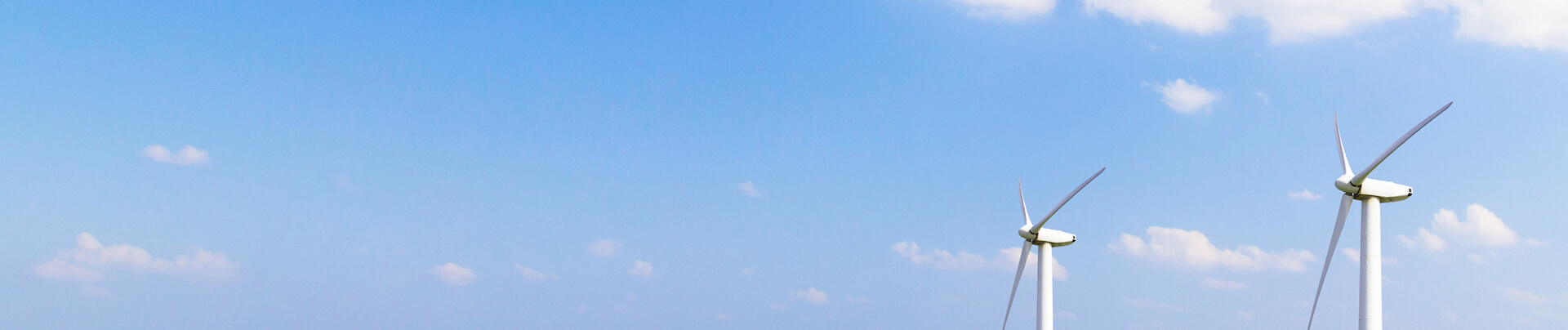
El intercambio y la participación promueven el crecimiento
y trabajan juntos para el desarrollo común
El paquete de baterías es la fuente de energía principal de los vehículos de nueva energía y proporciona la potencia necesaria para impulsar todo el vehículo. Por lo general, evaluamos las ventajas y desventajas de la tecnología de paquetes de baterías desde el punto de vista de la eficiencia (densidad energética), la seguridad, los costos de fabricación y mantenimiento.
En el diseño de baterías, el voltaje de una sola celda es de solo 3-4 V, mientras que el voltaje requerido por los vehículos eléctricos es de al menos 100 V. Los autos nuevos ahora tienen un voltaje de 700 V/800 V, y la potencia de salida es generalmente de 200 W, por lo que la batería necesita ser reforzada. Para cumplir con los requisitos de corriente y voltaje de los vehículos eléctricos, se deben conectar diferentes celdas en serie o en paralelo.
El paquete de baterías está compuesto de celdas de batería, sistemas electrónicos y eléctricos, sistemas de gestión térmica, etc., que están encerrados por una estructura de marco de batería: placa base (bandeja), marco (marco de metal), placa de cubierta superior, pernos, etc. Cómo "empaquetar" estos componentes y sistemas en un todo de manera más eficiente y segura siempre ha sido un tema de investigación y exploración continua para toda la industria.
Artículo anterior: Innovación y desarrollo de la tecnología de integración de baterías
El origen de la tecnología de grupos de baterías de potencia se remonta a la década de 1950 y se originó en la ex Unión Soviética y algunos países europeos. Esta tecnología se utilizó originalmente como un concepto de ingeniería y fabricación para determinar las similitudes físicas de las piezas (rutas de proceso universales) y establecer su producción eficiente.
El núcleo de la tecnología de grupo (GT) es identificar y explorar las similitudes de cosas relacionadas en las actividades de producción, clasificar problemas similares en grupos y buscar soluciones óptimas relativamente unificadas para resolver este grupo de problemas para lograr beneficios económicos. En el campo de las baterías de energía, la tecnología de grupo involucra principalmente la tecnología de integración de baterías de celdas individuales en paquetes de baterías (Packs), incluida la estructura, la gestión térmica, el diseño de conexión eléctrica y la tecnología del sistema de gestión de baterías (BMS).
