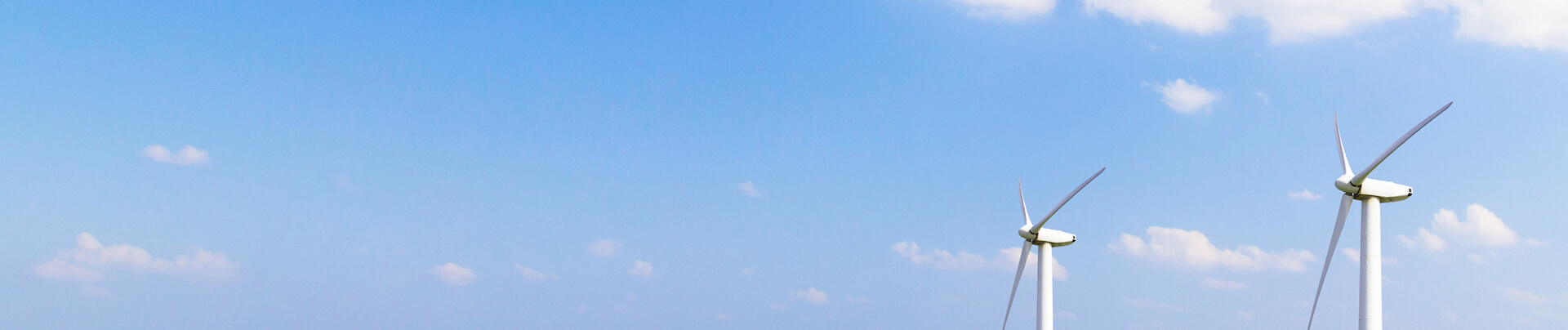
分かち合うことで成長します
手を携えて共に行い共に発展する
電子機器の電力密度が高まり続ける中、放熱設計はシステムの信頼性と寿命を左右する重要な要素となっています。19年にわたる熱管理の経験を持つ専門メーカーとして、当社は典型的なエンジニアリング事例とマルチフィジックスのフィールドシミュレーションの経験を組み合わせ、高電力シナリオにおいてエンジニアが見落としがちな5つの主要な技術的誤解を深く分析し、業界の慣行に準拠したソリューションを提供します。
誤解1:高熱伝導率材料の乱用、インターフェース熱抵抗の計算誤差
典型的な問題:熱伝導性材料の理論値を追求しすぎ、インターフェース接触熱抵抗の工学的現実を無視している。
事例分析:ある車載レーザーレーダー放熱モジュールでは、純銅基板(熱伝導率401W/m·K)を使用していましたが、熱伝導性材料(TIM)のコーティング厚さが正確に制御されておらず(設計値0.1mm、実測値±0.05mm)、測定された接触熱抵抗が0.6°C·cm²/Wに達し、FPGAジャンクション温度が規格値を22%超過しました。そこで、成形サーマルパッド(許容差±0.02mm、熱抵抗<0.03°C·cm²/W)に切り替え、真空焼結プロセスと組み合わせることで、ジャンクション温度は17°C低下し、MTBF(平均故障間隔)は10万時間に向上しました。最適化計画:
材料選定:ASTM D5470規格に基づき、TIMの熱抵抗を測定し、相変化材料または金属充填エラストマーを推奨します。
工程管理:自動塗布装置(精度±3%)を使用し、厚さ公差を10%未満に抑え、エアギャップを回避します。
誤解2:空冷システムにおける気流構成の不一致、局所的なホットスポットの制御不能
典型的な問題:ファンの数を盲目的に積み重ね、流路インピーダンス整合と境界層剥離効果を無視している。
エンジニアリング例:あるデータセンターのGPUクラスターでは、4基の12038ファン(風量200CFM)を使用していましたが、エアガイド角度(90°直角曲げ)の設計が不適切だったため、実際の有効風量は公称値の65%に過ぎず、局所的な温度差は40℃に達しました。CFDシミュレーションによる最適化の後、エアガイドを徐々に拡大する流路(拡散角度<7°)に変更し、フィン間隔の勾配を2mmから3.5mmに増加させるスタッガードフィンレイアウトを採用することで、全体の風圧抵抗を30%削減し、ホットスポットの温度差を8℃以内に抑えることができました。
コア戦略:
流れ場設計:ISO 5801規格に準拠した風洞試験を実施し、入口と出口の面積比を最適化します(推奨:1:1.2)。
動的制御:PWMファンのQ-H曲線に基づき、システムインピーダンス点を最高効率範囲(通常、最大風量の60~80%)に合わせます。
誤解3:環境保護設計の不備が材料の劣化を加速させる
典型的な問題:初期の放熱性能のみを重視し、湿度、熱、粉塵、塩水噴霧などの長期的な環境ストレスの影響を無視している。
事例分析:洋上風力発電コンバータは、6061アルミニウム合金ヒートシンク(表面陽極酸化処理)を使用していました。塩水噴霧環境で6ヶ月間稼働させた後、酸化層が剥離し、接触熱抵抗が50%増加し、IGBTの故障率が急上昇しました。5052アルミニウム合金(耐塩水噴霧性1000時間以上)に切り替え、ポリウレタン耐水性塗料(厚さ50μm、IEC 60068-2-11規格に準拠)を塗布したところ、3年間のフィールド故障率は75%減少しました。
設計ポイント:
コーティング技術:高温環境下でも使用できるよう、プラズマ溶射Al2O3セラミックコーティング(熱伝導率30W/m·K、耐熱温度800℃以上)を採用しています。
シーリング構造:IP69K保護等級(ダブルパスシリコンシール+圧力リリーフバルブ)により、粉塵や水蒸気の侵入を防止します。
誤解4:過渡熱負荷モデリングの欠如と相変化材料の不適切な選択
典型的な問題:定常状態シミュレーションで設計された放熱ソリューションは、ミリ秒レベルの電力パルスに対応できません。
実測データ:5G基地局において、ソリッドステートパワーアンプに2ms@2000Wのパルス負荷が印加されました。従来のアルミニウム基板ソリューションでは過渡温度上昇が55℃に達しましたが、マイクロカプセル型相変化材料(パラフィン/グラフェン複合材、相変化潜熱220J/g)と過渡熱シミュレーション(ANSYS Icepak 過渡ステップ長1ms)を組み合わせることで、温度上昇を18℃に抑え、MIL-STD-810G衝撃試験要件を満たしました。
動的管理技術:
相変化パッケージング:ハニカム構造で相変化材料(多孔度>70%)をカプセル化することで、液漏れを防ぎ、熱拡散効率を向上させました。
モデルキャリブレーション:シミュレーション境界条件は赤外線熱画像(サンプリングレート100Hz)に基づいて補正され、誤差は±1.5°C未満です。
誤解5:TCO評価は一方的で、隠れた運用・保守コストが考慮されていない
典型的な問題:ハードウェアの初期コストのみが比較され、エネルギー消費量、保守コスト、ダウンタイムによる損失が定量化されていない。
コスト比較:ある半導体工場では、当初空冷キャビネット(初期コスト50万元)を使用しており、年間電気代は120万元(PUE=1.8)でした。二相液浸液冷却(初期コスト180万元)にアップグレードした後、年間電気代は45万元(PUE=1.05)にまで低下しました。クリーンルームの空調負荷の削減により、年間の総合的な節約額は90万元に達し、増分投資は2.1年で回収可能(IRR>25%)です。
意思決定モデル:
改良モデリング:モンテカルロシミュレーションを導入し、機器故障率(ワイブル分布)がTCOに与える影響を定量化する。
政策の重ね合わせ:炭素税メカニズム(EU CBAMなど)と組み合わせることで、液体冷却システムのライフサイクル全体にわたる炭素排出量は60%削減され、さらに15%の追加補助金が得られる。
結論:熱設計パラダイムを経験主導からデータ主導へアップグレード
標準化プロセス:概念設計段階でJESD51-14熱試験規格を導入し、後々の手戻りを回避(ある光モジュールのプロジェクトサイクルが30%短縮)。
学際的連携:COMSOL Multiphysicsの電磁損失(HFSS抽出)と熱ひずみ場の連成により、レーダーTRコンポーネントの放熱効率が40%向上。
インテリジェントな運用・保守:ファイバーグレーティング温度センサー(精度±0.1℃)とデジタルツインプラットフォームを導入し、障害予測を実現(スーパーコンピューティングセンターの予期せぬダウンタイムを90%削減)。
厳格なエンジニアリング思考とフルリンクデータ検証により、熱設計エンジニアは「見えないキラー」を正確に回避し、高信頼性システムの基盤を築くことができます。当社は業界の実務家として、材料からシステムまでのクローズドループソリューションを提供することに尽力しており、お客様と共同で熱管理の課題に取り組んでいます。
ご参考になるために、定期に熱設計及び軽量化に関する技術と情報を更新させていただきます。当社にご関心をお持ちいただき、ありがとうございます。