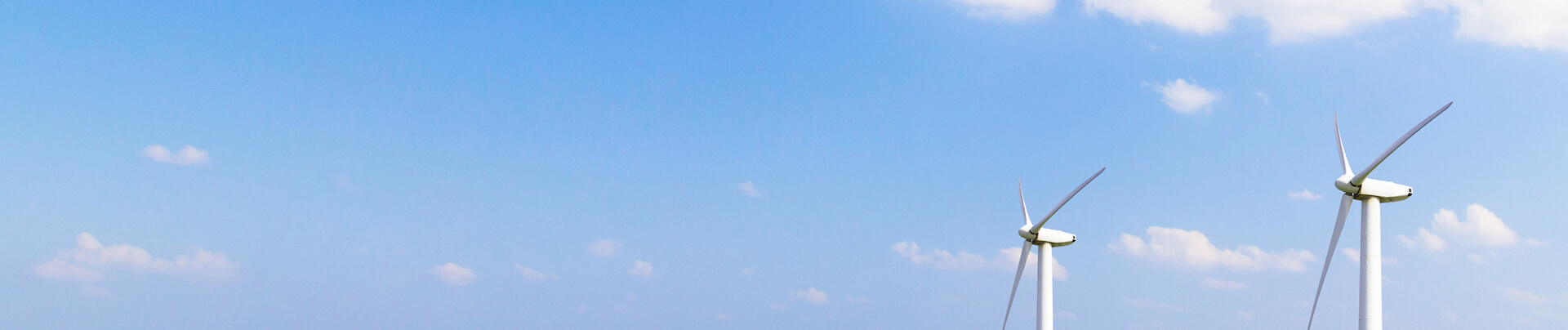
El intercambio y la participación promueven el crecimiento
y trabajan juntos para el desarrollo común
1- Características del proceso de soldadura de aleación de aluminio de la bandeja de batería/caja de almacenamiento de energía
En la fabricación de cajas de almacenamiento de energía refrigeradas por líquido, bandejas de batería y otros productos, los canales de refrigeración líquida y las estructuras multicavidad son características típicas de diseño complejo (como se muestra en la Figura 1). Dichas estructuras suelen incluir las siguientes características:
Figura 1: Diseño típico de una bandeja de batería
Entrelazado espacial tridimensional: los canales de flujo se distribuyen en forma de serpentín, con numerosos puntos de giro espaciales.
Conexión multinivel: la cavidad principal y la subcavidad están conectadas mediante tabiques de paredes delgadas (de 2 a 3 mm de espesor).
Características de miniaturización: sección transversal reducida del canal de flujo (el espesor mínimo de pared del canal de flujo del perfil de aluminio es de 1,2 mm) y difícil acceso para la soldadura.
2- Análisis de la dificultad de combinar múltiples tecnologías de soldadura en la fabricación de bandejas de baterías
En la práctica de la fabricación de bandejas de baterías, es necesario combinar múltiples tecnologías de soldadura, como la aplicación coordinada de la soldadura por fricción y agitación (FSW), la soldadura de transición de metal frío (CMT), la soldadura por fusión tradicional (TIG/MIG) y otras tecnologías. Esta combinación busca considerar la ligereza, la resistencia, el sellado y la eficiencia de producción, pero también enfrenta las siguientes dificultades principales:
a. El problema de la aportación de calor coordinada de múltiples procesos
Las diferentes tecnologías de soldadura (como la FSW y la soldadura láser) presentan grandes diferencias en la aportación de calor, lo que puede causar fácilmente alteraciones en el rendimiento del material y deformación térmica, y debe solucionarse optimizando la secuencia de soldadura y el ajuste de parámetros.
b. Compatibilidad de equipos y cuello de botella en la eficiencia
La conmutación de equipos es compleja y los requisitos de precisión en la sincronización de parámetros son elevados. Se requiere un diseño modular de estaciones de trabajo y máquinas de soldadura inteligentes para mejorar la eficiencia colaborativa y reducir el tiempo de ciclo.
c. Desafíos de equilibrar la resistencia del sellado y el costo
El riesgo de fugas en la intersección de múltiples soldaduras es alto (representa el 70 % de los defectos), por lo que se requiere un diseño de sellado redundante y optimización topológica.