La tecnología de agrupación anterior en el campo automotriz es MTP (Module To Pack), lo que significa que las celdas se integran primero en módulos y luego los módulos se integran en paquetes. Esta tecnología se caracteriza por módulos desmontables y reemplazables, que tienen una buena capacidad de mantenimiento, pero la eficiencia de agrupación es baja. Con el desarrollo de la tecnología, la tecnología de agrupación ha experimentado una transformación de MTP a CTP (Cell To Pack). La tecnología CTP se refiere a la tecnología de integración directa de celdas en paquetes, eliminando la estructura modular tradicional y mejorando la eficiencia de agrupación y la eficiencia de producción. En los últimos años, la industria también está explorando tecnologías de agrupación como CTC (Cell To Chassis), CTB (Cell To Body & Bracket) y MTB (Module To Body) con mayor eficiencia de integración.
En el campo de las baterías de energía y el almacenamiento de energía electroquímica, los principales avances tecnológicos de las baterías de litio provienen de la innovación estructural y la innovación de materiales. El primero es optimizar la estructura del "paquete de baterías de celdas-módulos" a nivel físico para lograr el objetivo de mejorar la densidad de energía del volumen del paquete de baterías y reducir los costos; el segundo es explorar los materiales de las baterías a nivel químico para lograr el objetivo de mejorar el rendimiento de las celdas individuales y reducir los costos. Este artículo se centra en el impacto de diferentes tecnologías de integración estructural en la tecnología de fabricación de paquetes de baterías y la dirección del desarrollo innovador desde la perspectiva de la integración estructural de los paquetes de baterías. Las tecnologías clave actuales para la integración de baterías de energía se muestran en la siguiente figura:
1- MTP que ha sido eliminado1- MTP que ha sido eliminado
Al comienzo de la actual ola de desarrollo de vehículos eléctricos, se han lanzado muchos modelos de vehículos de nueva energía que utilizan petróleo como combustible. Estos modelos siguen la disposición espacial y el diseño de estilo de los vehículos de gasolina tradicionales. Los ingenieros han ensamblado un módulo de celdas de batería relativamente grande conectando una cierta cantidad de celdas de batería individuales en serie/paralelo y luego han colocado varios de esos módulos de celdas de batería en el paquete de baterías, que es el conocido paquete de baterías "MTP". Dado que el paquete de baterías debe "envasarse" más de dos veces, la cantidad de componentes necesarios es extremadamente grande y el paquete de baterías aparece como "tres capas internas y tres capas externas", con demasiadas partes redundantes que ocupan más volumen y peso del sistema, lo que resulta en una densidad de energía volumétrica y densidad de energía gravimétrica deficientes del paquete de baterías "MTP". Además, dado que el diseño de los vehículos de gasolina no reservó específicamente espacio para la batería, el sistema de baterías solo se puede "apretar donde quepa", lo que conduce a una mala competitividad del producto y una mala experiencia del usuario.
Desde el lanzamiento de las nuevas plataformas de vehículos eléctricos inteligentes representadas por Tesla, los vehículos eléctricos puros nativos han permitido instalar los paquetes de baterías en ubicaciones espaciales ideales de una manera más eficiente y regular, los sistemas trieléctricos se pueden distribuir de manera más razonable y la arquitectura electrónica y eléctrica del vehículo y el diseño de gestión térmica se pueden integrar de manera más eficiente. La solidez del producto del vehículo en términos de eficiencia energética, resistencia e inteligencia se ha mejorado enormemente.
2-Era de la tecnología integrada 2.0—CTP
El paquete de baterías con estructura MTP tiene un problema de utilización del espacio significativo. La utilización del espacio de la celda de batería al módulo es del 80%, la utilización del espacio del módulo al paquete de baterías es del 50% y la utilización del espacio total es solo del 40%. El costo del hardware del módulo representa aproximadamente el 14% del costo total de la batería. Esta estructura de baja utilización del espacio no puede satisfacer los requisitos de desarrollo de los vehículos de nueva energía. En el marco de la idea de integración de celda de batería → módulo → paquete de baterías → carrocería, si el vehículo quiere cargar la mayor cantidad de energía posible en el espacio limitado del chasis y mejorar la utilización del volumen, es necesario considerar la estandarización de cada paso de integración. A medida que la demanda del mercado de autonomía de conducción continúa aumentando, el volumen de un solo módulo de batería continúa aumentando, lo que indirectamente conduce al surgimiento de la solución CTP.
