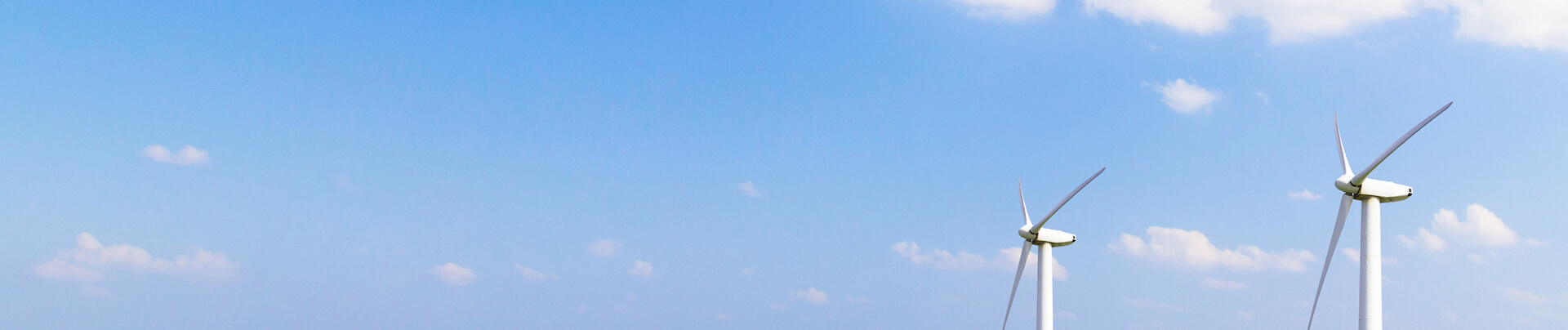
Communication and sharing promote growth
Joining Hands for Development!
Il pacco batteria è la fonte energetica principale dei nuovi veicoli energetici, che fornisce potenza motrice all'intero veicolo. In genere valutiamo i vantaggi e gli svantaggi della tecnologia del pacco batteria in base alle dimensioni di efficienza (densità energetica), sicurezza, costi di produzione e manutenzione.
Nella progettazione delle batterie, la tensione di una singola cella è di soli 3-4 V circa, mentre la tensione richiesta dai veicoli elettrici è di almeno 100 V. Le nuove auto ora hanno persino una tensione di 700 V/800 V e la potenza in uscita è generalmente di 200 W, quindi la batteria deve essere potenziata. Per soddisfare i requisiti di corrente e tensione dei veicoli elettrici, è necessario collegare celle diverse in serie o in parallelo.
Il pacco batteria è composto da celle, sistemi elettronici ed elettrici, sistemi di gestione termica, ecc., che sono racchiusi da una struttura del telaio della batteria: piastra di base (vassoio), telaio (telaio metallico), piastra di copertura superiore, bulloni, ecc. Come "confezionare" questi componenti e sistemi in un tutto in modo più efficiente e sicuro è sempre stato un argomento di continua ricerca ed esplorazione per l'intero settore.
Articolo precedente: Innovazione e sviluppo della tecnologia di integrazione delle batterie
L'origine della tecnologia dei gruppi di batterie di potenza può essere fatta risalire agli anni '50, e ha avuto origine nell'ex Unione Sovietica e in alcuni paesi europei. Questa tecnologia è stata originariamente utilizzata come concetto di ingegneria e produzione per determinare le somiglianze fisiche delle parti (percorsi di processo universali) e stabilire la loro produzione efficiente.
Il fulcro della Group Technology (GT) è identificare ed esplorare le somiglianze di cose correlate nelle attività di produzione, classificare problemi simili in gruppi e cercare soluzioni ottimali relativamente unificate per risolvere questo gruppo di problemi per ottenere benefici economici. Nel campo delle batterie di potenza, la group technology riguarda principalmente la tecnologia di integrazione delle batterie da singole celle in pacchi batteria (Pack), tra cui struttura, gestione termica, progettazione della connessione elettrica e tecnologia del sistema di gestione della batteria (BMS).
La prima tecnologia di raggruppamento nel campo automobilistico è MTP (Module To Pack), il che significa che le celle vengono prima integrate nei moduli e poi i moduli vengono integrati nei Pack. Questa tecnologia è caratterizzata da moduli staccabili e sostituibili, che hanno una buona manutenibilità, ma l'efficienza di raggruppamento è bassa. Con lo sviluppo della tecnologia, la tecnologia di raggruppamento ha subito una trasformazione da MTP a CTP (Cell To Pack). La tecnologia CTP si riferisce alla tecnologia di integrazione diretta delle celle nei Pack, eliminando la tradizionale struttura del modulo e migliorando l'efficienza di raggruppamento e l'efficienza di produzione. Negli ultimi anni, il settore sta anche esplorando tecnologie di raggruppamento come CTC (Cell To Chassis), CTB (Cell To Body & Bracket) e MTB (Module To Body) con maggiore efficienza di integrazione.
