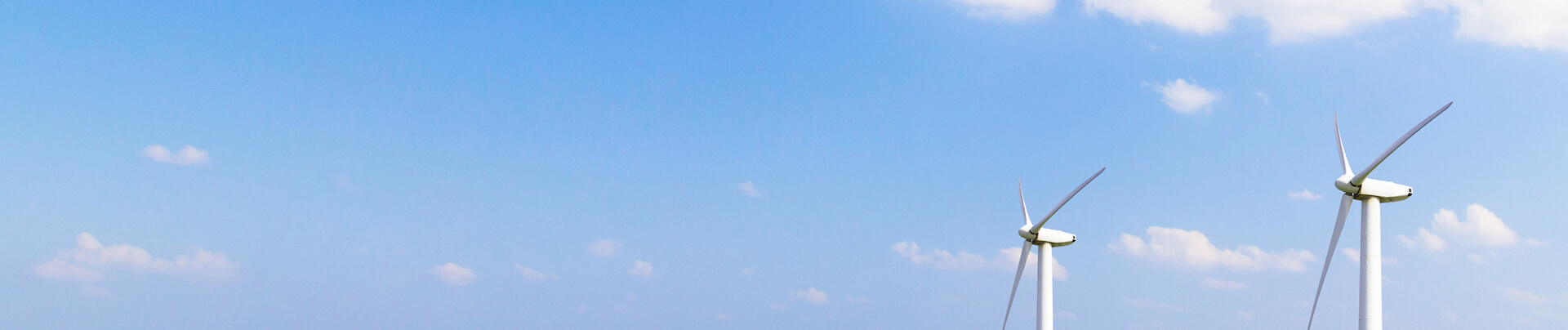
Communication and sharing promote growth
Joining Hands for Development!
Il ruolo del dissipatore è quello di ottenere una maggiore superficie di trasferimento del calore all'interno di uno spazio volumetrico limitato. Ciò si ottiene migliorando la forma della struttura per aumentare l'efficienza di trasferimento del calore dalla sua superficie al fluido circostante. Inoltre, l'area effettiva di trasferimento del calore può essere aumentata con trattamenti superficiali, con l'obiettivo finale di migliorare la dissipazione del calore e controllare la temperatura.
Nei contesti in cui i requisiti di densità di potenza volumetrica e di flusso termico non sono elevati, il dissipatore a pinne dritte rettangolari è particolarmente apprezzato dagli ingegneri per la sua struttura semplice, il costo di produzione ragionevole e le buone prestazioni di dissipazione del calore.
Confronto dei diversi metodi di trasferimento del calore
1-Progettazione delle alette del dissipatore
Il dissipatore è una superficie di espansione del calore che si concentra principalmente su parametri quali l'altezza, la forma e la distanza delle alette, nonché lo spessore del substrato.
Sezione delle alette del dissipatore
Dalla figura sopra, possiamo calcolare l'area di espansione del dissipatore:
Area di una singola aletta:Af = 2L(h+t/2),
Area dello spazio tra le alette:Ab= Lh,
Area totale di dissipazione:At=nAf +(n±1)Ab(dove n è il numero delle alette).
Dimensioni del dissipatore a pinne piatte
La funzione principale delle alette è quella di aumentare l'efficienza del trasferimento di calore aumentando la superficie. La distanza, lo spessore e l'altezza delle alette del dissipatore sono fattori determinanti per stabilire la quantità, la distribuzione e l'area di espansione del dissipatore. Come mostrato nella figura, quando h↑ o t↓, le alette diventano più alte, più sottili e più dense, permettendoci di ottenere una maggiore superficie di espansione del calore.
Quando aumenta la superficie delle alette, aumenta anche la superficie di contatto con l'aria, facilitando così la dissipazione del calore. Gli ingegneri possono inoltre ottimizzare la forma delle alette, ad esempio con profili ondulati o a denti di sega, per aumentare ulteriormente l'area di espansione del dissipatore.
Sebbene un'area superficiale più ampia migliori l'efficacia della dissipazione del calore, non si può presumere che alette più grandi siano sempre migliori. Sia che si tratti di raffreddamento naturale che forzato, la distanza tra le alette del dissipatore è un fattore cruciale per determinare il coefficiente di scambio termico dell'aria che scorre sulla loro superficie.
L'impatto della distanza e dell'altezza delle alette sull'efficienza della dissipazione del calore
In caso di raffreddamento naturale, il cambiamento di temperatura della superficie del dissipatore provoca la convezione naturale, che porta a uno strato d'aria (strato limite) sulle superfici delle alette. Una distanza troppo piccola tra le alette ostacola un flusso convettivo regolare. Nel caso di raffreddamento forzato, lo spessore dello strato limite delle alette viene compresso, permettendo una distanza più stretta. Tuttavia, il limite è dettato da vincoli di produzione e potenza dei componenti, rendendo cruciale un equilibrio tra spessore e altezza delle alette.