La tecnología de estructura CTP nació teniendo en cuenta la seguridad, la complejidad del empaquetado, la reducción de costos, etc. Bajo la premisa de garantizar la seguridad de la celda de la batería, la tecnología CTP reduce los cables internos y las piezas estructurales. En comparación con la tecnología MTP, la tecnología CTP no tiene estructura modular y empaqueta directamente la celda de la batería en un paquete de baterías antes de instalarlo en el vehículo.
Actualmente, existen dos ideas principales: una es considerar el Pack como un gran módulo completo que reemplaza la estructura de múltiples módulos pequeños en su interior, representados por CATL; la otra es considerar el uso de una solución sin módulos durante el diseño y diseñar la propia batería como el participante de la potencia, como la batería Blade de BYD.
El punto central de la tecnología CTP es la eliminación del diseño modular, combinando directamente las celdas de batería con la carcasa, lo que reduce el uso de placas terminales y separadores. Los problemas que surgen a continuación son la fijación del paquete de baterías y la gestión térmica.
De hecho, el producto original del paquete de baterías CTP no era un diseño puro sin módulos, sino un diseño que fusionaba los módulos pequeños originales en tres módulos grandes y dos módulos medianos, y también había placas de aluminio en ambos extremos, por lo que en teoría sigue siendo MTP, pero de hecho hay grandes mejoras en la estructura.
Tras la introducción de CTP 3.0, CATL presentó un método de fabricación más avanzado, logrando un diseño completamente libre de módulos. Las celdas de la batería han cambiado de una orientación vertical a lo largo de la altura a una posición horizontal. Además, se ha implementado una nueva solución de refrigeración entre las celdas de la batería, que no solo disipa el calor sino que también proporciona funciones de soporte, amortiguación, aislamiento y control de temperatura. La carcasa inferior también se ha diseñado con una característica de fijación limitante.
Figura 1: Comparación entre la batería CATL Kirin CTP2.0 y CTP3.0
3-Era de la tecnología integrada 3.0: CTB, CTC
l Tecnología CTB
La tecnología CTP es un gran paso adelante en la innovación de la estructura de la batería, pero no ha supuesto un gran avance en el propio paquete de baterías. En la tecnología CTP, el paquete de baterías sigue siendo un componente independiente. En comparación con la estrategia simplificada de CTP para los paquetes de baterías, la tecnología CTB combina el panel del suelo de la carrocería y la cubierta del paquete de baterías en uno. La superficie de sellado plana formada por la cubierta de la batería, el umbral de la puerta y las vigas delantera y trasera sella el habitáculo con sellador, y la parte inferior se ensambla con la carrocería a través del punto de instalación. Al diseñar y fabricar el paquete de baterías, el sistema de baterías se integra con la carrocería como un todo, se pueden cumplir los requisitos de sellado e impermeabilidad de la propia batería, y el sellado de la batería y del habitáculo es relativamente sencillo, y los riesgos son controlables.
De esta manera, la estructura sándwich original de "cubierta del paquete de baterías-celda de batería-bandeja" se transforma en una estructura sándwich de "cubierta del paquete de baterías integrada en los bajos de la carrocería-celda de batería-bandeja", reduciendo la pérdida de espacio causada por la conexión entre la carrocería y la cubierta de la batería. En este modo estructural, el paquete de baterías no solo es una fuente de energía, sino que también participa en la fuerza y la transmisión de todo el vehículo como estructura.
Figura 2: Diagrama esquemático de la estructura de la tecnología CTB
l Tecnología CTC
Después de adoptar el método CTC, el paquete de baterías ya no es un conjunto independiente, sino que se integra en la carrocería del vehículo, lo que optimiza el diseño del producto y el proceso de producción, reduce el número de piezas del vehículo, especialmente reduce las piezas estructurales internas y los conectores de la batería, tiene la ventaja inherente de ser liviano, maximiza la utilización del espacio y proporciona espacio para aumentar el número de baterías y mejorar la autonomía de conducción. Con la condición de que el sistema electroquímico en sí permanezca sin cambios, la autonomía de conducción se puede aumentar aumentando el número de baterías.