Nel campo delle batterie di potenza e dell'accumulo di energia elettrochimica, i principali progressi tecnologici delle batterie al litio derivano dall'innovazione strutturale e dall'innovazione dei materiali. Il primo consiste nell'ottimizzare la struttura di "cella-modulo-pacco batteria" a livello fisico per raggiungere l'obiettivo di migliorare sia la densità di energia del volume del pacco batteria sia la riduzione dei costi; il secondo consiste nell'esplorare i materiali delle batterie a livello chimico per raggiungere l'obiettivo di migliorare sia le prestazioni delle singole celle sia la riduzione dei costi. Questo articolo si concentra sull'impatto delle diverse tecnologie di integrazione strutturale sulla tecnologia di produzione del pacco batteria e sulla direzione dello sviluppo innovativo dal punto di vista dell'integrazione strutturale del pacco batteria. Le attuali tecnologie chiave per l'integrazione delle batterie di potenza sono illustrate nella figura seguente:
1-MTP è stato eliminato
All'inizio dell'attuale ondata di sviluppo di veicoli elettrici, sono stati lanciati molti modelli di veicoli a nuova energia da petrolio a elettrico. Essi continuano la disposizione spaziale e il design stilistico dei tradizionali veicoli a benzina. Gli ingegneri hanno assemblato un modulo di celle di batteria relativamente grande collegando un certo numero di singole celle di batteria in serie/parallelo, e poi hanno posizionato diversi di tali moduli di celle di batteria nel pacco batteria, che è il familiare pacco batteria "MTP". Poiché il pacco batteria deve essere "confezionato" più di due volte, il numero di componenti richiesti è estremamente elevato e il pacco batteria appare come "tre strati all'interno e tre strati all'esterno", con troppe parti ridondanti che occupano più volume e peso del sistema, con conseguente scarsa densità di energia volumetrica e densità di energia gravimetrica del pacco batteria "MTP". Inoltre, poiché la progettazione dei veicoli a benzina non ha specificamente riservato spazio per la batteria, il sistema di batterie può essere solo "schiacciato dove si adatta", con conseguente scarsa competitività del prodotto ed esperienza utente.
Dal lancio delle nuove piattaforme di veicoli elettrici intelligenti rappresentate da Tesla, i veicoli elettrici puri nativi hanno consentito di installare pacchi batteria in posizioni spaziali ideali in modo più efficiente e regolare, i sistemi tri-elettrici possono essere disposti in modo più ragionevole e l'architettura elettronica ed elettrica del veicolo e la progettazione della gestione termica possono essere integrate in modo più efficiente. La forza del prodotto del veicolo in termini di efficienza energetica, resistenza e intelligenza è stata notevolmente migliorata.
2-Era della tecnologia integrata 2.0——CTP
Il pacco batteria con struttura MTP presenta un problema significativo di utilizzo dello spazio. L'utilizzo dello spazio della cella della batteria rispetto al modulo è dell'80%, l'utilizzo dello spazio del modulo rispetto al pacco batteria è del 50% e l'utilizzo complessivo dello spazio è solo del 40%. Il costo dell'hardware del modulo rappresenta circa il 14% del costo totale della batteria. Questa struttura a basso utilizzo dello spazio non può soddisfare i requisiti di sviluppo dei nuovi veicoli energetici. Nell'ambito dell'idea di integrazione cella della batteria → modulo → pacco batteria → carrozzeria, se il veicolo desidera caricare quanta più potenza possibile nello spazio limitato del telaio e migliorare l'utilizzo del volume, è necessario considerare la standardizzazione di ogni fase di integrazione. Poiché la domanda di mercato per l'autonomia di guida continua ad aumentare, il volume di un singolo modulo batteria continua ad aumentare, il che porta indirettamente all'emergere della soluzione CTP.
La tecnologia della struttura CTP è nata per tenere in considerazione la sicurezza, la complessità del packaging, la riduzione dei costi, ecc. Con la premessa di garantire la sicurezza della cella della batteria, la tecnologia CTP riduce i cavi interni e le parti strutturali. Rispetto alla tecnologia MTP, la tecnologia CTP non ha una struttura modulare e confeziona direttamente la cella della batteria in un pacco batteria prima di installarlo sul veicolo.
