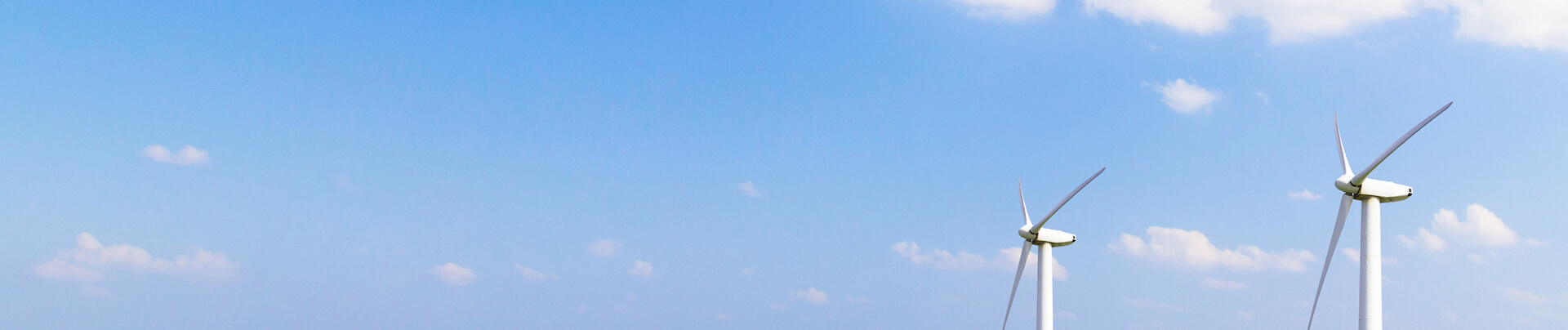
El intercambio y la participación promueven el crecimiento
y trabajan juntos para el desarrollo común
1- Requisitos especiales de tolerancia para piezas clave
En la fabricación de bandejas de baterías para vehículos eléctricos y carcasas de baterías de almacenamiento de energía con refrigeración líquida, el control de la tolerancia de las superficies de conexión clave y las interfaces afecta directamente el sellado, la eficiencia de disipación de calor y la precisión del ensamblaje.
a. Superficie de instalación de la placa de refrigeración líquida
La placa de refrigeración líquida es el componente principal del sistema de gestión térmica de la batería. La planitud de su superficie de instalación afecta directamente el sellado del canal de flujo del refrigerante. Si la planitud está fuera de la tolerancia, provocará una compresión desigual de la junta de silicona, lo que provocará fugas locales o un aumento de la resistencia térmica.
b. Desalineación de la soldadura
La bandeja de la batería suele utilizar una estructura de soldadura de aleación de aluminio. La desalineación de la soldadura provocará concentración de tensiones y reducirá la resistencia a la fatiga. Especialmente en entornos con altos requisitos de hermeticidad para las carcasas de baterías (como IP67), la desalineación debe controlarse estrictamente.
c. Orificio de posicionamiento del módulo de batería
El orificio de posicionamiento se utiliza para fijar con precisión el módulo de batería. Una tolerancia excesiva provocará desalineación del módulo, lo que provocará fallos en la conexión eléctrica o riesgos de vibración mecánica.
d. Posición del orificio del perno de fijación
El orificio del perno se utiliza para conectar la carcasa del paquete de baterías al chasis. Una desviación de la posición provocará tensiones de montaje e incluso la rotura del perno.
e. Rectitud del borde de la carcasa del paquete de baterías
La rectitud del borde de la carcasa del paquete de baterías afecta al montaje de las cubiertas superior e inferior y al nivel de protección IP, especialmente en carcasas soldadas por láser, donde el borde debe usarse como referencia para el seguimiento del cabezal láser.
2- El impacto de la tolerancia dimensional en la eficiencia de fabricación
El impacto de la tolerancia dimensional en la eficiencia de fabricación se refleja principalmente en el equilibrio entre el flujo de procesamiento, el control de costes y la calidad del producto. Un diseño con tolerancias razonables no solo garantiza la función del producto, sino que también optimiza el ritmo de producción. El impacto de un control razonable de la tolerancia dimensional en la eficiencia de fabricación se refleja principalmente en los siguientes aspectos:
a. Equilibrio entre la precisión del procesamiento y el coste de producción
· Si bien una tolerancia dimensional estricta puede mejorar la precisión del sellado y el montaje, se requieren equipos de procesamiento de alta precisión y procesos complejos, lo que aumenta significativamente la inversión en equipos y el tiempo de procesamiento.
· La búsqueda excesiva de la precisión puede aumentar los costes de procesamiento. Es necesario establecer tolerancias estrictas en las piezas funcionales clave y flexibilizarlas adecuadamente en áreas no críticas para reducir costes.
b. Control de la tasa de retrabajo y de desperdicio
· Un diseño con tolerancias razonables puede reducir el retrabajo causado por desviaciones dimensionales.
· La deformación por soldadura es el principal problema en la fabricación de bandejas de batería. El uso del proceso de soldadura en frío CMT puede optimizar la entrada de calor, reducir la deformación después de la soldadura y acortar el ciclo de retrabajo.
c. Producción modular y estandarizada
· Gracias a la estandarización de componentes, los requisitos de tolerancia se concentran en piezas reemplazables locales, lo que reduce la dificultad general del procesamiento.
· El diseño de tolerancia estandarizada también permite la compatibilidad multimodelo y reduce la necesidad de procesamiento personalizado.
3- Estándares de la industria y aplicaciones prácticas del control de planitud
Para las bandejas de baterías de vehículos de nuevas energías, los estándares de la industria tienen requisitos estrictos:
a. Estándar de planitud: La planitud de la superficie de instalación de la placa de refrigeración líquida debe ser ≤ 0,2 mm, la planitud de la placa de soporte inferior debe ser ≤ 0,5 mm/m² y el error de planitud del marco después de la soldadura debe ser ≤ 0,8 mm².
b. Optimización del proceso de fabricación: El fresado de precisión CNC, la soldadura en frío CMT y el tratamiento de envejecimiento por vibración (VSR), combinados con la detección en línea mediante interferómetro láser, reducen el riesgo de deformación.
c. Selección del material: Se recomienda utilizar aleaciones de aluminio de alta resistencia, como el 6061, con un límite elástico ≥ 1180 MPa, considerando tanto la ligereza como la estabilidad estructural.
4- Estrategia de ajuste de tolerancias basada en materiales y procesos
a. La innovación en materiales impulsa la reducción de peso
El uso de aleaciones de aluminio ligeras de alta resistencia (como el 6061) y materiales compuestos (matriz de aluminio reforzada con carburo de silicio), combinados con anodizado y recubrimiento aislante, permite lograr una reducción de peso del 30 % y mejorar la resistencia a la corrosión, adaptándose a los requisitos de disipación de calor de los sistemas de refrigeración líquida.
b. La colaboración en procesos mejora la precisión de fabricación
El moldeo por extrusión de una pieza + la soldadura por fricción y agitación (FSW) reduce el número de soldaduras, mientras que la soldadura en frío CMT y la soldadura láser controlan la deformación térmica.
c. Circuito cerrado de detección por simulación para garantizar la fiabilidad
La simulación CAE optimiza la disposición de las nervaduras de refuerzo, el escaneo láser y la tecnología de detección de fugas de helio permiten la monitorización completa del proceso. El diseño modular es compatible con una tolerancia de ±5 mm, lo que reduce costes y aumenta la eficiencia.
Actualizaremos periódicamente la información y las tecnologías relacionadas con el diseño térmico y la reducción de peso. Gracias por su interés en Walmate.