Figura 3: Diagrama de la estructura de la tecnología CTC de Tesla
Por ejemplo, Tesla y otros fabricantes de automóviles han lanzado sucesivamente modelos de tecnología CTC. A nivel de celda, pueden utilizar estructuras sándwich elásticas multifuncionales y tecnología de refrigeración por agua de gran superficie, y superponer la tecnología de reutilización del espacio anticolisión en la parte inferior del paquete de baterías aportada por el desarrollo integrado, teniendo en cuenta la eficiencia de agrupación, la disipación de calor y la seguridad, y promoviendo la aplicación de la tecnología CTC desde las dos dimensiones de optimización de celdas y protección de la estructura del vehículo. A nivel de desarrollo integrado del vehículo, la celda de la batería se integra directamente en el chasis, eliminando los vínculos de los módulos y los paquetes de baterías. Se realiza la integración de los tres sistemas eléctricos principales (motor, control electrónico, batería), los tres sistemas eléctricos secundarios (CC/CC, OBC, PDU), el sistema de chasis (sistema de transmisión, sistema de conducción, sistema de dirección, sistema de frenado) y los módulos relacionados con la conducción autónoma, y se optimiza la distribución de energía y se reduce el consumo de energía a través del controlador de dominio de energía inteligente.
4-Cambios en los requisitos específicos para cajas de baterías para tecnologías CTP, CTB y CTC
En la estructura tradicional de los paquetes de baterías, el módulo de batería cumple la función de soportar, fijar y proteger la celda de la batería, mientras que el cuerpo de la caja de la batería soporta principalmente la fuerza de extrusión externa. La aplicación de las tecnologías CTP, CTB y CTC plantea nuevos requisitos para las cajas de baterías, que se reflejan específicamente en:
Se mejoran los requisitos de resistencia del cuerpo de la caja de la batería: dado que el enlace del módulo se reduce o se elimina en las estructuras CTP, CTB y CTC, el cuerpo de la caja de la batería no solo debe soportar la fuerza de extrusión externa, sino también la fuerza de expansión de la celda de la batería que originalmente soporta el módulo. Por lo tanto, los requisitos de resistencia del cuerpo de la caja de la batería son más altos.
Capacidad de protección contra colisiones: después de utilizar la tecnología CTP para quitar las vigas laterales del paquete de baterías, la batería soportará directamente el impacto de la colisión, por lo que el paquete de baterías CTP debe tener suficiente resistencia a las colisiones.
Requisitos de aislamiento, aislamiento y disipación de calor: las estructuras CTP o CTB y CTC cambian el perfil de la placa inferior a una placa refrigerada por agua basada en la caja estructural que soporta el chasis. La caja de la batería no solo soporta el peso de las celdas de la batería, sino que también proporciona gestión térmica y otras funciones para la batería. La estructura es más compacta, el proceso de fabricación está optimizado y el grado de automatización es mayor.
Menor capacidad de mantenimiento: el diseño altamente integrado hace que sea complicado reemplazar el paquete de baterías. Por ejemplo, en la estructura CTC, las celdas de la batería están rellenas de material de resina, lo que dificulta su reemplazo y hace casi imposible su reparación.
5- Impacto de la integración de paquetes de baterías en la infraestructura de carga de vehículos eléctricos
La elección de diferentes tecnologías de integración de paquetes de baterías también implica la elección de diferentes métodos de compensación. La CTP tiende a ser la sustitución de la batería, mientras que la CTB/CTC, más integrada, tiende a ser la carga rápida.
Un alto nivel de integración significa que se pueden alojar más baterías en el mismo espacio, lo que aumenta la autonomía de los vehículos eléctricos. Es posible que los usuarios ya no necesiten cargar con frecuencia para distancias cortas, sino que prefieran cargar rápidamente durante viajes largos. Por lo tanto, la planificación de la infraestructura de carga debe tener en cuenta estos cambios para garantizar que pueda satisfacer las necesidades de los usuarios.
A medida que aumenta la integración de los paquetes de baterías, el tamaño físico y la estructura de los paquetes de baterías pueden cambiar, lo que puede afectar el diseño de la interfaz de carga y la compatibilidad del equipo de carga.
Además, la mayor integración de los paquetes de baterías también puede afectar la velocidad y la eficiencia de la carga. Es posible que sea necesario desarrollar e implementar sistemas de gestión de baterías y tecnologías de carga más eficientes para garantizar un proceso de carga rápido y seguro.
Actualizaremos periódicamente la información y las tecnologías relacionadas con el diseño térmico y la reducción de peso. Gracias por su interés en Walmate.