Attualmente ci sono due idee principali. Una è quella di considerare il Pack come un grande modulo completo che sostituisce la struttura di più piccoli moduli al suo interno, rappresentata da CATL; l'altra è quella di considerare l'utilizzo di una soluzione senza modulo durante la progettazione e progettare la batteria stessa come partecipante alla forza, come la batteria blade di BYD.
Il punto centrale della tecnologia CTP è l'eliminazione del design del modulo, con le celle della batteria che si combinano direttamente con il guscio, riducendo l'uso delle piastre terminali e dei separatori. I problemi che ne derivano riguardano il fissaggio del pacco batteria e la gestione termica.
In effetti, il prodotto originale del pacco batteria CTP non era un progetto completamente privo di moduli, ma un progetto che univa i piccoli moduli originali in tre moduli grandi e due moduli medi, e c'erano anche piastre terminali in alluminio ad entrambe le estremità, quindi in teoria è ancora MTP, ma ci sono davvero grandi miglioramenti nella struttura.
Dopo l'introduzione di CTP 3.0, CATL ha presentato un metodo di produzione più avanzato, ottenendo un design completamente privo di moduli. Le celle della batteria sono state modificate da un orientamento verticale lungo l'altezza a una posizione orizzontale. Inoltre, è stata implementata una nuova soluzione di raffreddamento tra le celle della batteria, che non solo dissipa il calore ma fornisce anche funzioni di supporto, ammortizzazione, isolamento e controllo della temperatura. Anche il guscio inferiore è stato progettato con una funzione di fissaggio limitante.
Figura 1: Confronto tra la batteria CATL Kirin CTP2.0 e CTP3.0
3-Tecnologia integrata 3.0 Era—CTB, CTC
l Tecnologia CTB
La tecnologia CTP è un importante passo avanti nell'innovazione della struttura della batteria, ma non ha fatto una svolta nel pacco batteria stesso. Nella tecnologia CTP, il pacco batteria è ancora un componente indipendente. Rispetto alla strategia semplificata di CTP per i pacchi batteria, la tecnologia CTB combina il pannello del pavimento della carrozzeria e il coperchio del pacco batteria in uno. La superficie di tenuta piatta formata dal coperchio della batteria, dalla soglia della portiera e dalle travi anteriore e posteriore sigilla l'abitacolo passeggeri con sigillante e il fondo è assemblato con la carrozzeria attraverso il punto di installazione. Quando si progetta e si produce il pacco batteria, il sistema della batteria è integrato con la carrozzeria nel suo insieme, i requisiti di tenuta e impermeabilità della batteria stessa possono essere soddisfatti e la sigillatura della batteria e dell'abitacolo passeggeri è relativamente semplice e i rischi sono controllabili.
In questo modo, la struttura a sandwich originale di "coperchio pacco batteria-cella batteria-vassoio" si trasforma in una struttura a sandwich di "coperchio pacco batteria integrato sottoscocca-cella batteria-vassoio", riducendo la perdita di spazio causata dalla connessione tra carrozzeria e coperchio batteria. In questa modalità strutturale, il pacco batteria non è solo una fonte di energia, ma partecipa anche alla forza e alla trasmissione dell'intero veicolo come struttura.
Figura 2: Schema della struttura della tecnologia CTB
l Tecnologia CTC
Dopo aver adottato il metodo CTC, il pacco batteria non è più un assemblaggio indipendente, ma è integrato nella carrozzeria del veicolo, il che ottimizza la progettazione del prodotto e il processo di produzione, riduce il numero di parti del veicolo, in particolare riduce le parti strutturali interne e i connettori della batteria, ha il vantaggio intrinseco della leggerezza, massimizza l'utilizzo dello spazio e fornisce spazio per aumentare il numero di batterie e migliorare l'autonomia di guida. A condizione che il sistema elettrochimico stesso rimanga invariato, l'autonomia di guida può essere aumentata aumentando il numero di batterie.
