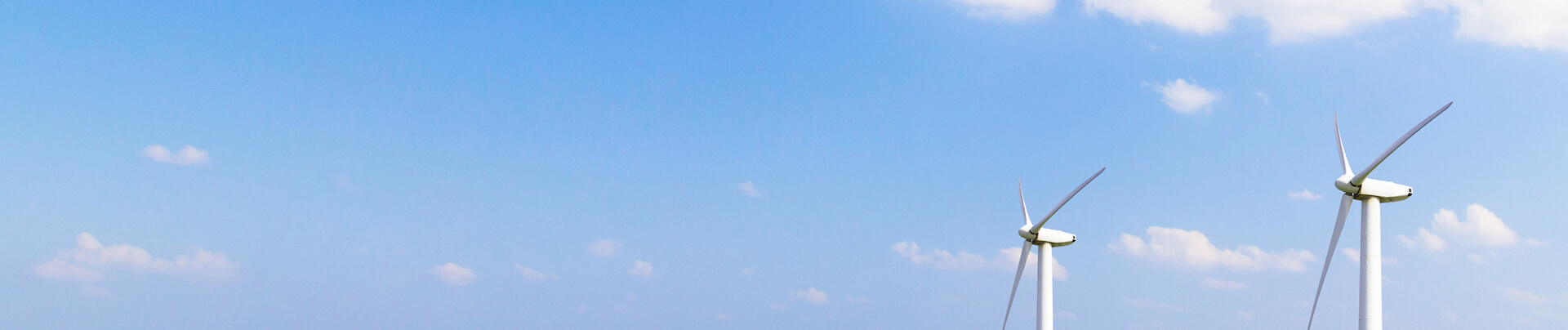
El intercambio y la participación promueven el crecimiento
y trabajan juntos para el desarrollo común
Para hacer frente a las demandas del mercado, como grandes extensiones, iteraciones rápidas y líneas de productos ricas, al mismo tiempo que se garantiza la reducción de costos, la mejora de la eficiencia y el control de calidad, para la industria automotriz, la estandarización de productos (plataformatización de vehículos) es, sin duda, una buena estrategia. A través de la plataformatización de baterías, se puede combinar la misma solución de paquete de baterías para diferentes modelos, o se pueden combinar soluciones de paquetes de baterías compuestas por el mismo tipo de celdas de batería y estructuras similares. Esto significa que se pueden estandarizar tantas piezas como sea posible, lo que puede acortar el ciclo de desarrollo, ahorrar costos, agilizar las líneas de producción y mejorar la eficiencia de la producción.
Primero:Plataformatización de baterías
La solución de la plataforma de baterías favorece la planificación general de los productos, la reducción de costes y la optimización de la capacidad de producción. De acuerdo con la estrategia de la plataforma de baterías de la plataforma del vehículo, es necesario considerar la intersección y el ancho de banda de los requisitos de cada modelo de la plataforma, y utilizar la menor cantidad posible de baterías y soluciones de baterías para que sean compatibles con la mayor cantidad posible de modelos. En el desarrollo de la arquitectura de los proyectos eléctricos puros, es crucial organizar razonablemente el paquete de baterías de energía integrado. Los elementos de trabajo específicos incluyen los requisitos de potencia y rendimiento de potencia, seguridad contra colisiones, ubicación y espacio de diseño, etc.
1- Límites de tamaño espacial y estandarización de celdas de batería
l Ubicaciones de paquetes de baterías disponibles
En la actualidad, la disposición de la batería de alimentación principal se encuentra debajo del piso, incluso debajo de los asientos delanteros, debajo de los asientos traseros, en el canal central y en el reposapiés. Esta disposición puede maximizar el área disponible, ayudar a bajar el centro de gravedad del vehículo, mejorar la estabilidad de manejo del vehículo y optimizar la trayectoria de transmisión de la fuerza de colisión.
Figura 1: Disposición del paquete de baterías durante el desarrollo de vehículos eléctricos
l Evolución de la distribución del espacio de los paquetes de baterías
Paquete de batería dividido: se adopta un diseño de espacio de paquete de batería dividido, como en la serie JAC Tongyue. El módulo de energía consta de dos paquetes de baterías, uno ubicado en la posición del tanque de combustible original y el otro ubicado en el maletero donde se almacena la llanta de repuesto.