2-Progettazione della base del dissipatore
Lo spessore della base è un fattore fondamentale per l'efficienza del dissipatore. Una base del dissipatore troppo sottile aumenta la resistenza termica verso le alette lontane dalla fonte di calore, causando una distribuzione di temperatura irregolare e riducendo la resistenza agli shock termici.
Aumentare lo spessore della base può risolvere i problemi di distribuzione irregolare della temperatura e migliorare la resistenza agli shock termici. Tuttavia, uno spessore eccessivo può portare ad accumulo di calore, riducendo la capacità di conduzione termica.
Schizzo diagrammatico del principio di funzionamento del dissipatore
Come mostrato nella figura sopra:
Quando l'area della sorgente di calore è inferiore a quella della piastra di base, il calore deve diffondersi dal centro verso i bordi, formando una resistenza termica di diffusione. Anche la posizione della sorgente di calore influisce sulla resistenza termica di diffusione. Se la sorgente di calore è vicina al bordo del dissipatore, il calore si propaga più facilmente attraverso i bordi, riducendo così la resistenza termica di diffusione.
Nota: La resistenza termica di diffusione si riferisce all'ostacolo che il calore incontra quando si diffonde dal centro della sorgente di calore verso i bordi nel design del dissipatore. Questo fenomeno si verifica generalmente quando vi è una significativa differenza di area tra la sorgente di calore e la piastra di base, costringendo il calore a diffondersi da un'area più piccola a una più grande.
3-Tecniche di connessione tra alette e piastra di base
Le tecniche di connessione tra le alette del dissipatore e la piastra di base comprendono diversi metodi per garantire una buona conduttività termica e stabilità meccanica. Si suddividono principalmente in due categorie: formazione integrata e non integrata.
I dissipatori a formazione integrata presentano alette e piastra di base in un unico blocco, senza resistenza termica da contatto. Le principali tecniche sono:
l Fusione in pressione dell'alluminio: consente di fondere lingotti di alluminio e di riempire stampi metallici con essi utilizzando alta pressione, formando alette di dissipatori direttamente in pressocolata, permettendo la realizzazione di strutture complesse.
l Estrusione dell'alluminio: consiste nel riscaldare l'alluminio, inserirlo in un cilindro di estrusione e applicare una certa pressione, facendolo uscire attraverso uno stampo per ottenere la forma e dimensione desiderate, seguito da taglio e lavorazione finale.
l La forgiatura a freddo permette di ottenere alette sottili e dense con un'elevata conducibilità termica, anche se il costo è relativamente elevato. La capacità di modellazione è migliore rispetto all'estrusione dell'alluminio.
l I dissipatori a lame possono essere in rame, con un'elevata conducibilità termica e alette molto sottili. Le alette vengono sollevate dalla piastra con utensili da taglio, ma in caso di altezza e lunghezza notevoli possono subire deformazioni dovute allo stress.
Nella formazione non integrata, le alette e la piastra di base del dissipatore sono realizzate separatamente, e successivamente unite mediante tecniche quali saldatura, rivettatura o incollaggio. Le principali tecniche sono:
l Tipo saldatura: le alette e la piastra di base vengono unite con saldatura, utilizzando sia saldatura a caldo che a bassa temperatura.
La saldatura offre ottime prestazioni termiche; per saldare la piastra in alluminio e le alette utilizzando pasta di stagno, è necessario applicare un rivestimento di nichel, che comporta costi elevati e non è ideale per dissipatori di grandi dimensioni. La brasatura non richiede il nichel, ma i costi di saldatura rimangono comunque elevati.
l Tipo rivettatura: le alette vengono inserite nelle scanalature della piastra e poi fissate saldamente attraverso la compressione delle scanalature verso il centro, creando un'unione solida e stabile.
I vantaggi della rivettatura sono le buone prestazioni termiche, ma con l'uso prolungato, il prodotto può allentarsi o sviluppare spazi vuoti. È possibile migliorare l'affidabilità aumentando la qualità della rivettatura, ma ciò comporta costi aggiuntivi, quindi i dissipatori con alette rivettate vengono utilizzati in applicazioni che richiedono una minore affidabilità.
l Tipo adesivo: generalmente si utilizza una resina epossidica conduttiva per unire saldamente le alette e la piastra, consentendo il trasferimento del calore.
L'adesivo utilizza una resina epossidica termoconduttiva, con un coefficiente di conduzione termica inferiore rispetto alla saldatura. È comunque adatto per dissipatori con alette alte, rapporti elevati e piccoli spazi tra le alette. Può essere utilizzato in contesti dove non sono richieste prestazioni termiche elevate.
Condivideremo regolarmente aggiornamenti e informazioni su tecniche di progettazione termica e alleggerimento, per la vostra consultazione. Grazie per l'interesse verso Walmate.