Figura 3: Diagramma della struttura della tecnologia Tesla CTC
Ad esempio, Tesla e altre case automobilistiche hanno lanciato in successione modelli di tecnologia CTC. A livello di cella, possono utilizzare strutture sandwich elastiche multifunzionali e tecnologia di raffreddamento ad acqua di grandi dimensioni e sovrapporre la tecnologia di riutilizzo dello spazio anti-collisione nella parte inferiore del pacco batteria apportata dallo sviluppo integrato, tenendo conto dell'efficienza di raggruppamento, della dissipazione del calore e della sicurezza e promuovendo l'applicazione della tecnologia CTC dalle due dimensioni di ottimizzazione delle celle e protezione della struttura del veicolo. A livello di sviluppo integrato del veicolo, la cella della batteria è direttamente integrata nel telaio, eliminando i collegamenti di moduli e pacchi batteria. L'integrazione dei tre principali sistemi elettrici (motore, controllo elettronico, batteria), i tre sistemi elettrici minori (CC/CC, OBC, PDU), il sistema del telaio (sistema di trasmissione, sistema di guida, sistema di sterzo, sistema di frenata) e moduli correlati alla guida autonoma è realizzata e la distribuzione di potenza è ottimizzata e il consumo di energia è ridotto tramite il controller di dominio di potenza intelligente.
4-Modifiche ai requisiti specifici per i box batteria per le tecnologie CTP, CTB e CTC
Nella struttura tradizionale del pacco batteria, il modulo batteria svolge il ruolo di supporto, fissaggio e protezione della cella della batteria, mentre il corpo del box batteria sopporta principalmente la forza di estrusione esterna. L'applicazione delle tecnologie CTP, CTB e CTC propone nuovi requisiti per i box batteria, che si riflettono specificamente in:
I requisiti di resistenza del corpo della scatola della batteria sono migliorati: poiché il collegamento del modulo è ridotto o eliminato nelle strutture CTP, CTB e CTC, il corpo della scatola della batteria non deve solo resistere alla forza di estrusione esterna, ma anche alla forza di espansione della cella della batteria originariamente sopportata dal modulo. Pertanto, i requisiti di resistenza del corpo della scatola della batteria sono più elevati.
Capacità di protezione dalle collisioni: dopo aver utilizzato la tecnologia CTP per rimuovere le travi laterali del pacco batteria, la batteria subirà direttamente l'impatto della collisione, pertanto il pacco batteria CTP deve avere una resistenza alle collisioni sufficiente.
Requisiti di isolamento, isolamento e dissipazione del calore: le strutture CTP o CTB e CTC modificano il profilo della piastra inferiore in una piastra raffreddata ad acqua basata sulla scatola strutturale portante del telaio. La scatola della batteria non solo sopporta il peso delle celle della batteria, ma fornisce anche gestione termica e altre funzioni per la batteria. La struttura è più compatta, il processo di produzione è ottimizzato e il grado di automazione è più elevato.
Manutenibilità ridotta: il design altamente integrato rende complicata la sostituzione del pacco batteria. Ad esempio, nella struttura CTC, le celle della batteria sono riempite con materiale in resina, il che rende difficile la sostituzione delle celle della batteria e quasi impossibile la riparazione.
5- Impatto dell'integrazione del pacco batteria sull'infrastruttura di ricarica dei veicoli elettrici
La scelta di diverse tecnologie di integrazione del pacco batteria implica anche la scelta di diversi metodi di compensazione. CTP tende a essere la sostituzione della batteria, mentre CTB/CTC, più altamente integrato, tende a essere la ricarica rapida.
Un'elevata integrazione significa che più batterie possono essere ospitate nello stesso spazio, aumentando così l'autonomia dei veicoli elettrici. Gli utenti potrebbero non aver più bisogno di caricare frequentemente per brevi distanze, ma potrebbero preferire caricare rapidamente durante i lunghi viaggi. Pertanto, la pianificazione dell'infrastruttura di ricarica deve tenere conto di questi cambiamenti per garantire che possa soddisfare le esigenze degli utenti.
Con l'aumento dell'integrazione dei pacchi batteria, le dimensioni fisiche e la struttura dei pacchi batteria potrebbero cambiare, il che potrebbe influire sulla progettazione dell'interfaccia di ricarica e sulla compatibilità dell'apparecchiatura di ricarica.
Inoltre, la maggiore integrazione dei pacchi batteria potrebbe anche influire sulla velocità e l'efficienza della ricarica. Potrebbe essere necessario sviluppare e implementare sistemi di gestione della batteria e tecnologie di ricarica più efficienti per garantire un processo di ricarica rapido e sicuro.
Condivideremo regolarmente aggiornamenti e informazioni su tecniche di progettazione termica e alleggerimento, per la vostra consultazione. Grazie per l'interesse verso Walmate.