Además, los ingenieros están explorando continuamente el espacio utilizable dentro de la arquitectura original de los vehículos de combustible, lo que da como resultado diseños de paquetes de baterías que aparecen en formas de "工" , "T" y "土"
Este tipo de diseño es una modificación menor de un vehículo de combustible tradicional. El espacio es muy limitado, y el volumen y el peso del paquete de baterías que se puede cargar son muy limitados, por lo que la capacidad es difícil de aumentar y la autonomía de crucero no es alta.
Paquete de baterías integrado: se trata de un nuevo concepto de diseño de producto. El diseño de todo el vehículo gira en torno al componente principal: el paquete de baterías. El paquete de baterías tiene un diseño modular y se coloca de forma plana sobre el chasis del vehículo para maximizar el espacio disponible.
l Disposición de los puntos de instalación del paquete de baterías
La disposición razonable del paquete de baterías es crucial, y los factores limitantes en el diseño son la distancia al suelo, la transitabilidad, la seguridad en caso de colisión, los requisitos de energía y muchos otros aspectos.
Figura 2: Restricciones de diseño del tamaño del paquete de baterías
La plataforma del vehículo debe definir la categoría, el nivel y la posición de cada modelo de vehículo dentro de la plataforma, y luego determinar el tamaño y la distancia entre ejes del vehículo. El diseño del vehículo descompone la envolvente de tamaño del paquete de baterías en las direcciones X, Y y Z de acuerdo con el espacio del vehículo. La batería debe estar dispuesta dentro de la envolvente dada del vehículo para garantizar que no haya interferencias entre los diversos sistemas del vehículo. El índice de peso en vacío puede descomponer los requisitos de calidad del sistema del paquete de baterías.
En términos de tamaño de la batería, el diseño de los paquetes de baterías de potencia no puede evitar indicadores de referencia rígidos como el espacio del vehículo y el peso en vacío, lo que significa que existe un umbral para el diseño de las celdas de la batería. Limitado por este umbral, el tamaño de la celda de la batería se concentrará en un rango determinado, como: la longitud de las celdas de batería cuadradas varía de 150 a 220 mm, el ancho varía de 20 a 80 mm y la altura varía alrededor de 100 mm. La tendencia cambiante de las especificaciones del tamaño de las celdas de la batería es el resultado de la relación complementaria entre la plataforma del vehículo y la estandarización de la batería.
Sin embargo, las estrategias de plataformas de baterías, los modelos de vehículos y la comprensión de la estandarización de los distintos fabricantes de automóviles son diferentes, lo que da como resultado diferencias significativas en las soluciones de productos actuales. Por ejemplo, la estrategia de estandarización de BYD es reemplazar por completo la batería de cuchillas, cuyo tamaño está fijado en 960*13,5 (14)*90 (102) mm, y el voltaje de celda única es 3,2/3,3 V.
2- Desarrollo de límites de resistencia y soluciones de capacidad de batería
La batería de potencia proporciona energía para que el vehículo se desplace: la capacidad de la batería, la profundidad de descarga y la densidad de energía afectan la cantidad de energía disponible. Para satisfacer las necesidades de los diferentes modelos, la diferencia en el consumo de energía de los modelos se ha convertido en una preocupación importante. La autonomía de crucero del vehículo se verá afectada por factores como la propulsión eléctrica, la batería, el peso en vacío, la resistencia al viento, la resistencia mecánica, el consumo de energía de bajo voltaje y la recuperación de energía. La posibilidad de compartir soluciones de batería entre modelos con grandes diferencias en el consumo de energía es débil, por lo que es necesario desarrollar soluciones de energía de batería personalizadas, que incluyan el tamaño de la batería, la calidad, la potencia y la optimización del rendimiento de la energía para cumplir con los requisitos del rendimiento de crucero.
En el marco de las limitaciones de la autonomía eléctrica pura de la plataforma de fabricación de vehículos, la descarga neta requerida por la batería se verá afectada por el consumo de energía de los diferentes modelos. Es necesario confirmar la distribución del consumo de energía de cada modelo en la plataforma para convertir aún más el ancho de banda del consumo de energía en la distribución de la demanda de la batería y, a continuación, determinar el plan de energía de la batería requerido por la plataforma.