3- Práctica de ingeniería: Coordinación del proceso de soldadura múltiple de la bandeja de batería y la caja PACK de refrigeración líquida para almacenamiento de energía
a. Planificación de la posición de las marcas de soldadura
· Optimización de la posición de soldadura: En la etapa de diseño del producto, se debe considerar cuidadosamente la racionalidad de la posición de soldadura para evitar la aparición de marcas de soldadura en piezas clave o áreas que afecten las funciones del producto. Por ejemplo, ajuste la separación entre el marco frontal y la boquilla de agua para evitar la interferencia de las marcas de soldadura; optimice la posición de soldadura de la boquilla de agua para reducir el impacto en el rendimiento del producto.
· Adaptación a la estructura del producto: La posición de soldadura debe ser coherente con la estructura del producto para garantizar que la soldadura pueda soportar diversas cargas y tensiones durante su uso. Por ejemplo, en el proyecto de la placa de refrigeración líquida, la estabilidad estructural y la fiabilidad del producto se mejoran mediante la planificación racional de la posición de soldadura.
· Fácil de operar y detectar: La posición de soldadura debe ser conveniente para que los operadores realicen las operaciones de soldadura y las posteriores inspecciones de calidad. Por ejemplo, evite soldar en lugares de difícil acceso o con poca visibilidad para mejorar la eficiencia y la calidad de la soldadura.
b. Control de la cicatriz de soldadura
· Tamaño de la cicatriz de soldadura: El tamaño de la cicatriz de soldadura debe controlarse estrictamente. Generalmente, la altura de la cicatriz debe estar entre 4 y 6 mm, y no debe sobrepasar el plano para garantizar la apariencia y la precisión del ensamblaje del producto. Por ejemplo, en el proyecto de la placa de refrigeración líquida, el tamaño de la cicatriz de soldadura se controló correctamente mediante el ajuste de los parámetros y el proceso de soldadura, evitando así su impacto en el rendimiento y la calidad del producto.
· Forma de la cicatriz de soldadura: La forma de la cicatriz de soldadura debe ser lo más regular posible para evitar una fusión excesiva o incompleta. Optimizando los parámetros de soldadura y las técnicas de operación, se puede mejorar eficazmente la forma de la cicatriz de soldadura y la calidad de la soldadura.
· Tratamiento de rectificado: Para las marcas de soldadura cóncavas producidas en la posición de soldadura por fricción, se utiliza un tratamiento de rectificado para garantizar una superficie lisa que cumpla con los requisitos de apariencia y rendimiento del producto.
c. Optimización de la secuencia de soldadura
· Soldadura por partición: Para productos grandes, el método de soldadura por partición permite controlar eficazmente la deformación general. Al dividir el producto en varias áreas y soldarlas secuencialmente, se reduce la concentración de calor durante el proceso de soldadura y el riesgo de deformación térmica.
· Corrección paso a paso: Durante el proceso de soldadura, se utiliza el método de corrección paso a paso para ajustar la deformación de la soldadura a tiempo. Mediante la medición y corrección continuas de la deformación del producto durante el proceso de soldadura, se garantiza la precisión dimensional y la forma del producto final para cumplir con los requisitos de diseño.
· Optimización de la trayectoria de soldadura: Planifique racionalmente la trayectoria de soldadura para evitar la repetición de soldaduras en la misma área y reducir el aporte de calor. Por ejemplo, en el proyecto de la placa de refrigeración líquida, se redujo el aporte de calor durante el proceso de soldadura y se mejoró la calidad de la soldadura mediante la optimización de la trayectoria de soldadura.
d. Control colaborativo de la deformación
La placa de refrigeración líquida sufre deformación térmica durante el proceso de soldadura, lo que resulta en una disminución de la precisión dimensional del producto. Medidas de optimización:
· Utilizar soldadura de partición y métodos de corrección gradual para controlar la deformación general.
· Optimizar los parámetros de soldadura, reducir la corriente y el voltaje, y reducir la entrada de calor.
· Utilizar accesorios para fijar el producto y reducir el movimiento y la deformación durante la soldadura.
· Utilizar un método de soldadura simétrica para distribuir uniformemente el calor.
Actualizaremos periódicamente la información y las tecnologías relacionadas con el diseño térmico y la reducción de peso. Gracias por su interés en Walmate.