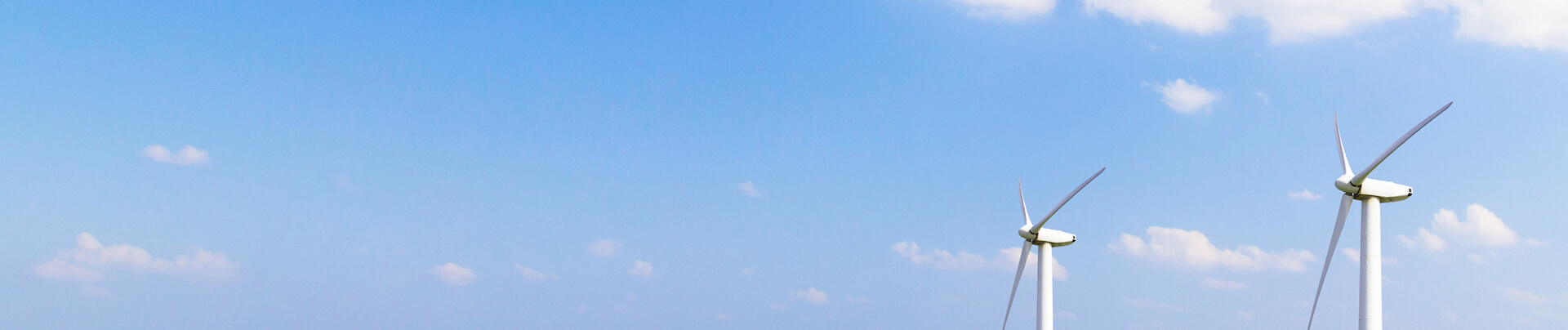
分かち合うことで成長します
手を携えて共に行い共に発展する
1-撹拌摩擦溶接(FSW)の基本的な原理です。
高速回転ミキサーヘッドをワークに挿入後、溶接方向に移働します。ミックスヘッドとワークの接触部は摩擦により熱を発生し、攪拌針の働きによって周囲の金属の塑性を柔らかくし、攪拌針の後ろの空洞を埋める金属層を柔らかくします。
現在,撹拌摩擦溶接は主にアルミ,銅,マグネシウム,チタニウムなどの媒体や異材料の接続に使われています。
2-攪拌摩擦溶接(FSW)プロセス
溶接始める時:溶接部分の溶接エリアに高速回転するピボットと針状突起のあるミキサーを入れます。ピボットは塑性状態での材料のオーバーフローを防ぐために同時に使用できます。
溶接作業中:撹拌ヘッドと溶接材料の間の摩擦抵抗は摩擦熱を発生し、材料を柔らかくして塑性変形を引き起こし、塑性変形エネルギーを放出します。撹拌ヘッドが溶接する界面に沿って前方に移働する時、熱可塑性材料は撹拌ヘッドの前部から後部に転移して、撹拌ヘッドの軸肩の鍛造作用の下で、ワーク間の固相接続を実現します。
溶接完了する時:撹拌ヘッドが回転して部品を出します。
撹拌摩擦溶接
3-技術の特徴です
変形小さい:材料は溶解する必要はありません、低入力熱、変形最小;
適応性が強い:環境の温湿度の影響を受けないで、適応性が強いです;
優れた性能です:溶接エリアは緻密な「鍛造構造」を形成し、気泡や収縮欠陥がありません;
環境と安全です:溶接プロセスはアーク、煙、飛散物などを発生しません、安全、グリーン、環境にやさしいです。
攪拌摩擦溶接継手の強度試験です
一般的な溶接方式と比較して、攪拌摩擦溶接には以下の優れた利点があります:
固体の溶接技術に属して、溶接の過程の中で溶接材料は溶けません;
溶接位置の制限、継手溶接の様々な形を実現することができます;
溶接効率が高くて、0.4-100mmの厚さ範囲内で片道溶接成形を実現できます;
溶接部位の残存応力が低く、変形が小さく、高精度な溶接を実現できます;
ジョイントの強度が高くて、疲労の性能が良くて、沖撃の靱性が良いです;
溶接コストが低くて、溶接プロセスの消耗がなくて、溶接線の充填と保護ガスが必要ありません;
溶接操作が簡単で、自働化溶接を実現しやすいです。
4-攪拌摩擦溶接技術の電池トレイ製造への応用です
アルミ合金は、低密度、高強度、熱安定性、耐腐食性と熱伝導性、無磁性、簡単な成形、リサイクル価値などの利点を持っており、電池パック軽量化設計の理想的な材料です。
現在、アルミ合金製の電池トレイやプラスチック製のカバーは、軽量化効果が高く、多くの自働車メーカーに採用されています。電池トレイはアルミニウム押出型+摩擦攪拌溶接+MIG溶接の方式を採用して、総合的な応用コストが低くて、性能要求を満たして、水冷電池循環の水通路を一体化することができます。
典型的な電池トレイは主にアルミ合金形材フレームとアルミ合金形材基板で構成され、それらは6シリーズ押出形材を使用して一緒に溶接されています。以下の図に示します。
アルミ合金の電池トレイ
断面の構造と材料:
フレームと基板はアルミニウム合金押出型材で作られ、材料は通常6061-T6(屈伏強度240 MPa、引張強度260 MPa)、6005A-T6(屈伏強度215 MPa、引張性能255 MPa)と6063-T6(屈伏性能170 MPa、引張耐性215 MPa)です。断面の復雑さ、コスト、金型の消耗などによって、どの特定のブランドを選ぶかを考えます。
技術的な難易度です:
フレームと基板は電池モジュールの担体であり、強度が要求されます。したがって、強度を確保するために空洞を有する二層断面が一般的に選択されます。基板の厚さは10mm前後,壁の厚さは2mmが一般的です。単層のアルミ板はあまり使われません。
フレームの典型的な断面は復数の空洞で構成され、6061-T6材料で作られ、最も薄い壁の厚さは2mmです。
基板の典型的な断面は、主に電池モジュールを取り付けるための上部突起を含む複数の空洞で構成されています。断面寸法が大きく、厚さは2mm、材料の一般的な選択600a -T6です。
型材の断面
解決策です:
基板と基板、および基板とフレームは、主に攪拌摩擦溶接によって接続されます。溶接強度は基材の約80%までできます。
基板型材は攪拌摩擦溶接継手を採用し、基板間は両面ドッキング継手を採用して溶接します。両面溶接の強度が高く変形が小さいです。
フレームと基板の間に両面攪拌摩擦溶接継手を形成します。撹拌ヘッドに十分なスペースを確保するために、フレームと基板の連結部の延長長は十分に長くして、フレームと撹拌ヘッドの間の干渉を避け、フレームの型材のサイズの増加と押し出し難度を避けるべきです。しかし、両面溶接は強度が高く変形が少ないのが長所です。
熱設計と軽量化に関する技術と情報を定期的に更新し、ご参考までにご共有します。Walmateをフォローしていただきありがとうございます。