3-Límite de rendimiento de 3 potencias
La potencia del vehículo completo incluye el rendimiento de potencia en diferentes estados de carga (SOC) y temperaturas ambientales, como aceleración, velocidad constante y modo de ahorro de energía. Esto se traduce en las características de potencia-voltaje de la batería en diferentes SOC y temperaturas, donde la potencia de la batería corresponde a los requisitos de potencia del sistema de propulsión del vehículo y el voltaje corresponde a los requisitos de voltaje nominal del motor de tracción.
Generalmente, la evaluación de soluciones de batería para toda la plataforma del vehículo comienza desde el tiempo de aceleración de 100 kilómetros a temperatura normal y alta potencia y su descomposición del indicador de batería, y se extiende gradualmente hasta la descomposición del indicador de batería en todo el rango y bajo todas las condiciones de operación.
SEGUNDO: Desarrollo de la caja de batería
1- Integración y modularización de baterías
Optimizar el diseño de los módulos de batería, mejorar la integración y modularidad de los paquetes de baterías, reducir los componentes inactivos y aumentar la densidad energética de los paquetes de baterías.
Las tecnologías de integración de paquetes de baterías más populares en la actualidad incluyen CTP, CTB, CTC y otras formas. La forma, el material y la combinación de piezas han cambiado con el avance de la tecnología de integración. La dirección general es la integración y la integración. Al reducir la cantidad de piezas independientes y usar una pieza grande para reemplazar varias piezas, se forman componentes más grandes y más funcionales.
2-Diseño de caja de batería
La caja de la batería es el portador del conjunto del sistema de batería de potencia, desempeña un papel clave en el funcionamiento seguro y la protección del producto, y afecta directamente a la seguridad de todo el vehículo. El diseño estructural de la caja de la batería incluye principalmente la selección de materiales de carcasa para la carcasa superior, la carcasa inferior y otros componentes de la caja de la batería, y la selección de soluciones de proceso de fabricación. La cubierta superior de la caja de la batería desempeña principalmente una función de sellado y no está sujeta a mucha fuerza; la carcasa inferior de la caja de la batería es el portador de todo el producto del sistema de batería de potencia, y el módulo de batería está dispuesto principalmente en la carcasa inferior. Por lo tanto, debe haber medidas estructurales como ranuras incrustadas y deflectores dentro de la caja de la batería para garantizar que el módulo de batería esté fijado de manera confiable cuando el vehículo está conduciendo, y no haya movimiento en las direcciones delantera, trasera, izquierda, derecha, arriba y abajo, para evitar el impacto en las paredes laterales y la cubierta superior y afectar la vida útil de la caja de la batería.
Figura 3: Solución de caja inferior de batería, marco a-skin, soldadura b-FSW + marco, soldadura c-FSW + marco
l Diseño de la estructura del punto de instalación del paquete de baterías y fijación de la conexión
El punto de instalación del paquete de baterías generalmente adopta una estructura de viga de montaje, que se extiende a través de la parte delantera y trasera, y el extremo delantero está conectado a la viga longitudinal de la cabina delantera para formar una estructura de viga cerrada eficaz y coherente. Los puntos de instalación están razonablemente dispuestos de acuerdo con la distribución del peso del paquete de baterías. El paquete de baterías y el vehículo se fijan de varias maneras, incluida la fijación con pernos, la fijación mecánica + conexión híbrida de unión adhesiva, conexión a presión, etc.
Figura 4: Disposición del paquete de baterías y sección de instalación
El paquete de baterías de potencia se instala generalmente en el vehículo mediante múltiples estructuras de argollas de elevación. Además del gran peso del propio paquete de baterías de potencia, las argollas de elevación también deben soportar la excitación de la carretera provocada por el movimiento del vehículo, como caminos de piedra y baches profundos. Estas condiciones de trabajo duraderas y las condiciones de uso indebido imponen mayores requisitos a la resistencia de la estructura de las argollas de elevación.
