの表面に付着し、熱伝達効果が低下し、システム動作時の抵抗が増加し、ポンプなどにキャビテーション腐食を引き起こし、機器を損傷する可能性があります。
l 渦電流が気密性に与える影響:
流体がパイプや隙間を流れるとき、速度の変化によって渦が形成されることがあります。特に、流体が狭い部分や障害物を通過するときに、渦が形成されやすくなります。流体の粘度と密度も渦の発生に影響します。粘度の高い流体は渦を形成しやすく、密度の高い流体は渦の形成を弱める可能性があります。
漏れ経路: 渦電流は接触面に渦を形成し、隙間や不規則な表面に小さな漏れ経路を形成し、ガスや液体の漏れを引き起こす可能性があります。
表面の摩耗: 渦流は、特に高速流の状態で接触面の摩耗を引き起こす可能性があります。摩耗した表面では新たな漏れ経路が形成される可能性が高くなるため、この摩耗により気密性がさらに低下する可能性があります。
熱の影響: 渦電流により熱が発生し、接触面の材料が変形したり熱膨張したりして、特に温度変化が大きいシステムでは気密性に影響を及ぼします。
4-結露水の問題
特定の条件下では、液体冷却ラインに結露が発生し、機器が損傷したり、効率が低下したりする可能性があります。 断熱不良:パイプの断熱材が損傷したり老朽化したりすると、熱が失われ、冷却効果に影響します。特に低温環境では、断熱不良によりパイプ表面に霜や氷が形成される可能性があります。 凍結割れ:寒冷環境では、適切な凍結防止対策を講じないと、パイプ内の冷却剤が凍結してパイプが破裂する可能性があります。
ソリューション
l 密閉対策: 外部の湿った空気がバッテリー コンパートメント内に入らないように、液体冷却パイプラインの入口と出口が完全に遮断されていることを確認します。
l 除湿装置:除湿エアコンを設置するか、除湿機能を使用してバッテリー室内の湿度を適切な範囲に維持します。
l 温度制御: 空調または換気システムを設置することで、エネルギー貯蔵キャビネットが設置されている環境の温度と湿度を制御できます。たとえば、温度を 20 ~ 25 ℃ に保ち、相対湿度を 40% ~ 60% に制御できます。
l 隔離対策: 空のバッテリー ラックを単純に隔離して、バッテリー クラスターを含むコンパートメントに湿気が入るのを防ぎます。
ご参考になるために、定期に熱設計及び軽量化に関する技術と情報を更新させていただきます。当社にご関心をお持ちいただき、ありがとうございます。
流体シミュレーション
ラジエーターと冷板の放熱性能をシミュレーションソフトで解析します。
応用シーン
工況:高熱流密度の状況
典型な応用:顧客定制
取り付け:片側面組立
特性:放熱効果が高い
応用シーン
プロセス:アルミ型材接合溶接
取り付け:底部液冷
典型な応用:顧客定制
特性:軽量で冷却効果が高い
クーラントはポンプ駆動で配管を通って循環します。冷却材がサーバー内部の熱交換器を流れると、高温コンポーネント(CPU、GPUなど)と熱交換を行い、熱を奪います。
Lori is a heat sink manufacturer of design and manufacturing high power heat sink, we have provided innovative thermal solutions for many high power industry device such as Aerospace industry,Medical, Communication server, Consumer Electronics etc. Our solutions include high power heat pipe thermal mould, liquid cooling system, staked fin heat sink solution etc.
Lori is a heat sink manufacturer of design and manufacturing high power heat sink, we have provided innovative thermal solutions for many high power industry device such as Aerospace industry,Medical, Communication server, Consumer Electronics etc. Our solutions include high power heat pipe thermal mould, liquid cooling system, staked fin heat sink solution etc.
Lori is a heat sink manufacturer of design and manufacturing high power heat sink, we have provided innovative thermal solutions for many high power industry device such as Aerospace industry,Medical, Communication server, Consumer Electronics etc. Our solutions include high power heat pipe thermal mould, liquid cooling system, staked fin heat sink solution etc.
液冷方案の基本的な原理:液冷とは、液体を冷却剤とし、液体の流れを利用してデータセンターのIT設備の内部部材で発生した熱を設備の外に伝え、IT機器の発熱部を冷却して安全に運用する技術です。
液冷の利点:液冷は高いエネルギー効率、高い熱密度を備え、熱を効率よく放熱し、標高、地域、気温などの環境に影響されません。
Walmateの液冷板式の液冷ソリューション
冷板な液冷は、液冷板(通常は銅やアルミなどの熱伝導性のある金属で構成された密閉空洞)を通じて発熱デバイスの熱を循環管に閉じ込められた冷却液に間接的に伝え、冷却液によって熱を持ち去る放熱形態です。冷板な液冷案の中で技術的成熟度が最も高く、大電力消費設備の配置、エネルギー効率の向上、冷房運行費用の低減、TCO (Total Cost of Ownership)の効果的な応用案です。