Figura 5: Diferentes soluciones de conexión de orejetas de elevación: a Orejeta de elevación soldada b Orejeta de elevación de marco de aluminio extruido
l Estructura de seguridad y protección de la caja de batería
Resistencia mecánica y protección: La caja de la batería debe tener suficiente resistencia mecánica para proteger las baterías en su interior de golpes e impactos mecánicos. La caja de la batería debe poder soportar vibraciones, extrusiones y golpes mecánicos para garantizar la seguridad de la batería en diversas condiciones.
Protección contra colisiones: el diseño de la caja de la batería debe tener en cuenta la seguridad contra colisiones, especialmente en caso de colisiones laterales y colisiones en la parte inferior. Por lo general, está hecha de aluminio o acero y se conecta a la bandeja inferior a través de un marco exterior para proporcionar rigidez estructural y mejorar las capacidades de absorción de energía de colisión. Además, se deben diseñar estructuras de absorción de colisiones adecuadas para evitar la deformación de la caja de la batería y daños a las celdas de la batería.
Resistente al agua, al polvo y a la corrosión: la caja de la batería debe ser resistente al agua y al polvo, y normalmente utiliza juntas de sellado de nivel IP67 para garantizar la hermeticidad. Además, también se deben considerar medidas anticorrosión, como rociar un revestimiento de PVC en el exterior para mejorar la resistencia a la corrosión.
Diseño a prueba de explosiones y con alivio de presión: cuando una batería explota, la energía debe liberarse de manera concentrada y direccional a través de dispositivos como válvulas antideflagrantes balanceadas para evitar que ingrese a la cabina del cliente. Además, se deben tomar medidas a prueba de explosiones (como la destrucción estructural parcial) para evitar la ruptura total del equipo.
l Diseño de sellado
El diseño de la superficie de sellado entre la tapa superior y la carcasa inferior de la caja de la batería desempeña un papel importante en el rendimiento del sellado, y su diseño debe diseñarse junto con la estructura de la caja de la batería y el anillo de sellado. La superficie de sellado debe mantenerse en el mismo plano tanto como sea posible para evitar demasiadas estructuras curvas. Dado que la tapa superior y la carcasa inferior están conectadas por pernos, se utiliza una gran cantidad de pernos, por lo que es particularmente importante asegurar la coaxialidad de los orificios. Al organizar las posiciones de los orificios de los pernos de manera razonable, las dimensiones de la posición deben ser lo más redondas posible y estar dispuestas simétricamente en las direcciones X e Y. La selección del número de pernos de conexión debe considerarse de manera integral en función del nivel de sellado y la cantidad de carga de trabajo de desmontaje y montaje.
Figura 6: Diseño de sellado de la caja superior e inferior, 1-cubierta superior de la batería 2-junta de sellado 3-cubierta inferior de la batería 4-conducto de metal
l Seguridad eléctrica y protección contra cortocircuitos
Fiabilidad de la conexión: Los conectores dentro de la caja de la batería deben tener la conexión de polaridad correcta para garantizar la capacidad de sobrecorriente de la caja de la batería y la confiabilidad de las conexiones eléctricas/mecánicas, incluidas las medidas de relajación, etc.
Diseño de aislamiento eléctrico y resistencia al voltaje: El diseño del módulo adopta una protección de doble aislamiento. La celda de la batería en sí tiene una capa de película azul y un parche superior para cumplir con los requisitos de aislamiento y resistencia al voltaje. La protección de aislamiento y resistencia al voltaje se establece entre la placa del extremo/lateral y la celda de la batería, y entre la celda de la batería y la superficie de montaje inferior.
l Diseño de gestión térmica
El desarrollo de la gestión térmica de la batería abarca todo el ciclo de diseño y desarrollo del sistema de paquete de baterías, incluido el diseño del control de temperatura de la batería, la placa fría, el sistema de tuberías, etc. El objetivo principal del diseño del sistema de gestión térmica de la batería es garantizar que el sistema de batería funcione a una temperatura de funcionamiento relativamente adecuada a través del control de calefacción o refrigeración, teniendo en cuenta la distribución del espacio, el coste del diseño, el peso ligero, etc., al tiempo que se reduce la diferencia de temperatura entre las celdas para garantizar la coherencia.
Actualizaremos periódicamente la información y las tecnologías relacionadas con el diseño térmico y la reducción de peso. Gracias por su interés en Walmate.